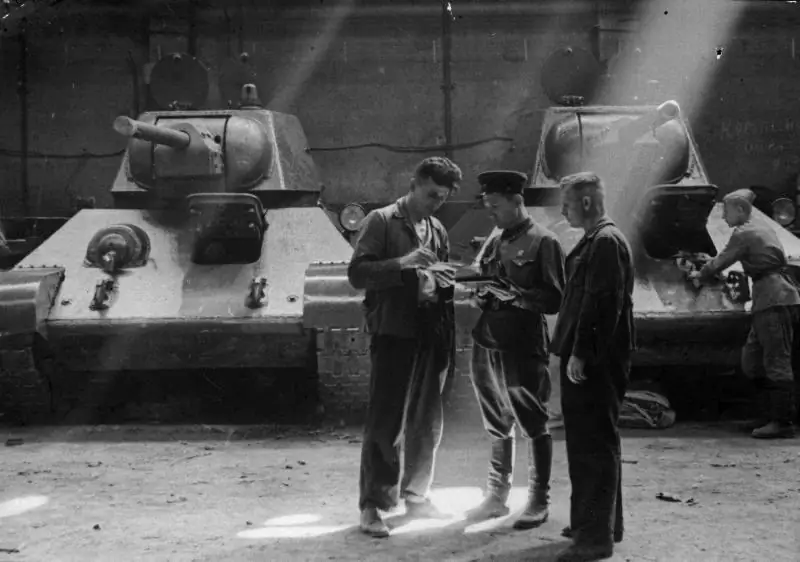
All to the war with a crack
The highly solid homogeneous 8C armor steel, which became the main one for the T-34 medium tank, introduced a lot of difficulties in the production process. It should be noted that such solid armor was used on tanks only in the Soviet Union during the entire Second World War. And in this, of course, there were both positive and negative sides. In the previous parts of the cycle, we have already discussed the numerous cracks accompanying the welding of the hulls and turrets of Soviet medium tanks. At the same time, heavy KV and then ISs were deprived of this: the more ductile armor of medium hardness tolerated excessive stresses when welding parts much easier. Since the beginning of 1942, Armored Institute engineers have proposed a set of measures to simplify armored hull production and modernize welding technology. It was decided not to weld some nodes at all: for example, the fastening of the rear and front frames was transferred to riveting. In many ways, this was a borrowing after a thorough study of German armored vehicles.
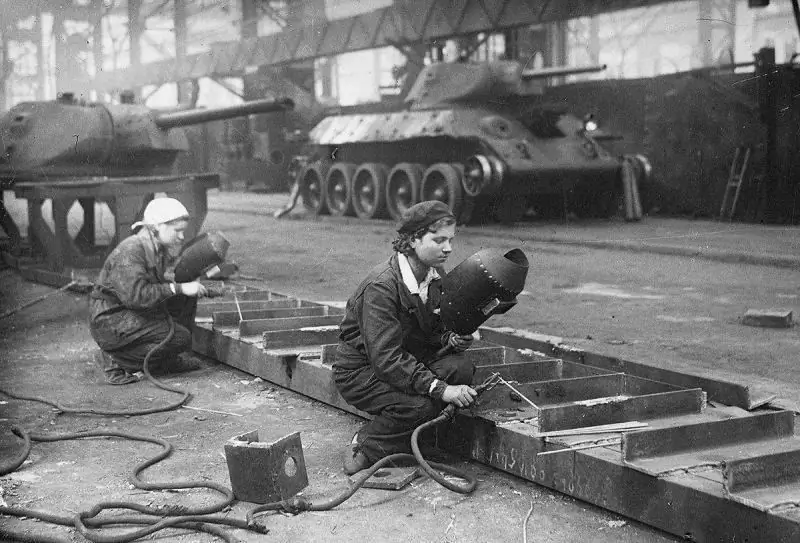
The frontal and side parts of the tank were now welded at the request of TsNII-48 only with austenite electrodes, better suited for difficult-to-weld grades of ferrous metal. In total, now up to 10% (or more) of all electrodes consumed for an armored vehicle were austenite. If you focus on the data given in Nikita Melnikov's book "Tank Industry of the USSR during the Great Patriotic War", then about 400 electrodes were consumed for one T-34-76, and 55 of them were austenite. Among the requirements for the use of such electrodes was a ban on their operation at high current modes - up to 320A. Exceeding this indicator threatened with high heating of the weld area with subsequent deformation during cooling and the formation of cracks. Please note that functions similar to the domestic "Armored Institute" in Germany were performed by the 6th Department of the Armaments Directorate of the Ground Forces. It was to him that tank factories were supposed to submit the methods of welding hulls and turrets for approval in writing. Specialists of the 6th Department, in turn, checked the submitted materials for compliance with the temporary specifications for welding armor T. L.4014, T. L.4028 and T. L.4032. These requirements were calculated for welding German armor with a thickness of 16 to 80 mm. As already mentioned in the article "Welding of Tank Armor: German Experience", automatic welding was not used in Germany. This, of course, seriously slowed down the speed of the German tank industry, but in the Soviet Union there were some problems with welding machines. Along with the undoubted high quality of the weld, the automation of welding required high-quality filler materials and strict adherence to the work technology. However, this was an inevitable price to pay for the introduction of a revolutionary production method, which had such a significant impact on the quality and speed of tank assembly.
