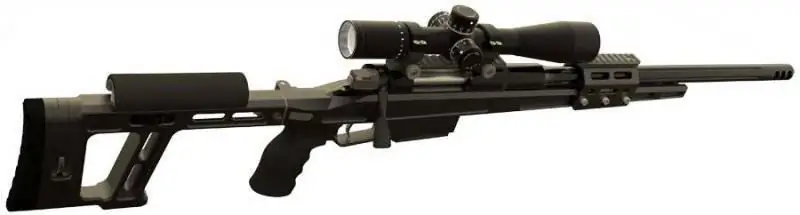
Is it possible in Russia from scratch to create a private plant specializing in the production of high-precision small arms? The experience of the Promtechnologii group of companies shows that this is possible. But is it realistic to withstand competition with eminent foreign firms and, in part, large state-owned arms factories? The specialists of the Promtechnologii Group of Companies are full of optimism and believe that they will be able to occupy their niche not only in the Russian but also in foreign arms markets. And perhaps - and not only in this highly specialized segment.
Most of our fellow citizens who have at least some idea of sniper shooting, at the mention of the phrase "sniper rifle" will imagine SVD. Dragunov's sniper rifle, without exaggeration, can be called an outstanding example of small arms designed for solving special tasks. However, the role that was assigned to the SVD in the Russian, and earlier in the Soviet army, differs somewhat from the generally accepted standards for the use of sniper weapons in most of the world's armed forces. SVD is primarily intended to increase the effective firing range at those distances at which aimed firing from standard weapons, that is, a Kalashnikov assault rifle, is no longer possible for a shooter with an average level of training - that is, at distances from 100-150 to 500-600 meters. Sniper shooting in the strict sense of the word involves aimed fire at ranges from 600 to 1000 meters. For this, as a rule, bolt-action rifles are used, while the SVD is self-loading. This does not mean that weapons of this class are not used in modern warfare. For example, after the start of operations in Iraq and Afghanistan, the Pentagon decided to re-transfer to the troops the self-loading M21 sniper rifles, which were in service until 1988 and then replaced with various modifications of the bolted Remington 700.
Until recently, there was no alternative to SVD in our country. The military was forced to satisfy the need for precision weapons through imports. The most popular among Russian snipers is the AW (Arctic Warfare) rifle of the British company Accuracy International. Of course, one cannot fail to mention the SV-98 bolt-action rifle developed not so long ago at Izhmash. However, its quality does not satisfy everyone. So the need to create a high-tech production of modern sniper weapons is obvious.
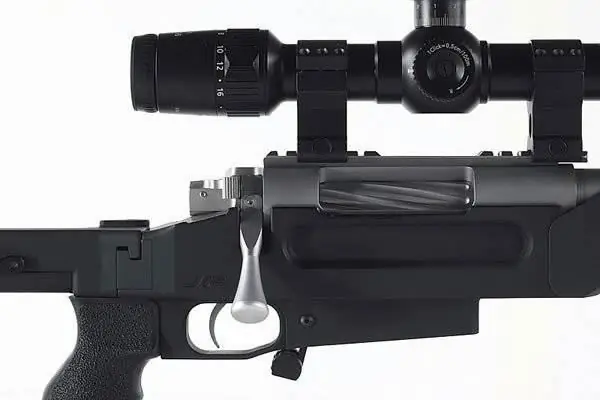
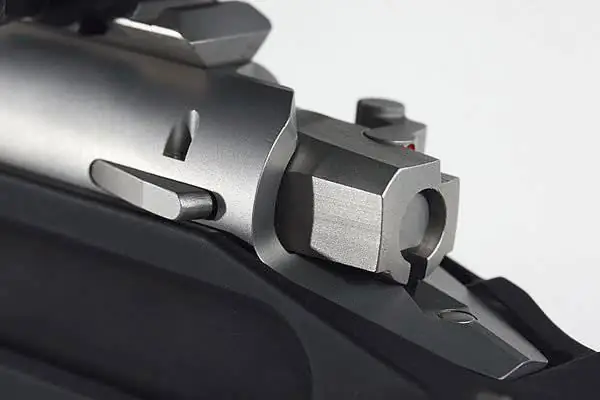
The ideologist of the creation of such a production was Alexey Sorokin, General Director of the Promtechnologii Group of Companies, the USSR Master of Sports in bullet shooting, one of the leading Russian experts in precision small arms. In an unprecedentedly short time, a new arms factory was built and equipped with the most modern high-tech equipment in Moscow, where the first barrel was manufactured in November 2010, and the first rifle was assembled in February of this year.
