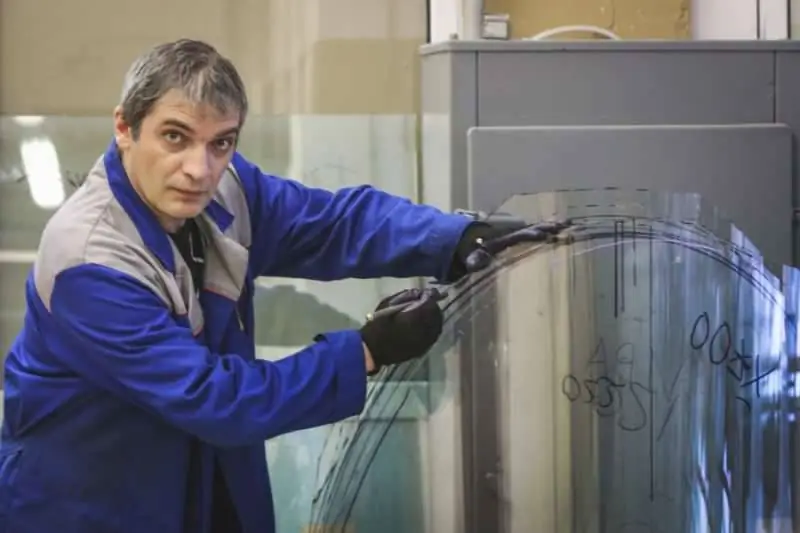
In Russia, new technologies have been developed for the manufacture of glazing of the cabins of military and civil aircraft from silicate glass. Such products turn out to be lighter and stronger than if they were created from previously used organic materials. Silicate glass is also used in other fields, from space exploration to housing construction.
For several years now, there has been a debate among space researchers over the safety assessment and operation of the International Space Station. The fact is that there are 13 windows installed in the Russian segment of the ISS. During joint discussions of the ISS, it is proposed to close the windows in the Russian segment with blind plugs because of the danger of defects in the glass due to impacts of micrometeorites - they say, the safety of the station could improve. But the representative of the Russian side - the director of the Scientific Research Institute of Technical Glass (NITS), Honored Scientist, Vice President of the Academy of Engineering Sciences of the Russian Federation, Doctor of Technical Sciences, Professor Vladimir Solinov stands his ground - for many years the residual strength after the impact of space microparticles has been preserved and, various radiation and other threats from space did not affect the safety of the windows created at the institute, as well as the crew, therefore there are no reasons to limit the observation of our planet, "obscure" the work of cosmonauts in the Russian modules of the orbital station.
Portholes for the orbital station are just one of the few products manufactured by NITS. The main part of the work of scientists and technologists of the institute located in the south-west of Moscow, of course, is associated with the creation of structural optics, glazing, or as they say here "complex transparent optical systems" for combat aircraft of the fourth and fifth generations produced by the UAC plants. And every year there is much more work for aviation.
Silicate or organic
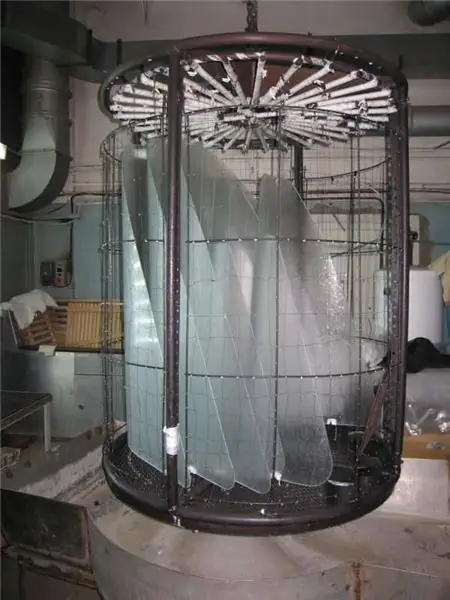
In the photo: T-50 windshield blanks in a hardening cassette.
Silicate glass is a material with unique properties. Its transparency, high optics, heat resistance, strength, and the ability to use various coatings make it irreplaceable for aircraft glazing. But why was the priority given to organic matter when glazing aircraft cabins abroad and in our country? For one reason only - it is easier. They also say that silicate glass is too fragile.
In the last few years, the developments of NITS materials scientists have made it possible to radically change the concept of silicate glass as a brittle material. Modern methods of strengthening make it possible to give the glazing for modern combat aircraft strength sufficient to withstand the impact of a bird weighing about two kilograms at a speed of 900 km / h.
“Today, the method of hardening in the surface layer has exhausted itself. It's time to change the internal structure of the glass, its defectiveness,”says Vladimir Solinov. Strange as it may seem, this is facilitated by the sanctions imposed by the West. The fact is that even in the "pre-sanction" times, foreign firms, by NATO decision, did not supply to Russia silicate glasses of improved quality, which were used there for special purposes. This forced NITS to use architectural glass. Although Russian manufacturers produce millions of square meters of such glass, its quality is not suitable for use in aviation.