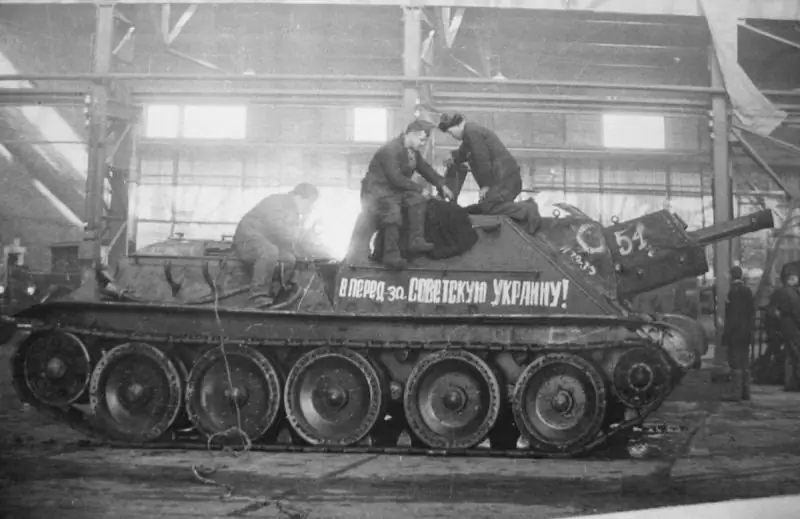
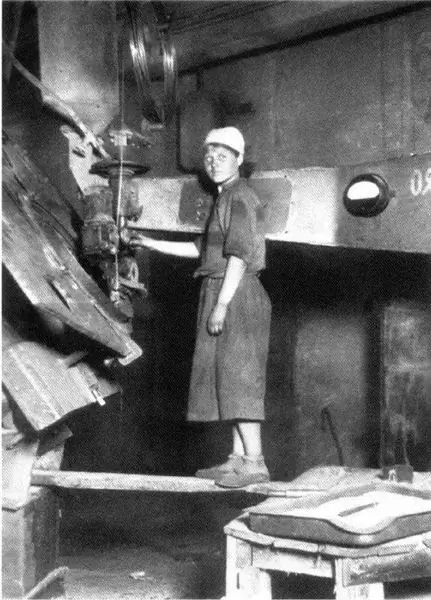
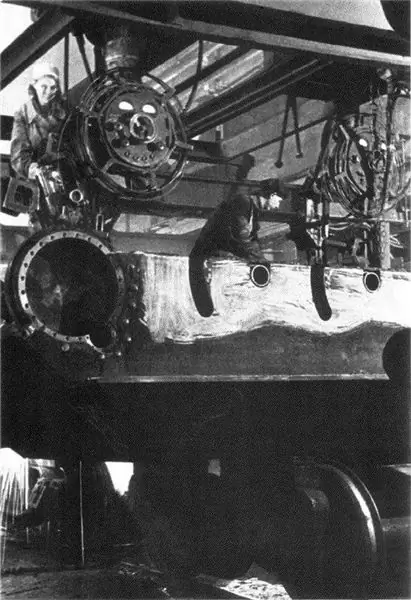
If the main electrode and filler wire turned out to be excessively contaminated with sulfur, carbon and phosphorus (or, conversely, it lacked manganese or manganese oxide), this led to the formation of cracks directly in the weld. It was important to carefully prepare the products to be welded under flux. The requirements were tough: the parts had to be of the correct dimensions, without violations of tolerances. Otherwise, for welding, the part on the slipway had to be "pulled", thereby creating serious internal stresses. And a simple non-observance of the strength and voltage of the welding current led to the defectiveness of the seams: porosity, nostrils and lack of penetration. Given the low level of qualifications of workers allowed to access welding machines, it is easy to believe in the possibility of such a marriage. All highly qualified welders were engaged in manual welding and could not influence the welding quality of "Paton's machines". Although they were involved in correcting defects in welding machines.
