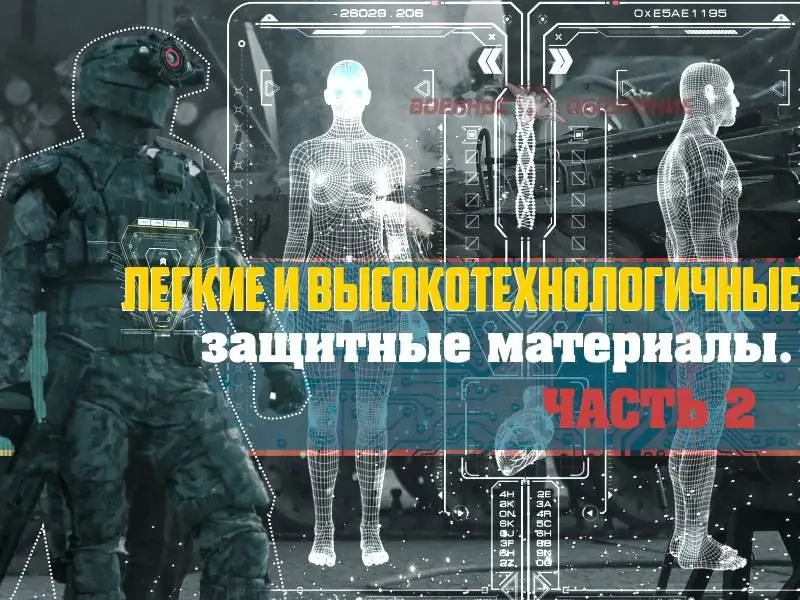
About the latest developments and forecasts for the future
For almost a century, Alcoa Defense has kept its finger on the pulse of innovative technologies, being a reliable partner and supplier of military structures, its products allow maintaining the protection of land, air and sea platforms of weapons at the highest level.
Continuing the discussion (Part 1), Vice President of Alcoa Defense Margaret Cosentino noted that one of the promising areas of development is the technology of stamping large metal parts. The strength of a monolithic part is much higher, while in the process of stamping, it is possible to distribute the metal of the workpiece more efficiently, depending on the loads acting on certain zones of the part. This powerful design idea is now achievable thanks to Alcoa's innovations. Alcoa, working with the US Army and DARPA (Defense Advanced Research Projects Agency), brought this idea to fruition by developing the technology to produce the world's largest all-forged aluminum case for military vehicles - no one in the world makes such large parts in closed dies. Cosentino spoke about the prospects for this achievement. “This breakthrough stamped part replaces the lower hull of a combat vehicle - a solid piece that is stronger than traditional welded hulls - ultimately improving crew survivability. In addition, Alcoa's development workflow reduces machine weight, assembly time, and cost. If a higher level of protection (that is, more metal) in certain areas is structurally necessary, then this can be easily achieved with the help of stamping. Another advantage of stamping is that it becomes easier for us during the design process to make the shape of the part closer to the final one, which allows us to reduce the amount of machining."
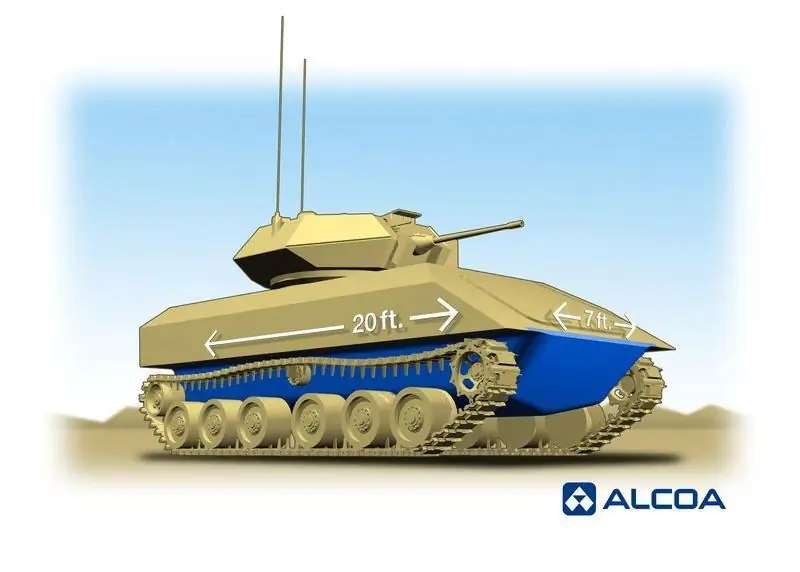
Alcoa is actively collaborating with the military on innovative materials and manufacturing processes to further improve the level of protection of combat and tactical vehicles and achieve superiority in this parameter over the vehicles of a potential enemy. “We signed a five-year contract with the US Army last year, worth up to $ 50 million, to work together to develop aluminum alloy solutions that increase combat survivability,” Cosentino said. “We worked closely with the US military and worked with them to develop a stamped monolithic lower hull for combat vehicles. By eliminating welds, we can significantly increase the level of survivability when using both IEDs and other threats. By reducing the number of parts and improving the efficiency of the supply chain, we are arriving at a more affordable solution. We believe that by combining modern passive armor solutions such as a monolithic hull with advanced active protection systems, we can get the best combat resilience package for our ground vehicles."