Import substitution came to the rescue: a new project for R&D and design of equipment that was fundamentally new for the glass industry was launched in Moscow.
All glass synthesis processes with Russian priority will be tested on it.
The project was entrusted to the young scientist Tatiana Kiseleva. 26-year-old graduate of the Russian University of Chemical Technology. D. I. Mendeleeva is the head of the laboratory, in 2015 she defended her thesis. At the glass department in Mendeleevka, Tatiana studied the properties of transparent armor. One of her professional challenges is to develop glass that would surpass in its properties one of the world's best analogs - herkulit glass, which Russia does not yet produce.
The project is based on a new original method of glass melting. Already today, the laboratory has obtained glass samples, the structural strength of which is three times higher than the analogs obtained by the traditional method. Add to this the existing methods of hardening, and you get glass, the strength of which is several times higher than many types of alloy steel. More durable glass makes lighter products. However, it should be noted that the developers of organic glass are constantly improving the technical performance of their products, the dispute about which glass is better is not over.
Lantern for T-50
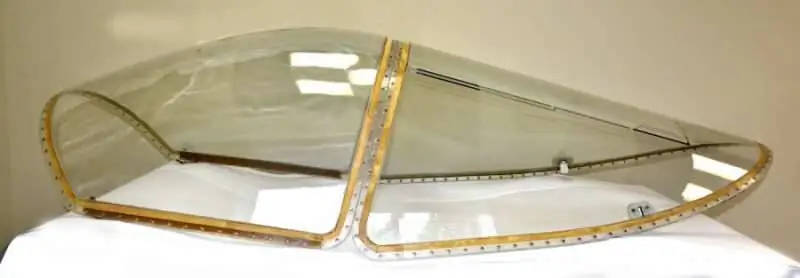
In the photo: a set of glazing for a T-50 aircraft - a frontal visor and a folding part.
Imagine a package of several silica glass plates that you want to streamline the front visor of a high-speed aircraft.
About forty years ago, NITS specialists developed the technology of deep bending. Several layers of glass are laid in a special oven. For several hours at high temperatures under its own weight, the glass bends, acquiring the desired shape and curvature. If necessary, special mechanisms push the workpiece, forcing it to bend according to a special schedule.
For the first time in the world, using this technology, the MiG-29 fighter has replaced the lantern, which consisted of three glasses, with one glass free from silicate.
With an increase in the speed, the requirements for the heat resistance of the glazing increased, with which organic glass could no longer cope. At the same time, the optical and visibility requirements were tightened. Several years ago, in cooperation with the Sukhoi Company, the United Aircraft Corporation, a new technology for the production of glass for the T-50 was developed.
The development was funded by aircraft manufacturers, partly by the Ministry of Industry and Trade. Substantial assistance was rendered in carrying out the technical re-equipment of the enterprise, says Yuri Tarasov, director of the UAC Technology Center.
As a result, the windshield of the T-50 aircraft is almost twice the size of the visor of the MiG-29, and the shape of the product from a classic cylinder has turned into a complex 3D format.
The result - for the first time in the world, the frontal and folding part of the T-50 aircraft canopy (manufactured by Sukhoi) was made of silicate glass in 3D format. Moreover, the weight of these parts turned out to be lower than if they were made of organic glass.
The results achieved gave impetus to equipping aircraft of other factories and design bureaus that are part of the UAC with similar glazing. Immediately there was a need for modernization, replacing organic glazing with silicate, for example, on the Yak-130, Su-35, MiG-31, MiG-35 aircraft. After such a replacement (that is, improving the strength characteristics of the glazing), the MiG-35, for example, for the first time reached a speed of up to 2000 km / h, that is, it was able to fly 40% faster on average than any other aircraft in the world.
In recent years, the style of work of Moscow scientists has seriously changed. About three hundred NITS specialists perform a full cycle - from technical specifications to small-scale production. This includes the development of technology, and the selection of key materials when using glass, and a large test cycle for all factors affecting the aircraft, both on the ground and in the air.
Several key requirements are imposed on modern glass, among which, in addition to high strength, are optical transparency, high light transmission, increasing the viewing range, anti-reflective properties, protection from the effects of solar radiation and other radiation, anti-icing properties, ensuring uniform electrical resistivity.
All this is achieved by aerosol, vacuum or magnetron coating. Powerful and sophisticated equipment evaporating metal and depositing it on the glass surface allows NITS to apply any coatings, including those protecting against special factors.
This set of properties makes it possible to speak of a glazing product as a complex optical system, and the high strength properties of glass, which is part of the aircraft cockpit, created a new field of science and technology and introduced the term “structural optics products” (ICO).