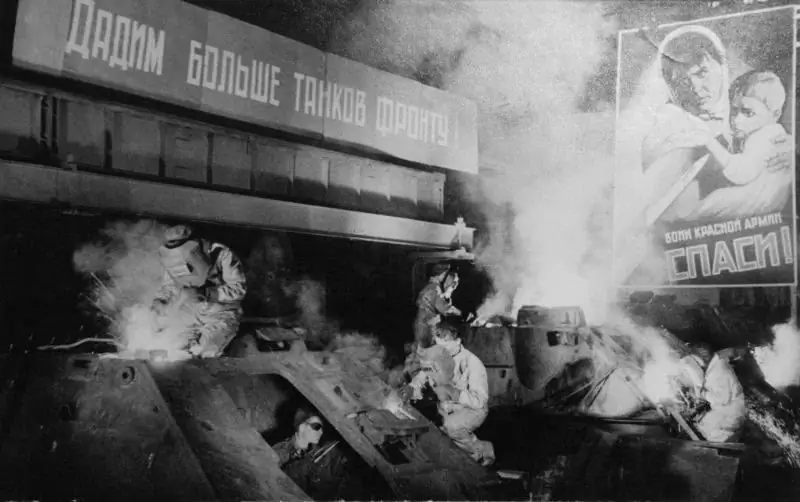
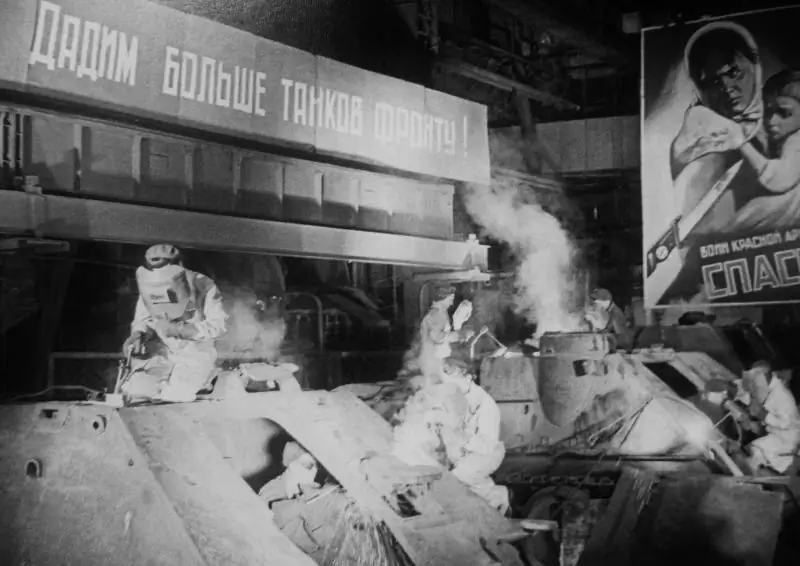
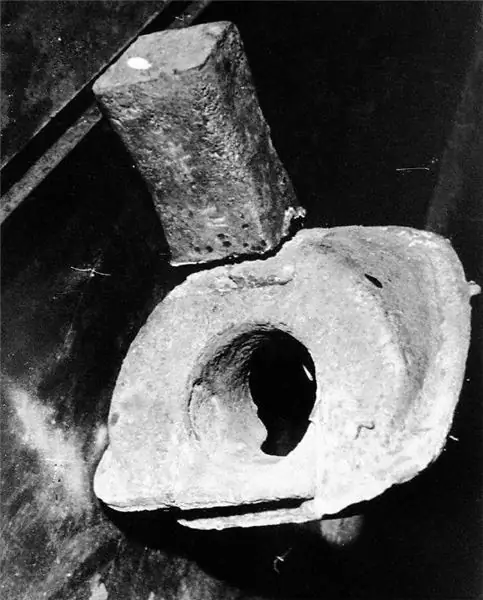
The dramatic increase in the productivity of tank factories led to an unexpected problem in 1943. It turned out that the rest of the production did not always keep up with the tank building. The machines worked for wear and tear, sometimes there were no ammeters to control the current strength on machines, there was a lack of high-quality welding electrodes. All this caused periodic "bursts" of cracking among the serial T-34s. It was necessary to extinguish these waves of marriage with the operational forces of plant technologists and engineers from TsNII-48.
