According to the website rosinform.ru, the specialists of the Military Industrial Company have completed the development and testing of a wheeled vehicle based on the BTR-90 Rostok as part of the research work (code Krymsk). The novelty uses a hybrid power plant and electric transmission.
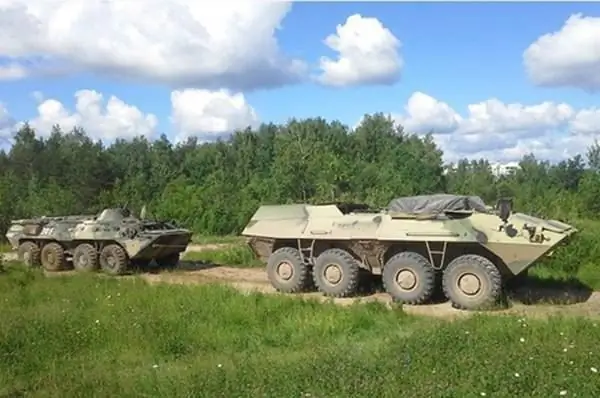
Of course, it is worth celebrating the success of Russian developers. However, it is worth noting that projects of similar vehicles with a hybrid electric drive have already been created in Western countries, and some of them appeared more than ten years ago.
Mention may be made of an 8x8 vehicle that used the Advanced Hybrid Electric Drive (AHED), the United Defense's Thunderbolt armored cannon system with a hybrid electric drive, the Reconnaissance, Surveillance and Target Designation (RST-V) combat vehicle, the Anglo-American program for the reconnaissance vehicle of the future FSCS / TRACER and some others.
Practical use
Electric drives will be used in both civil and military vehicles. Electric wheel drive technology, which, for example, allows the machine bottom to be flat and solid, offers a clear design advantage. This technology has already proven its effectiveness and reliability in daily use. The intentions of the military, first of all, are to transfer this technology to prototypes for use in large-scale programs. Thus, in the American program - the combat system of the future (FCS) - the diesel-electric combined drive became the main form of the drive, becoming the most important configuration of the entire family of machines. At the moment, prototypes of machines close to serial, equipped with electric drives, are undergoing a testing stage.
The main reason for using electric drive technology in military equipment is new combat characteristics and qualities that can only be achieved in this way. First of all, this concerns the reliability of the vehicle, its protection and logistic support. This is the key for the new basic production of wheeled vehicles.
When using this technology, it is possible to create a wheel drive module in which the electric motor is completely embedded in its hub. Suspension, powertrain, steering and shock absorber will be integrated into a compact, standardized chassis module. The brakes will also be electric, with only the parking brake acting as an additional mechanical brake.
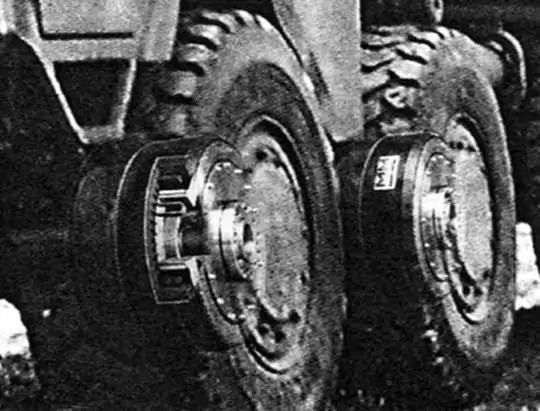
Wheel drive module with an electric motor mounted in the wheel hub
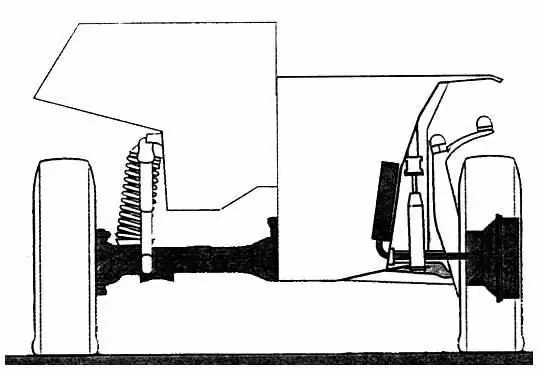
The usable space advantage of a wheeled vehicle due to the use of an electric drive compared to an older rigid axle (source: magnet motor)
Advanced Hybrid Drive Machine (AHED)
A vehicle with a promising hybrid electric drive (AHED) and 8x8 wheel arrangement from General Dynamics Land Systems (GDLS) can act as a relevant example of such a technique. It was first shown to the public in 2002 at the annual AUSA show in Washington.
