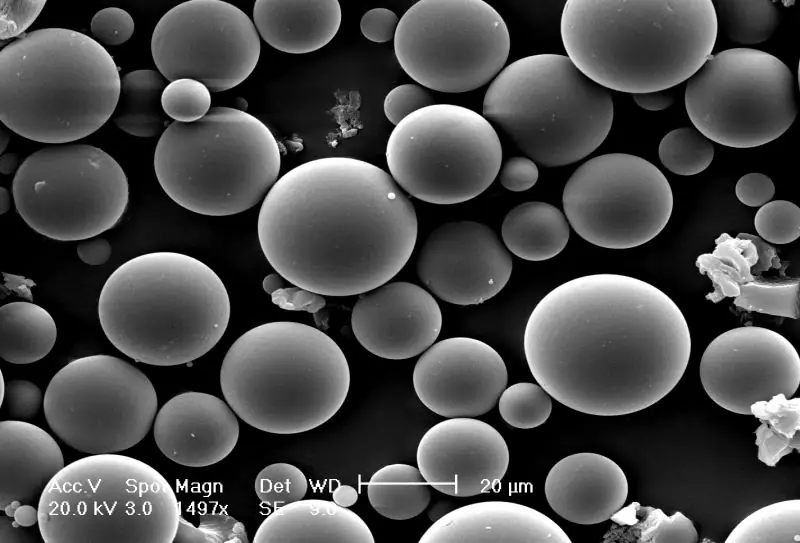
"Non-traditional materials" is one of the most important areas of technology development in the military and aerospace industries. Materials need to do more than just serve as a supporting structure - they need to be smart materials
Smart materials are a special class of materials that have the ability to act as an actuator and as a sensor, providing the necessary mechanical deformations associated with changes in temperature, electric current or magnetic field. Since composite materials are composed of more than one material and due to modern technological progress, it is now possible to include other materials (or structures) in the process of providing integrated functionality in such areas as:
- Morphing, - Self-healing, - Perception, - Lightning protection, and
- Energy storage.
We will focus on the first two areas in this article.
Morphing materials and morphing structures
Morphing materials include those materials that, following the input signals, change their geometric parameters and which are able to restore their original shape when external signals stop.
These materials, due to their reaction in the form of a change in shape, are used as actuators, but they can also be used in the opposite way, that is, as sensors in which an external influence applied to the material is transformed into a signal. The aerospace applications of these materials are varied: sensors, actuators, switches in electrical installations and apparatus, avionics, and connections in hydraulic systems. The advantages here are: exceptional reliability, long service life, no leaks, low installation costs and a significant reduction in maintenance. In particular, among actuators made of morphing materials and shape memory alloys, actuators for automatic control of avionics cooling systems and actuators for closing / opening directional dampers in cockpit air conditioning systems are of particular interest.
Materials that change shape as a result of the application of an electric field include piezoelectric materials (the phenomenon of polarization of materials with a crystalline structure under the action of mechanical stresses (direct piezoelectric effect) and mechanical deformations under the action of an electric field (reverse piezoelectric effect)) and electrostrictive materials. The difference lies in the response to an applied electric field: a piezoelectric material can lengthen or shorten, while an electrostrictive material only lengthens, regardless of the direction of the applied field. In the case of sensors, the voltage generated by mechanical stress is measured and processed in order to obtain information about the same stress. These materials with direct piezoelectric effect are widely used in acceleration and load sensors, acoustic sensors. Other materials based on the reverse piezoelectric effect are used in all actuators; they are often used in optical systems for reconnaissance satellites, as they are capable of adjusting the position of lenses and mirrors with nanometer precision. The aforementioned materials are also included in morphing structures in order to change certain geometric characteristics and impart special additional properties to these structures. A morph structure (also called a smart structure or active structure) is capable of sensing changes in external conditions due to the operation of the sensor / electromechanical transducer system built into it. In this way (due to the presence of one or more microprocessors and power electronics), appropriate changes can be induced in accordance with the data coming from the sensors, allowing the structure to adapt to external changes. Such active monitoring is applicable not only to an external input signal (eg mechanical pressure or shape change), but also to changes in internal characteristics (eg damage or failure). The scope of application is quite wide and includes space systems, aircraft and helicopters (control of vibration, noise, shape change, stress distribution and aeroelastic stability), marine systems (ships and submarines), as well as protection technologies.