Ceradyne, which plays a prominent role in the field of personal protection systems, is conducting the final stage of qualification testing of the VTP (Vital Torso Protection) torso protection system, which is part of the US Army's Soldier Protection System (SPS) program. VTP will help the army achieve its goal and reduce the weight of the liners for body armor, while maintaining the required level of protection. Cheryl Ingstad, Head of Advanced Ceramics at 3M, added: “As part of the SPS program, we are also developing the Integrated Head Protection System, which will enable the army to get the next generation helmet. ZM's experience in creating uniform and convenient protection systems for the commercial segment will help us meet the needs of military customers as accurately as possible."
Also working in the related security industry, Ceradyne will supply US law enforcement with its UltraLight Weight Ballistic Bump Helmet N49 (ULW-BBH N49). “This helmet is also well suited for special forces. It features a patented bolt-free design and a mass of clean, unlined helmet, and more. is only 575 grams”.
The search for new solutions is also a priority activity of DuPont, which, according to the chief technologist of this company Joseph Hovanek, constantly uses its scientific and practical experience to study and develop new advanced materials. “We have recently developed several new materials for hard and soft protection, including products with unidirectional and chaotic orientation of Kevlar fibers for protection against piercing weapons, as well as several products from Tensyion,” he added. QNA's Mr. Riu, in addition to evaluating the new personal protective equipment, also gave his assessment of how the industry will respond to the army's drive to improve the safety of its equipment and personnel. “At QNA, we are continually pushing the limits to achieve the best multi-hitting performance in our advanced composites combined with the weight reduction of new systems, and will work with our customers to deploy these solutions across our divisions. We are also working to bring to the market new solutions for passive and active protection against RPGs”.
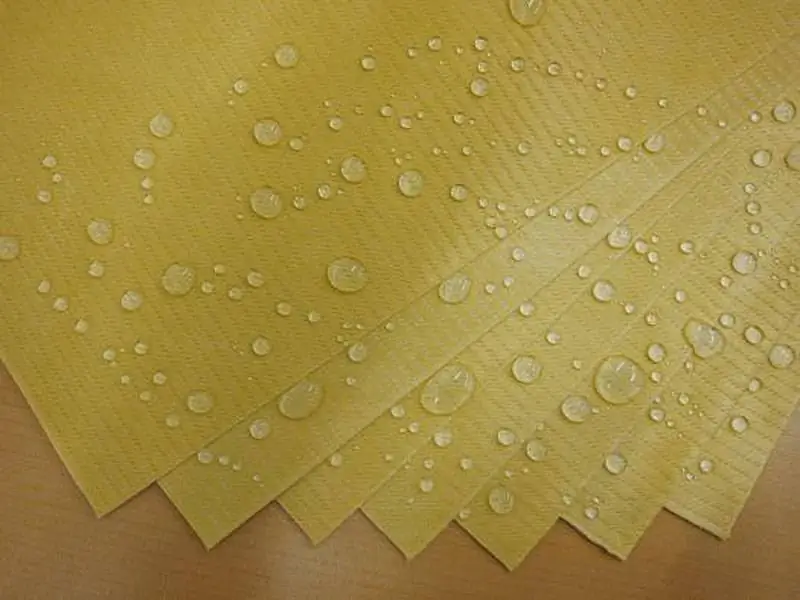
Ryu further expressed his opinion on the trends in the near future: “We see the continuing threat of mines and improvised explosive devices (IEDs), which only contributes to the growing demand for lightweight solutions that can be included either in the design of the machine or used as an add-on kit. Our high quality anti-splinter liners, as well as energy-absorbing seats and floor-mounted anti-explosion solutions will enable vehicle manufacturers to provide cost-effective solutions that give the fighter the highest level of protection.”
