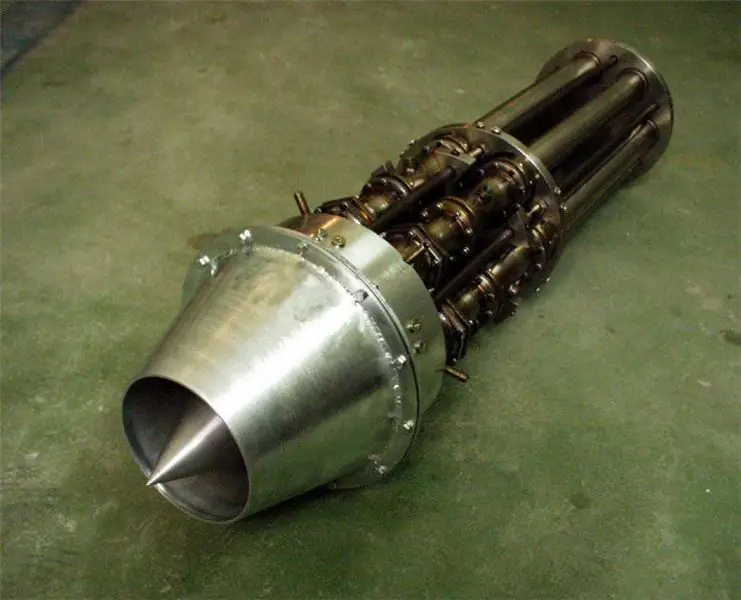
The US Navy plans to upgrade the gas turbine power plants currently installed on its aircraft and ships in the future, replacing conventional Brighton cycle engines with detonation rotary engines. Due to this, fuel savings are expected to amount to about $ 400 million annually. However, the serial use of new technologies is possible, according to experts, not earlier than in a decade.
The development of rotary or spinning rotary engines in America is carried out by the US Navy Research Laboratory. According to initial estimates, the new engines will be more powerful and also about a quarter more economical than conventional engines. At the same time, the basic principles of operation of the power plant will remain the same - the gases from the burnt fuel will enter the gas turbine, rotating its blades. According to the US Navy laboratory, even in the relatively distant future, when the entire American fleet will be powered by electricity, gas turbines will still be responsible for generating power, to some extent modified.
Recall that the invention of the pulsating jet engine dates back to the late nineteenth century. The inventor was the Swedish engineer Martin Wiberg. New power plants became widespread during the Second World War, although they were significantly inferior in their technical characteristics to aircraft engines that existed at that time.
It should be noted that at this point in time, the American fleet has 129 ships, which use 430 gas turbine engines. Each year, the cost of providing them with fuel is about $ 2 billion. In the future, when modern engines are replaced by new ones, the amount of fuel costs will change.
Internal combustion engines currently in use operate on the Brighton cycle. If you define the essence of this concept in a few words, then it all comes down to the successive mixing of the oxidizer and fuel, further compression of the resulting mixture, then - arson and combustion with the expansion of combustion products. This expansion is just used to drive, move pistons, rotate a turbine, that is, perform mechanical actions, providing constant pressure. The combustion process of the fuel mixture moves at a subsonic speed - this process is called dufflagration.
As for the new engines, scientists intend to use explosive combustion in them, that is, detonation, in which combustion occurs at supersonic speed. And although at present the phenomenon of detonation has not yet been fully studied, it is known that with this type of combustion, a shock wave arises, which propagates through a mixture of fuel and air, causes a chemical reaction, the result of which is the release of a fairly large amount of thermal energy. When the shock wave passes through the mixture, it heats up, which leads to detonation.
In the development of a new engine, it is planned to use certain developments that were obtained in the process of developing a detonation pulsating engine. Its principle of operation is that a pre-compressed fuel mixture is fed into the combustion chamber, where it is ignited and detonated. Combustion products expand in the nozzle, performing mechanical actions. Then the whole cycle is repeated from the beginning. But the disadvantage of pulsating motors is that the repetition rate of the cycles is too low. In addition, the design of these motors themselves becomes more complex as the number of pulsations increases. This is due to the need to synchronize the operation of the valves, which are responsible for supplying the fuel mixture, as well as directly by the detonation cycles themselves. Pulsating engines are also very noisy, they need a lot of fuel to operate, and work is possible only with constant metered injection of fuel.
