To begin with, the Stirling surname is quite common in both England and Scotland. That is, if there is Stirling Castle, then why not "Mr. Stirling"? And just such a person - Scottish priest Robert Stirling, on September 27, 1816, received a British patent for an engine that had nothing to do with a steam engine! Moreover, the engine named after him turned out to be unique, as it could work from any heat source!
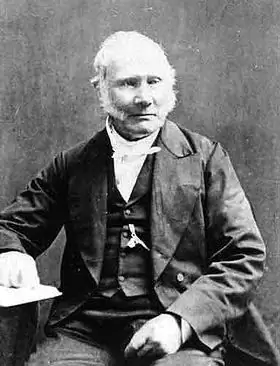
Robert Stirling.
In 1843, his son James Stirling used his father's engine in a factory where he worked as an engineer. Well, already in 1938, stiirlings with a capacity of up to 200 hp were created. and an efficiency of 30 percent.
The principle of operation of this engine consists in alternating heating and cooling of the working fluid in a completely closed cylinder. Usually the working medium is air, but hydrogen and helium, as well as freons, nitrogen dioxide, liquefied propane-butane, and even water can be used. Moreover, it remains liquid throughout the thermodynamic cycle. That is, the design of the engine is extremely simple and uses the well-known property of gases: their volume increases from heating, and decreases from cooling.
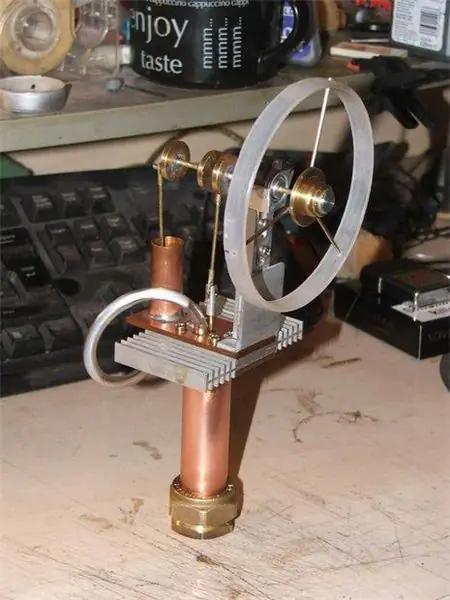
One of the many homemade sterlings.
The Stirling engine uses … the "Stirling cycle", which, in terms of its thermodynamic efficiency, is not only not worse than the Carnot cycle, but even has some advantages. In any case, it is the "Stirling cycle" that allows you to get a working engine made from an ordinary tin can in just a couple of hours.
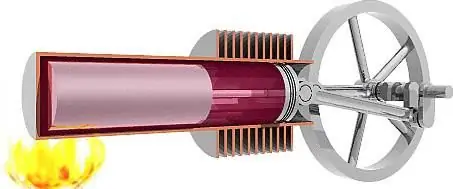
Beta Stirling Device.
The "Stirling cycle" itself includes four main phases and two transitional ones: heating, expansion, transition to a cold source, cooling, compression and transition to a heat source. Well, we get useful work in the process of expanding the volume of heated gas.
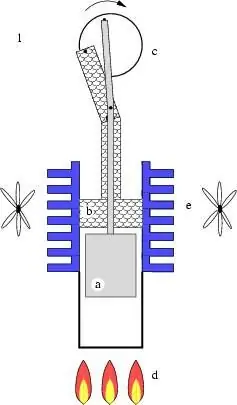
Phase 1.
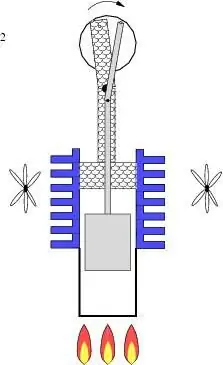
Phase 2.
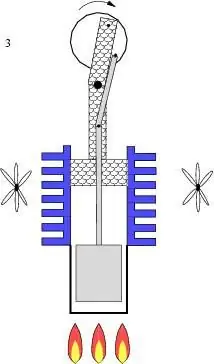
Phase 3.
