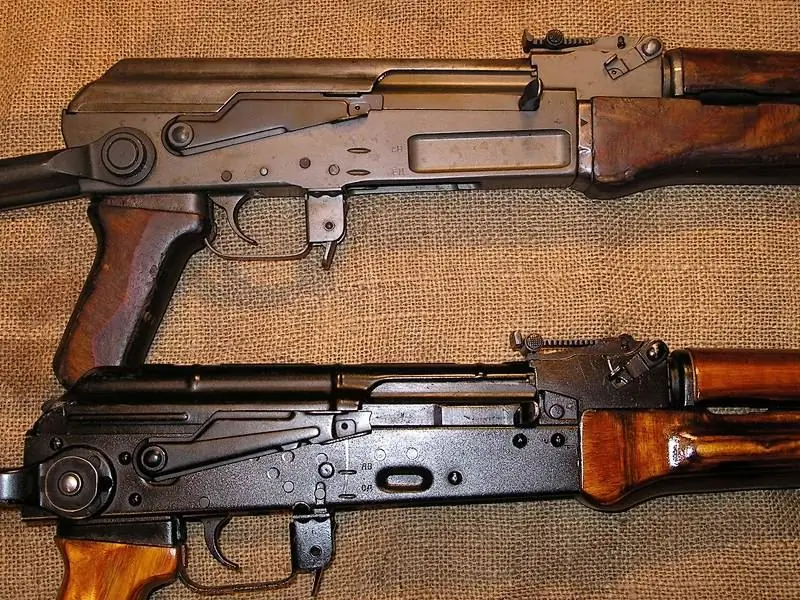
Stamp 3. Due to the innate (innate, inherent, etc.) technological backwardness of the Soviet industry, it was not possible to master the production of stamped receiver boxes, which is why they had to be made by milling from forgings, which led to a monstrous consumption of metal.
If we talk about the embarrassment that allegedly happened to Izhmash, who was unable to withstand the required quality of “stamping”, then the authors of these statements themselves find themselves in this state. The name of confident users, "experts", analysts and other connoisseurs is a legion, people who not only know machine-building production, but also directly on their own skin know the incredible severity of mastering a new production - a few (Note. The author of the article refers to such lucky ones). What actually happened with the replacement of a stamped box with a milled box in the AK-47? Pay attention - only boxes, this did not concern the rest of the details, but the conclusion is made on a global basis - on the entire Soviet "stamping" as a technology as a whole.
Let's look at the construction first. The receiver in the AK is not a milled bolt box with a stamped casing, as in the Sturmgewer. In the German assault rifle, different stamped parts are responsible for the direction of the bolt carrier, for the location of the magazine and mounts for optics, for the location of the trigger parts. When assembling them, it is easy to fit them with a mallet (this is such a wooden hammer), while losing the interchangeability of parts, as the Americans correctly noted. In the Kalashnikov assault rifle, all this is placed in one stamped box with a large number of additional riveted parts, including the barrel liner. Its complexity not at times, but an order of magnitude higher than the receiver of a Sturmgewer of two parts, of which only one is stamped and does not have any functions, except for the installation of sighting parts and the direction of the bolt carrier. In the AK receiver, a reliable basing and fixation of the magazine was achieved. In a stamped box and without using a shaft. This is great.
Here and below, quotes from the book by A. A. Malimona "Domestic Automata":
During the period of preparation for military trials, studies carried out at the test site found that when firing from a machine gun with an emphasis on the magazine, the accuracy of shooting is almost 2.5 times better than from the hand.
The AK (and SVD) encapsulation of all functional mechanics in one box and at the same time providing easy access to it during incomplete and complete disassembly without the use of tools is one of several excellent engineering solutions that together create a design masterpiece of the Kalashnikov assault rifle. Similar technical solutions, when all the functionality is assembled into one core and at the same time provides flexible expansion and development of the system due to well-thought-out interfaces, can be found in other areas, even in programming. Of course, debugging such a core of the system takes much more time (see Guderian's statement). But later, when a reliable optics bracket appeared on the stamped receiver, interchangeability appeared on the receiver cover, a side-folding butt, under-barrel grenade launchers appeared, a trigger retarder appeared inside, all this did not lead to a significant alteration of the technology or design of the machine (!) …
An experimental batch of Kalashnikov assault rifles was manufactured at the Izhevsk Motozavod and sent to field tests, which it could not stand. Among the comments were comments on the receiver. After the revision, the weapon went to military trials, and at the same time preparations for production began at Izhmash. According to the results of military tests, 228 design changes were made (almost two changes per one part) and 114 technological changes. The simultaneous change in the design of the product and the development of tooling for its production is no longer sugar in itself. But the task was even steeper, on the old squares, using part of the old equipment and by no means stamping machines from the Henel company (which did not exist in nature), an unprecedented production was created with production volumes of more than half a million machines per year - providing the holy of holies of mechanical engineering - interchangeability … And this production required new technologies, auto lines, which had yet to be created.
The plant had extensive experience in the development and mass production of large-caliber small arms and cannon armament, accumulated during the Great Patriotic War, but the plant had no practice in the production of medium-caliber automatic weapons. Factory designers and technologists, chemists and metallurgists had to acquire it in the course of mastering a new product.
