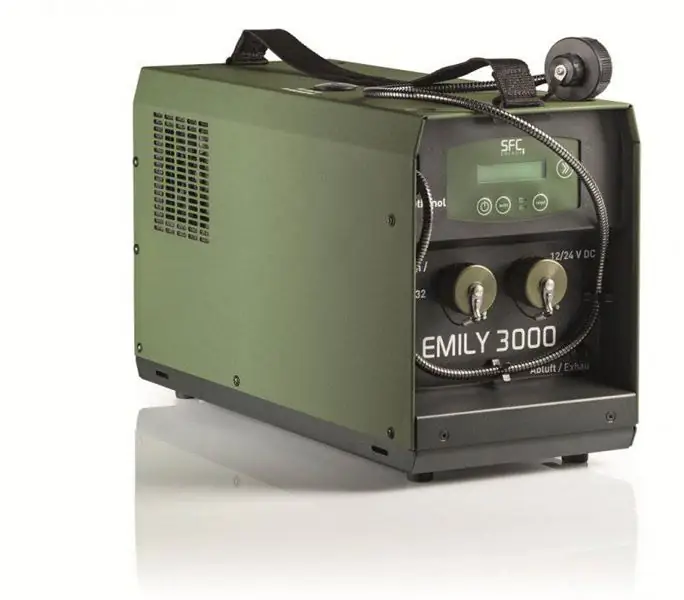
The EMILY 3000 fuel cell system has a rated output power of 125 W and a daily charge capacity of 6 kWh. It can recharge multiple batteries or act as a field generator. The system was created specifically for military applications, including test scenarios in which data on new defense systems must be collected and evaluated in the field.
Ultimately, hybrid power plants offer comparable or even better benefits to armored vehicles. While fuel efficiency, at least historically, has not been at the top of the list of mandatory characteristics of armored vehicles, nevertheless, it does increase mileage and / or duration for a given fuel capacity, increases payload, protection or firepower for a given total weight and, in general, reduce the overall logistics burden on the fleet
The hybrid electric drive may play an important role in the future of military vehicles, but the corresponding cancellation and reduction of the volume of many defense programs (not forgetting the famous FCS and FRES) and the struggle to meet urgent requirements for protected vehicles have postponed its implementation on military vehicles indefinitely.
However, when applicants for the American ground combat vehicle GCV (Ground Combat Vehicle) were announced in January 2011, among them was a project from the BAE Systems / Northrop Grumman team with a hybrid electric power unit with the E-X-DRIVE system from Qinetiq. This can be seen as a kind of gamble because none of the contenders for the JLTV (Joint Light Tactical Vehicle) light tactical vehicle program, which also included a hybrid electric drive, did not qualify for the final due to the fact that, according to available data, it is believed that the technology for this machine is not yet mature enough at this point in time. Nevertheless, the history of hybrid electric drives in ground combat vehicles has a sufficient number of programs to develop and demonstrate this technology. There is something unforgiving and inevitable about the global quest for technology that promises to save fuel, improve performance and survivability, while meeting the growing demand for onboard electricity. This is undoubtedly underpinned by parallel developments in the automotive industry, driven by environmental legislation.
Military vehicle manufacturers and systems providers have invested heavily in this technology, often pushed by some of the aforementioned ambitious government programs, before facing the particular uncertainty inherent in long-term government plans. AM General, BAE Systems, General Dynamics, Hagglunds, MillenWorks and Qinetiq have developed hybrid electric drives for the UK, US and Swedish programs, while Nexter is working on the ARCHYBALD technology development program for heavy vehicles, civilian and military.
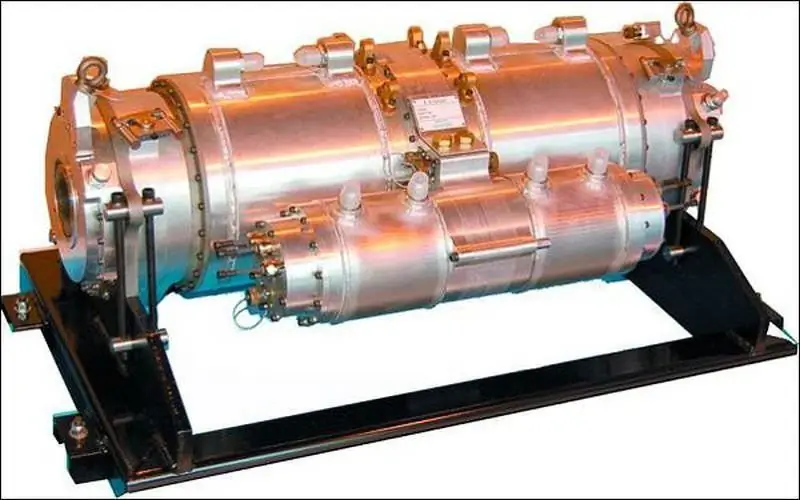
Electric drive transmission E-X-DRIVE for tracked vehicles from QinetiQ, lightweight, compact and efficient system
Hybrid predecessors
Hybrid propulsion systems have become firmly established in warships, especially on submarines, trains and heavy trucks used in quarry and opencast mines. In these applications, a prime mover, such as a diesel engine, a gas turbine, or even both, drives a generator that supplies current to drive motors and charge batteries. Some systems include a gearbox to transfer mechanical power to the final drives, while others do not.