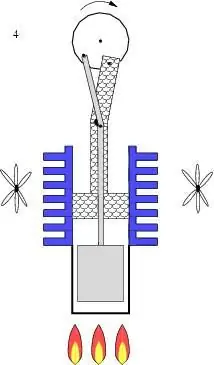
Phase 4.
The working cycle of the beta-type Stirling engine: a - displacement piston; b - working piston; c - flywheel; d - fire (heating area); e - cooling fins (cooling area).
It works like this: there are two cylinders and two pistons. An external source of heat - and they can be even burning wood, even a gas burner, even sunlight - increases the temperature of the gas in the lower part of the heat exchange cylinder. Pressure arises and it pushes the working piston upwards, and the displacement piston does not fit tightly against the cylinder walls. Further, the flywheel, scrolling, pushes it down.
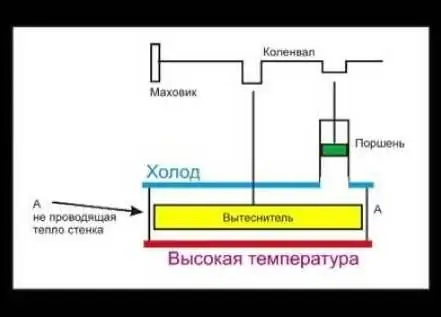
Stirling scheme from a tin can.
In this case, hot air from the bottom of the cylinder enters the cooling chamber. In the working chamber, it cools and contracts, and then the working piston rushes down. The displacement piston moves upward, and thus the cooled air moves to the bottom. The cycle is thus repeated. In the case of the Stirling, the movement of the working piston is shifted by 90 ° relative to the displacement piston.
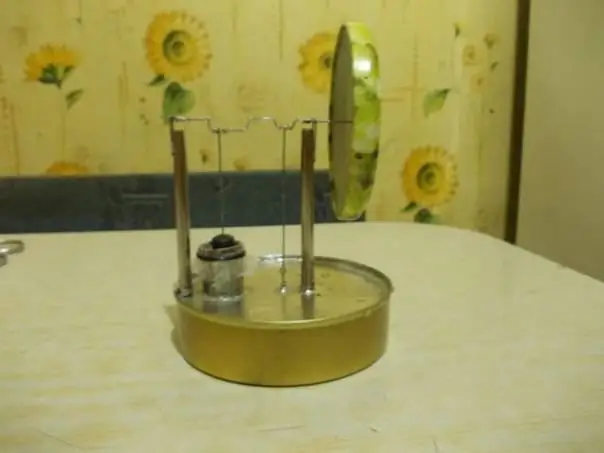
Photo of a stirling from a tin can.
Over time, many different designs of "styling" appeared, named after the letters of the Greek alphabet: alpha, beta, gamma, which have differences in the duty cycle. The fundamental differences between them are small and boil down to the arrangement of the cylinders and the size of the pistons.
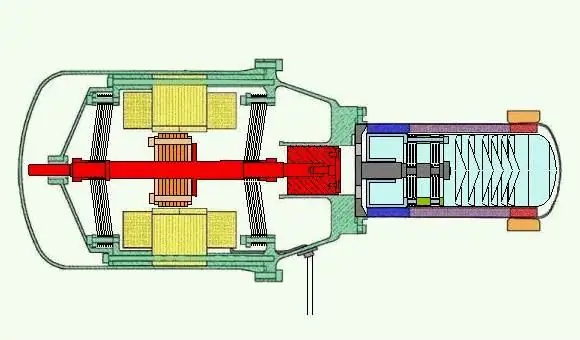
Stirling engine with linear alternator.
Alpha Stirling has two separate power pistons in different cylinders: hot and cold. A cylinder with a hot piston is located in a heat exchanger with a higher temperature, and a cylinder with a cold piston, respectively, in a colder one. The regenerator (i.e. the heat exchanger) is located between the hot part and the cold part.