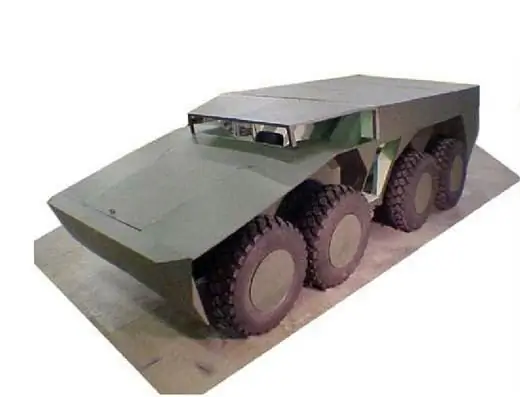
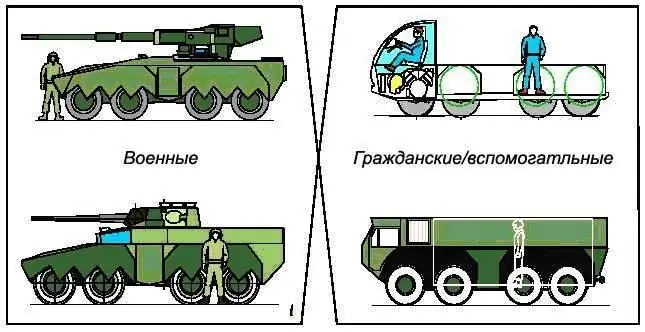
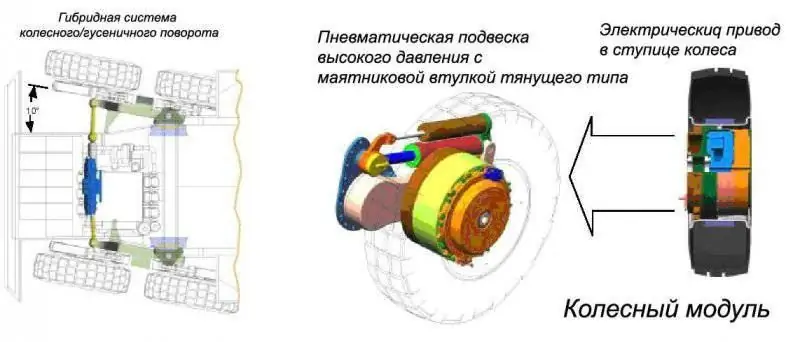
Machine with an 8 × 8 wheel arrangement and an advanced hybrid electric drive (AHED) from GDLS with an electric drive in the wheel hub of Magnet-Motor
This machine was equipped with an electric wheel hub drive from Magnet-Motor GmbH (by order of GDLS). A diesel generator and storage batteries are installed on it. MM wheel drives are part of the wheel module, which is installed on all drive wheels. The primary power is generated by a 200 kW generator, which is directly connected to the diesel engine by means of a flange. An additional 200 kW of power is provided by a highly efficient battery. Thus, the total drive power is about 400 kW. To recharge the batteries while driving, braking energy is used, as well as excess primary power. This combined configuration provides additional benefits including silent watch and stealth mode. In addition, there are no drive system components in the interior of the machine, as well as no "double bottom" to accommodate its mechanical parts. Compared to conventional drive models, the silhouette is significantly lower.
The wheel modules have a flexible “umbilical cord” that provides all the electrical functions of the sensing and power piping and supplies coolants.