In warships, hybrid power plants allow the use of complex and widely varying speed profiles, while the prime movers are operated in an effective speed range: electric motors for silent propulsion, diesel engines for normal propulsion, gas turbines for acceleration, etc. A submarine, powered by the traditional method, cannot launch its primary propulsion device during a dive (if it does not have a snorkel) and, in this regard, one has to rely mainly on batteries or other air-independent propulsion system. Giant earthmoving machines rely on the tremendous zero rpm torque generated by the electric motors to drive, since manual transmissions that could do the job would be huge, complex, and expensive. Trains face the same problem even more, as they have to haul several hundred tons with them from standstill, in many cases up to speeds in excess of 150 mph.
A hybrid propulsion system can save fuel by allowing a smaller, more fuel efficient prime mover to be used without degradation, because the system, when the driver is fully depressing the accelerator pedal, complements the main engine with battery-powered electric motors. Electric drives also allow damping of the prime mover when driving at low speeds, when it can be relatively ineffective. Modern hybrid cars can also store kinetic energy (for example, from a regenerative braking system) and use it to charge their batteries. Additional savings are achieved by operating the prime mover most of the time at its most efficient speed range, as well as using any additional energy to charge batteries and / or power onboard electrical consumers.
Modern military vehicles require more and more electrical power to operate communications systems, command and control equipment, surveillance and reconnaissance sensors such as optoelectronics and radars, remotely controlled weapon stations, and improvised explosive device (IED) silencers. Advanced systems such as electric armor will further increase consumption. Using all of the installed power to run electrical systems is, in theory, at least more efficient than having one system for propulsion and another for specialized equipment.
Increasing emphasis is being placed on surveillance and intelligence gathering capabilities in counterinsurgency missions, and in this regard, requirements for silent surveillance are being put forward in an increasing number of armored vehicle programs. This further increases the importance of electrical power consumption and makes fuel cells more attractive.
Hybrid electric drive systems fall into two broad categories: parallel and series. In parallel systems, an internal combustion engine and an electric motor (or electric motors) rotate the wheels or tracks through a gearbox, either separately or together. In series hybrid systems, the prime mover only drives the generator. A sequential system is simpler, all the driving power in it must go through the electric motors and therefore they must be larger than the electric motors in a parallel system with the same machine performance requirements. Systems of both types have been developed.
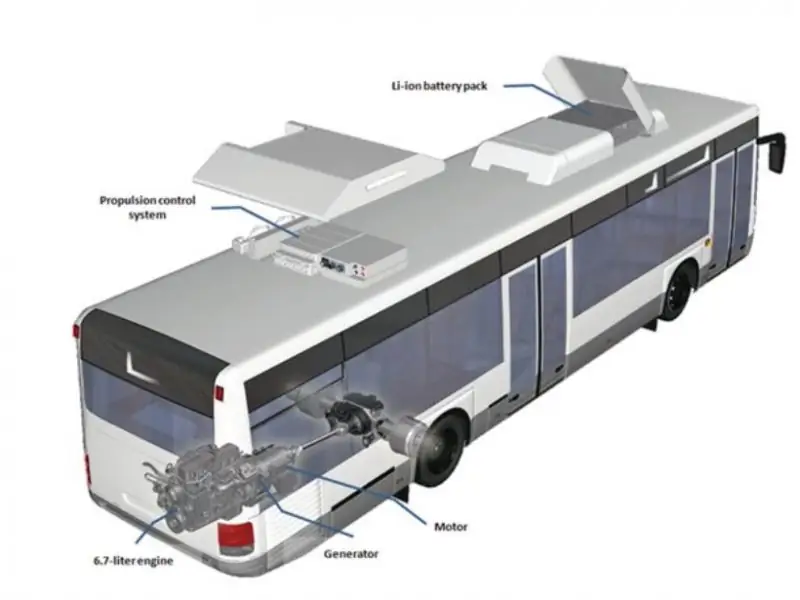
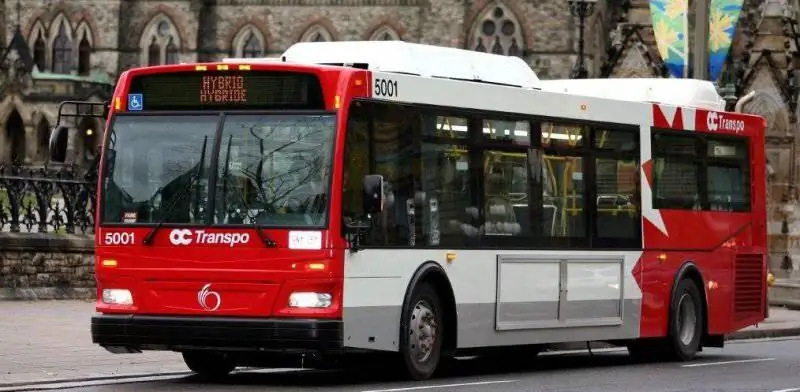
Innovations in hybrid-electric drives and fuel cell technology can be drawn from commercial technology. For example, BAE Systems manufactures hybrid-electric buses, the technology from which can be used to demonstrate the energy efficiency and improved exhaust characteristics of modern hybrid-electric vehicles designed for heavy conditions.
Increased survivability