Beta Stirling has only one cylinder, hot at one end and cold at the other. The piston moves inside the cylinder (from which the power is removed) and the displacer, which changes the volume of its hot zone. Gas is pumped to the hot end of the cylinder from the cold end of the cylinder through a regenerator.
Gamma Stirling also has a piston and a displacer, and two cylinders - cold (where the piston moves from which power is removed) and hot (where the displacer moves, respectively). The regenerator is external, in this case it connects the hot part of the second cylinder with the cold one and simultaneously with the first (cold) cylinder. The internal regenerator in this case is part of the displacer.
There are varieties of the Stirling engine that do not fall under these three classic types: for example, the rotary Stirling engine, in which the leakage problems are solved and there is no crank mechanism, since it is rotary.
What is good about stirlings and why are they bad? First of all, they are omnivorous and can use any temperature difference, including that between different layers of water in the ocean. Combustion in them is of a constant nature, which ensures efficient combustion of fuel, which means that its environmental friendliness is higher. Moreover, it has no exhaust. Less noise level - no "explosions" in the cylinders. Less vibration, for example, with a beta stirling. The working fluid is not consumed by styling. The design of the engine is extremely simple, it does not require gas distribution mechanisms. A starter is not needed, just as a gearbox is not needed.
The simplicity and the absence of a number of "delicate" units provide the "stirling" with an unprecedented performance for all other engines in tens and hundreds of thousands of hours of continuous operation.
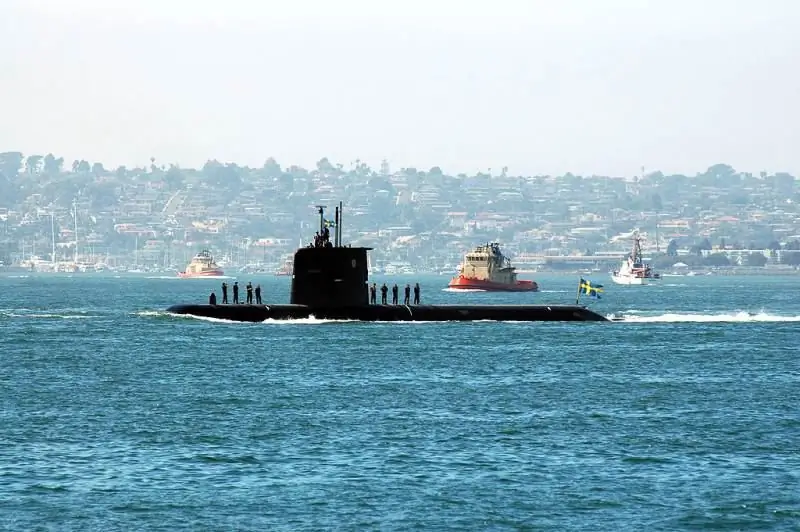
Swedish submarine "Gotland".
Stirlings are very economical. Thus, the conversion of solar energy into electricity by means of stirling gives a higher efficiency (up to 31, 25%) than heat engines operating on steam. For this, the "styling" is set at the focus of the parabolic mirror, which "follows" the sun so that its cylinder is constantly heated. It was on such an installation in California that the above-mentioned result was obtained in 2008, and now there is a construction of a large solar station on the stirlings. You can attach them to the shell of blast furnaces and then the continuous smelting of pig iron will give us a lot … cheap energy, because now this heat is wasted!
There is, in general, only one drawback to styling. It can be overheated and then it will immediately fail. In addition, to achieve high efficiency, the gas must be under very high pressure in the cylinder. Hydrogen or helium. And this is an exceptional precision of fit of all its working units and a special high-temperature grease. Well, the dimensions … the combustion chamber is not needed. Stirling cannot live without her! And this is an extra volume and a system of insulation and cooling!