In other words, it was necessary to create a technology that did not yet exist in the world, but for now it was necessary to use outdated machines and universal equipment, which also needed its own equipment, which also had to be designed and manufactured, and, most importantly, it was required to release machines.
At that time, there was no German, American, or any other alien “stamping” so that it was possible to immediately start producing a product that had not yet existed. It is quite natural that difficulties arose in the development of production. Mastering production is always a solution to a set of issues that can arise anywhere, both at the production stage and as a result of the combat use of products. The first thing you need to decide is whether the solution to the problem is in flaws or design features, or is it being treated by changing technological processes. The solution may not be obvious, or there may be several solutions.
In both cases, this requires additional research and experimentation, collecting and processing statistics - spending the most valuable resource - time. In total, in 1949 (the year the assault rifle was put into service), 700 changes were made to the drawings of the assault rifle and 20% of the production equipment was altered. Finally, there is another factor - the human one. And we are not talking about the innate at the genetic level syndrome "maybe it will go away" and not about the hands of the collector trembling with a hangover, although, most likely, this is how those who like to speculate about the "culture of production" imagine this. In wartime, and even now, at a defense enterprise, such shortcomings were treated elementarily. It takes time for a worker to start making quality products and not just making, but doing a lot and with high quality. In management science, these phenomena are described by curves of "learning" and "experience". And there is one more factor, it is little known because of its peculiarity. The peculiarity is that the worker develops a skill that cannot be formalized and described in the technical process. I will just give an example from the history of mastering the production of Maxim machine guns at the Izhevsk Motozavod. The machine-gun belt, made according to the drawings and the technical process obtained from Tula, could not pass military acceptance in any way. I got stuck. I had to fly by plane from Tula the girls who were collecting ribbons at TOZ. The reason turned out to be simple - when assembling, the girls slightly tightened the tape with their finger.
In production, there was a large screening out of the receiver in terms of dimensional characteristics and barrels for defects in chrome plating. The stamped-riveted receiver did not have the necessary rigidity, due to which, during its passage through the machining operations, a distortion of dimensions occurred. She also did not have the necessary strength in the riveted joints of the casing and the place of attachment of the butt.
During the manufacture of the box and the assembly of the machine, the need for a large number of edits of the casing was revealed, it was difficult to ensure the parallelism of the guides of the box with the axis of the barrel, the deformation of this part also occurred when the fuse-translator sector was riveted.
And this despite the fact that:
The volume of deliveries of products to the customer was strictly scheduled not only by quarters, but also by months, which created, taking into account the true state of affairs, a certain tension in the work of production. Failures and irregularities in work were most typical for the initial period of mastering the machine. They were repeated periodically in the future, which led to disruptions in the schedule for the supply of weapons, which caused serious concern on the part of the military department, since it posed a threat to the fulfillment of the plans of orders and the timely rearmament of the army with new weapons.
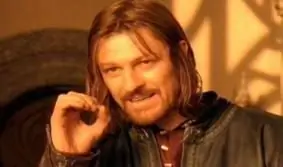
Here you can't just take and ensure the "parallelism of the box guides with the axis of the barrel", draw drawings of the punch and matrix, so that after they are made and put into production, the residual stresses in the metal do not begin to warp it at the fifth or sixth operation after stamping. Not so long ago I got acquainted with the foundry industry. Casting is unique, that is, almost all orders for large-sized parts differed in shape and size. The twenty-first century, heaps of monographs on non-ferrous casting have been written, a lot of tables and formulas, and I was asked to write an expert system in which the guys would enter the dimensions and configuration of cast parts, alloy compositions, modes of melting and pouring and the results of metal shrinkage by size and location, in order to gain experience and calculate the shrinkage angles in injection molds, taking into account past heats. The “scientific poke” method was and remains an unsurpassed way of knowing the world around us in order to transform it for the better. Its essence is in collecting, processing and analyzing statistics, which gradually leads to finding the right solution.
I hope after reading all this at least some idea of industrial production has appeared for those who did not have it.
The war has just ended, which required unprecedented physical and moral efforts to master new types of weapons and a manifold increase in production. And here's a new challenge. In conditions of wild time pressure, when it is necessary to release weapons, fulfilling the supply plan, when its design is constantly changing, when on some issues there is not only our own, but also world experience, the only correct decision is made - a temporary transition to a milled receiver case. This is an understandable step that does not in any way belittle the technical or professional qualifications of those designers and technologists who created the glory of the Soviet machine gun. But any mention of this fact in vain without paying tribute to the labor feat of these people, at least, is simply disrespectful to them.
Literature and sources:
Dieter Handrich, Sturmgewehr 44.
Dr. Dieter Kappell, Sturmgewer-Patrone 7, 92x33
Norbert Moczarski, Die Ära der Gebrüder Schmeisser in der Waffenfabrik Fa. C. G. Haenel Suhl 1921-1948
A. S. Yushchenko, Submachine guns designed by A. I. Sudaev
From the history of arms business. Digest of articles. Kalashnikov Museum
M. T. Kalashnikov, Notes of a gunsmith designer
A. A. Malimon, Domestic machine guns (notes of a weapons-maker)
D. F. Ustinov, In the name of victory
V. N. Novikov. On the eve and on the days of trials
B. L. Vannikov, Notes of the People's Commissar
And also books by Fedorov, Bolotin, Monetchikov, Nagaev, Chumak, etc.