One of the tendencies to reduce vibration (vibrations) that occurs in structural systems is very interesting. Special sensors (consisting of multilayer piezoelectric ceramics) are placed at the most stressed points in order to detect vibrations. After analyzing the vibration-induced signals, the microprocessor sends a signal (proportional to the analyzed signal) to the actuator, which responds with an appropriate movement capable of inhibiting vibration. The US Army's Office of Applied Aviation Technology and NASA have tested similar active systems in order to reduce vibrations of some elements of the CH-47 helicopter, as well as the tail planes of the F-18 fighter. The FDA has already begun integrating active materials into rotor blades to control vibration.
In a conventional main rotor, the blades suffer from high levels of vibration caused by rotation and all related phenomena. For this reason, and in order to reduce vibration and facilitate control of the loads acting on the blades, active blades with a high bending capacity were tested. In a special type of test (called "embedded twisting circuit"), when the angle of attack changes, the blade is twisted along its entire length thanks to the active fiber composite AFC (electro-ceramic fiber embedded in a soft polymer matrix) integrated into the blade structure. Active fibers are stacked in layers, one layer above the other, on the upper and lower surfaces of the blade at an angle of 45 degrees. The work of the active fibers creates a distributed stress in the blade, which causes a corresponding bending throughout the blade, which can balance the swing vibration. Another test (“activation of discrete swings”) is characterized by the widespread use of piezoelectric mechanisms (actuators) for vibration control: actuators are placed in the blade structure to control the operation of some deflectors located along the trailing edge. Thus, an aeroelastic reaction occurs that can neutralize the vibration generated by the propeller. Both solutions were evaluated on a real CH-47D helicopter in a test called the MiT Hower Test Sand.
The development of morphing structural elements opens up new perspectives in the design of structures of increased complexity, while their weight and cost are significantly reduced. A marked reduction in vibration levels translates into: increased structure life, fewer structural integrity checks, increased profitability of final designs as structures are subject to less vibration, increased comfort, improved flight performance and noise control in helicopters.
According to NASA, it is expected that over the next 20 years, the need for high performance aircraft systems that will become lighter and more compact will require more widespread use of morphing designs.
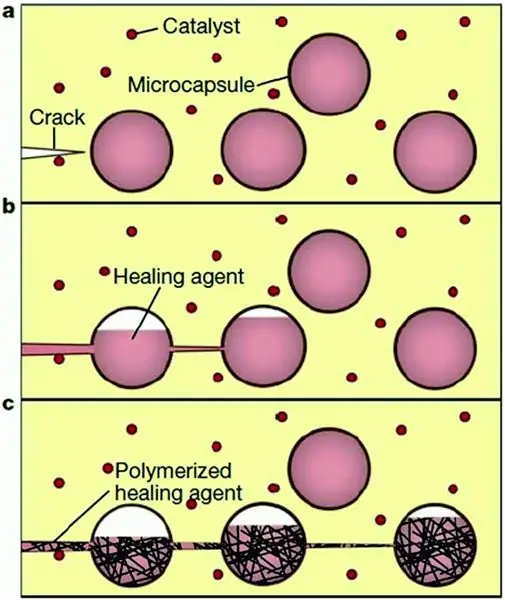
Self-healing materials
Self-healing materials belonging to the class of smart materials are able to independently repair damage caused by mechanical stress or external influences. When developing these new materials, natural and biological systems (for example, plants, some animals, human skin, etc.) were used as a source of inspiration (in fact, in the beginning they were called biotechnological materials). Today, self-healing materials can be found in advanced composites, polymers, metals, ceramics, anti-corrosion coatings and paints. Particular emphasis is placed on their application in space applications (large-scale research is being carried out by NASA and the European Space Agency), which are characterized by vacuum, large temperature differences, mechanical vibrations, cosmic radiation, as well as to reduce damage caused by collisions with space debris and micrometeorites. In addition, self-healing materials are essential for the aviation and defense industries. Modern polymer composites used in aerospace and military applications are susceptible to damage caused by mechanical, chemical, thermal, enemy fire, or a combination of these factors. Since damage inside materials is difficult to notice and repair, the ideal solution would be to eliminate the damage that has occurred at the nano and micro levels