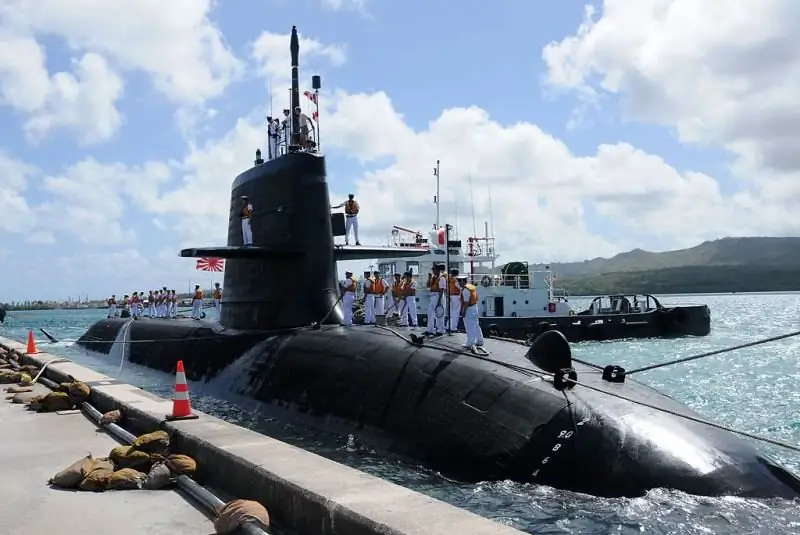
Soryu is a Japanese submarine powered by Stirling engines.
However, the change of priorities is likely to pave the way for the Stirling engines. If we put environmental friendliness at the forefront, then it will be possible to say goodbye to the internal combustion engine once and for all. In addition, great hopes are pinned on them for the creation of promising solar power plants. They are already being used as autonomous generators for tourists. And some enterprises have established the production of sterling, which work from a conventional gas oven burner. NASA is also considering options for Stirling-based power generators powered by nuclear and radioisotope heat sources. In particular, it is planned to use such styling, coupled with an electric generator, in the space expedition to Titan planned by NASA.
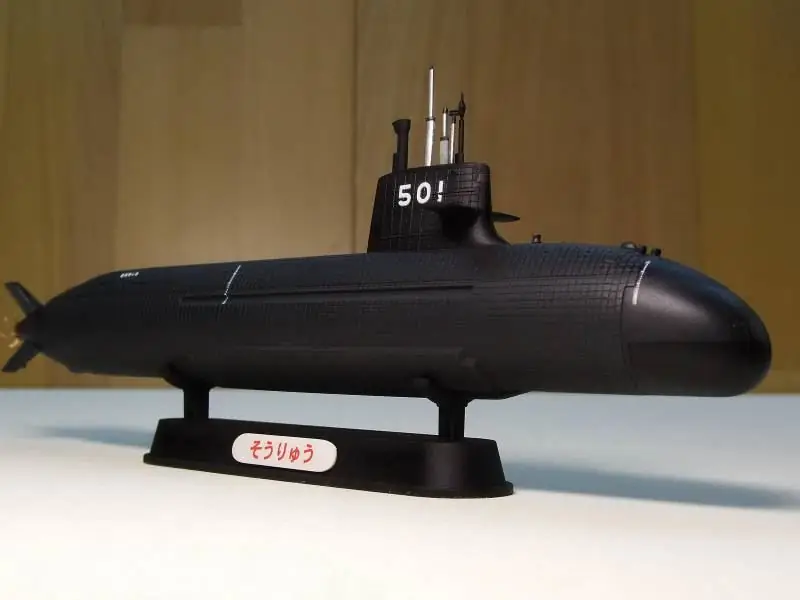
"I litter" - the layout.
It is interesting that if you start the Stirling engine in reverse mode, that is, turn the flywheel from another engine, then it will work as a refrigeration machine (reverse Stirling cycle), and it is these machines that turned out to be very effective for producing liquefied gases.
