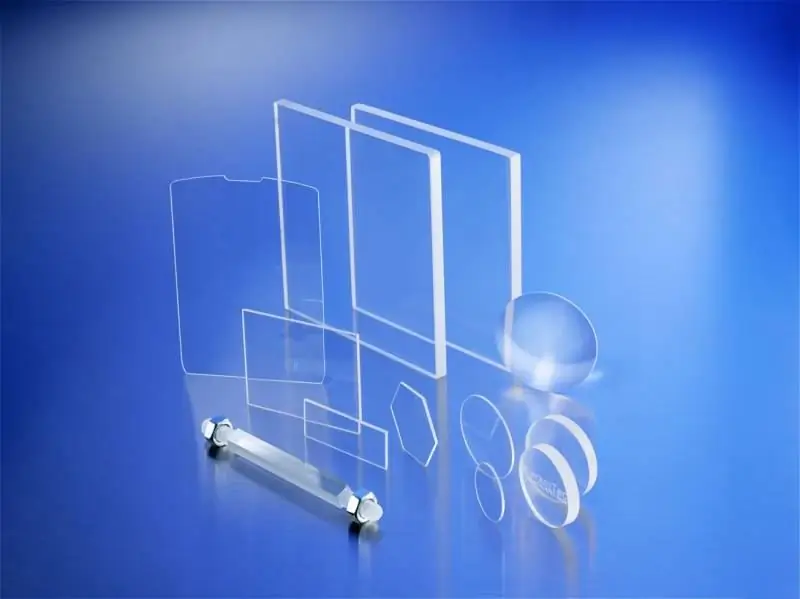
Increasing the situational awareness of drivers and crews has become a key issue, as asymmetric combat requires a better assessment of the situation around the vehicle, both in terms of operation and safety
The latter is largely due to the surrounding environment, when the combat vehicle often moves on city roads clogged with civilian traffic from cars, motorcycles, bicycles and pedestrians; any incident can have serious consequences for the relationship with the local population, negatively affect the operation "to win hearts and minds." Strictly speaking, from the point of view of the military, the ability to see what should be seen in close proximity allows the driver to fully use the capabilities of the vehicle, and the paratroopers to fully assess the situation and increase the effectiveness of their actions when landing from the vehicle.
In an increasingly virtual world, numerous companies are pursuing digital solutions, often referred to as “transparent security,” using sensors to provide the driver and crew with images they can “play” with, and ultimately add VR elements to them to enhance driving level or combat effectiveness. While wide screens in the troop compartment of armored personnel carriers or infantry fighting vehicles are becoming quite commonplace, and fully virtual driver's workplaces are being tested, ergonomic considerations remain at the forefront. However, larger transparent surfaces are increasingly being used. Recently, light armored vehicles, mainly used for reconnaissance missions, are equipped with wide windshields and side windows. The same applies to the MRAP troop transport category, which emerged during the war in Iraq and Afghanistan in the early 2000s. With regard to combat vehicles, some companies practice the use of wide windshields in order to improve the visibility of the outside world for the driver and commander.
Typically, the average mass ratio between traditional transparent armor and opaque armor is approximately 4: 1. Since the armored glass is always located at the top of the vehicle, the problem is not only in the mass itself, which reduces the payload, but also in the center of gravity, which inevitably rises, thereby reducing stability. In addition, conventional transparent protection does not fit into the rule of increasing the level of protection, since problems with light transmission and image distortion grow with the thickness of the glass. Cost is another key element in the transparent armor equation: exotic solutions already offered by many manufacturers are mostly based on transparent ceramics, but remain significantly more expensive than traditional glass.
