Half a century after the start of work in the field of exoskeletons, the first samples of this equipment are ready to go to full-fledged work. Lockheed Martin recently boasted that its HULC (Human Universal Load Carrier) project has not only been field tested with the Pentagon, but is ready for serial production. The exoskeleton HULC is now "breathing in the back" by several similar projects from other companies. But such an abundance of designs was not always the case.
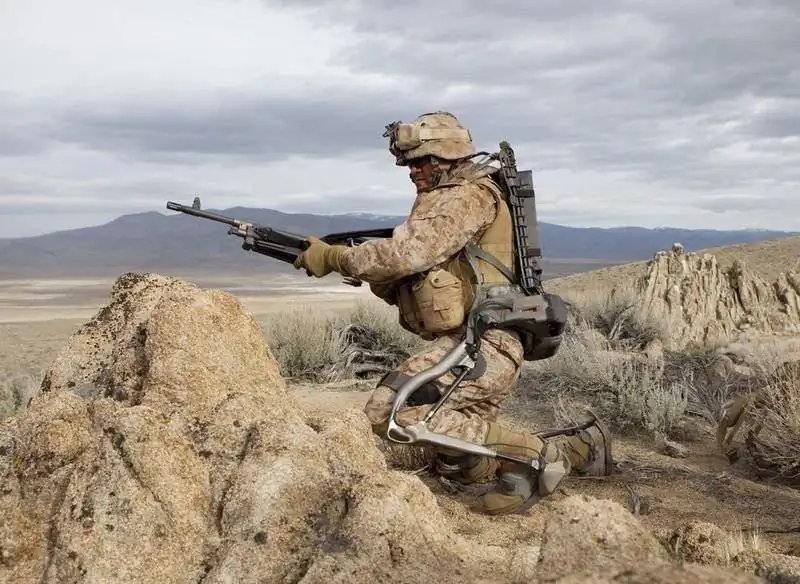
Actually, the idea of creating some kind of device that could be worn by a person and significantly improve his physical qualities appeared in the first half of the last century. However, until a certain time it was just another notion of science fiction writers. The development of a practically applicable system was only started at the very end of the fifties. General Electric, under the auspices of the US military, launched a project called Hardiman. The technical task was bold: the exoskeleton from GE was supposed to allow a person to operate with loads weighing up to one and a half thousand pounds (about 680 kilograms). If the project was successfully completed, the Hardiman exoskeleton would have great prospects. So, the military intended to use new technology to facilitate the work of gunsmiths in the air force. In addition, nuclear scientists, builders and representatives of many other industries stood in line. But even ten years after the start of the program, the engineers of General Electric have not been able to translate everything that was conceived into metal. Several prototypes were built, including a working mechanical arm. The huge claw of the Hardymen was hydraulically powered and could lift 750 pounds of load (approximately 340 kg). On the basis of one workable "glove" it was possible to create a second one. But the designers faced another problem. The mechanical "legs" of the exoskeleton did not want to work properly. The Hardiman prototype with one arm and two support legs weighed under 750 kilograms, while the maximum design capacity was less than its own weight. Due to this weight and the peculiarities of the centering of the exoskeleton, when lifting the load, the entire structure often began to vibrate, which led to overturning several times. With bitter irony, the authors of the project called this phenomenon “the mechanical dance of St. Vitus”. No matter how hard the designers of General Electric fought, they did not manage to cope with the alignment and vibrations. At the very beginning of the 70s, the Hardiman project was closed.