Well, now, since we have a military site, we note that stirlings were tested on Swedish submarines back in the 60s of the last century. And then in 1988 the Stirlings became the main engine of the Nakken-class submarine. With them, she was sailing underwater for more than 10,000 hours. The "Nakken" was followed by the serial submarines of the "Gotland" type, which became the first submarines equipped with Stirling engines, which allows them to stay under water for up to 20 days. Today, all submarines of the Swedish Navy have stirling motors, and Swedish shipbuilders have worked out the original technology of installing such engines on ordinary submarines, by cutting into them an additional compartment with a new propulsion system. They run on liquid oxygen, which is then used to breathe in the boat, and are noted to have very low noise levels. Well, the above-mentioned shortcomings (size and cooling problem) on a submarine warship are not significant. The example of the Swedes seemed to the Japanese worthy of attention, and now the Stirlings are also on the Japanese submarines of the "Soryu" class. It is these engines that are considered today as the most promising all-mode single engines for 5th generation submarines.
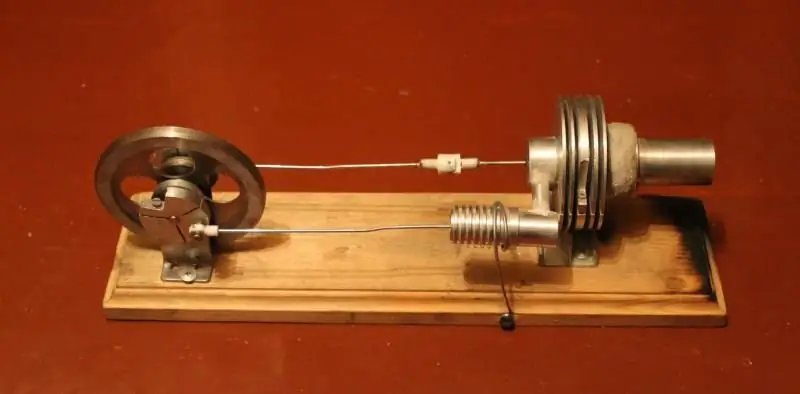
And this is how the styling of a student of the Penza State University Nikolai Shevelev looks like.
Well, now quite a bit about what kind of … "bad youth" we have. I come to students - future engine engineers on September 1, ask them traditional questions, what they read (practically nothing!), What they are fond of (with this the situation is not much better, but mostly the legs are busy, not the head!), What technical journals are they known - "Young Technician", "Model Designer", "Science and Technology", "Popular Mechanics" … (none!), and then one student tells me that he is fond of engines. One in 20, but that's already something! And then he tells me that he made the Stirling engine himself. I know how to make such an engine out of an ordinary tin can, but then it turned out that he did something much more effective. I say: "Bring it!" - and he brought. "Describe how you did it!" - and he described, and I liked his "essay" so much that I am presenting it here without any changes or abbreviations.
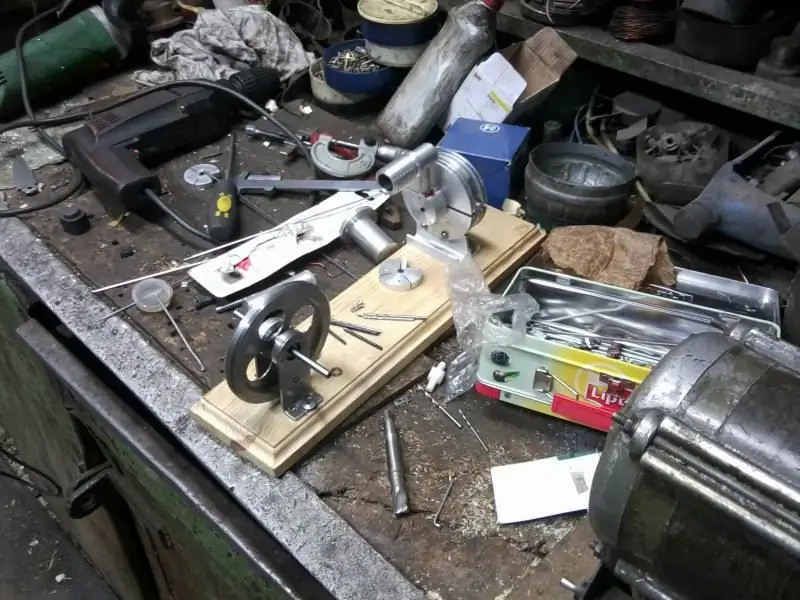
The beginning of work is “creative chaos”.