However, in order to realistically assess the additional costs, we must balance between pros and cons: lighter glass means either increased payload or reduced wear on mechanical components. Since the thickness is also reduced, this saves on the weight of the glass frames. Many vehicles currently being manufactured with a basic level of protection can accept replacement kits to increase this level, and this is fully true for transparent armor. A lighter solution that provides a full level of protection avoids adding a transparent armor kit, which creates significantly more problems than adding an opaque armor kit regarding: first, characteristics, since optical properties become critical, and second, logistics, since with a transparent armor kit it is necessary Handle with greater care than opaque shielding kits. Manufacturers of transparent armor solve other issues, including: service life - the strength of the bulletproof glass decreases over time; cost - the longer the service life, the less the impact on the life cycle costs of the machine; resistance to external factors such as sandstorms; the ability to withstand large fluctuations in temperature, such as using an air conditioning system in very hot areas.
As mentioned, the advantage of all digital systems lies in the simplified implementation of virtual technologies, when elements of virtual reality can be easily added. However, this is partially feasible for bulletproof glasses, for example, the projection of driving-related data on the windshield is currently implemented in commercial vehicles (this is a further development of the technology for projecting the instrument panel on the windshield of the cockpit).
The German company GuS is one of the main European manufacturers of armored glass for military purposes. Recently, she has managed to reduce its specific density by more than 10%, respectively, to reduce the thickness and increase the light transmission. Among its newest products is glass with Protection Level 4, the density of which is now 294 kg / m2, thickness of 124 mm and light transmittance of 73%, its glass with Protection Level 3 is almost 20% lighter than the previous version, its characteristics are respectively 177 kg / m2, 86 mm and 85%. GuS, whose bulletproof glass has been installed on many vehicles operated by the Bundeswehr in Afghanistan, has also developed a cost-effective solution called "quick repair", which allows vehicles whose transparent surfaces have been damaged by scratches to quickly return to service without replacing a one-piece windshield. In 2017, the German company from Lubbecke is to show a new transparent ceramic material developed in collaboration with CeramTec (see below) capable of withstanding threats from Level 2 to Level 4. GuS is also one of the main suppliers of periscopes. most European tracked and wheeled armored vehicles are equipped with these systems. It has developed wide periscopes with an increased vertical field of view, which provides optimal visibility for the driver and commander and replaces the windshield, while guaranteeing high Protection Levels, up to the 4th or 5th. This significantly reduces the cost and weight of a typical Level 4 windshield weighing over 300 kg, while the GuS solution adds only 50 kg to the vehicle weight.
