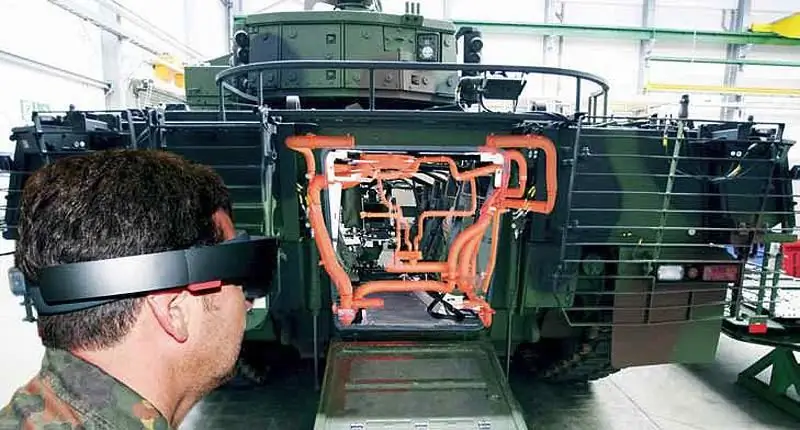
For a modern commander, one of the first tasks is to ensure the readiness of the weapons and equipment of his subunit for work at any time. Lack of sufficient (read: staffing) numbers can mean a decrease in firepower or the ability to concentrate warheads of the correct size in a precise location and at a precise time. Maintaining high combat readiness is especially critical for troops participating in expeditionary operations. Here, the commander is severely limited by the forces and means that are delivered by sea or by air, he must maintain all systems in good condition and be able not only to conduct operations, but also maintain sufficient potential until supplies are replenished. When carrying out maintenance and repair, expeditionary units face unique problems that units with traditional rear workshops do not face, since most of the work must be carried out on the principle of "self-sufficiency". Undoubtedly, systems are becoming more complex, more difficult to repair and maintain, but technologies are emerging that simplify this work and allow it to be done faster and at a lower organizational level.
Integrated condition monitoring systems
In the past, maintenance was carried out on a schedule based on specific periods of time, such as annually or upon reaching a certain number of kilometers or hours. These scheduled maintenance often did not reflect actual wear and tear or need. On the other hand, repairs were made only when a malfunction actually happened and something broke. The malfunction could have occurred during the operation, depriving the commander of the failed component until the repair was completed. The Integrated Condition Monitoring System (ISMS) allows predictive maintenance and repairs by continuously collecting, storing and cataloging data on the use and condition of various components of a vehicle, aircraft, or other subsystems.
This database is then either analyzed by on-board computers or downloaded by technicians and compared with a large database of statistics to determine possible component failure.
The vice president of ISMS manufacturer North Atlantic Industries said that “once the probable failures and failures have been identified, appropriate corrective action can be taken. Our solutions enable repair personnel to better predict service based on the actual performance and condition of the component itself or parts of it, rather than waiting for a component to fail.” ISMS can be embedded in a variety of platforms, but their use in aircraft and vehicles is especially attractive. They provide new opportunities, including improved service and repair efficiency while dramatically reducing downtime.
The practical value of continuous monitoring of parameters and state of subsystems was demonstrated by a representative of Bell and Boeing when describing the ISMS built into the next generation V-280 Valor tiltrotor. The V-280 tiltrotor system not only detects a broken node, but can also automatically report it to the maintenance team on the ground, even during its flight. With this information, personnel on the ground can get everything they need and make repairs as soon as the machine returns. With the advent of digital wireless networks and integrated messaging, these same capabilities can be built into virtually any system. Predictive repairs can prevent and correct the problem in advance.
Built-in on-board diagnostics
By combining ISMS and local data processing, you can get built-in on-board diagnostics. On-board diagnostics provide the crew with an initial indication of a possible malfunction or breakdown, and is also the basis for deeper analysis by the technician. These systems continuously monitor and, in some cases, record the performance history of various key components of the underlying platform. As a result, they allow you to proactively detect problems and fix them before something more serious happens. Oshkosh Defense's Command Zone system includes on-board diagnostics as part of a wider, platform-integrated digital network. The Command Zone can not only carry out self-diagnostics, but also periodically or, if necessary, report its status to external control devices. Thus, the availability of the system largely depends on the knowledge of the technical staff, who can evaluate and plan preventive maintenance. The result is a purely "conditional maintenance" that can lead to preventive maintenance that increases the system's availability for the intended operation.
Quick change blocks
Since maximizing the availability of systems is the main goal of maintenance and repair work, it directly follows that the time and effort required to return a system, especially a critical combat system, to service, should ideally be minimal. The concept of quick-change blocks would be a good solution here. According to it, the components of the designed system should be easily accessible, easy to remove and replace. The quick-change component is repaired at a later date, with the front line technician focusing on getting the entire system back on track as soon as possible. Originally adopted in aviation, this practice has been widely extended to land and sea systems. A representative from Denel Vehicle Systems explained that “Optimization for maximum operational readiness is the main goal of our combat vehicle projects. For example, the RG35 armored vehicle implements a quick replacement of subsystems with a minimum number of operations. The suspension can be replaced with just four bolts, and even the dash can be removed and replaced in less than 15 minutes. The quick-change block method is equally useful in repairing combat damage as it allows for front line repairs that would otherwise be impractical or require evacuating the vehicle to the rear.
