CNIM did not stop there and developed the PFM F3 family, which will be released in several configurations, all of which will be able to withstand the track load of MLC85 (G - tracked) and wheel load MLC100 (K - wheel). The F3 bridge pontoon park is a completely new project. Although aluminum remained the base material, improvements in materials and welding technology have allowed CNIM to obtain a module with the same mass but increased payload. The same applies to the ramps, with the same dimensions they are stronger and can withstand heavy loads, up to MLC100 (G) and up to MLC120 (K). The F3 system will also receive more powerful engines, which are not yet known, as the company is in the process of selecting them. In addition to the basic F3 variant, the company offers the F3XP variant, based on a module (section) with a length of 7 meters (the standard one is 10 meters long), which can be transported by an 8x8 truck without a trailer. A middle ramp was also developed, two of them can be transported on the same truck; over time, the machine will be equipped with a DROP palletized load system.
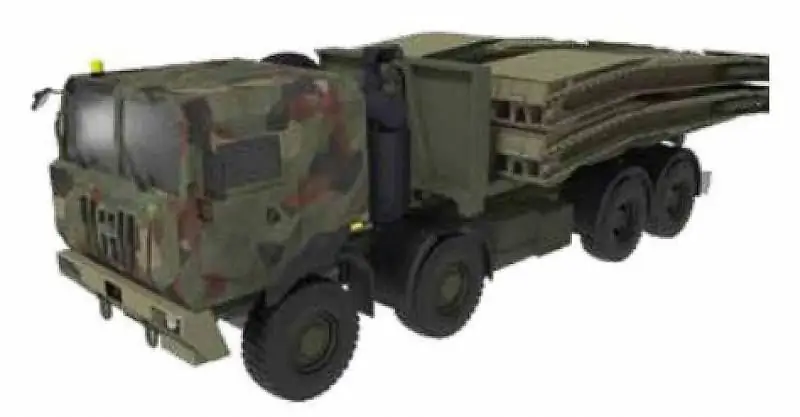
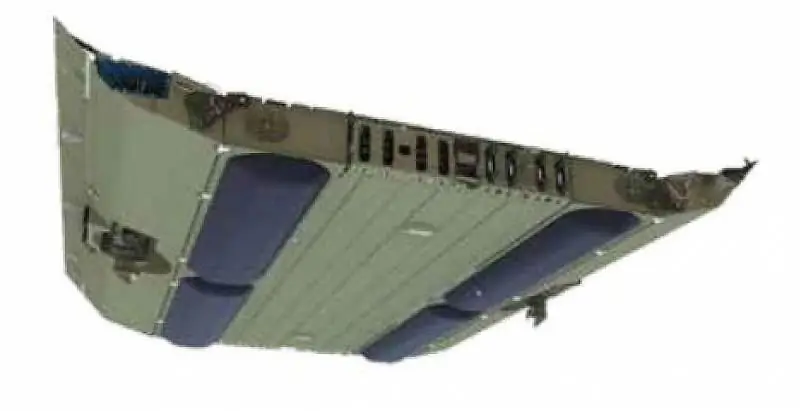
According to CNIM, this meets the needs of many northern European countries, which tend to deploy their bridges on trucks of this type without the use of trailers. From an expeditionary point of view, the deployment of the F3XP ferry 21 meters long requires 4 trucks - three for modules and one for ramps. To carry heavier loads, CNIM has developed additional rigid floats to improve buoyancy, making the bridge capable of supporting the MLC100 (G) and MLC120 (K) loads. The floats are transported on a separate truck and, before launching, are installed under the floating modules. This configuration is known as the F3MAX. Shorter floating elements are also being developed for installation with the F3XP bridge, resulting in the lifting capacity of the MAX version. Last but not least, the PFM F3D has a D stands for drone. Its modules are equipped with a navigation system and an automatic section clutch system, which makes it possible to assemble the bridge without people on board. Both the F3MAX and F3D use a long ramp designed for bridges rather than ferries. In terms of compatibility, F3 modules can be fitted with locking systems that are compatible with the Improved Ribbon Bridge.