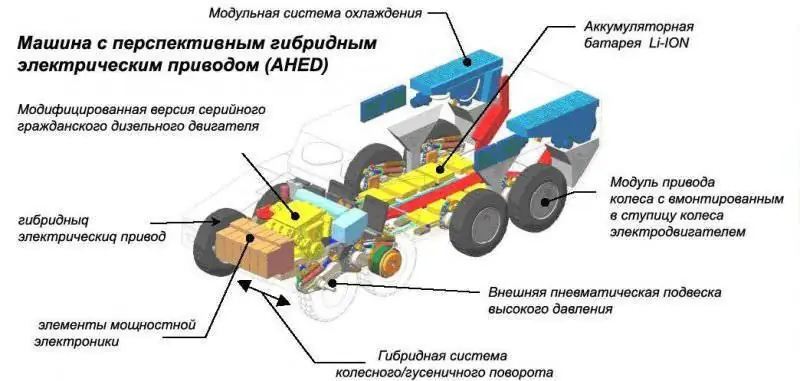
8 × 8 Wheeled Vehicle Configuration with Advanced Hybrid Electric Drive (AHED)
Also worth mentioning are the power electronics that provide the machine with electrical energy and integrate high-performance batteries into a system. They are located at the front of the machine, somewhat "raising" it.
Reconnaissance, target designation and surveillance combat vehicle (RST-V)
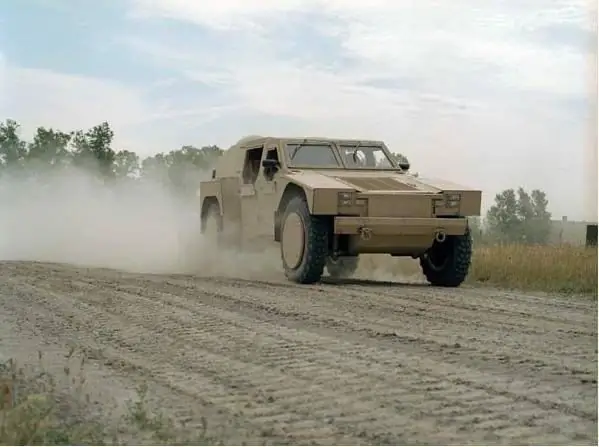
Reconnaissance, surveillance and target designation combat vehicle (RST-V)
Another order from GDLS, implemented by Magnet-Motor, was an electric combined drive system, which was used in four prototypes of the reconnaissance, target designation and surveillance (RST-V) combat vehicle. They were built for the United States Marine Corps and the Defense Advanced Planning Agency (DARPA). The drive system also includes wheel hub drives and power from a diesel generator and batteries. The use of electric wheel modules made it possible to install a special movable and folding wheel suspension on the car in order to change its clearance. In addition, the car has a raised floor between the rear and front wheels. This allows it to fit into an Osprey V 22 aircraft. The total drive power is 210 kW (110 kW diesel generator and 100 kW batteries), which allows the 3.8-ton machine to accelerate to 120 km / h and climb up to 60%.
The prototypes of the machine have passed a number of successful tests, which have confirmed compliance with the characteristics. Work is currently underway on the first small batch, which will include further intensive testing.
It is worth noting that all Magnet-Motor actuators have no wear parts and a minimum of moving parts. They practically do not require maintenance, are highly reliable, and, as a result, require low costs during operation. In addition, the development of mechanisms and electronics took into account the need to reduce personnel and maintenance costs for devices and materials, which improved logistics. In practice, the use of a fully automatic and highly efficient drive system relieves the driver. The gear selection is electric, not mechanical, the wheels of the car are steered separately, which provides better acceleration.
Even early prototypes from Magnet-Motor could provide electrical energy from the machine's drive network to various external consumers, for example, lighting elements and various mechanisms. Both drive systems developed for GDLS have electronic components that are directly integrated into the electrical drive system. With their help, you can connect command posts, radar installations, engineering vehicles, etc. to the power supply. Also, the electrical drive network can be used as an electrical primary supply system for electrical combat systems of the future, for example, electric cannons, combination cannons, laser and microwave weapons.