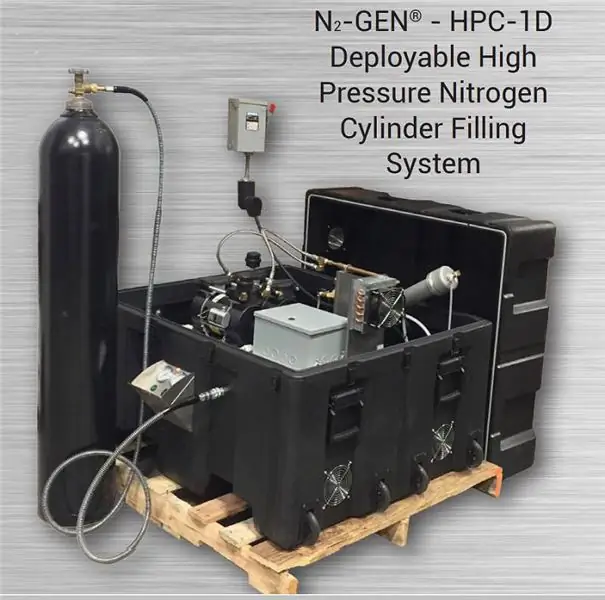
3D printing
It is very important to have the necessary part available for the repair. Deployed troops can only take a limited number of parts with them, so if the required component is not on hand, repairs cannot be made. Over the past few years, 3D printing technology has been thoroughly studied. which allows you to make a specific part on site even in the field. A project manager at the US Marine Corps Systems Development Authority explained that “ZD technology, also called adaptive, allows one part to be printed as needed. These technologies and processes essentially transform digital files into physical objects. A digital file can be created by scanning an existing object or by using a computer-aided design system. The program sends instructions to the 3D printer, which prints the object, adding layers of material until a finished product is obtained."
The US Navy began using 3D printing on board its ships in 2014 to replicate the required parts. Since then, the Marines and the US Air Force have begun to integrate these capabilities into their service and logistics structures. The US and Indian militaries have also begun programs to integrate digital direct manufacturing into their supply chains. The main advantage here is the ability to ship parts to the user faster, resulting in less downtime while waiting for repairs. In addition, it is possible to transfer digital data required to reproduce the part from remote production to the user's position, which also speeds up the repair process. This method is also suitable for the production of parts for obsolete equipment that are no longer in production and for which parts are difficult to obtain.
The use of 3D printing is especially attractive to expeditionary forces. Using ZD-printing on site can eliminate the need to transport stocks of spare parts and reduce costs, and help improve the efficiency and combat readiness of troops. Since some of the supplies can be invented in the field, this will make the military more innovative. In addition, ZD printing requires cheaper raw materials rather than finished products.
The USMC has already demonstrated the X-FAB deployable 3D printing complex. It includes computers with CAD software; storage of digital drawings for 3D printing; handheld 3D scanner; uninterrupted power supply unit; large format 3D printer Cosine; 3D printer LulzBot TAZ; and desktop composite printer Markforged; they all belong to the class of extruder machines. Although the complex is currently only capable of producing parts from plastic, plans are being hatched to include printers that print parts from metal powder. Parts made by the X-FAB complex are available in just a few hours, as opposed to receiving them through the spare parts ordering system, which can take days or weeks.
3D printing becomes even more attractive when combined with ISMS and real-time fault reporting. The ability to have on-site manufacturing of parts reduces the concern that a required part may not be in stock.
On-site consumables
The need for self-sufficiency is not limited to details. Many categories of military equipment, including vehicles, aviation and artillery, require different fluids or special gases to operate their subsystems, for example, suspension travel controls, rollback mechanisms, fire extinguishing systems, day optics, night vision systems, and even tires. They can be delivered to the places of permanent deployment by the supplier, which is called "right to the door". During deployment or in field camps, technicians must have these substances on hand, many of which are harmful and dangerous during storage and transport, especially in the combat zone. The ability to obtain these substances as needed and as close to the consumer as possible allows for the most part to eliminate these hazards while ensuring the availability of the product at any time.
One of these substances is compressed nitrogen. It is used in night vision systems, suspension systems, helicopter racks, various control systems, fuel tanks and tires of drones and aircraft. Heavy compressed nitrogen cylinders are difficult to handle and can be hazardous if damaged.“The Marines were the first to accept field-deployed nitrogen generators for supply,” explained Scott Bodman of South-Tek Systems. “It has integrated our compact, separate N2 Gen low pressure nitrogen generation unit into its optoelectronic maintenance systems in Iraq and Afghanistan. These field workshops included everything needed to maintain and repair scopes and night vision devices. The N2 Gen generates nitrogen from air, operates on a portable power source, and supplies nitrogen to consumers anywhere, eliminating the need for external suppliers. These systems allow marines to quickly repair and return scopes and night vision devices back to fighters. The increasing use of advanced active suspensions and the growing use of nitrogen for military purposes have led South-Tek to also develop a fully deployable high pressure nitrogen generation system, designated N2 Gen HPC-1D. Powered by a common mains or generator, the system can operate both on military bases and in the field. The system generates nitrogen for combat vehicles such as the Stryker and AMV, the latest tactical trucks with advanced suspension such as the JLTV, artillery pieces including the M777 155mm howitzer, and aircraft and helicopters.