Hybrid systems also increase survivability through a more flexible layout and the elimination of transmission components that could become a side projectile when detonated by a mine or IED. Wheeled armored vehicles especially benefit from this. By integrating the drive motors into the wheel hubs, all propeller shafts, differentials, drive shafts and gearboxes associated with traditional manual transmissions are eliminated and replaced with power cables and therefore cannot become additional shells. The elimination of all these mechanisms also allows the crew compartment to be raised above the ground at a given vehicle height, which makes passengers less vulnerable to explosions under the hull. This type of design was used in the General Dynamics UK AHED 8x8 demonstrator and the wheeled version of the SEP machine from BAE Systems / Hagglunds, the tracked version of which was also manufactured (and subsequently safely forgotten).
The electric motors integrated into the individual wheels control the power delivered to each wheel very precisely and this, according to GD UK, almost eliminates the advantage of tracks over wheels in terms of off-road terrain.
The promising ground combat vehicle will move on tracks and the BAE Systems / Northrop Grumman proposal indicates that Qinetiq's E-X-DRIVE electric transmission will be lighter, more compact and more efficient than traditional transmissions. It also allows for improved acceleration along with fault tolerance and is configurable for a wide range of machine and technology adoption programs, the company says.
Although the system includes four permanent magnet motors, the powertrain in the E-X-DRIVE is not fully electric; power recovery during cornering and mechanical gear shifting, the latter using a cam clutch. This design is a low risk solution that minimizes stresses on motors, gears, shafts and bearings. The use of a transverse shaft arrangement to regenerate mechanical power in the swing mechanism is an alternative to the use of independent drive wheels in a purely electric transmission.
One of the innovations at the heart of E-X-DRIVE is the center gearbox (known as an adjusting differential), which combines the steering motor torque, the main motor torque and the previously mentioned mechanical control recuperation mechanism. In addition to minimizing torsional loads, it eliminates the bulk and weight of the external cross shaft used in traditional solutions and other hybrid electric drive systems.
Advances in electrical engineering
Permanent magnet motors are an area of technology that has greatly improved the efficiency and power density of electric drive systems in all applications in recent years. Permanent magnet motors rely on naturally occurring powerful rare earth magnets to generate magnetic fields in the stator components, rather than on current-carrying windings (electromagnets). This makes the motors more efficient, in particular due to the fact that only the rotor needs to be supplied with electric current.
Modern power electronics is also a key technology for hybrid electric vehicles of all types. IGBT based motor controllers, for example, control the flow of power from a battery, generator, or fuel cells to determine rotational speeds and output torque from electric motors. They are much more efficient than electromechanical control systems and significantly improve the performance of variable speed drives - a technology that is far less mature than fixed speed drives that are widely used in industry.
New Jersey-based TDI Power is an example of an investor investing in liquid-cooled power electronics for electric and hybrid vehicles for civil and military applications. The company manufactures standard modular DC / DC converters and inverters that exceed current SAE and MIL standards.
