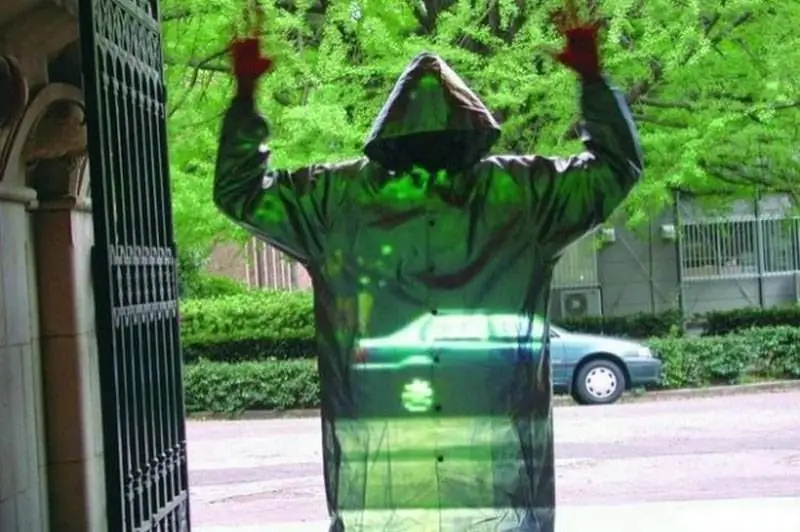
The possibility of creating a material with a negative angle of refraction was predicted back in 1967 by Soviet physicist Viktor Veselago, but only now are the first samples of real structures with such properties appearing. Due to the negative angle of refraction, the rays of light bend around the object, making it invisible. Thus, the observer notices only what is happening behind the back of the person wearing the “wonderful” cloak.
To gain an edge on the battlefield, modern military forces are turning to potentially disruptive capabilities such as advanced body armor and vehicle armor, and nanotechnology. innovative camouflage, new electrical devices, super-accumulators and "intelligent" or reactive protection of platforms and personnel. Military systems are becoming more complex, new advanced multifunctional and dual-use materials are being developed and manufactured, and the miniaturization of heavy-duty and flexible electronics is taking place by leaps and bounds.
Examples include promising self-healing materials, advanced composite materials, functional ceramics, electrochromic materials, “cyber-shielding” materials that react to electromagnetic interference. They are expected to become the backbone of disruptive technologies that will irrevocably change the battlefield and the nature of future hostilities.
Next-generation advanced materials such as metamaterials, graphene and carbon nanotubes are generating great interest and investment because they have properties and functions that are not found in nature and are suitable for defense applications and tasks performed in extreme or hostile spaces. Nanotechnology uses nanometer-scale materials (10-9) in order to be able to modify structures at the atomic and molecular levels and create various tissues, devices or systems. These materials are a very promising area and in the future can have a serious impact on combat effectiveness.
Metamaterials
Before continuing, let's define metamaterials. Metamaterial is a composite material, the properties of which are determined not so much by the properties of its constituent elements as by an artificially created periodic structure. They are artificially formed and specially structured media with electromagnetic or acoustic properties that are technologically difficult to achieve, or are not found in nature.
Kymeta Corporation, a subsidiary of Intellectual Ventures, entered the defense market in 2016 with an mTenna metamaterial antenna. According to the director of the company Nathan Kundz, a portable antenna in the form of a transceiver antenna weighs about 18 kg and consumes 10 watts. Equipment for metamaterial antennas is about the size of a book or netbook, has no moving parts, and is manufactured in the same way as LCD monitors or smartphone screens using TFT technology.
Metamaterials are composed of subwavelength microstructures, that is, structures whose dimensions are less than the wavelength of the radiation they must control. These structures can be made from non-magnetic materials such as copper and etched onto a fiberglass PCB substrate.
Metamaterials can be created to interact with the main components of electromagnetic waves - dielectric constant and magnetic permeability. According to Pablos Holman, an inventor at Intellectual Ventures, antennas created using metamaterial technology could eventually supplant cell towers, landline telephone lines, and coaxial and fiber optic cables.
Traditional antennas are tuned to intercept controlled energy of a specific wavelength, which excites electrons in the antenna to generate electrical currents. In turn, these encoded signals can be interpreted as information.