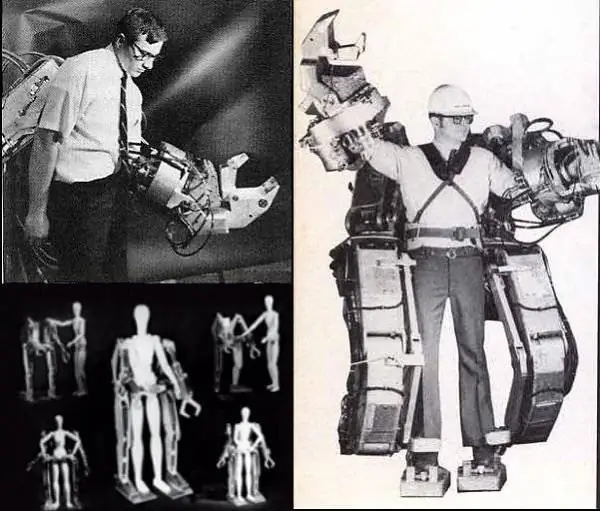
In subsequent years, work in the direction of exoskeletons went inactive. From time to time, various organizations began to deal with them, but almost always the desired result did not follow. At the same time, the purpose of creating an exoskeleton was not always its military use. In the 70s, employees of the Massachusetts Institute of Technology, without much success, developed equipment of this class, designed for the rehabilitation of disabled people with injuries of the musculoskeletal system. Unfortunately, at that time, the engineers also got in the way of synchronizing the various parts of the suit. It should be noted that exoskeletons have a number of characteristic features that do not make their creation a bit easier. Thus, a significant improvement in the physical capabilities of the human operator requires an appropriate source of energy. The latter, in turn, increases the dimensions and dead weight of the entire apparatus. The second snag lies in the interaction of the person and the exoskeleton. The principle of operation of such equipment is as follows: a person makes any movement with his arm or leg. Special sensors associated with his limbs receive this signal and transmit the appropriate command to the actuating elements - hydraulic or electrical mechanisms. Simultaneously with the issuance of commands, these same sensors ensure that the movement of the manipulators corresponds to the movements of the operator. In addition to synchronizing the amplitudes of movements, engineers are faced with the issue of timing. The point is that any mechanic has some reaction time. Therefore, it should be minimized for the purpose of sufficient convenience in using the exoskeleton. In the case of small, compact exoskeletons, which are now being emphasized, the synchronization of human and machine movements has a special priority. Since the compact exoskeleton does not allow for an increase in the supporting surface, etc., mechanics that do not have time to move with a person can adversely affect use. For example, an untimely movement of a mechanical "leg" can lead to the fact that a person simply loses balance and falls. And this is far from all the problems. Obviously, the human leg has fewer degrees of freedom than the hand, not to mention the hand and fingers.
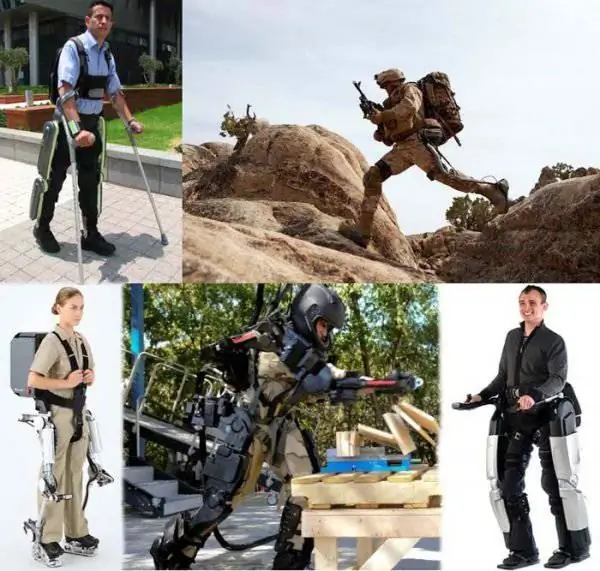
The newest history of military exoskeletons began in 2000. Then the American agency DARPA initiated the start of the EHPA program (Exoskeletons for Human Performance Augmentation - Exoskeletons for increasing human performance). The EHPA program was part of a larger Land Warrior project to create the look of the soldier of the future. However, in 2007, the Land Warrior was canceled, but its exoskeleton part was continued. The aim of the EHPA project was to create the so-called. a complete exoskeleton, which included amplifiers for human arms and legs. At the same time, no weapons or reservations were required. The officials in charge of DARPA and the Pentagon were well aware that the current state of affairs in the field of exoskeletons simply does not allow equipping them with additional functions. Therefore, the terms of reference for the EHPA program implies only the possibility of a long-term carrying by a soldier in an exoskeleton of a load weighing about 100 kilograms and an increase in its movement speed.