DuPont's Mr. Hovanek sees growth and continuous development in this sector: “As the number of asymmetric threats to the military and law enforcement agencies grows in the world, we understand that an increasing number of military and paramilitary structures need protection from various threats, both ballistic and non-ballistic. We also expect the so-called 'must-wear' trend to intensify, meaning that comfort, fit and flexibility (literally) of body protectors will be a key requirement in the next two to three years."
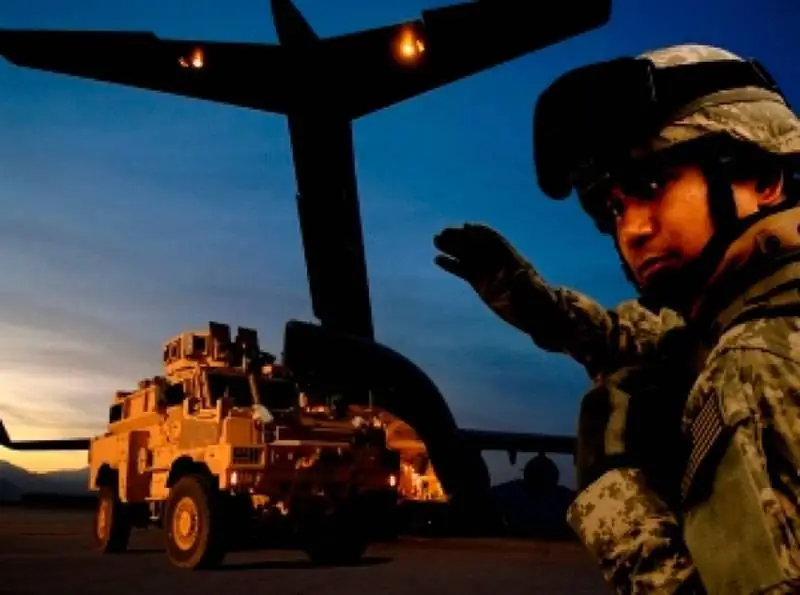
Protection of armored vehicles
Worldwide military spending on armored vehicles and personal protective equipment amounts to many zeros. The United States alone spent an estimated $ 30 billion on this in 2016.
In August 2016, the British company Permali Gloucester announced the supply of composite armor for the British AJAX combat vehicle under a £ 15 million contract issued by General Dynamics European Land Systems (GDELS).
According to the company Permali, composite materials will become an integral part of the ballistic protection of this machine. The British Department of Defense has ordered 589 of these medium combat armored platforms.
Permah solutions are based on lightweight passive ballistic and explosion-proof protective panels (tested in accordance with STANAG 4569 and AEP-55 standards), which are made of glass, aramid or ultra high molecular weight polyethylene UHMWPE (ultra high molecular weight polyethylene), as well as thermoset rubber and modern thermoplastic polymers.
“They could also include ceramic tiles for armor-piercing projectiles and aluminum or steel claddings to add stiffness or higher levels of protection. The panels can be supplied as optional upgrades or integrated into completely new platforms. Working closely with consumers and manufacturers of military vehicles allows us to optimize booking solutions, increase the level of protection and reduce the weight of the final product,”explained a company representative.
One of the company's innovative solutions is the Tufshield polyurethane coating, which provides protection from adverse external influences. In addition, Permali armor kits are found on many British platforms, including CVRT, VVARTMOG and VIKING tracked vehicles, as well as on heavy wheeled tractors and tankers manufactured by the American Oshkosh. In addition, the company has developed a reservation kit for the HMT EXTENDA open-top vehicle from Supacat. As with other special forces vehicles, it does not require protection of the upper part of the minimum level, since soldiers must have the maximum level of situational awareness when performing reconnaissance tasks, as well as direct combat contact. Composite ballistic panels for the underside of this vehicle will be supplied to Supacat in 2017-2018.