Modern antenna systems are cumbersome because different frequencies require a different type of antenna. In the case of antennas made of metamaterials, the surface layer allows you to change the direction of bending of electromagnetic waves. Metamaterials exhibit both negative dielectric and negative magnetic permeabilities and therefore have a negative refractive index. This negative refractive index, not found in any natural material, determines the change in electromagnetic waves when crossing the border of two different media. Thus, the receiver of a metamaterial antenna can be electronically tuned to receive different frequencies, which makes it possible for developers to achieve broadband and reduce the size of antenna elements.
The metamaterials inside such antennas are assembled into a flat matrix of densely packed individual cells (very similar to the placement of pixels on a TV screen) with another flat matrix of parallel rectangular waveguides, as well as a module that controls the wave emission through software and allows the antenna to determine the direction of radiation.
Holman explained that the easiest way to understand the merits of metamaterial antennas is to take a closer look at the physical apertures of the antenna and the reliability of Internet connections on ships, airplanes, drones and other moving systems.
“Every new communications satellite launched into orbit these days,” Holman continued, “has more capacity than the constellation of satellites had just a few years ago. We have enormous potential for wireless communication in these satellite networks, but the only way to communicate with them is to take a satellite dish, which is large, heavy, and expensive to install and maintain. With an antenna based on metamaterials, we can make a flat panel that can steer the beam and aim directly at the satellite.
“Fifty percent of the time the physically steerable antenna is not satellite-oriented and you are effectively offline,” Holman said. "Therefore, a metamaterial antenna can be especially useful in a maritime context, because the dish is physically controlled to point to a satellite, since the ship often changes course and constantly sways on the waves."
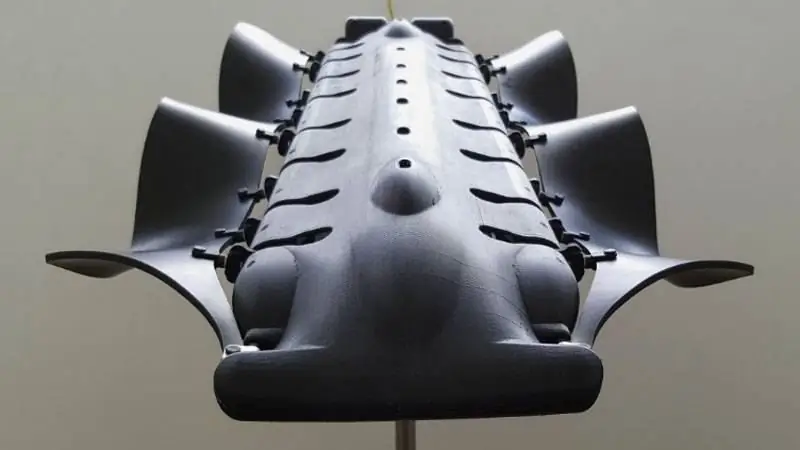
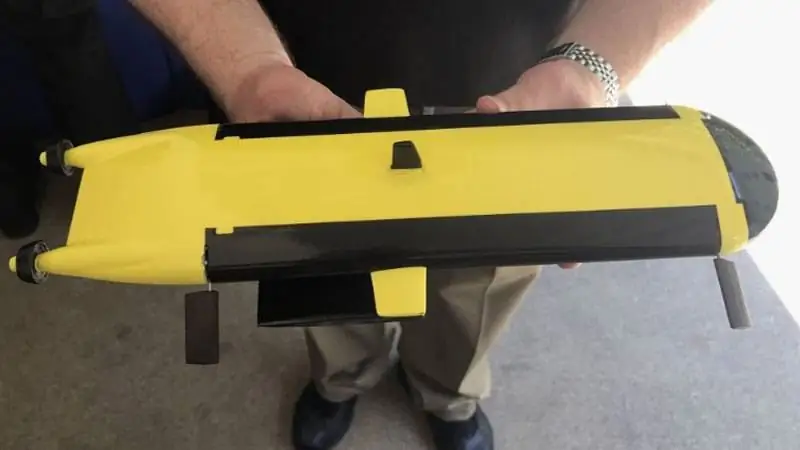
Bionics
The development of new materials is also moving towards the creation of flexible multifunctional systems with complex shapes. Here an important role is played by applied science on the application of principles of organization, properties, functions and structures of living nature in technical devices and systems. Bionics (biomimetic in the Western literature) helps a person create original technical systems and technological processes based on ideas found and borrowed from nature.