It should be noted that in Russia, the pioneer on this path was Vladislav Lobaev, who founded in the mid-2000s. a small firm "Tsar Cannon". For a number of reasons, it failed to withstand competition with Western manufacturers. One of them was a small volume of production and a limited range. But most importantly, "Tsar Cannon" did not manufacture all the components of the weapon, using components from third-party, mainly American, manufacturers. Therefore, the final product, with all its merits, took a long time to manufacture and was very expensive. The Promtekhnologii Group of Companies chose a different path and launched full-cycle serial production. Only a few parts of rifles produced under the ORSIS brand - bipods, rubber butt-pads and magazines - are not yet made in-house. The main components of the rifles - the barrel, the bolt group, the trigger, the stock - are designed and manufactured independently. The volume of production is also impressive: if Tsar Cannon made no more than 80 rifles a year, then at the Moscow arms plant of the Promtechnologii Group of Companies it is planned to produce at least 25 different rifles a day.
According to Aleksey Rogozin, Deputy General Director of Promtechnologii Group of Companies, this production volume is planned to reach approximately by the summer of 2012. The final products of the plant are magazine and single-shot hunting, sporting and tactical rifles, both serial and custom-made.
The plant has its own design bureau, which today is one of the leading Russian research centers in the field of creating advanced models of small arms. The bureau is equipped with modern research equipment, test benches and installations that allow for complex scientific research and development work on defense and civilian issues. This applies not only to the design of weapons, but also to technologies, machines, tools.
The most difficult technological process in the production of high-precision rifles (although there are no "frivolous" or secondary stages in this matter, because the final result is influenced by any little thing) - the manufacture of rifling of the barrel. At the arms plant of the Promtechnologii Group of Companies, two methods of their manufacture are used: backing and single-pass cutting (trellis planing).
In the process of dornning, a special hard-alloy tool, a mandrel, is pulled through the barrel bore under pressure. The profile of the mandrel, which has a larger diameter than the barrel bore, squeezes out the grooves on its inner surface when moving. After broaching for almost two days, the barrel is heat treated in an electric furnace, during which two tasks are solved: the voltage in the metal is removed and the barrel is compressed in a controlled manner to the required size. To date, the plant of the Promtechnologii Group of Companies is the only Russian manufacturer of stainless steel barrels using the dornning technology.
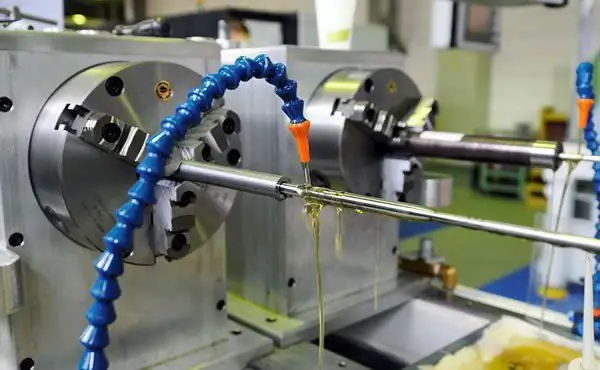
The production of the barrel by the single-cut method allows making the most accurate rifles.