Sacros and the University of Berkeley (USA), as well as the Japanese Cyberdyne Systems, expressed their desire to participate in the development of new technology. Twelve years have passed since the start of the program, and during this time the composition of the participants has undergone some changes. Sacros has now become part of the Raytheon concern, and a department of the university called Berkeley Bionics has become a division of Lockheed Martin. One way or another, there are now three prototype exoskeletons created under the EHPA program: Lockheed Martin HULC, Cyberdyne HAL and Raytheon XOS.
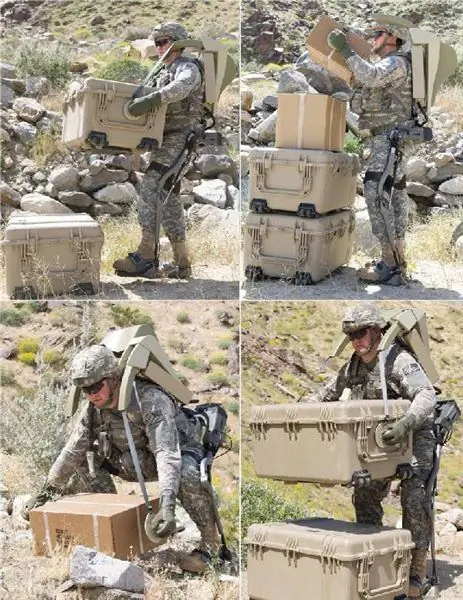
The first of the listed exoskeletons - HULC - does not fully meet the requirements of DARPA. The fact is that the 25-kg construction contains only a back support system and mechanical "legs". Hand support is not implemented in HULC. At the same time, the physical capabilities of the HULC operator are increased due to the fact that through the back support system, most of the load on the arms is transferred to the force elements of the exoskeleton and ultimately "goes" into the ground. Thanks to the applied system, a soldier can carry up to 90 kilograms of cargo and at the same time experience a load that meets all army standards. The HULC is powered by a lithium-ion battery that lasts up to eight hours. In economical mode, a person in an exoskeleton can walk at a speed of 4-5 kilometers per hour. The maximum possible speed of the HULC is 17-18 km / h, but this mode of operation of the system significantly reduces the operating time from one battery charge. In the future, Lockheed Martin promises to equip HULC with fuel cells, the capacity of which will be enough for a day of operation. In addition, in subsequent versions, the designers promise to "robotic" hands, which will significantly increase the capabilities of the exoskeleton user.
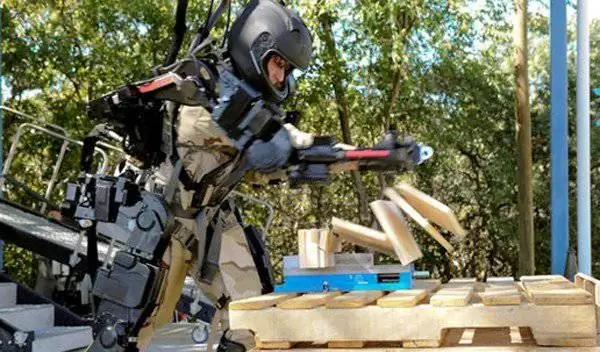
Raytheon has so far presented two somewhat similar exoskeletons with indices XOS-1 and XOS-2. They differ in weight and size parameters and, as a result, in a number of practical characteristics. Unlike the HULC, the XOS family is equipped with a hand relief system. Both of these exoskeletons can lift about 80-90 kilograms of their own weight. It is noteworthy that the design of both XOS allows you to install various manipulators on mechanical arms. It should be noted that XOS-1 and XOS-2 have significant power consumption so far. Because of this, they are not yet autonomous and require external power supply. Accordingly, the maximum travel speed and battery life are out of the question. But, according to Raytheon, the need for cable power will not be an obstacle to the use of XOS in warehouses or military bases where there is an appropriate source of electricity.