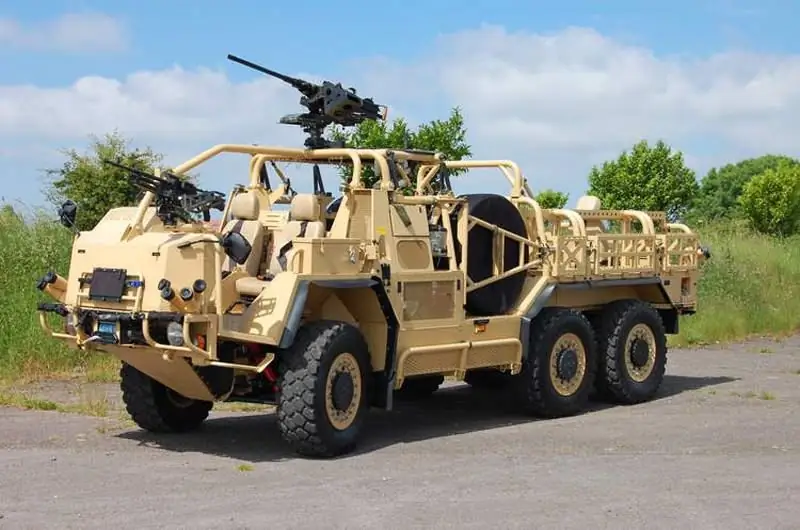
General Robert Rice, Director of the Office of Military Equipment and Supplies of the British Department of Defense, explained: “The new AJAX armored vehicle is the backbone of the new British Strike brigades, it gives the military the ability to respond quickly and effectively on almost any type of terrain. The next generation of British combat vehicles now have world-class protection.”
Talking about the fact that Permali is currently working in much closer relationship with the main manufacturers of final products, starting from the very early stages of design and development of combat vehicles, the spokesman noted that ceramic composite armor offers much higher levels of protection. compared to metal armor. To a greater extent, this concerns solutions to protect against threats such as small arms and large-caliber machine guns and even medium-caliber cannons and IEDs; the latter were simply the scourge of coalition forces that had operated for more than a decade in Iraq and Afghanistan.
“For each of these programs, we worked with platform type, end-user and Department of Defense views in mind, with the goal of delivering tailored solutions to meet complex technical and design requirements,” he added.
British proposals for the protection of armored vehicles
Another major initiative of the British Department of Defense is the CHALLENGER 2 Main Battle Tank (MBT) modernization program, in which Lockheed Martin and Elbit Systems joined forces to win, and announced this later in August 2016. The program, with a total cost of more than 600 million pounds, provides for the upgrade to 227 MBTs. BAE Systems and General Dynamics, Rheinmetall, RUAG, Krauss-Maffei Wegman (KMW) and CMI Defense / Ricardo also competed for the contract.
In accordance with the terms of the competition for armored vehicles announced by the British Department of Defense in April 2016, the proposals must take into account “possible future requirements”. The program, designated CR2 LEP (CHALLENGER 2 Life Extension Project - extending the service life of the CHALLENGER 2 tank), will extend its service life from 2025 to 2035 "in order to preserve the capabilities of maneuverable high-precision direct fire throughout a wide range of military operations." …
However, there are quite few details regarding the replacement or modernization of the CHALLENGER 2's Chobham 2 composite armor, which provides protection against small arms fire, RPGs and various IEDs, including charges of the "shock core" type. Additional upgrades are expected to include the installation of active protection complexes on this MBT. In this regard, the Laboratory of Military Applied Research of the British Ministry of Defense in July 2016 signed a contract with QinetiQ to review and evaluate several systems, including the MUSS complex developed by Airbus Defense & Space.
On December 23, 2016, the Ministry of Defense announced that it had selected two finalists for the CR2 LEP program - BAE Systems and Rheinmetall. The Ministry of Defense will allocate each of them 23 million pounds to develop an upgrade program, after which it will choose the winner and sign a contract with him for the modernization of the CHALLENGER 2 tank before the Mk2 modification and subsequent production until 2019.
IBD Deisenroth Engineering is currently actively promoting its latest development in the field of composite ceramics. The company explained that ceramic protection solutions provide more flexibility and, therefore, allow for higher levels of protection for the "more difficult surfaces" of modern MBTs, BMPs and armored personnel carriers compared to more traditional materials made from heavier steel. IBD pioneered the development of one-piece composite materials for vulnerable areas, including wheel arches and sponsons, as previously only flat panels were used for ceramic shielding.