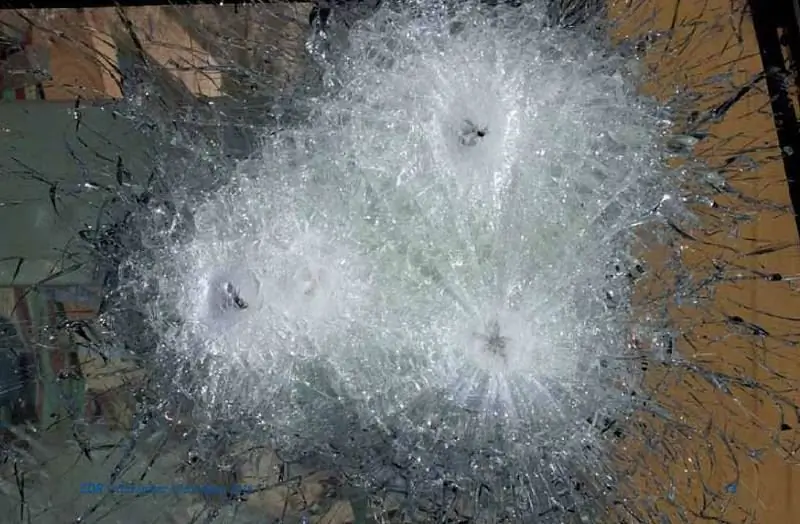
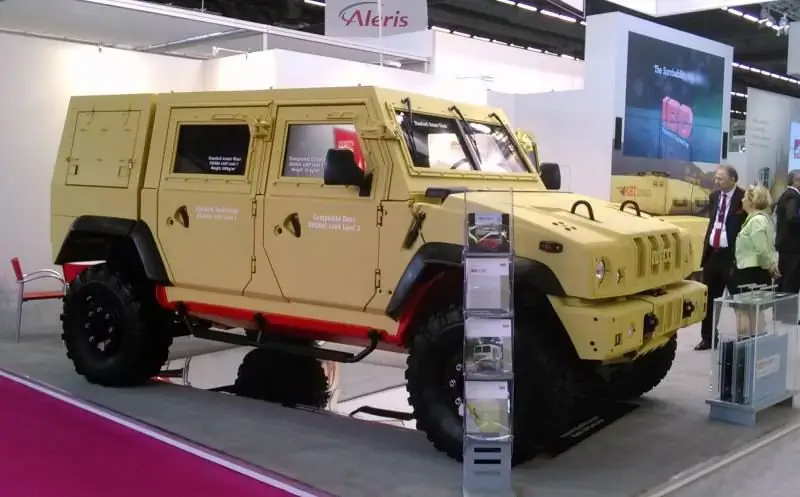
The German company IBD, as one of the suppliers of booking solutions, actively uses ceramic technologies, especially nanoceramics. So it comes as no surprise that a company specializing in opaque armor has developed transparent armor based on ceramics, which has already been used in practice for some time, but is now in its final qualification stage in two countries. The Level 3 solution has a density of 56 kg / m2, which is less than a third of that of conventional armored glass. The technology is based on a special bonding process that allows IBD to shape small tiles into a large transparent panel, which will then be covered with tempered glass backing layers. According to IBD, diffraction is less than that of conventional bulletproof glass, and the rest of the optical properties are at least not worse. The company is constantly working to reduce costs, its goal is to produce products that are no more than 50% more expensive than standard solutions.
The French company Saint-Gobain is also active in the field of transparent protection, offering both traditional and ceramic solutions. The latter are known under the SAFirE brand and provide a 65% reduction in surface density compared to standard glass with a thickness reduction of more than 30%.
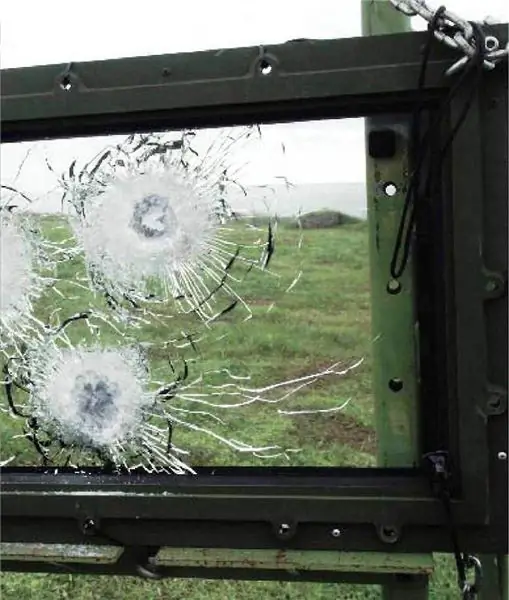
The Italian company Isoclima is currently manufacturing bulletproof glass windshield panels that allow dry installation; they are sealed to keep solvents and moisture out and allow glass to be replaced using the same frame. In terms of performance, according to the latest available data, Tier 3 is achieved with a density of 157-162 kg / m2 and a thickness of 9 mm, and Tier 2 at 125-130 kg / m2 and 59 mm, although the research division of Isoclima may well have improved the coefficient " protection / mass ". Iveco DV is currently installing Isoclima glass on its LMV, MMV and Astra trucks equipped with armored cabins. According to the company, customers are also starting to request armored glass for protection against 12.7 mm bullets, and it is able to provide a similar level of protection with a glass density of 235 kg / m2 and a thickness of 108 mm. Isoclima is also working on ceramic solutions, mostly in collaboration with CeramTec. The company develops an adhesive with the same reflectivity as transparent ceramics, so that the glue line between the tiles is almost invisible. To provide multi-impact capabilities, 90 x 90 mm tiles are used, the entire 500 x 500 mm panel glued from such tiles can withstand up to 12 bullets. Isoclima aims to reduce weight by 35% and thickness by 40%. However, if resistance to hitting a 20-mm FSP (Fragment Simulating Projectile is a standard [in NATO] fragmentation simulator.), Isoclima believes that a weight reduction of 50% is achievable.