The US Navy's Submarine Warfare Research Center is testing an autonomous mine search vehicle (APU) that uses bionic principles. imitating the movements of marine life. The Razor is 3 meters long and can be carried by two people. Its electronics coordinate the work of four flapping wings and two aft propellers. The flapping movements imitate the movements of some animals, such as birds and turtles. This allows the APU to hover, perform precise maneuvering at low speeds and reach high speeds. This maneuverability also allows the Razor to easily reposition itself in space and float around objects for 3D imaging.
The US Navy Research Agency is funding Pliant Energy Systems' development of a prototype for the optionally autonomous Velox submersible, which replaces propellers with a system of multistable, non-linear, paper-like fins that generate repetitive ramp-like undulating movements. The device converts the movements of electroactive, wavy, flexible polymer fins with a planar hyperbolic geometry into a translational movement, freely moving under water, in the waves of the surf, in the sand, over sea and terrestrial vegetation, on slippery rocks or ice.
According to a Pliant Energy Systems spokesman, the undulating forward motion prevents entanglement in dense vegetation, as there are no rotating parts, while minimizing damage to plants and sediment. The low-noise craft, powered by a lithium-ion battery, can improve its buoyancy to maintain its position under the ice, while it can be remotely controlled. Its main tasks include: communication, including GPS, WiFi, radio or satellite channels; intelligence and information gathering; search and rescue; and scanning and identification of min.
The development of nanotechnology and microstructures is also very important in bionic technologies, the inspiration for which is taken from nature in order to simulate physical processes or optimize the production of new materials.
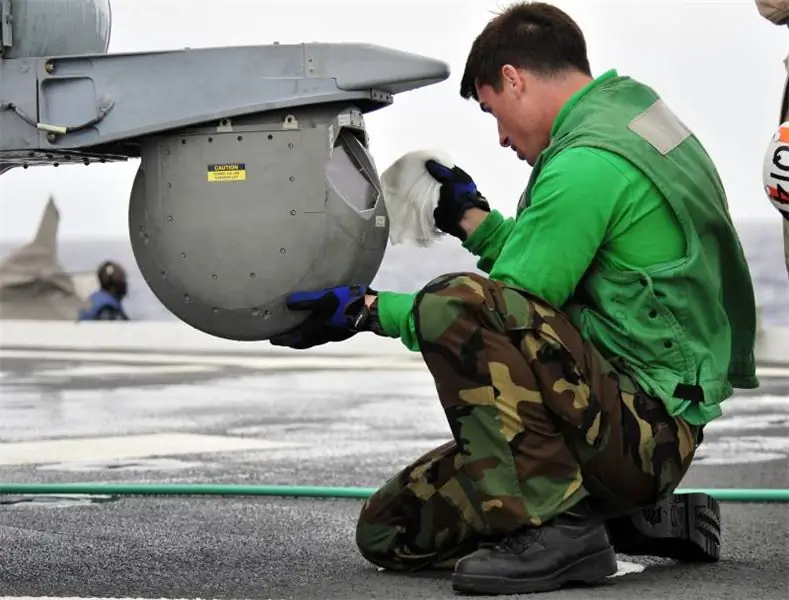
The US Navy Research Laboratory is developing a transparent polymer shield that has a layered microstructure similar to the chitinous shell of crustaceans, but made from plastic materials. This allows the material to remain conformal over a wide range of temperatures and loads, which allows it to be used to protect personnel, stationary platforms, vehicles and aircraft.
According to Yas Sanghera, head of optical materials and devices in this laboratory, the protection available on the market is usually made of three types of plastic and cannot one hundred percent withstand a 9-mm bullet, fired from 1-2 meters and flying from speed 335 m / s.
Transparent armor developed by this laboratory allows a 40% reduction in mass while maintaining ballistic integrity and absorbs 68% more bullet energy. Sanghera explained that the armor could be perfect for several military applications, such as mine-protected vehicles, amphibious armored vehicles, supply vehicles and aircraft cockpit windows.
According to Sanghera, his laboratory intends, based on existing developments, to create a light conformal transparent armor with multi-impact characteristics and achieve a weight reduction of more than 20%, which will provide protection against 7.62x39 mm rifle bullets.