Often not paid due attention to loading fire extinguishing systems in the field. This includes, for example, tanks with extinguishing agents for automatic fire extinguishing systems for combat and tactical vehicles, aircraft and helicopters, as well as hand-held fire extinguishers. To obtain these capabilities in the field, the US Army has developed the Fire Suppression Refill System (FSRS). The entire system is housed in a robust container that can be mounted on an aircraft or ship and placed on a trailer for overland transportation. A spokesman for the US Army's Armored and Vehicle Administration noted that “a defective fire suppression system on the platform means the platform cannot be operated. FSRS ensures that frontline technicians can repair the system and get it back online without delay. The first FSRS systems will be deployed to the US Army in 2019.
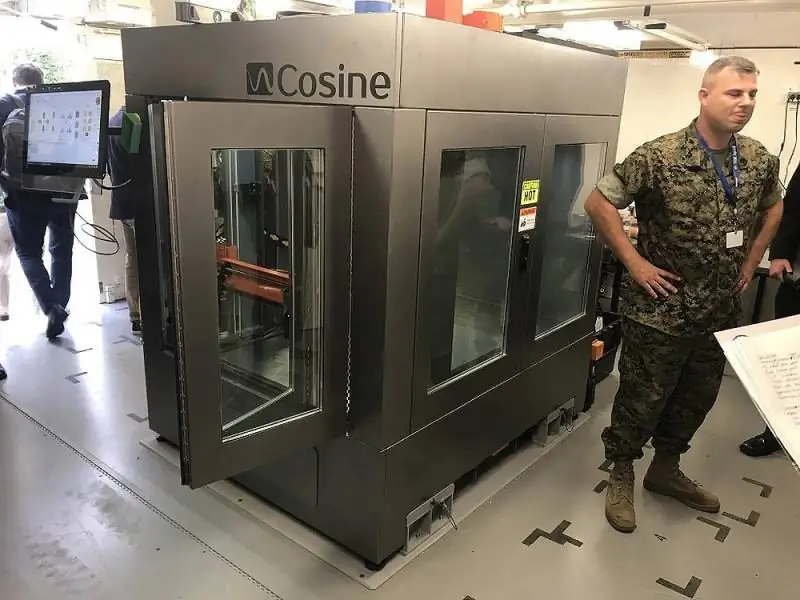
Maintenance and repair with augmented reality
The increased complexity of military systems has increased the complexity of their maintenance and repair. This, coupled with the need to carry out these actions at the lowest level and even more advanced to the forefront, where resources are more limited, creates great problems for the technical staff. The main question is how to give these specialists the competence to perform the basic tasks required to return an aircraft, vehicle, weapon system and other property to service. One of the proposed solutions is to use the capabilities of "virtual reality". Increasingly using simulation for teaching, Krauss-Maffei Wegmann has extended this technology to a dedicated technician. The head of the department of training and modeling describes this system as follows: “The semblance of a video game with elements of virtual reality, in which the owner of the helmet-display sees not only the 3D image of the machine (or other system), but is also guided step by step through the repair process. It can be purely virtual for a learning or familiarization process, or it can be overlaid on a real platform. In the second case, the repairer will go through every necessary step in the repair or maintenance process."
The use of augmented reality technology allows the specialist to take on any number of tasks with greater confidence, even if he has never done them before. It additionally guarantees the correctness of the process, which, as a result, eliminates errors that could jeopardize it. This is more effective than using printed or even video tutorials, as users are actually immersed in the process. The system also allows the supervisor to remotely monitor the specialist's actions in real time, point out errors and give advice. The use of augmented reality technologies in training allows the personnel of repair units located in the forefront or deployed in expeditionary operations to perform a wider range of maintenance and repair tasks without the need for mandatory training of personnel for this specific task. As a result, the likelihood of repairs increases, otherwise, if such technologies are unavailable, it should be postponed due to lack of experience at the repair site. This, in combination with the use of ISMS, on-board diagnostic tools and the concept of quick-change units, makes it possible to put equipment and weapons back into operation faster (due to, among other things, a lower organizational level).
The future is in maintenance and repair
The emergence of these technologies has the potential to revolutionize the process of maintenance and repair, as well as operation. The new and unique complementary capabilities these technologies offer will have a major impact on how and at what level these activities are carried out. Engaged in an integrated service, repair, operation and parts supply process, these technologies will enhance the independence and self-sufficiency of forward forces deployed in expeditionary operations. As a result, faster repair work and, accordingly, faster return of equipment or weapons to service. In addition, this will increase the number of forces and assets available to carry out operational tasks. This new approach to maintenance and repair is becoming a factor in increasing combat capabilities and combat power, which can positively affect the ratio of victories and defeats.