IBD, which presented its forward-looking solutions at Eurosatory 2016, has focused on the creation of three-dimensional shaped profiles made of ceramic tiles that meet the protection requirements in accordance with Level 5 and 6 of the NATO standard STANAG 4569. In addition, such solutions can be successfully used for protection against IEDs and charges of the "shock core" type.
The company also noted that the transition from steel to ceramic composites entails a significant reduction in the mass of armored vehicles, which allows the addition of weapons and equipment for reconnaissance, surveillance and control in accordance with operational needs.
Reactive armor (reactive armor) with a low level of fragmentation, called HL-Schutz, and formerly known as CLARA (Composite Lightweight Adaptable Reactive Armor - lightweight adaptive composite reactive armor), is based on the same principles as traditional ERA technology. Dynamit Nobel Defense (DND)'s new insensitive attachment armor concept is a combination of composite panels and an all-new, low-burning explosive with low sensitivity. This explosive can withstand being hit by bullets and shells fired from machine guns and small-caliber cannons, shrapnel, fire and lightning. Reactive blocks are initiated from the impact of the cumulative jet. Only such a jet creates enough energy to initiate the explosive contained in the block, which, detonating, deflects and thereby reduces the armor penetration characteristics of the cumulative jet. Also, reactive armor units are immune to any type of environment and hit by a bullet or even a medium-caliber projectile.
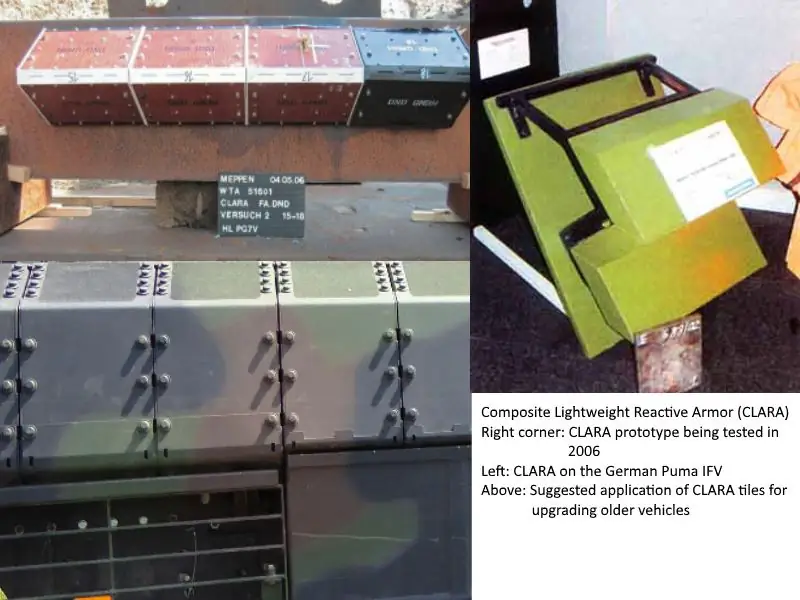
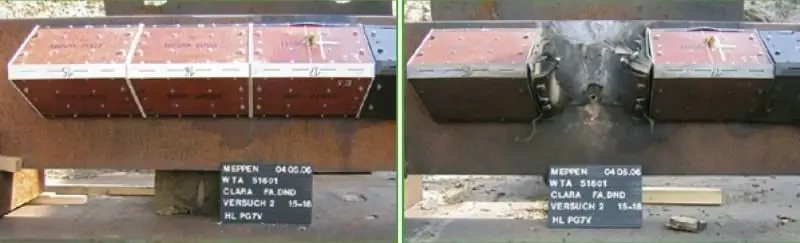
Depending on the type of vehicle and requirements, the HL protection kit can either be installed directly on the main armor of the vehicle, or in combination with additional armor (for example, an armor plate), which increases the level of protection against armor-piercing projectiles. In this case, it is installed between the main armor and the DZ blocks. The two panels are stacked one on top of the other, the lower one weighs about 40 kg, and the upper one about 20 kg. The average weight of such reactive armor is approximately 260 kg / m2. Such a system reduces the effect of the cumulative jet, and also provides additional protection against large-caliber bullets, up to 14, 5-mm armor-piercing incendiary bullets fired from a machine gun. When installed on an armored vehicle, HL-Schutz reactive armor units are installed at different angles. This "smooth" placement allows for additional space behind the protection system that can be used for stowing equipment. But, most importantly, it allows you to get the optimal level of protection against hand-held anti-tank grenade launchers.