Thunderbolt - armored cannon system
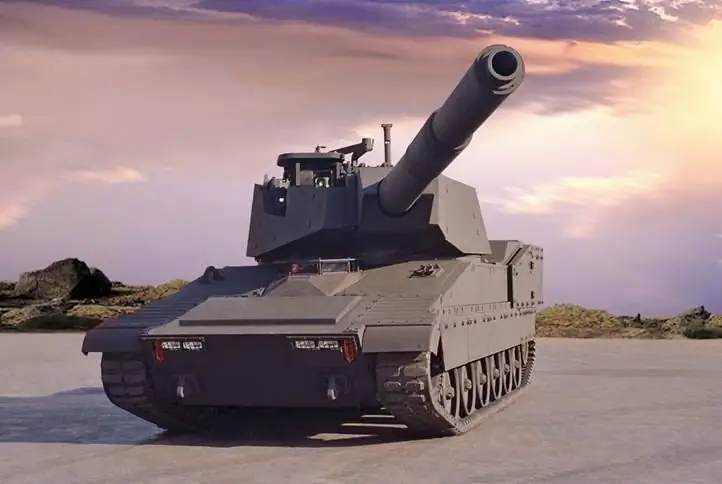
Thunderbolt armored cannon system
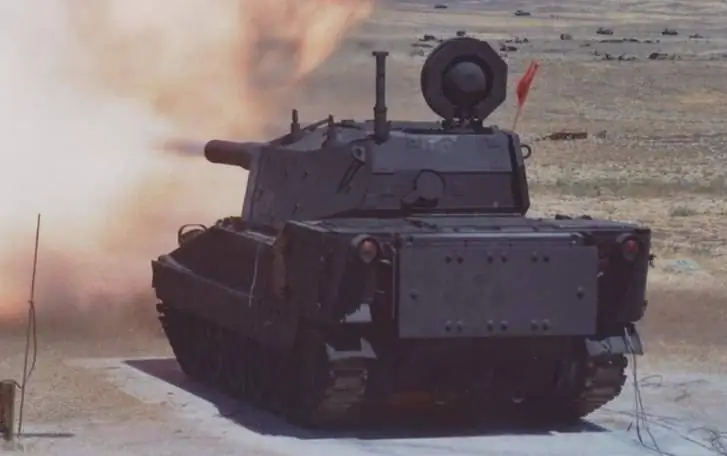
The United Defense Thunderbolt armored cannon system with a hybrid electric drive fires from its 120mm tank cannon.
The Thunderbolt armored cannon system was developed in September 2003. This is a modernized M8 armored cannon system as part of the XM291 120mm tank gun (instead of the M35 105mm cannon). The main advantage of the system is space saving due to the use of a hybrid electric drive. Two traction motors appeared in the front of the hull, and a 300 hp diesel engine appeared in one of the sponsons. This freed up space that previously housed a 580-horsepower diesel power unit and final drives. Now it can accommodate four people or additional ammunition. The difference in power is compensated for by the energy of a block of 24 lead-acid batteries.
During the development process, a demo model TTD was used - the main development tool for the HED drive. The use of a John Deere diesel engine (250 hp 187 kW) and a block of 40 lead-acid batteries (187 kW) reduced fuel consumption by 89% compared to the standard M113A3 armored personnel carrier, which is equipped with a Detroit Diesel engine (275 hp). and the Allison X2000-4A hydrodynamic transmission, when driving on rough terrain with changes in height and on roads.
True, this improvement is partly directly related only to the replacement of the engine, since the Detroit Diesel power unit has a rather high specific fuel consumption.
Electric transmissions of United Defense drive systems are classic two-way, two-way parallel circuits that transfer current from a generator driven machine engine to separate actuator motors for each track. Similar two-way systems have been used in other electrically powered tracked vehicles. True, if induction motors were used in United Defense transmissions, then they used permanent magnet electric motors, which were developed later.