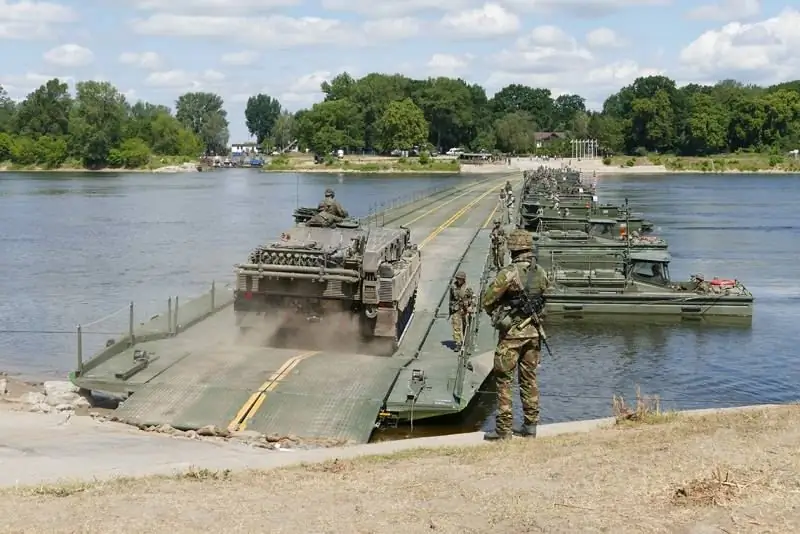
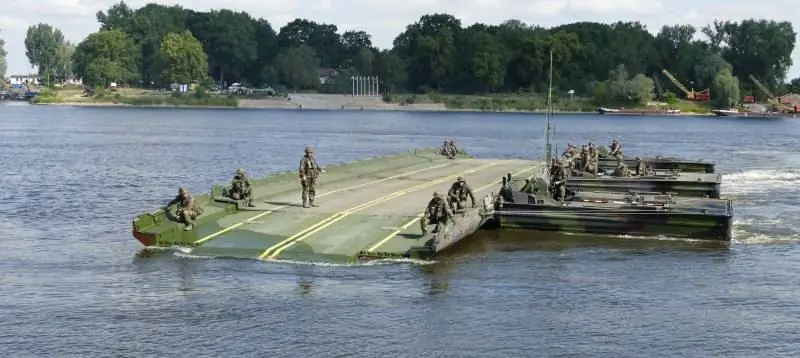
CNIM began development of the F3 and F3XP systems in January 2019, while the prototype is slated to appear in mid-2020, possibly by the opening of the Eurosatory exhibition. F3MAX elements will appear six months later. F3D development will begin when all other development is complete; however, modules for it are already being designed as the integration of relative positioning and automatic clutch systems has begun.
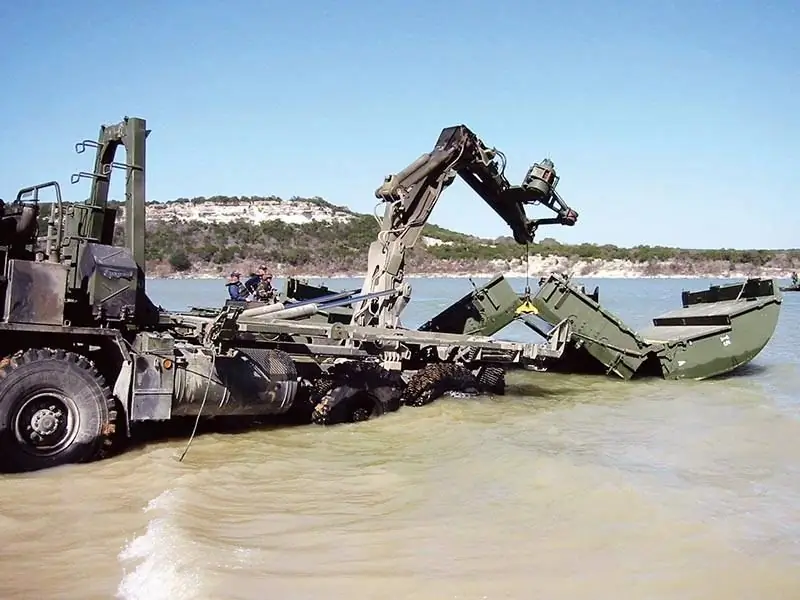
With regard to floating modules, the most popular is undoubtedly the improved IRB (Improved Ribbon Bridge) by GDELS, which is used by the armies of the USA, Germany, Australia and Sweden, and more recently also Iraq and Brazil. The main element of the IRB is an internal span of 6.71 meters long and 3.3 meters wide in transport position and 8.33 meters when unfolded. The sections are lowered into the water in a folded state and unfold on the water. In bridge configuration, they support the MLC80 (T) and MLC96 (K) loads on a 4.5-meter single-lane carriageway; two-way traffic is allowed with a carriageway width of 6, 75 meters, but the load is limited by the MLC20 (T) and MLC14 (K). The ramps are attached to the ends of the bridge; at the same time, for every 2-3 spans, as a