When detonating the energetic material that fills the blocks, no fragments are formed that fly away from the vehicle in different directions, that is, the risk of indirect losses among the infantrymen who are in the immediate vicinity of the vehicles is minimized. Within a few milliseconds, the composite material is fragmented into a ball of fibers. In addition, the HL-Schutz reactive armor concept is aimed at minimizing fragmentation inside the vehicle, thus reducing armor damage to the crew and equipment. One of the most important characteristics of the HL-Schutz system is that if one reactive block is initiated, a chain reaction will not happen and adjacent blocks will not detonate. This is achieved thanks to the special design of individual tiles and the use of a special low-sensitivity explosive.
LEOPARD 2A4 is now 100% digital
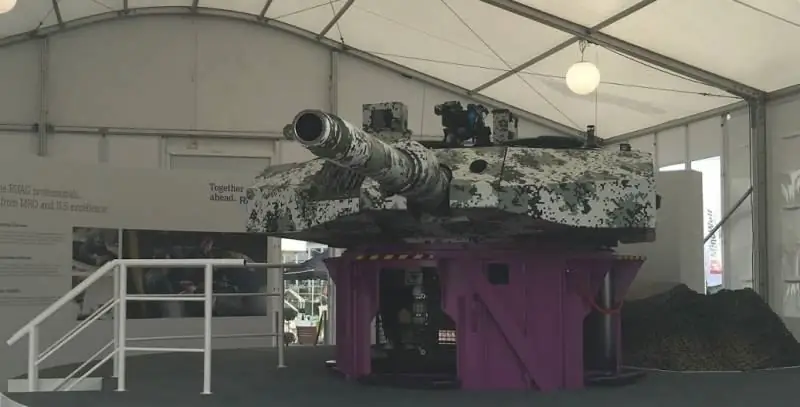
At the beginning of last year, RUAG Defense showed what the company calls the world's first "100%" digital MBT LEOPARD 2A4. Perhaps the project was specifically designed as a mid-life upgrade, which allows us to flexibly adapt to the needs of each customer. According to RUAG Defense, the latest intermediate upgrade concept for the LEOPARD 2A4 MBT represents another innovative milestone achieved by it. As such, the company humbly describes itself as "the only supplier in the market able to offer a fully digital model."
The reconnaissance and command systems are closely interconnected, that is, a combat mission can be successfully completed in accordance with the assigned task only if the relevant information has correctly passed through all data transmission channels. Thanks to open interfaces, it is now possible to send and receive voice messages, images and data at any time and in the most adverse conditions. Of particular note is the updated tank fire control system, which was completely redesigned by RUAG Defense, and now, thanks to universal interfaces, it can be easily combined with existing and new systems, such as a battle control system or ammunition programming. The modern LMS supports all types of ammunition and, as a result, has a high functional flexibility. Digital modernization has made it possible to bring the aging tank to a new level and significantly increase its combat capabilities.
Microprotection
Another area of development in the field of protection systems for MBT, armored personnel carriers and infantry fighting vehicles is the so-called "microprotection" of specific elements of vehicles, such as fuel tanks. The growing demand in this market allowed the British company Permali to enter the American market together with the local company HIT (High Impact Technology) and present there its BattleJacket Fuel Cell Containment System (FCCS).
The BattleJacket system, based on self-sealing elastomer spray coating technology, can be used on metal, ceramic and plastic products. It protects machine components not only from corrosion and abrasion, but also from excessive heat.
The FCCS system, designed to prevent leaks from bullets, can be sprayed with special tools on the surfaces of machines already deployed in small forward bases and repair sites.
Permali has confirmed that this technology will be included in the program for the new AJAX combat vehicle, as well as integrated into the machines of the HMT EXTENDA family from Supacat.
HIT has also entered the tactical defense market with its BattleGuard solution, which it calls "a physical bullet and explosion barrier to protect forward bases and roadblocks."
The Czech Army is currently considering a similar technology to protect personnel from bullets and shrapnel. Developed since 2014 by the Military Research Institute (MRI), the dome-shaped system (photo below) underwent a series of anti-explosion and qualification tests in the Czech Armed Forces in mid-2016.