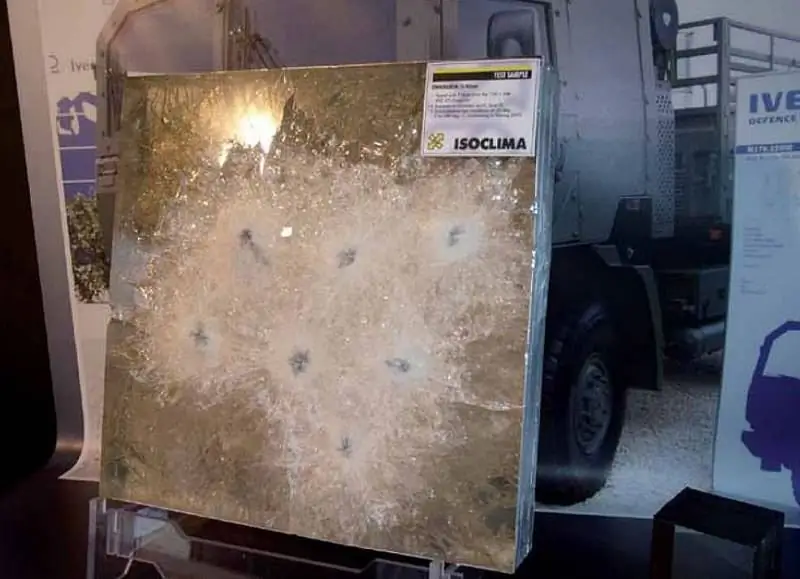
The Israeli company Oran Safety Glass (OSG) is one of the world leaders in the field of transparent protection. The top product under the CeraLite brand was developed in cooperation with the German company CeramTec. Like all transparent ceramic based protectors, CeraLite is made up of multiple tiles that are glued together to form panels of the desired size. According to the Israeli company, Crystallized Materials (CM) technology allows a weight reduction of 50-60%. While the standard STANAG Level 4 glass, made according to the traditional technology (glass plus polycarbonate), has a density of 284 kg / m2, in CeraLite it is reduced by almost 50%, to 146 kg / m2, to which can be added a 40% reduction in frame weight for glass. It also has better light transmission due to its reduced thickness, and also improves the performance of night vision goggles over conventional goggles. On impact, CeraLite behaves better than classic glass, the "cobweb" of cracks around the impact site is reduced, and multi-impact characteristics are increased. CeraLite has been tested in German and American laboratories and is currently being offered in parallel to European and American customers. The cost remains an order of magnitude higher than the cost of conventional solutions, although in the last two years it has been reduced by 30%. That is, this type of transparent armor is used only when the mass problem is critical.