DARPA is also developing transparent Spinel armor with unique properties. This material is distinguished by excellent multi-impact characteristics, high hardness and erosion resistance, increased resistance to external factors; it transmits wider medium-wave infrared radiation, which increases the capabilities of night vision devices (the ability to see objects behind glass surfaces), and also weighs half the weight of traditional bulletproof glass.
This activity is part of DARPA's Atoms to Product (A2P) program, which "develops the technologies and processes needed to assemble nanoscale particles (close to atomic sizes) into systems, components or materials at least on a millimeter scale."
Over the past eight years, the Agency has achieved a reduction in the thickness of the base transparent armor from about 18 cm to 6 cm, while maintaining its strength characteristics, according to the head of the A2P program at DARPA, John Maine. It consists of many different layers, "not all of them ceramic and not all of them plastic or glass", which are adhered to the backing material to prevent cracking. "You should think of it as a defense system, not as a monolithic piece of material."
Spinel glass was manufactured for installation on prototypes of the American Army FMTV (Family of Medium Tactical Vehicles) trucks for evaluation by the Armored Research Center.
Under the A2P program, DARPA awarded Voxtel, an Oregon Institute for Nanomaterials and Microelectronics, a $ 5.59 million contract to research manufacturing processes that scale from nano to macro scale. This bionic project involves the development of a synthetic adhesive that mimics the capabilities of the gecko lizard.
“On the soles of the gecko, there are something like little hairs … about 100 microns long, which branch violently. At the end of each small branch is a tiny nanoplate about 10 nanometers in size. When in contact with a wall or ceiling, these plates allow the gecko to adhere to the wall or ceiling."
Maine said that manufacturers could never replicate these capabilities because they could not create branching nanostructures.
“Voxtel develops production technologies that replicate this biological structure and capture these biological qualities. It uses carbon nanotubes in a really new way, it allows you to create complex 3D structures and use them in very original ways, not necessarily as structures, but in other, more inventive ways."
Voxtel wants to develop advanced additive manufacturing techniques that will produce "materials that are themselves assembled into functionally complete blocks, then assembled into complex heterogeneous systems." These techniques will be based on imitating simple genetic codes and general chemical reactions found in nature that allow molecules to self-assemble from the atomic level into large structures capable of supplying themselves with energy.
“We want to develop an advanced reusable adhesive. We would like to have a material with the properties of an epoxy adhesive, but without its disposability and surface contamination, - said Main. "The beauty of a gecko-style material is that it leaves no residue and works instantly."
Other rapidly advancing advanced materials include ultra-thin materials such as graphene and carbon nanotubes, which have structural, thermal, electrical and optical properties that will revolutionize today's battlefield.
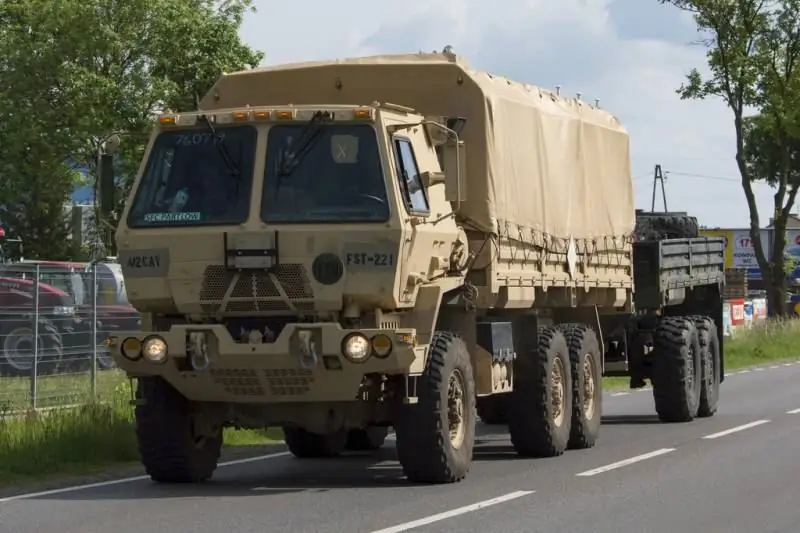
Graphene
While carbon nanotubes have good potential for applications in electronic and camouflage systems, as well as in the biomedical field, graphene is "more interesting because it offers, at least on paper, more possibilities," said Giuseppe Dakvino, a spokesman for the European Defense Agency (EOA).