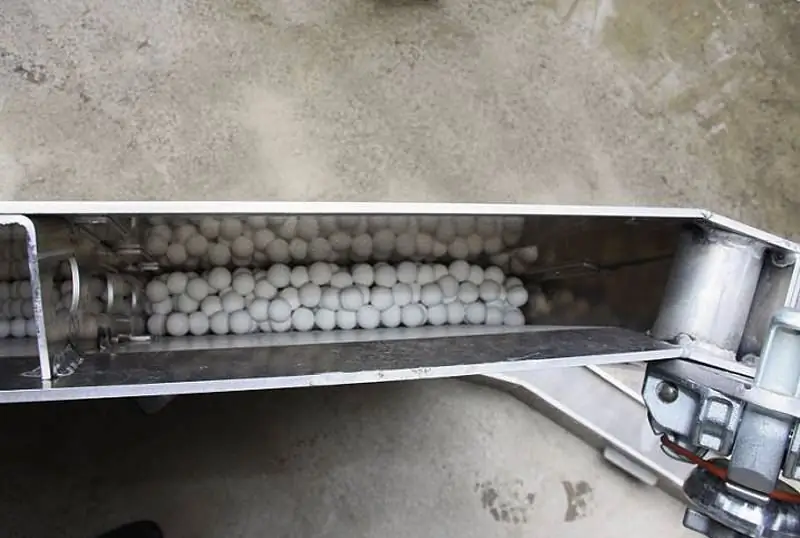
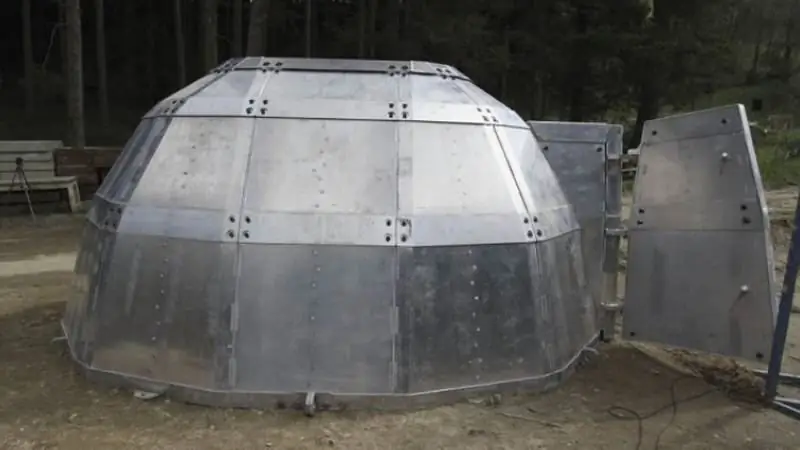
The 90 cm wide interior space between two layers of aluminum armor can be filled with corundum balls, insulating materials and even sand in order to absorb the kinetic energy of bullets and shrapnel. To date, anti-explosion tests have confirmed the resistance of the system when detonating 10 kg of TNT at a distance of 10 meters.
Inside the dome can accommodate up to six people, the space can be divided into two zones of 5, 6 m2 and 7, 8 m2. According to MRI, the system can be transported by air, land or sea and assembled in 4 hours, but special tools are required.
Personal protection
Meanwhile, for ballistic protection systems currently worn by infantry and special forces, such as body armor and helmets, the trend continues to increase the level of modularity so that they can be upgraded depending on the level of protection required for a specific combat mission.
For example, the American command of special operations forces carries out the FTHS program (Family of Tactical Headbome Systems), within which a basic shockproof helmet is being developed with an additional set of increasing the level of bullet protection. Revision Military and 3M Ceradyne received a contract last summer to study solutions offered in the market.
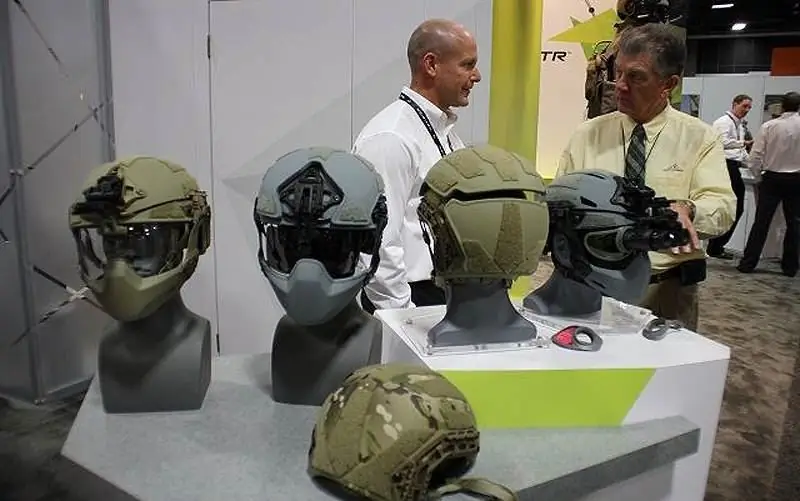
The selected FTHS helmet, starting in September 2017, will begin to replace the standard Ops Core FAST helmets. It will provide protection against 9mm and 7.62mm bullets, as well as shrapnel and blunt injuries due to modular and multi-layer padding systems inside the helmet itself.