If we compare detonation rotary engines with pulsating ones, then the principle of their operation is slightly different. Thus, in particular, the new engines provide for a constant continuous detonation of the fuel in the combustion chamber. This phenomenon is called spin, or rotating detonation. It was first described in 1956 by the Soviet scientist Bogdan Voitsekhovsky. And this phenomenon was discovered much earlier, back in 1926. The pioneers were the British, who noticed that in certain systems a bright luminous "head" appeared, which moved in a spiral, instead of a flat detonation wave.
Voitsekhovsky, using a photo recorder that he himself designed, photographed the wave front, which was moving in an annular combustion chamber in a fuel mixture. Spin detonation differs from plane detonation in that a single shock transverse wave arises in it, followed by a heated gas that has not reacted, and already behind this layer there is a chemical reaction zone. And it is precisely such a wave that prevents the combustion of the chamber itself, which Marlene Topchiyan called “a flattened donut”.
It should be noted that detonation engines have already been used in the past. In particular, we are talking about the pulsating air-jet engine, which was used by the Germans at the end of World War II on the V-1 cruise missiles. Its production was quite simple, its use was easy enough, but at the same time this engine was not very reliable for solving important problems.
Further, in 2008, the Rutang Long-EZ, an experimental aircraft equipped with a pulsating detonation engine, took to the air. The flight lasted only ten seconds at an altitude of thirty meters. During this time, the power plant developed a thrust of the order of 890 Newtons.
The experimental prototype of the engine, presented by the American laboratory of the US Navy, is an annular cone-shaped combustion chamber having a diameter of 14 centimeters on the fuel supply side and 16 centimeters on the nozzle side. The distance between the walls of the chamber is 1 centimeter, while the “tube” is 17.7 centimeters long.
A mixture of air and hydrogen is used as a fuel mixture, which is supplied at a pressure of 10 atmospheres to the combustion chamber. The mixture temperature is 27.9 degrees. Note that this mixture is recognized as the most convenient for studying the phenomenon of spin detonation. But, according to scientists, in the new engines it will be possible to use a fuel mixture consisting not only of hydrogen but also of other combustible components and air.
Experimental studies of a rotary engine have shown its greater efficiency and power in comparison with internal combustion engines. Another advantage is significant fuel economy. At the same time, during the experiment it was revealed that the combustion of the fuel mixture in the rotary "test" engine is non-uniform, therefore it is necessary to optimize the engine design.
Combustion products that expand in the nozzle can be collected in one gas jet using a cone (this is the so-called Coanda effect), and then this jet can be sent to the turbine. The turbine will rotate under the influence of these gases. Thus, part of the work of the turbine can be used to propel ships, and partly to generate energy, which is necessary for ship equipment and various systems.
The engines themselves can be produced without moving parts, which will greatly simplify their design, which, in turn, will reduce the cost of the power plant as a whole. But this is only in perspective. Before launching new engines into serial production, it is necessary to solve many difficult problems, one of which is the selection of durable heat-resistant materials.
Note that at the moment, rotary detonation engines are considered one of the most promising engines. They are also being developed by scientists from the University of Texas at Arlington. The power plant that they created was called the "continuous detonation engine". At the same university, research is being carried out on the selection of various diameters of annular chambers and various fuel mixtures, which include hydrogen and air or oxygen in different proportions.
Development in this direction is also underway in Russia. So, in 2011, according to I. Fedorov, Managing Director of the Saturn Research and Production Association, scientists from the Lyulka Scientific and Technical Center are developing a pulsating air jet engine. The work is being carried out in parallel with the development of a promising engine called "Product 129" for the T-50. In addition, Fedorov also said that the association is conducting research on the creation of promising aircraft of the next stage, which are supposed to be unmanned.
At the same time, the head did not specify what kind of pulsating engine was in question. At the moment, three types of such engines are known - valveless, valve and detonation. It is generally accepted, meanwhile, that pulsating motors are the simplest and cheapest to manufacture.
Today, several large defense firms are conducting research into high-performance pulsating jet engines. Among these firms are the American Pratt & Whitney and General Electric and the French SNECMA.
Thus, certain conclusions can be drawn: the creation of a new promising engine has certain difficulties. The main problem at the moment is in theory: what exactly happens when the detonation shock wave moves in a circle is known only in general terms, and this greatly complicates the process of optimizing designs. Therefore, the new technology, although it is very attractive, is hardly feasible on the scale of industrial production.
However, if researchers manage to sort out the theoretical issues, it will be possible to talk about a real breakthrough. After all, turbines are used not only in transport, but also in the energy sector, in which an increase in efficiency can have an even stronger effect.