Electric drives in military vehicles will benefit from extensive R&D on variable speed electric drives for industry, fueled by the prospect of overall energy savings of around 15-30%, which can be realized if fixed gear machines are replaced by variable speed drives for most industrial users, like outlined in a recent study by the University of Newcastle commissioned by the UK Science and Innovation Authority. “Improving the potential efficiency of drive loads is projected to save the UK 15 kWh billion hours per year, and when combined with improved motor and drive efficiency, total savings of 24 billion kWh,” the study said.
One of the important ways to improve the efficiency of power transfer in any electrical system is to increase the voltage, since Ohm's law dictates that for any given power, the higher the voltage, the lower the current. Small currents can pass through thin wires, allowing compact, lightweight electrical systems to provide the required loads. This is why national power grids use very high voltages when transmitting power; British power grids, for example, operate their transmission lines at up to 400,000 volts.
It is unlikely that the electrical systems of military vehicles will use voltages of this magnitude, but the days of 28 volts and similar electrical systems appear to be numbered. In 2009, for example, Qinetiq was selected by the British Department of Defense to research the generation and distribution of electrical power using 610 volt technology. Qinetiq led a team that included BAE Systems and electrical machine specialist Provector Ltd, which converted the WARRIOR 2000 BMP into a demonstrator capable of powering 610 volt high demand customers as well as existing 28 volt equipment. The machine is equipped with two 610 volt generators, each providing twice the power of the machine's original generator, effectively quadrupling the Warrior's electrical output.
Energy for a vehicle using fuel cells from SFC
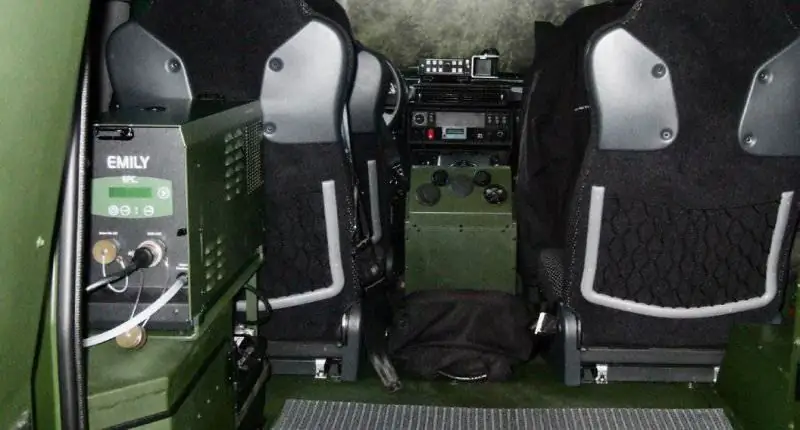
Soldiers in the field need a reliable source of energy for their machines. It must supply current to on-board devices such as radios, communications equipment, weapons systems, and optical electronic systems. But when needed, it should also act as a charging station for soldiers on assignment.
Often it is not possible to start the engine to charge the batteries while performing the task, due to the fact that this can reveal the location of the unit. Therefore, the soldiers need a way to get electric current - quietly, constantly and independently.
SFC's EMILY 2200 system is based on the successful EFOY fuel cell technology. Installed on the machine, the EMILY unit ensures that the batteries remain constantly charged. Its built-in regulator constantly monitors the voltage in the batteries and automatically recharges the batteries when needed. It works silently and its only "exhaust" is water vapor and carbon dioxide in quantities comparable to the breathing of a child.
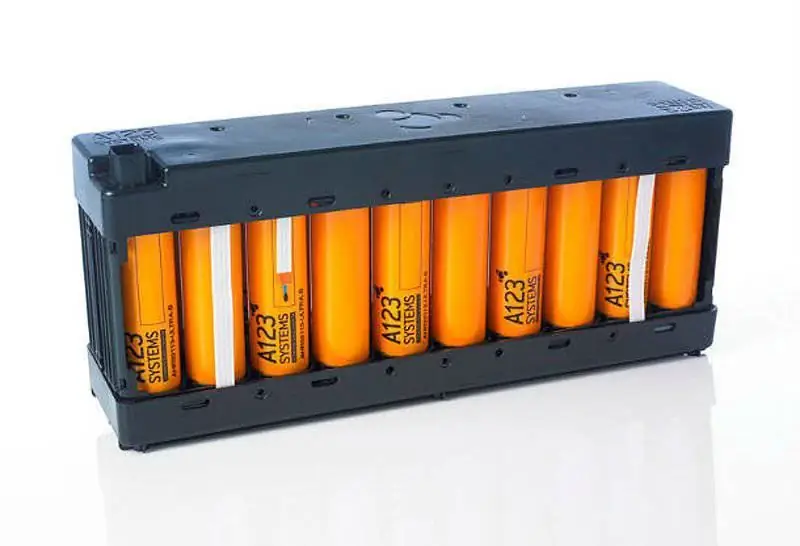
Large machines require large batteries. This lithium-ion cell package is part of BAE Systems' hybrid bus propulsion technology.