“I've always liked the technology, but especially the engines. I am engaged in maintenance, repair and customization with great interest. Having learned about the Stirling engine, I was fascinated by it like no other engine. The world of styling is so diverse and large that it is simply impossible to describe all possible options for its execution. No other engine will give such a variety in terms of design, and most importantly, the ability to make it yourself.
I had ideas to make a model of an engine from a tin can and other improvised means, but it was not in my rules to do "anyhow and from what it got". Therefore, I decided to take this task seriously, to begin with preparing theoretically. I studied the literature on the Internet, but the search did not bring the desired result: review articles and videos, the lack of drawings for the models of this engine. The finished models were sold at too high a price. In addition, a great desire to make everything yourself, understand the principle of operation, debug and conduct tests, get useful work from this engine and even try to find its use in the economy.
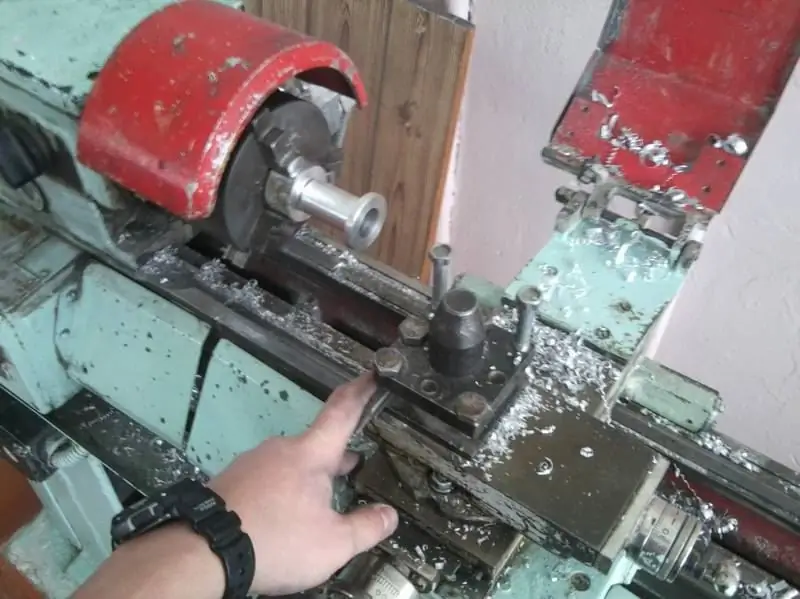
"Turning business!" (A clever student, he filmed the whole process of work as a keepsake. Present, citizen, documentary photographic evidence … and here they are!)
I asked around on the forums, and they shared the literature with me. It was the book "Stirling Engines" (Authors: G. Ryder and C. Hooper). It reflected the whole history of this type of engine building, why the rapid development stopped, and where these engines are still used. From the book, I learned in more detail all the processes occurring in the engine, found the answers to the questions of interest. It was interesting to read, but I wanted to practice. Of course, there were no drawings of garage models, as well as on the Internet, well, of course, except for a model from a can and foam rubber.
To my great happiness, the person who sold the styling models posted a course on making such models, he put it up at that time for $ 20, I wrote to him and paid for the course. After watching all the videos, in each of which he explained a certain type of styling, I decided to do exactly the high-temperature styling of the gamma type. Since he interested me with his design, characteristics and appearance. From the video course, I learned the approximate ratio of the cylinder diameter, piston diameters, what clearances, roughness should be, what materials to use in the manufacture, some of the nuances of construction. But nowhere were the sizes of the author's engines, only approximately the ratio of the sizes of the nodes.
I myself live in a village, one might say in the suburbs, my mother is an accountant, and my father is a carpenter, so it was somehow inappropriate to turn to them for advice on building an engine. And I turned to my neighbor, Gennady Valentinovich, for help, he worked at the now collapsed KZTM plant in Kuznetsk.