New technologies
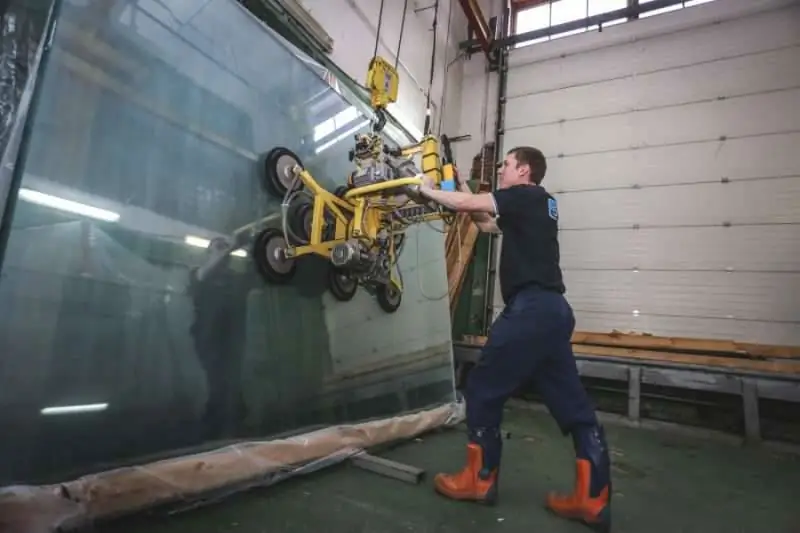
In the photo: loading a sheet of glass for further processing.
When the product - the hinged part of the lantern for the T-50 - is unloaded from the furnace for further processing, it hardly resembles a future product. When bending glass, the edges of the workpiece are deformed, and it is impossible to remove them from a large-sized workpiece, which has a complex geometric shape, with a diamond tool. The laser came to the rescue. The laser beam of the robotic complex not only cuts the workpiece according to the program laid down in it, but also, by melting the edge, increases the strength of the edge of the products, preventing the appearance of cracks. Laser cutting of large-sized 3D products was first used in Moscow. This method was patented in March 2012. The laser beam is also used to cut off the electrically conductive layer on the glass surface, creating heating zones. After laser processing, the workpiece looks more and more like a T-50 flashlight.
After cutting, each workpiece is processed on a five-axis machine. The unique lodgment allows it to provide zero initial mounting stresses on it. The chief technologist of the institute, Alexander Sitkin, spoke about the prospects for using the complex for grinding and polishing the glass surface: work that, if necessary, is carried out only manually. The developed technologies are the pride of the institute.
More recently, a finished glass block with the help of a sealant was mounted in a metal frame. The transition to composite materials developed by NITS made it possible to reduce the weight of the product by 25%, to increase bird resistance and the glazing resource to the level of the glazing glazing resource. It became possible to replace the glazing in the field.
The entire production cycle of the ICO lasts about one and a half months. Most of the products go to the UAC manufacturing plants, some go to repair plants for modernization, and some go to the airfields of the Air Force, in the so-called first-aid kits. The main part of NITS products is carried out within the framework of the state defense order.
NITS is reluctant to share information about the characteristics of glazing for combat aircraft. But it is clear that the glasses developed for the cockpits of domestic civil aircraft are superior to imported ones in a number of parameters.
For example, as can be seen on the NITS website, the thickness of the glass on the Tu-204 is 17 mm, the thickness of the glass with the same properties for the Boeing 787 is 45 mm.
Generation V
In the past few years, the director of the institute, Vladimir Solinov, has managed to significantly rejuvenate the team. Both young people and experienced specialists work at the Moscow production, which recently celebrated its 60th anniversary. Senior students of Mendeleevka willingly come here. Coming to practice at the institute and learning that there are salaries of 70 thousand rubles, at first they are employed by ordinary workers, then they quickly grow to the level of technologists. There are also many experienced workers.
One of them, Nikolai Yakunin, processes glass for helicopters. “I came here right after the army, forty years ago. But if it were not for the high level of automation, it probably would not have survived. It's hard for me to work all day even in good physical shape with a product weighing 30 kg,”says Yakunin.
People and nails
All over the world, technologies developed for aircraft construction that allow the production of glasses of the required strength are used in many other sectors of the national economy.
Several years ago, to prove the high strength of silicate glass, the institute made … glass nails. They beat me with a hammer. They could find application in products with anti-magnetic properties.
Also, these nails were tested during construction, instead of clamps when gluing yacht hulls. But the nails remained only exotic. Now no one needs to prove the high strength of glass - all the works of NITS are evidence of the high quality of this ancient and, at the same time, completely new material.
Institute Director Vladimir Solinov uses all his capabilities to prove the need to ensure high strength of glass, including architectural and construction.
He is a member of the Russian-American Commission on Space Safety, which was discussed at the beginning of this article, as well as the Commission on Urban Development under the State Duma - after all, in the construction of modern buildings, more and more of the materials are glass. This means that technologies and materials developed for aviation will in the near future make the lives of millions of people more comfortable and safe.