Are fuel cells possible?
Fuel cells, which use chemical processes to directly convert fuel into electric current with great efficiency, have long been viewed as a technology that can be widely used in the military field, including propelling a car and generating electricity on board. However, there are significant technical hurdles that need to be overcome. First, fuel cells run on hydrogen and mix it with oxygen from the air to generate electrical current as a byproduct. Hydrogen is not readily available and difficult to store and transport.
There are many examples of fuel cells that power electric vehicles, but they are all experimental. In the automotive world, Honda's FCX CLARITY is probably the closest availability to a commercial product, but even then it is only available in areas where there is some hydrogen refueling infrastructure and only under lease agreements. Even leading fuel cell manufacturers such as Ballard Power recognize the current limitations of this technology for use in automobiles. The company says that “mass production of fuel cell vehicles is in the long term. Today, most automakers believe that serial production of fuel cell vehicles is not feasible until around 2020, due to the industry facing issues of hydrogen distribution, optimizing durability, energy density, hot start capability and fuel cell cost.”
However, all of the world's major automakers are investing heavily in fuel cell R&D, often in conjunction with fuel cell manufacturers. Ballard, for example, is part of the Automotive Fuel Cell Cooperation, a joint venture between Ford and Daimler AG. The military is putting another obstacle to the adoption of fuel cells in the form of its requirement that everything must run on "logistic" fuels. Fuel cells can run on diesel or kerosene, but they must first be modified to extract the hydrogen they need. This process requires complex and bulky equipment, affecting the size, weight, cost, complexity and efficiency of the overall system.
Another limitation of fuel cells when operating as the prime mover of a military vehicle is the fact that they perform best at constant power settings and cannot respond quickly to required changes. This means that they must be supplemented with batteries and / or supercapacitors and associated power regulation electronics to meet peak power loads.
In the field of "supercapacitors", the Estonian company Skeleton Industries has developed a line of state-of-the-art SkelCap supercapacitors that are five times more powerful per liter of volume or more than four times more powerful per kilogram than premium military batteries. In practice, this means 60 percent more power and four times more current than the best military batteries. SkelCap's "supercapacitors" provide an instant burst of power and are used for a wide variety of applications, from fire control to turret tanks. As part of the United Armaments International (UAI) group, SkelCap fulfills various specialized orders as well as expanded programs through the UAI group based in Tallinn.
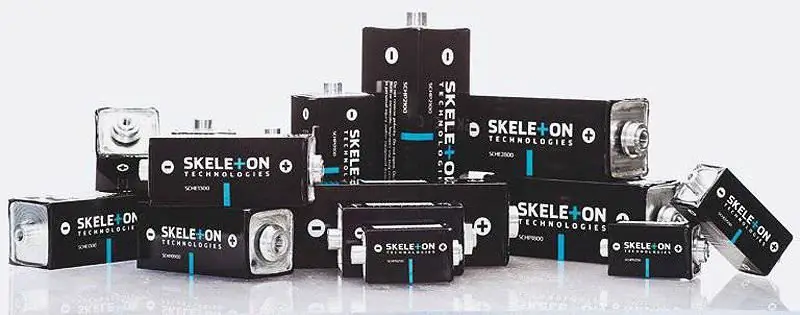
Supercapacitors from Skeleton Industries
However, this does not mean that fuel cells will not find a place in hybrid and electric military vehicles. The most promising immediate application is auxiliary power units (APU) in vehicles performing silent surveillance tasks of the ISTAR type (information gathering, target designation and reconnaissance)."In silent surveillance mode, vehicle engines do not have to run, and batteries alone cannot provide enough power for long-term operations," says the US Army Engineering Research Center, which is leading the development of solid oxide fuel cell generators and APUs that can operate. on military fuels, diesel fuel and kerosene.
This organization is currently focusing on systems up to 10 kW with an emphasis on fully integrating fuel systems with the operating needs of a fuel cell kit. Tasks that need to be addressed in the design of practical systems include control of vaporization and pollution, especially the control of sulfur through desulfurization (desulfurization) and the use of sulfur-resistant materials, as well as avoiding the formation of carbon deposits in the system.
Hybrid electric drives have a lot to offer for military vehicles, but it will be some time before the benefits of this technology become tangible.