In general, the next day Gennady Valentinovich brought me an aluminum blank about 1 m long and about 50 mm in diameter. I was very happy, sawed off the blanks I needed, and the next day I went to school to try to sharpen the heater and refrigerator for my internal combustion engine. I sharpened on a training lathe (on which grandfather Lenin worked).
Of course, there was no accuracy, the outer part of the heater turned out to be pretty good, but the cylindrical part itself under the piston was on a cone. Trudovik explained to me that the boring cutter bends, since the machine for such things is rather small and weak. The question arose what to do next … It was lucky that my mother at that time worked as an accountant at a private enterprise, which was a former car repair plant. Valery Aleksandrovich (the director of this plant) turned out to be a wonderful person and helped me a lot, I was already provided with a professional Soviet machine and a turner who helped me. Things went more fun, and literally a week later, almost everything was ready, the assembly of the motor began. There were interesting moments in the construction, for example: the shaft, onto which the flywheel was pressed, was given to the precision mechanics workshop at another plant (in order to obtain the necessary accuracy for the bearings); the refrigerator was sharpened on a lathe, and the places for fastenings were made with a milling machine, the flywheel was ground on a grinder. It was very interesting and exciting for me. The workers at the factory thought I was a student and am writing some kind of scientific work. I sat at the factory until late in the evening, and they brought me home in Valery Alexandrovich's official car. The engine was started up in a large circle of factory workers, everyone was very interested. The launch was successful, but the engine was running poorly.
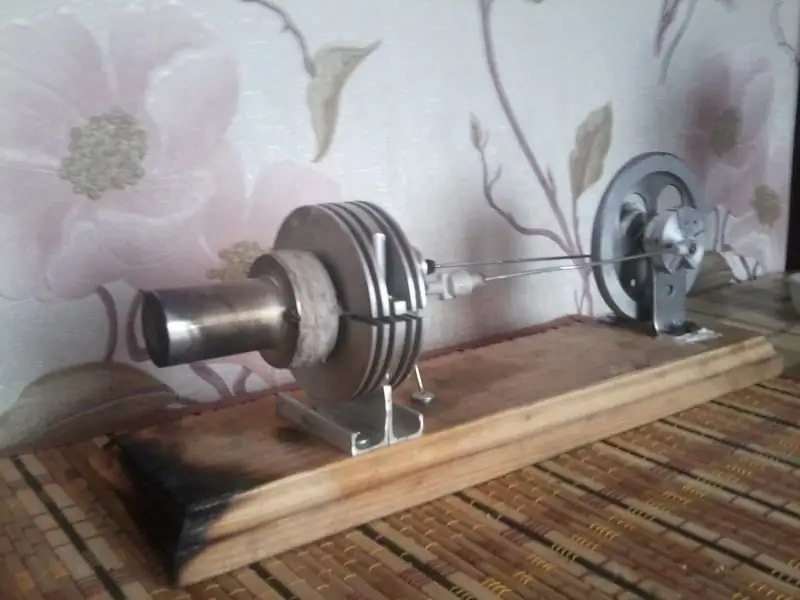
The result crowns the deal! The corner of the stand was burnt during testing.
Shortcomings were revealed, the plastic hinges were replaced with fluoroplastic ones, the flywheel was lightened and balanced, the piston received a fluoroplastic attachment for lower heat transfer, and the refrigerator became with a larger cooling area. After fine-tuning, the engine has significantly improved its technical performance.
I myself was delighted. When friends come to my house, the first thing they do is come up to him, ask him to start. Gennady Valentinovich drove to show the styling to his work, everyone was very interested, they didn't even have to call someone, everyone came up, looked, and asked."
The name of the young man is Nikolai Shevelev, and he is the head of the group. I took him to the dean, and the three of us had a very good talk. And then I remembered the statistics that only 2% of the world's population is enough to advance humanity along the path of scientific and technological progress. I counted the total number of students and realized that … there is no need to worry too much. With people like Nikolai, progress will still be guaranteed for us!