FCS-T and FCS-W systems with hybrid electric drive
Also, United Defense has introduced two more platforms for the combat systems of the future. The first, with the designation FCS-T (tracked), is a platform originally developed by UDLP for the Lancer consortium as a possible platform deployed on C-130 aircraft for the now phased out Anglo-American FSCS / TRACER reconnaissance vehicle program.
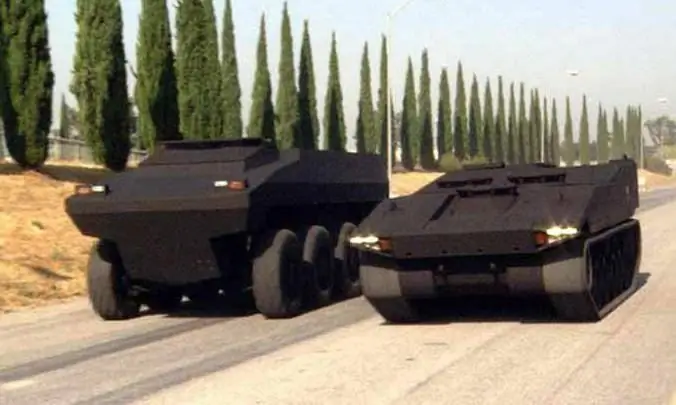
FCS-T and FCS-W with hybrid electric drive.
The FCS-T platform uses a hybrid system with three modes: hybrid, battery-only and engine-only. When operating on battery power (camouflage, silent mode), the car can travel about four kilometers, powered by a lithium battery pack (167 kW) at a voltage of 600 volts. Also, this mode is used to provide long-term (up to 6 hours at 2.5 kW) silent observation when the crew uses only electronic detection devices.
CERV - Diesel-Electric Hybrid Vehicle
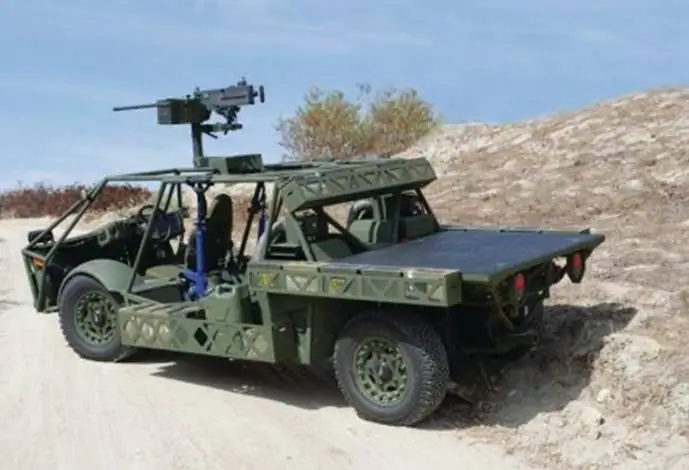
Diesel-electric hybrid vehicle CERV
The CERV Long Range Covert Vehicle is a lightweight diesel-electric vehicle with a top speed of 130 km / h. The main purpose is to carry out special operations of support, reconnaissance and target designation. The main advantage of the machine is its quiet movement and environmental friendliness. Californian company Quantum Fuel Systems Technologies Worldwide participated in the development of the car.
The four-wheel drive vehicle is powered by a Quantum Q-Force diesel-electric hybrid propulsion system consisting of a 1.4-liter diesel engine paired with a 75 kW generator and lithium-ion batteries. It powers an electric DC motor (100 kW). The unique lightweight body, developed by Quantum, has reduced the weight of the car to 2267 kilograms. There is a large loading platform at the rear of the vehicle.
As part of the work on the car, six prototypes were built. This car has a torque of 6800 Nm, which allows you to overcome water obstacles up to 0.8 meters, as well as climbs up to 60%.