Graphene is an ultra-thin nanomaterial formed by a layer of carbon atoms one atom thick. Lightweight and durable graphene has record high thermal and electrical conductivity. The defense industry is carefully studying the possibility of using graphene in applications that require its strength, flexibility and resistance to high temperatures, for example, in combat missions performed in extreme conditions.
Dakvino said graphene “is, at least in theory, the material of the future. The reason why there is so much interesting debate now is because after so many years of research in the civilian sector, it has become clear that it will actually change combat scenarios.”
“To list just a few of the possibilities: flexible electronics, power systems, ballistic protection, camouflage, filters / membranes, high heat dissipation materials, biomedical applications and sensors. These are, in fact, the main technological directions."
In December 2017, the EAO began a year-long study of possible promising military applications of graphene and its impact on the European defense industry. This work was headed by the Spanish Foundation for Technical Research and Innovation, with which the University of Cartagena and the British company Cambridge Nanomaterial Technology Ltd. In May 2018, a seminar of researchers and experts on graphene was held, where a roadmap for its use in the defense sector was determined.
According to the EOA, “Among the materials that have the potential to revolutionize defense capabilities in the next decade, graphene is high on the list. Lightweight, flexible, 200 times stronger than steel, and its electrical conductivity is incredible (better than silicon), as is its thermal conductivity."
The EOA also noted that graphene has remarkable properties in the area of "signature management". That is, it can be used to produce "radio-absorbing coatings, which will turn military vehicles, aircraft, submarines and surface ships into almost undetectable objects." All this makes graphene an extremely attractive material not only for the civilian industry, but also for military applications, land, air and sea."
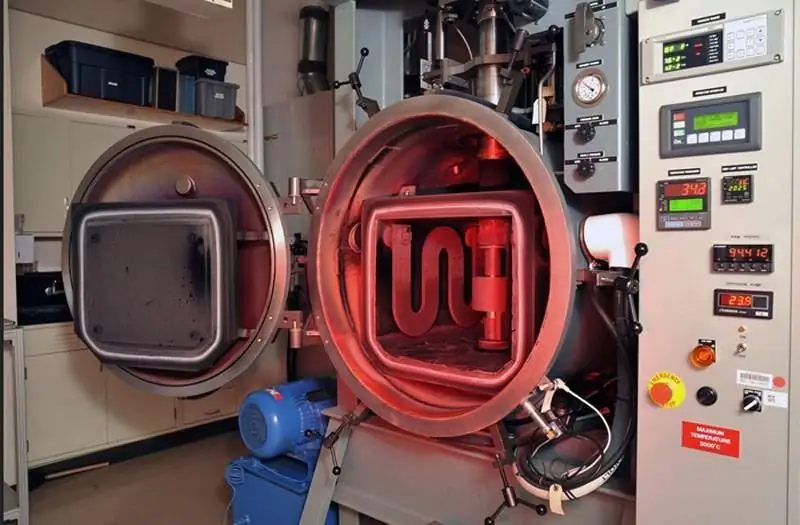
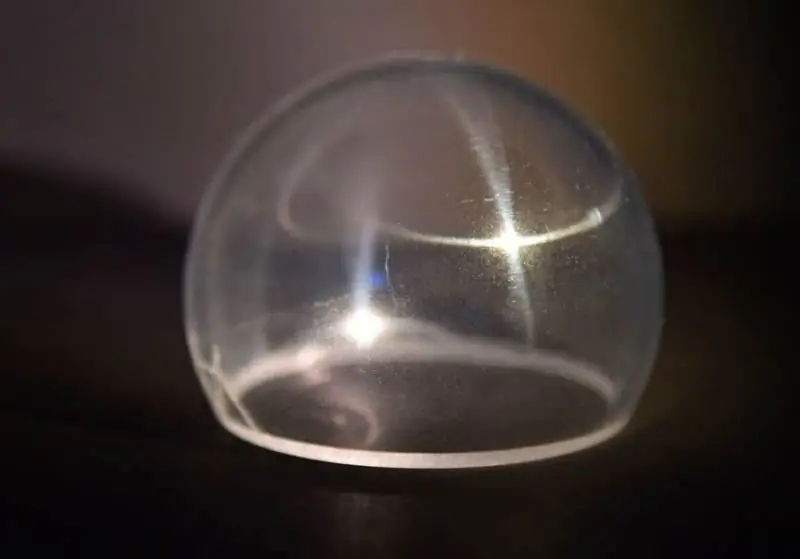
To this end, the US military is studying the use of graphene for vehicles and protective clothing. According to engineer Emil Sandoz-Rosado of the US Army Military Research Laboratory (ARL), this material has excellent mechanical properties, one atomic layer of graphene is 10 times stiffer and more than 30 times stronger than the same layer of commercial ballistic fiber. “The ceiling for graphene is very high. This is one of the reasons why several working groups in ARL have shown interest in it, because its design characteristics are very promising in terms of booking.
