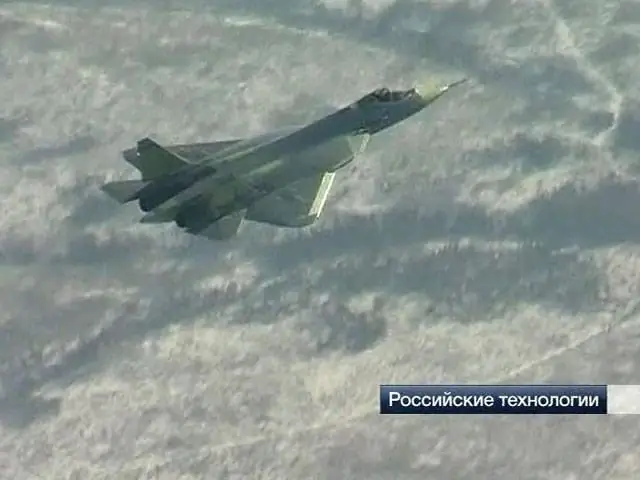
The T-50 wing is a typical composite design. Inside - aluminum honeycomb, top and bottom - about a hundred layers of carbon fiber. After laying out, this "sandwich" will go to an autoclave for 8 hours, where it will turn into a high-strength, and most importantly, lightweight aircraft part. This is how the unique "black wing" of the PAK FA - the T-50 Advanced Aviation Complex of Frontline Aviation - was born.
Like tailors, these women cut and lay the carbon fiber canvases layer by layer. This is how the unique "black wing" of the PAK FA - the Advanced Aviation Complex of Frontline Aviation - T-50 was born.
"Despite the seeming simplicity of the technology, in order to start the process of laying out, you need a special tooling. This tooling is made of composite materials, a number of requirements are imposed on it. This is also a science-intensive product," says Igor Shkarupa, scientific secretary of ONPP Technologiya.
The T-50 wing is a typical composite design. Inside - aluminum honeycomb, top and bottom - about a hundred layers of carbon fiber. After laying out, this "sandwich" will go to an autoclave for 8 hours, where it will turn into a high-strength, and most importantly, lightweight aircraft part.
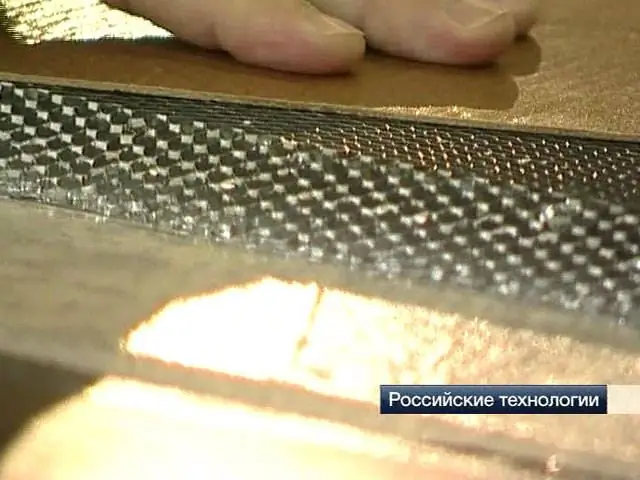
"Almost the entire fuselage and panels of this fighter are made at our enterprise. At first we had 18 products, then there were 22, and in the near future the production of the tail section of this fighter will also be transferred to us from the Voronezh aircraft building plant," says the General Director of ONPP "Tekhnologiya "Vladimir Vikulin.
A special carbon fiber material has been developed for the fifth generation fighter at the Obninsk research and production enterprise "Tekhnologiya", which is part of the "Khimkompozit" concern of the "Russian Technologies" corporation. The main technological know-how in the so-called prepregs - semi-finished materials. Their characteristics directly depend on how uniformly the carbon fiber and resin part are fused.
"These technologies are very closed in the world. For example, 2-3 countries of the world own the technology for producing good carbon fiber. And it is impossible to buy it. Either you have to develop it yourself, or you will buy a finished product, there is an airplane, etc., but you won't be able to do this anymore, "says Valery Litvinov, General Director of OJSC Moscow Machine-Building Experimental Plant - Composite Technologies.
In Obninsk, work with composite materials began back in the 70s of the last century, during the development of the unique space system "Energia-Buran". Now the enterprise has mastered the serial production of large-size head fairings for the Proton, Rokot, Angara launch vehicles from composites.
"They are not inferior in strength to metals, they have advantages in terms of durability and they are several times lighter than metals, and this is very important for space purposes, because launching a kilogram of weight into space is very expensive," says Vladimir Vikulin.
Civil aviation cannot do without composites. The new Russian mainline aircraft MS-21 will have more than 30 percent of them.
In planes made of familiar materials, passengers at altitude sometimes feel discomfort due to a lack of oxygen and pressure drops. Manufacturers promise that composite gliders will not have such negative sensations.
“If the next generation of airplanes is made of these materials, then a person will fly, as if all the time in a state at the level of the Earth. This is a completely different quality of flight,” explains Valery Litvinov.
In December last year, the Moscow region was freezing rain. Trees, roads, roofs of houses, cars were covered with a thick layer of ice. The trees that could not withstand the load began to fall, tearing the wires of the power lines. For more than two weeks, about 400 thousand residents of the Moscow region were left without electricity. The catastrophic consequences could be avoided if the wires passed above the forest level, and the power transmission towers were made of composites.
"We are developing and doing such a project in such a way that, for example, on one wagon or truck with a trailer, it would be possible to bring and mount this 50-meter support, and without any lifting means," says Valery Litvinov.
It is for such topical projects that the Engineering Research and Production Center was created about a year ago on the basis of the "Moscow Machine-Building Experimental Plant - Composite Technologies". The enterprises of the Khimkompozit concern are ready to switch from projects to serial production. Life shows that the future belongs to these materials.