rule, a tug boat is required, which allows work at current speeds up to 3.05 m / s; 13 internal and two ramp spans make it possible to build a bridge 100 meters long on average in 30-45 minutes. Three internal spans and two ramps are required to build a ferry with a carrying capacity of MLC80 (G) / 96 (K), which can be ready in 15 minutes. The IRB is compatible with the aforementioned MZ pontoon bridge system, as well as the 70's Standard Ribbon Bridge and Foldable Float Bridge, capable of taking the MLC60 load. During the already mentioned Anaconda 2016 exercise, a bridge with a record length of 350 meters was built by the engineering units of the American and German armies using the IRB bridges, and the Dutch engineers using the SRB.
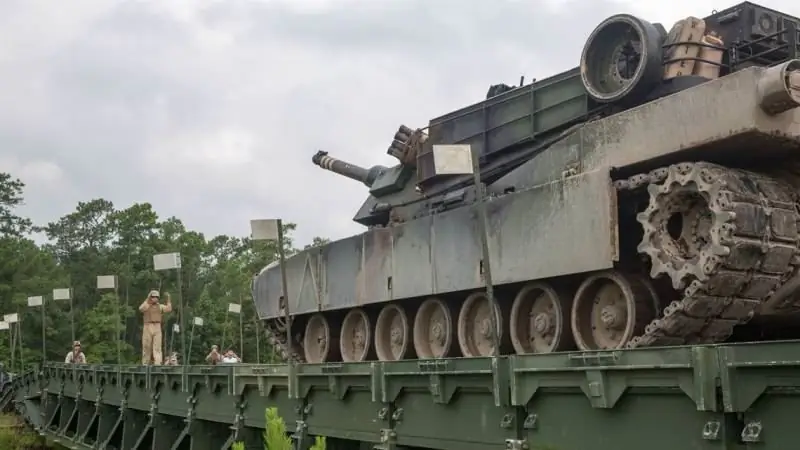
The Bundeswehr expires on the IRB and M3 bridges at the same time, therefore, the replacement of these systems should begin soon. Apparently, Germany wants to acquire a system that would combine the characteristics of the M3 and IRB bridges, and this is a serious task for the designers of the GDELS company.
The company emphasizes that its MLC classification is based on the STANAG 2021 standard and that upgraded tanks, such as the M1, Challenger 2 or Leopard 2, can be loaded and transported by its MLC 120 (G) class bridge systems and more.