However, there are also quite big difficulties. One of them is scaling the material; the army needs protective materials that can cover tanks, vehicles and soldiers. “We need a lot more. In general, we are talking about about a million or more strata that we need at the moment”.
Sandoz-Rosado said that graphene can be produced in one or two ways, either through a peeling process where high-quality graphite is separated into separate atomic layers, or by growing a single atomic layer of graphene on copper foil. This process is well established by laboratories producing high quality graphene. “It’s not quite perfect, but it’s pretty close to it. However, today it is time to talk about more than one atomic layer, we need a full-fledged product”. As a consequence, a program has recently been launched to develop continuous industrial-scale graphene production processes.
“Whether it's carbon nanotubes or graphene, you have to take into account the specific requirements that must be met,” Dakvino cautioned, noting that the formal description of the characteristics of new advanced materials, the standardization of the precise processes for creating new materials, the reproducibility of these processes, the manufacturability of the entire chain (from basic research to production of demonstration and prototypes) need careful study and justification when it comes to the use of such breakthrough materials as graphene and carbon nanotubes in military platforms.
“This is not just research, because after all, you need to be sure that a certain material is officially described and then you need to be sure that it can be produced in a certain process. It is not so easy, because the manufacturing process can change, the quality of the produced product can vary depending on the process, so the process must be repeated several times."
According to Sandoz-Rosado, ARL worked with graphene manufacturers to assess the product's quality class and its scalability. Although it is not yet clear whether the continuous processes, which are at the beginning of their formation, have a business model, the appropriate capacity and whether they can provide the required quality.
Dakvino noted that advances in computer modeling and quantum computing could accelerate research and development, as well as the development of methods for the production of advanced materials in the near future. “With computer-aided design and material modeling, many things can be modeled: material characteristics and even manufacturing processes can be modeled. You can even create virtual reality, where you can basically look at the different stages of creating a material."
Dakwino also said that advanced computer modeling and virtual reality techniques provide an advantage by creating an "integrated system where you can simulate a particular material and see if that material can be applied in a particular environment." Quantum computing could radically change the state of affairs here.
"In the future, I see even more interest in new ways of manufacturing, new ways of creating new materials and new manufacturing processes through computer modeling, since the enormous computing power can potentially only be obtained by using quantum computers."
According to Dakwino, some applications of graphene are technologically more advanced, while others are less. For example, matrix-based ceramic composites can be improved by integrating graphene plates that reinforce the material and increase its mechanical resistance while reducing its weight. “If we are talking, for example, about composites,” continued Dakvino, “or, in the most general terms, about materials reinforced by adding graphene, then we will get real materials and real processes of their mass production, if not tomorrow, but maybe in the next five years.
“This is why graphene is so interesting for ballistic protection systems. Not because graphene can be used as armor. But if you use graphene in your armor as a reinforcing material, then it can become stronger than even Kevlar."
Priority areas, for example, autonomous systems and sensors, as well as high-risk military areas, such as underwater, space and cybernetic, most of all depend on new advanced materials and the interface of nano- and microtechnology with biotechnology, “stealth” materials, reactive materials and energy generation and storage systems.
Metamaterials and nanotechnology such as graphene and carbon nanotubes are undergoing rapid development today. In these new technologies, the military is looking for new opportunities, exploring their applications and potential barriers, as they are forced to balance between the needs of the modern battlefield and long-term research goals.