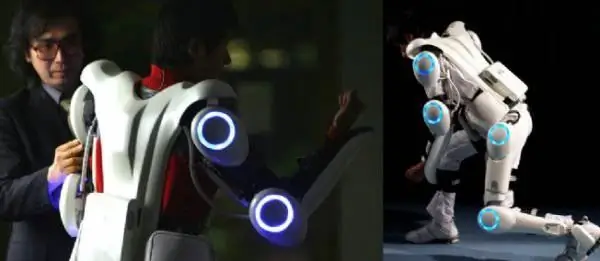
The third sample of the EHPA program is Cyberdyne HAL. Today, the HAL-5 version is relevant. This exoskeleton is to some extent a mixture of the first two. Like the HULC, it can be used independently - the batteries last for 2.5-3 hours. With the XOS family, Cyberdyne Systems' development is united by the "completeness" of the design: it includes support systems for both arms and legs. However, the carrying capacity of the HAL-5 does not exceed a couple of tens of kilograms. The situation is similar with the speed qualities of this development. The fact is that Japanese designers have focused not on military use, but on the rehabilitation of disabled people. Obviously, such users simply do not need high speed or load capacity. Accordingly, if the military is interested in HAL-5 in its current state, it will be possible to make a new exoskeleton on its basis, sharpened for military use.
Of all the options for promising exoskeletons submitted to the EHPA competition, only HULC has so far reached testing in conjunction with the military. A number of features of other projects still do not allow starting their field trials. In September, several HULC kits will be sent in parts to study the features of the exoskeleton in real conditions. If everything goes smoothly, large-scale production will begin in 2014-15.
In the meantime, scientists and designers will have better concepts and designs. The most anticipated innovation in the field of exoskeletons is robotic gloves. The existing manipulators are not yet very convenient for using tools and similar objects intended for manual use. Moreover, the creation of such gloves is associated with a number of difficulties. In general, they are similar to those of other exoskeleton assemblies, but in this case, synchronization problems are aggravated by a large number of mechanical elements, features of the movement of the human hand, etc. The next stage in the development of exoskeletons will be the creation of a neuroelectronic interface. Now the control of the movements of mechanics is carried out using sensors and servo drives. More convenient for engineers and scientists is the use of a control system with electrodes that remove human nerve impulses. Among other things, such a system will reduce the reaction time of mechanisms and, as a result, increase the efficiency of the entire exoskeleton.
With regard to practical application, over the past half century, views on it have hardly changed. The military are still considered the main users of promising systems. They can use exoskeletons for loading and unloading operations, preparing ammunition, and in addition, in a combat situation, to enhance the capabilities of fighters. It should be noted that the carrying capacity of exoskeletons will be useful not only for the military. The widespread use of technology that allows a person to significantly increase his physical capabilities can change the face of all logistics and cargo transportation. For example, the time for loading a cargo semitrailer in the absence of forklifts will decrease by tens of percent, which will increase the efficiency of the entire transportation system. Finally, nerve-controlled exoskeletons will help disabled support people to live a full life again. Moreover, great hopes are pinned on the neuroelectronic interface: in case of spinal injuries, etc. In injuries, signals from the brain may not reach a specific area of the body. If we “intercept” them to the damaged area of the nerve and send them to the exoskeleton control system, then the person will no longer be confined to a wheelchair or bed. Thus, military developments can once again improve the lives of not only the military. Just for now, making big plans, you should remember about the trial operation of the Lockheed Martin HULC exoskeleton, which will begin only in the fall. Based on its results, it will be possible to judge both the prospects of the entire industry and the interest in it from potential users.