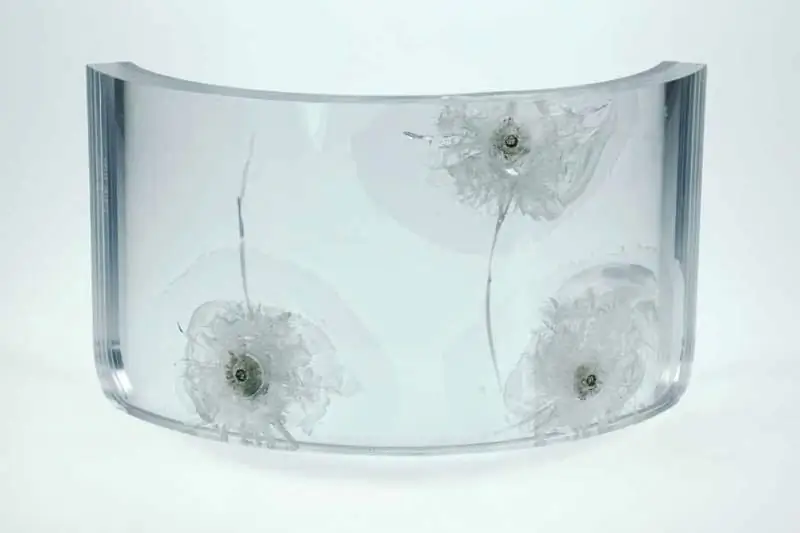
New transparent armor is installed on special vehicles of the special operations forces of the Israeli armed forces. The move towards exotic solutions does not stop research and development in more traditional fields. OSG's newest Level 4 transparent security solution has a density of 269 kg / m2 and a thickness of 122 mm, which is 5% less weight than previous glasses. The company participates in two major American programs JLTV and M-ATV. It is clear that in both cases OSG offers its ADI solution, which differs in that a different proprietary material is used on the internal surfaces instead of polycarbonate. The splinter protection material was developed by OSG to have a thermal performance similar to that of glass, as this greatly reduces delamination, which is one of the main problems that reduce the life of transparent protection. The tests were carried out at very low and at very high temperatures from -40 ° C to + 70 ° C and at a humidity of over 90%; after nearly two years of continuous testing, the sample was still in good condition. According to the company, the ADI system can last twice as long as traditional armored glass, significantly reducing vehicle lifecycle costs, although the purchase price may be slightly higher. In terms of situational awareness, OSG is developing a touchscreen variant of the ScreeneX, which features a digital display integrated into the windshield to maximize the driver's space.
The German company KRD Group has developed technologies that have made it possible to obtain a completely plastic transparent protection. Initially, her products were marketed through another company; KRD appeared just a couple of years ago and its products are now known under the Kasiglas brand. The company has developed a multi-layer material made from pure, highly transparent plastic that guarantees light transmission in excess of 90%. This allows for flat as well as curved shapes with unprecedented molding angles. We offer products with Protection Levels 2, 3 and 4, respectively, with a density of 144, 238 and 396 kg / m2 and a thickness of 121, 201 and 330 mm. Although the Kasiglas material is thicker than standard bulletproof glass, it provides higher transparency and maintains better visibility even when hit by multiple bullets, when standard glass cannot provide any visibility at all. Comparative tests carried out in Italy showed that the prototype with the third level of protection withstood the impact of six 7.62 x 51 mm armor-piercing bullets and six 7.62 x 54 mm bullets at close range, while maintaining good visibility. Other tests carried out in Germany have shown that the frame and glass remain intact after being blown up by a mine or IED. Kasiglas panels with Level 3 protection also guarantee the hit of successive and simultaneous shell-forming charge fragments in the sector from 0 ° to 45 ° and an RPG-7 grenade hit at an angle of 45 °.
Resistance to multiple hits and high resistance to a blast wave, strong impact, projectiles such as an impact core, fragmentation charges is one of the main advantages of plastic solutions, but the disadvantages are weight and thickness. In collaboration with the German Bundeswehr, KRD is implementing a program to develop a hybrid ceramic-plastic solution that exploits the strengths of the two materials. This study has three objectives: to confirm the technical feasibility of such a solution, to develop a Layer 4 solution with acceptable weight and thickness, and to develop a lightweight Layer 3 solution. The first characteristic has been tested; also tested a Level 4 solution with a density of 270 kg / m2, which has the properties of plastic, withstanding the explosion of mines and IEDs, but leaves the ceramic with the ability to withstand armor-piercing bullets. As for visibility after multiple hits, it depends on the energy of bullets and shells. A solution with Protection Level 4 retains good visibility after being hit by 7.62 mm bullets, but at the same time visibility after being hit by 14.5 mm bullets is only partially preserved; that is, the performance is worse than that of an all-plastic solution, but higher than that of a glass solution.
The company is currently working on integrating its hybrid solution into a test and qualification vehicle. The product is at the technological readiness level of TRL 6-7 (finalization and preparation for the series), while this solution will be available on the market in late 2017-mid-2018. As for the cost, it should be about 200% higher than the cost of all-glass solutions.