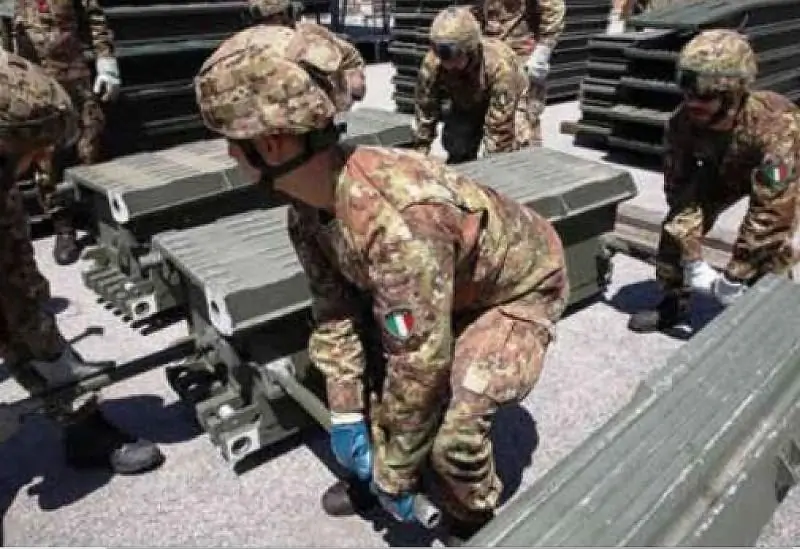
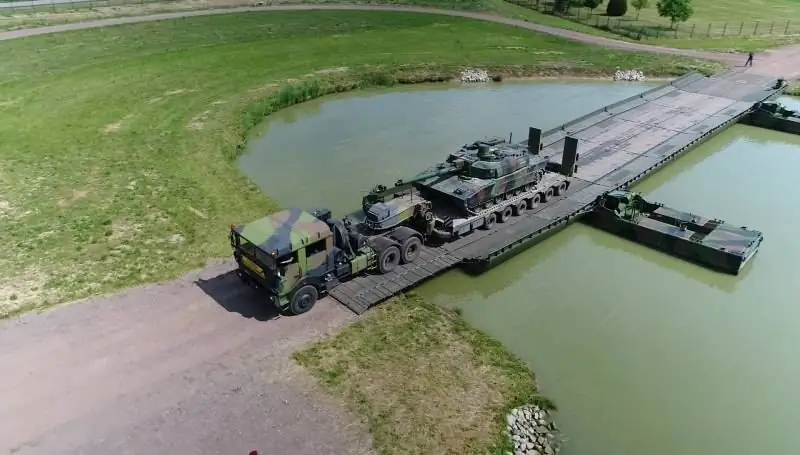
Four years ago, the French company CEFA studied the trends in bridge construction and decided to develop a new bridge very similar to the Russian Volna pontoon bridge vehicle or the German IRB bridge. As a result, the Steel Ribbon Bridge (SRB) prototype was manufactured in early 2019. The keyword “steel” refers to the inner sections, while the IRB bridge has these sections made of aluminum. The French SRB pontoon bridge system is of course stronger (but also heavier) and can handle the loads of the MLC85 (G) and MLC120 (K). The dimensions of its internal spans are very close to those of the IRB bridge, although the mass is greater, 7950 kg versus 6350 kg. Another key feature is that the guidance system is mounted on a pallet rather than directly on the truck, which allows the system to be quickly installed on any heavy truck equipped with a 10 ton PLS automatic loading system. The locking system allows the SRB section to be used in conjunction with IRB modules, thus ensuring interoperability. Holding in a certain position is also provided by tugboats. CEFA offers its Vedette F2, whose two jets provide a total thrust of 26 kN, but the SRB bridge can work with any boat that provides sufficient thrust. The Vedette F2 is powered by an air-cooled Cummins diesel engine for easy maintenance. The number of spans and the steering time of ferries and bridges is almost the same as for the IRB bridge. The SRB system has already been tested in the French army. CEFA will finalize the new bridge for series production scheduled for 2020.