Revision Military offers a 2.3 kg Multi-Use Bump Shell, first unveiled at the SOFIC (Special Operations Forces Industry Conference) in May 2016 with an optional bulletproof kit mounted over the base helmet shell.
Ballistic materials used in these areas continue to play a "very significant role", says DSM Dyneema's Mr Manik.
“We expect that the bulk of the growth in the defense sector will come from modernization programs that require new technologies. Many countries, such as the United States, Britain, Brazil and India, are modernizing their military forces. While the need for more troops to participate in global conflicts appears to be declining today, riots and the growing threat of terrorism around the world are driving advances in new technologies. This situation also led to the growth opportunities in personal protection overtaking the growth opportunities in vehicle protection, although this area is still very important.”
Speaking about the current trends in protection technology related to body armor and combat helmets, he stressed that manufacturers are concerned about reducing size and weight, and the military leadership is seeking lighter systems in order to increase convenience and freedom of movement.
Looking to the future, Dyneema is also considering the proliferation of special types of ammunition, as many military forces seek to move away from the traditional 5, 56 mm and 7, 62 mm assault rifles and submachine guns. In the appearance of bullets of caliber 6, 5 mm and 6, 8 mm, as well as Russian bullets of caliber 5, 45 mm, the company sees a new ballistic threat on a global scale. " According to Manik, “Special pistol and rifle cartridges have a higher penetration energy and are easily fragmented compared to standard cartridges. Unfortunately, nothing can stop their spread. Customers are asking for new materials that can protect them from new bullets. It's a constant race between the underworld and the personal protection industry. Helmets, body armor and various types of inserts for them open up significant opportunities for growth. The helmet industry is currently undergoing a transformation as existing products based on the US Army model are being replaced by lighter models.” He further noted the growing demand for inserts for body armor, attributing this to growing concerns about the widespread and easy availability of AK-47 and AR-15 assault rifles and the like. “As part of modernization programs, both military and law enforcement agencies are buying more comfortable vests with less weight. Although these items are bought in that order - vest, helmet and insert plates - they all play a key role in complete protection."
Continuous changes
Innovation to improve the lethality of weapons and improve tactics allows companies in the protective materials industry to remain dynamic and adaptable. These companies will continue to innovate with the goal of saturating the market with new materials and other advanced technologies. Likewise, these companies will seek partnerships to quickly communicate their protection solutions to military and law enforcement customers.
The need for well-protected personnel, vehicles and military bases will grow as the combat effectiveness of opponents close in combat power and technological level will continue to grow. However, these needs must be balanced by modularity and mobility, as modern operational space necessitates a fast and agile force capable of operating in an expeditionary style and away from permanent deployment sites.
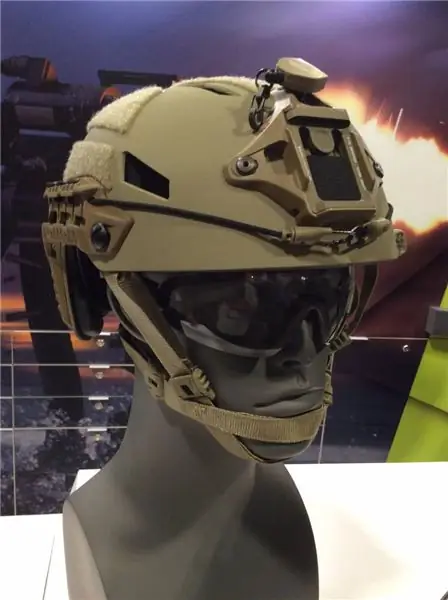
The first part of the article:
Lightweight and high-tech protective materials. Part 1