Revision of the design
The hard armor and cracks in it forced engineers to change not only the automatic welding technology, but also the manual approach. Large welding and thermal stresses, in particular, were experienced by the upper frontal part, when during the assembly line the protection of the DT machine gun, eyelets, a loop of the driver's hatch, a protective bar and other trifles were welded on. Around the machine gun protection, which was very carefully scalded, there were often cracks up to 600 mm long! Welding was voluminous in the area of the bow of the sides, where they were fastened with powerful double-sided seams with the frontal upper and lower plates, as well as with sloth brackets. Often the gap between the parts in these parts did not correspond to the normative ones, and therefore it was necessary to put in a particularly massive weld seam, leaving behind serious internal stresses. It was required to reduce the rigidity of some nodes and reduce the total share of welding in the joints, which was done by TsNII-48 specialists in the shortest possible time. In particular, the method of connecting the wheel arch liners to the front part of the hull roof has been changed. With the help of a special "buffer" strip made of mild steel, which was pre-welded to the fender liner, it was possible to reduce the level of the final stress inside the seam and the armor around it. Next, we figured out the aforementioned "infrastructure" on the frontal plate of the tank. Now, according to the new technical conditions, it was possible to weld the eyebolts, the protection of the machine gun and the hatch hinges only with 5-6 mm electrodes in several layers: at least four! In a similar way, the fenders were connected to the roof, the frontal plate with the sides, the fenders and the roof. The rest was cooked in 2-3 passes with 7-10 mm electrodes.
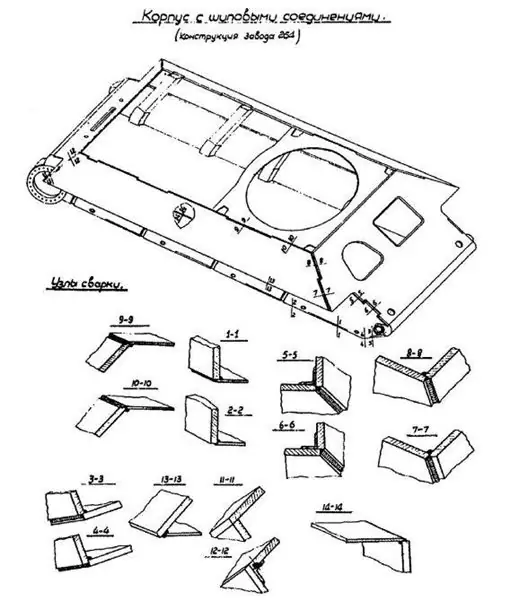
The technology of joining parts of the hull of the T-34 tank was also changed. Initially, all connections, except for the interface of the VLD and NLD, were made in a quarter as according to the drawings. But soon after the start of the war, they were changed to a spike, but it did not justify itself either - too many cracks appeared in the places where the seams were cut. A spike connection for high-hardness armor was not entirely appropriate also due to the strong local shrinkage stresses after welding. What was good for the plastic German armor was not suitable for domestic T-34s. Only in 1943 on the "victory tank" did the final articulation options appear, which satisfied TsNII-48 specialists - overlapping and back to back.
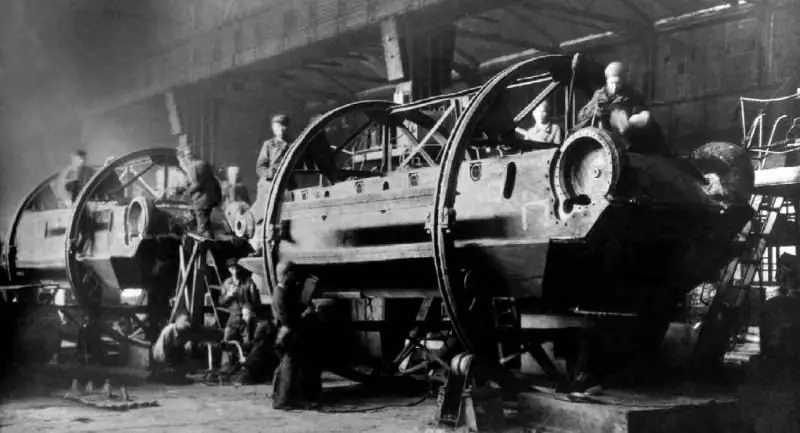
The hulls of heavy Soviet tanks went through the simplest process of optimizing welding operations. The connection of armor plates in a quarter on KV was left unchanged, but the internal reinforcing squares were replaced with internal fillet welds. Already in the midst of the war, for heavy tanks, the most optimal configurations of mating armor plates were chosen (by shelling first of all). If the angle of connection was close to 90 degrees, then it was better to use the method "in a thorn" or in a quarter, and in all other variants - in a spine or in a tooth. As a result of these studies, a peculiar shape of the upper part of the bow assembly of the IS-2 tank was born in TsNII-48, when, with a thickness of 100-110 mm, the armor provided all-round protection against 88-105 mm projectiles. The fit of the pieces in this solid construction was a simple surprise.