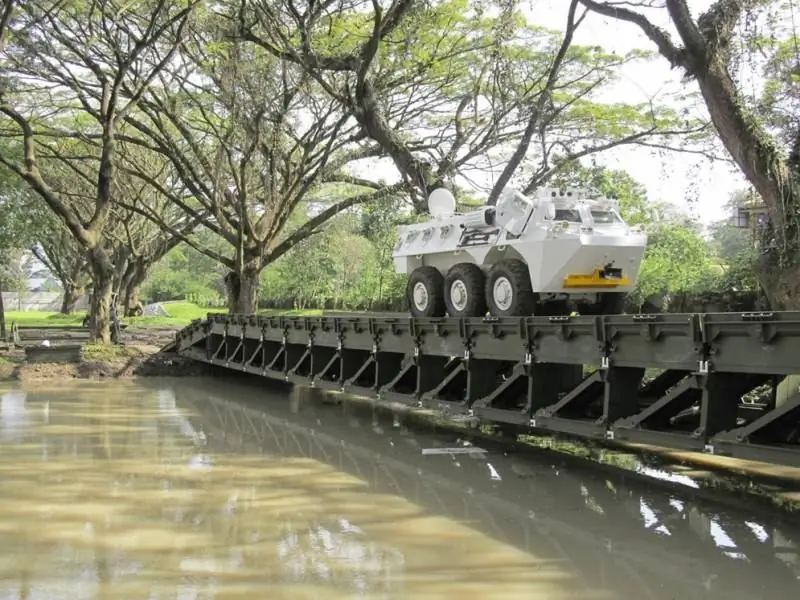
Assault bridges
Originally manufactured by the British company Fairey Engineering Ltd (now WFEL), the Medium Girder Bridge (MGB) is arguably one of the most widely used bridge systems in the West. More than 500 MGB systems have been sold to 40 countries and WFEL is currently supplying MGB systems to African countries. The heaviest elements of the bridge, designed from the outset for manual assembly, can be carried by six soldiers. It is available in five different configurations: Single Span, Multi-Span, Double Storey with Link Reinforcement Set (LRS), Floating and MACH (Mechanically Aided Constructed by Hand). The soldier for the construction of the last option is required half as much. In general terms, in this case, as a rule, a roll beam is used to reach the opposite bank, and an outward bend is attached to the front of the span (an element that lengthens the span for longitudinal sliding of the bridge). Typical construction time for a single-tier 9.8 meter long MLC70 bridge is 12 minutes during the day and triples at night; the bridge builder team should consist of 8 soldiers and one sergeant. It takes three times as many people and 40 minutes during the day and 70 minutes at night to assemble a two-tiered MLC70 class bridge with a length of 31 meters. The floating version uses pontoons made of aluminum alloy for shipbuilding purposes. The single-deck floating MGB is built in a continuous pattern, allowing one bridge span to be added every 30 seconds, while the double-deck floating MGB, capable of handling extreme shores of up to 5 meters, can be constructed in a multi-span or continuous pattern, depending on the width of the obstacle.
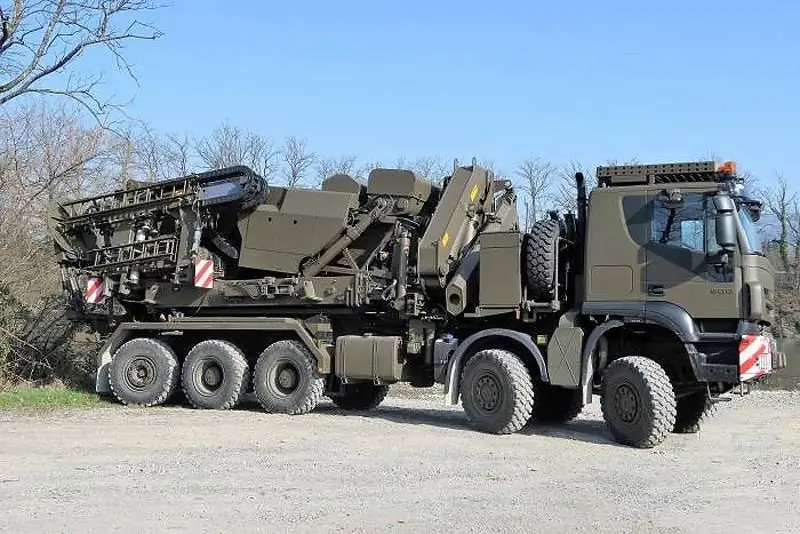
Taking into account the needs of the expeditionary force, WFEL has developed the APFB (Air Portable Ferry Bridge), a lightweight, collapsible solution capable of providing bridges or wheel and tracked ferries with the MLC35 capacity. The system can be transported seamlessly by land, air or sea using its own folding trailers, pallets or ISO containers. It can be thrown by an C130 military transport aircraft, suspended from a helicopter, or even dropped on special platforms. The complete APFB system consists of six standard and two special pontoons, a reduced number of pontoons (at least three) is required for specific tasks. A bridge with a span of 14.5 meters and a width of 4 meters, 12 engineers and one sergeant are able to build in 50 minutes. It takes twice as many engineers and two hours to build a reinforced version of the APFB with an increased span of 29.2 meters. As for the configuration of the ferry, it includes six pontoons, two of which are powered, it takes 14 soldiers, two sergeants and two hours to build it.