Single-pass cutting (trellis planing) is the oldest, very long, but also the most perfect of all the methods of making rifling that exist today. A special cutter, called a trellis, removes about 1 micron of metal for each pass through the bore without creating any tension in the workpiece. It takes 80-100 passes to make one rifling, and the barrel is finished in about 2 hours. The machines for single-pass cutting are computer controlled and were designed in the plant's design bureau with the assistance of consultants and component suppliers from Switzerland and Germany. Taking the classic English machines for single-pass cutting as a basis, redesigning them and developing an original computerized control system, the specialists of Promtechnologii Group of Companies were able to create a fundamentally new technology. A 10-ruble coin can be put on the edge of the moving part of the machine, which pulls the trellis through the barrel bore, and it will not fall, it will stick like a glued one, which indicates the absence of vibration, which means the highest accuracy when processing the workpiece. The barrel made in this way has an almost ideal geometry: the accuracy deviation in the rifling depth is less than 0.001 mm, in the rifling pitch - 0.004 mm! The tolerances are virtually equal to those of the measuring equipment. In addition, this technological process is very flexible - it allows you to set parameters for the width and depth of the rifling, according to their number, it allows you to make a variable pitch of the rifling, which is required for firing heavy bullets. In general, this technology is unique not only for Russia, but also for Europe.
The plant's equipment allows the manufacture of barrels up to 1050 mm long for ammunition of 20 calibers from 5, 6 to 20 mm. For their production, American stainless steel 416R is used - the world's best material for such products. The barrel and receiver can be coated with a wear-resistant Cerakote ceramic coating that is extremely resistant to corrosion and mechanical damage.
After each technological operation, instrumental control of the manufactured parts is carried out not only at the sites, but also in the production and testing laboratory with the help of digital and optical measuring instruments, which makes it possible to catch problems not at the level of finished products, but at the level of semi-finished products and eliminate the shortcomings in a timely manner. The laboratory maintains constant humidity and temperature, which allows all measurements to be carried out under the same conditions.
For the manufacture of boxes, a special weapon-grade wood laminate, wood, carbon, fiberglass is used. Weapon-grade wood laminate (in fact, it is thick plywood) has a number of advantages over solid wood: it is practically unaffected by moisture or temperature changes, which is important from the point of view of maintaining the rifle's geometry. Each ORSIS rifle stock undergoes a glass bedding procedure - a special treatment of the recess for the barrel and receiver. For foreign manufacturers, glass bedding is an additional service provided for a fee.
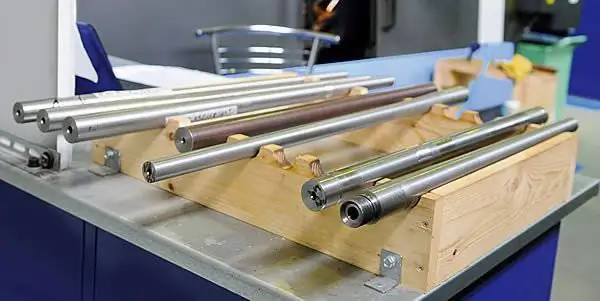
At the GK Promtechnologii plant, you can order a rifle of one of 20 calibers - from 5, 6 to 20 mm.
In fact, the "Promtechnologii" plant has introduced into mass production the technologies used in the unit production of benchrest rifles - a type of bullet shooting, which is often called "Formula 1" of shooting sports. In benchrest, the shooter's job is to fire five (or ten, depending on competition conditions) shots at a valid target with as little dispersion as possible. “When firing from our serial rifles, even with an ordinary cartridge, we got an accuracy of 0, 29 arc minutes - a spread of less than 1 cm in a group of 5 shots when firing at 100 meters. This is a very good indicator, allowing an ORSIS rifleman to compete in international tournaments. I think in due time we will show that with these rifles it is possible to win the most prestigious competitions, - says Alexey Rogozin. "Nobody makes such rifles in Russia, in Europe - 2-3 companies."
Russian Defense Minister Anatoly Serdyukov recently visited the enterprise. It is planned to test several combat models of ORSIS rifles. If they are successful, our army snipers will have a top-class domestic-made rifle. The most likely model for military needs is the ORSIS T5000 tactical rifle in.308 Win caliber. It has a folding butt made of aluminum, a magazine for 10 rounds.
Among the potential directions of the company's development is the production of high-quality cartridges suitable for high-precision shooting, the organization of shooting ranges accessible to athletes and hunters, allowing them to fire from rifles at long distances.
Of course, the new manufacturer has a lot of problems in terms of market development. This is both the already formed negative perception of Russian-made weapons, and the lack of mass interest in high-precision shooting. But the creators of ORSIS rifles are confident that all these problems are solvable.