CERAMTEC-ETEC: Transparent ceramics from Europe
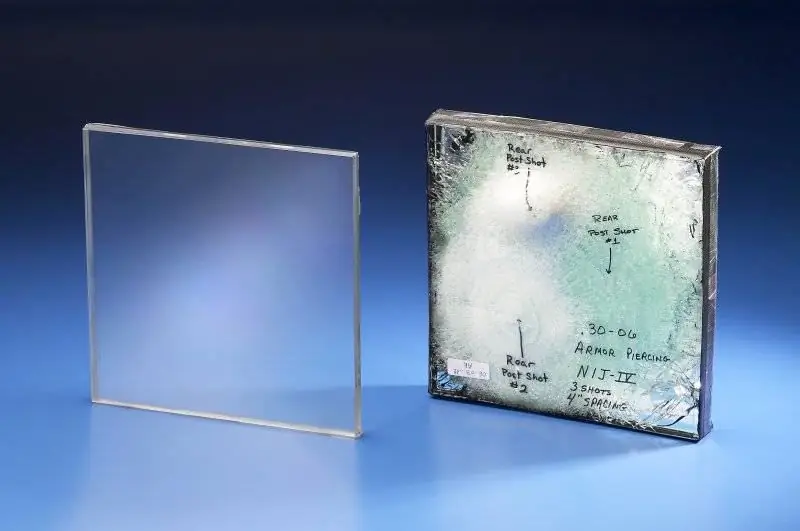
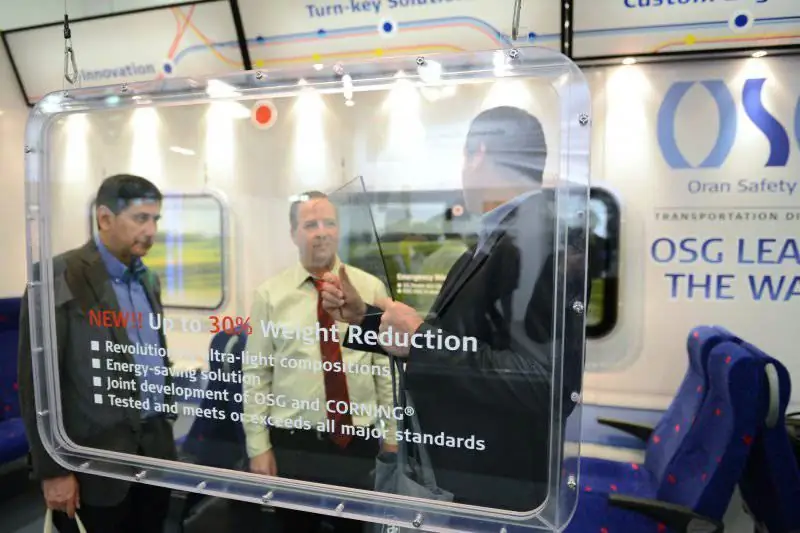
The German company from Lochmar is the main supplier for most German and European manufacturers that develop transparent ceramic-based protection. CeramTec-ETEC has developed the Perlucor polycrystalline ceramic material, which combines the superior qualities of sapphire - a solid crystal that has a strictly oriented multilayer structure with strong atomic and ionic bonds - with the qualities of glass, which is characterized by a disordered structure and weaker energy bonds between the elements. Perlucor retains the chemical bonds of sapphire, but is optically and mechanically isotropic, like glass. The latter characteristic simplifies the production process and allows for a lower cost compared to sapphire; according to CeramTec-ETEC, cost savings are over 60%. In terms of weight and thickness, the use of Perlucor in transparent protection systems results in savings of 40 to 60%. In addition, the high scratch resistance increases the service life by 2-5 times. Thus, the Perlucor material is used not only in transparent protection kits: the company has developed a technology for gluing a layer less than one millimeter thick on the front side of the glass, which allows it to increase its service life by 3-10 times.