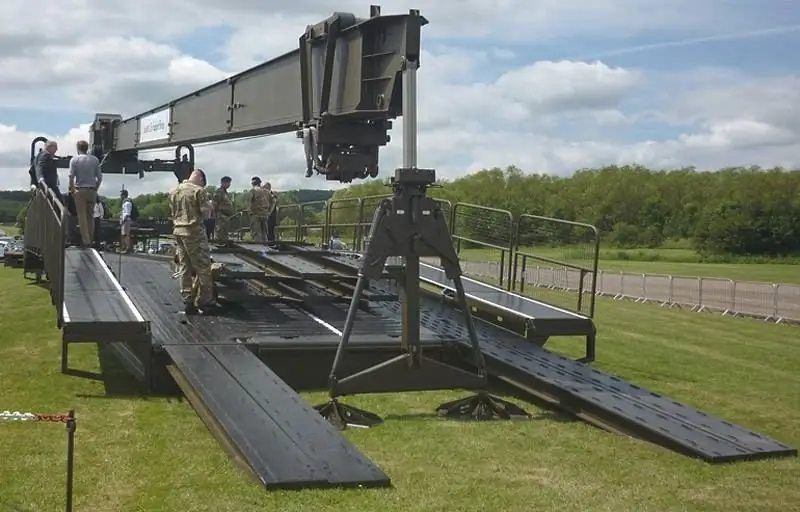
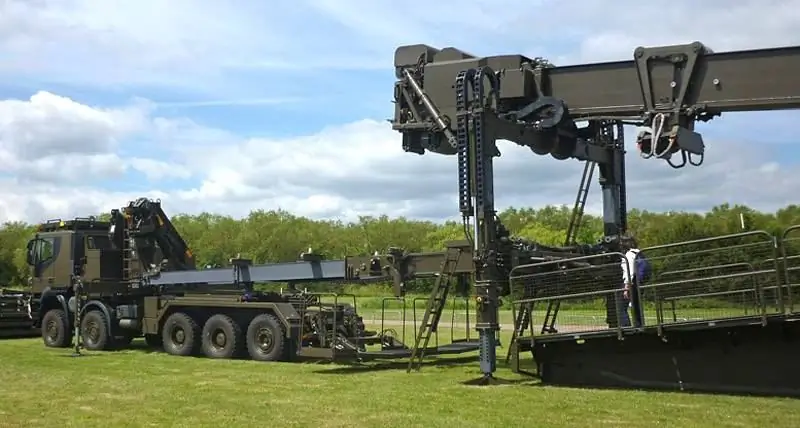
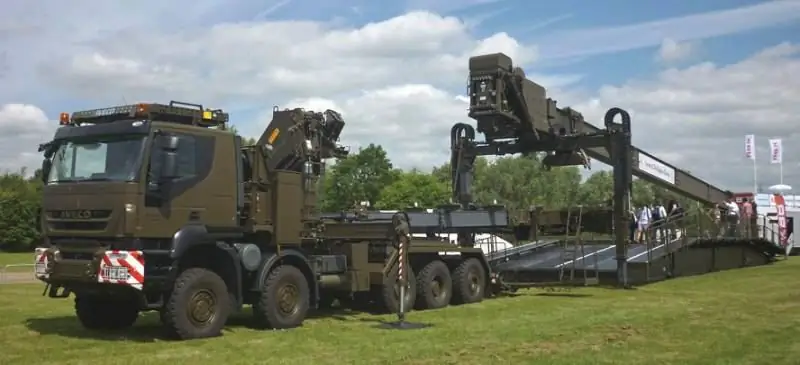
However, the newest system offered by WFEL is the DSB (Dry Support Bridge), which is deployed using a bridge-laying vehicle mounted on various military-standard chassis, usually a heavy truck; the American army uses Oshkosh М1075 10x10 for these purposes, the Swiss army uses Iveco Trakker 10x8 and Australia RMMV - НХ 10x10. The truck-mounted stacking system pushes the beam forward, which is thrown to the opposite bank, the bridge modules are moved forward on the beam suspension until the bridge reaches the opposite bank, then the beam is disassembled. The maximum span of this MLC120 class bridge is 46 meters, the width of the roadway is 4.3 meters, it takes 8 soldiers and less than 90 minutes to build the bridge. The DSB system has already been acquired by the USA, Turkey, Switzerland and Australia, the latter recently purchasing both DSB and MGB systems for its Land 155 project. In accordance with TDTC 1996, the 46 meter DSB was tested with MLC120 (K) and 80 (D) loads; its tests continue in accordance with the STANAG 2021 standard in order to determine a higher MLC class.