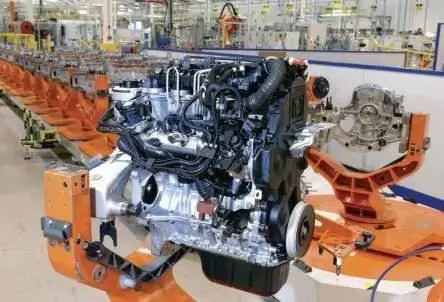
The use of the Q-Force hybrid drivetrain reduces fuel consumption by up to 25% compared to conventional vehicles of the same weight and size, and significantly reduces heat signature and carbon dioxide emissions.
When developing the CERV, the latest technologies were used that improved the battery performance and, accordingly, increased the range.
Oshkosh Defense L-ATV engineering vehicle
According to representatives of the Oshkosh Defense company, their new development confidently dominates the class of light combat engineering vehicles, combining proven technologies and advanced crew protection systems. It is possible that this car will be a replacement for the outdated Humvee wheeled armored car.
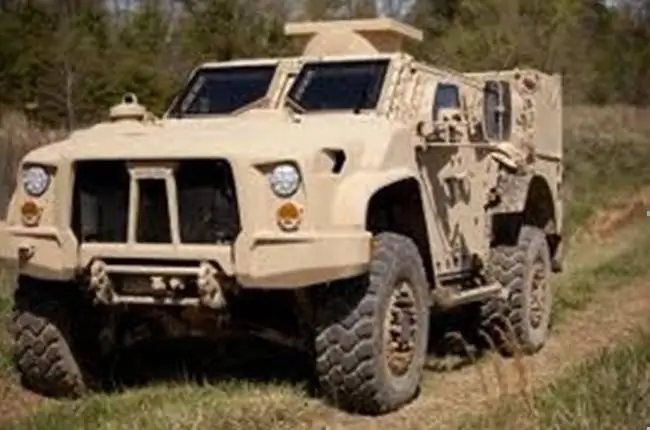
L-ATV
In developing the model, the experience gained during the clashes between Afghanistan and Iraq was used. The L-ATV is designed to provide high mobility and MRAP-level protection.
The armored car uses the intelligent, independent suspension of the new generation Oshkosh TAK-4i, which has a stroke increased by 505 mm, which increases efficiency when driving on unstable surfaces. The patented TAK-4 technology uses 20-inch wheels with independent steering.
Also worth noting is the innovative Propulse hybrid diesel-electric powertrain, which delivers an additional 70 kW of power when the car is moving, and also provides power for engineering needs when stopped. Power from a diesel generator is supplied to 4 electric motors for each drive wheel. In addition, the power plant improved fuel efficiency and power, made it possible to move almost silently over short distances.
There is a possibility of package armor equipment. Reservations can be changed depending on the tasks. In the bottom of the car, special protection against fragments and a blast wave of anti-personnel mines is installed.
Improving survivability
It's worth noting that American cars have yet to take advantage of another electric drive advantage, namely the use of some small diesel engines with generators as power suppliers. This significantly increases survivability - the vehicle does not lose mobility in the event of damage and can still return back, avoiding loss of mobility. In addition, it enables the global use of standard modern diesel engines. The unified design will make it easy to respond to machine upgrades.
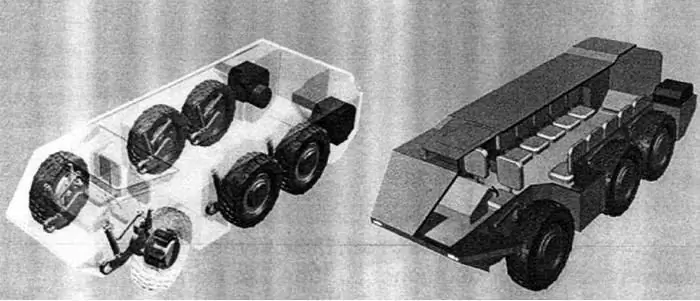
Sketch of a 6 × 6 machine with electric wheel drives and twin structural elements - diesel engine - generator
The useful volume of the machine is increased in comparison with a mechanical drive. In addition, the reduction in weight allows it to be transported by air without any problems.
As we can see, in Western countries, not just mock-ups were created, but completely ready-made platforms with a hybrid electric drive.