and restore the material to its original properties and condition. The technology is based on a system according to which the material includes microcapsules of two different types, one containing a self-healing component and the other a certain catalyst. When the material is damaged, the microcapsules are destroyed and their contents can react with each other, filling the damage and restoring the integrity of the material. Thus, these materials greatly contribute to the safety and durability of advanced composites in modern aircraft, while eliminating the need for costly active monitoring or external repair and / or replacement. Despite the characteristics of these materials, there is a need to improve the maintainability of materials used by the aerospace industry, and multilayer carbon nanotubes and epoxy systems are proposed for this role. These corrosion-resistant materials increase the tensile strength and damping properties of the composites and do not alter the thermal shock resistance. It is also interesting to develop a composite material with a ceramic matrix - a matrix composition that converts each oxygen molecule (penetrated into the material as a result of damage) into a silicon-oxygen particle with a low viscosity, which can flow into damage due to the capillary effect and fill them. NASA and Boeing are experimenting with self-healing cracks in aerospace structures using a polydimethylsiloxane elastomer matrix with embedded microcapsules.
Self-healing materials are capable of repairing damage by closing the gap around the punched object. Obviously, such capabilities are being studied at the defense level, both for armoring vehicles and tanks, and for personal protection systems.
Self-healing materials for military applications require careful evaluation of the variables associated with hypothetical damage. In this case, the impact damage depends on:
- kinetic energy due to the bullet (mass and velocity), - system designs (external geometry, materials, armor), and
- collision geometry analysis (meeting angle).
With this in mind, DARPA and the US Army Laboratories are experimenting with the most advanced self-healing materials. In particular, restorative functions can be initiated by bullet penetration where the ballistic impact causes localized heating of the material, allowing self-healing.
Studies and tests of self-healing glass are very interesting, in which cracks caused by some mechanical action are filled with liquid. Self-healing glass can be used in the manufacture of bulletproof windshields of military vehicles, which would allow soldiers to maintain good visibility. It can also find application in other fields, aviation, computer displays, etc.
One of the future major challenges is to extend the life of advanced materials used in structural elements and coatings. The following materials are being investigated:
- self-healing materials based on graphene (two-dimensional semiconductor nanomaterial consisting of one layer of carbon atoms), - advanced epoxy resins, - materials exposed to sunlight, - anti-corrosion microcapsules for metal surfaces, - elastomers capable of withstanding bullet impact, and
carbon nanotubes used as an additional component to enhance material performance.
A significant number of materials with these characteristics are currently being tested and investigated experimentally.
Output
For many years, engineers often proposed conceptually promising projects, but could not implement them due to the unavailability of appropriate materials for their practical implementation. Today, the main goal is to create lightweight structures with outstanding mechanical properties. Modern progress in modern materials (smart materials and nanocomposites) plays a key role, despite all the complexity, when the characteristics are often very ambitious and sometimes even contradictory. At present, everything is changing with a kaleidoscopic speed, for a new material, the production of which is just beginning, there is a next one, on which they conduct experiments and test. The aerospace and defense industry can reap many benefits from these amazing materials.