BAE Systems has been active in the field of military bridge construction for many years, producing the MBS (Modular Bridging System) modular bridge system. In July 2019, Rheinmetall and BAE Systems created a joint venture RBSL (Rheinmetall BAE Systems Land) to design military vehicles, including bridge systems. In 1993, the British Army ordered the MBS system in two versions: the Close Support Bridge (CSB), deployed from the Tank Bridge Transporter tractor, and the General Support Bridge (GSB); these systems have many elements in common.
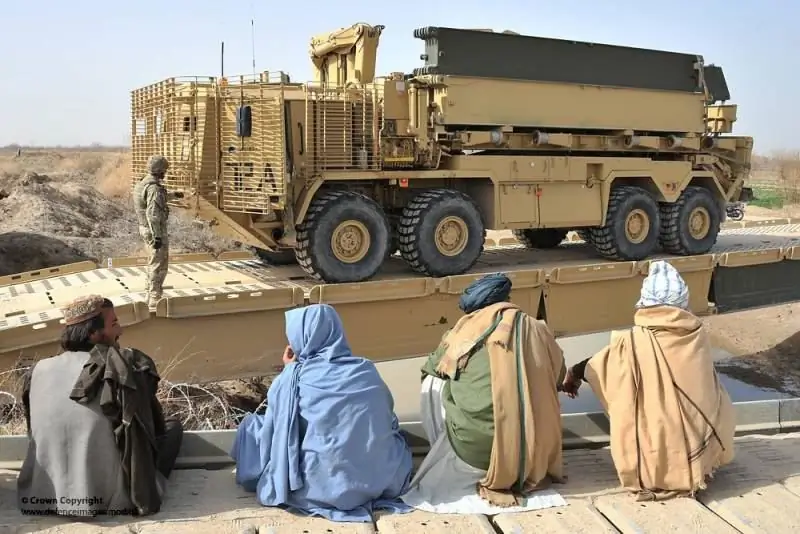
The GSB system includes panels with a length of 2, 4 and 8 meters, ramps of 8 meters and auxiliary components, the system allows you to assemble bridges of various configurations. The complex includes two types of vehicles, the BV (Bridging Vehicle) bridge carrier and the ABLE (Automotive Bridge Launching Equipment) bridge guidance equipment, both vehicles are available in armored and unarmored versions. The ABLE vehicle is used to guide the bridge. First, slide the rail to the opposite side of the obstacle, then the assembled bridge sections are attached with wheeled carts to the rail and move forward until the bridge reaches the opposite bank, then the rail is removed. Interestingly, the opposite bank can be three meters higher or lower than the bank from which the bridge is built. The ABLE car parks backwards to an obstacle, while the BV cars can park either side-by-side or in a queue, the second solution allows working in confined spaces. The single-span Single Span Unreinforced GSB system can connect an obstacle with a width of 16 or 32 meters, construction is carried out by one ABLE machine and two BVs. To increase the length, the Single Span Reinforced configuration is available, which allows the construction of bridges with a length of 34, 44 and 56 meters, for this, four, four and five BV vehicles are involved, respectively, carrying the necessary elements. If there is a suitable support surface at the bottom of the obstacle, a two-span Two Span Fixed Pier bridge with rigid support can be built. The unreinforced configuration allows the construction of bridges with a length of 30 or 64 meters, the same lengths are provided when using a floating support. All of these configurations require one ABLE and five BVs to transport the bridge structures. A minimum of 10 people is required, and a maximum of 15 people for the construction of a two-span bridge with floating support. RBSL guarantees that its GSB system will withstand 10,000 crossings with MLC70 (G) or 6,000 crossings with MLC90 (G). The company has integrated a usage monitoring system into the main elements, which transmits data wirelessly to a computer, which makes it possible to monitor the fatigue stresses of the bridge components.
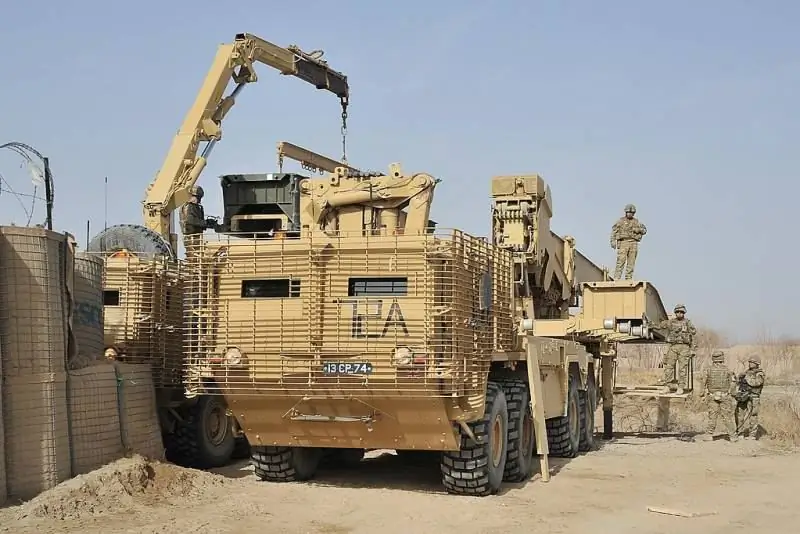
The company is also developing a new bridge that will meet the requirements of the British Army's Tight Project. This RBSL solution uses the existing guidance systems for the CSB and GSB bridges; all new bridges are designed and tested as part of the evaluation phase of the Tight Project. This new MBS bridge meets the requirements of the British Department of Defense for the MLC100 (D) payload class. The bridge panels have been tested in all respects at the RBSL test site in Telford. The requirements of the Ministry of Defense for wheeled vehicles are still being determined.
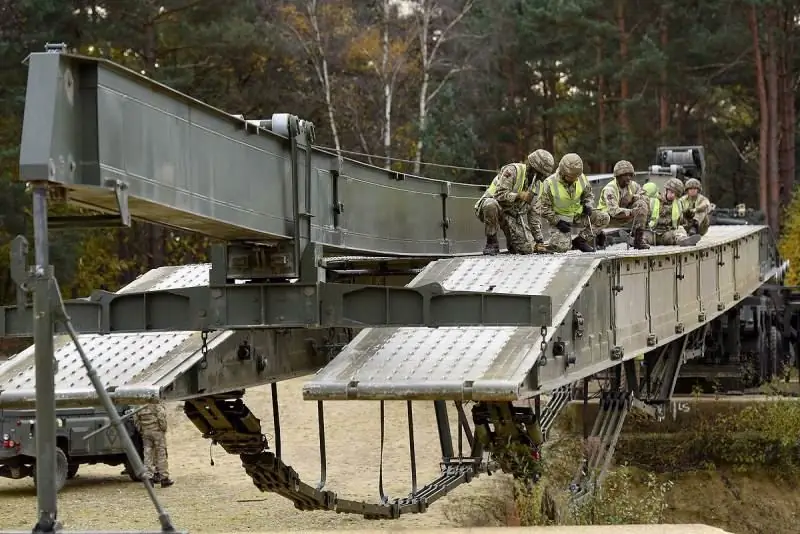
RBSL is also working to enhance the capabilities of the MBS system, aiming to achieve a length of 100 meters in a multi-span configuration. To this end, RBSL proactively analyzed the concept of the General Support Bridge with a span of 100 meters. Also under development are panels that can be used to build a 65-meter-long MLC30 (D) class bridge with guidance mechanisms made of carbon fiber. RBSL is also continuing to work on longer span bridges and guidance systems, although this is not part of Project Tight requirements.
In 2010, Turkey purchased two MBS systems from BAE Systems and would like to acquire five more such systems. The Turkish company FNSS will act here as the parent company, and the British RBSL will supply the bridge elements.