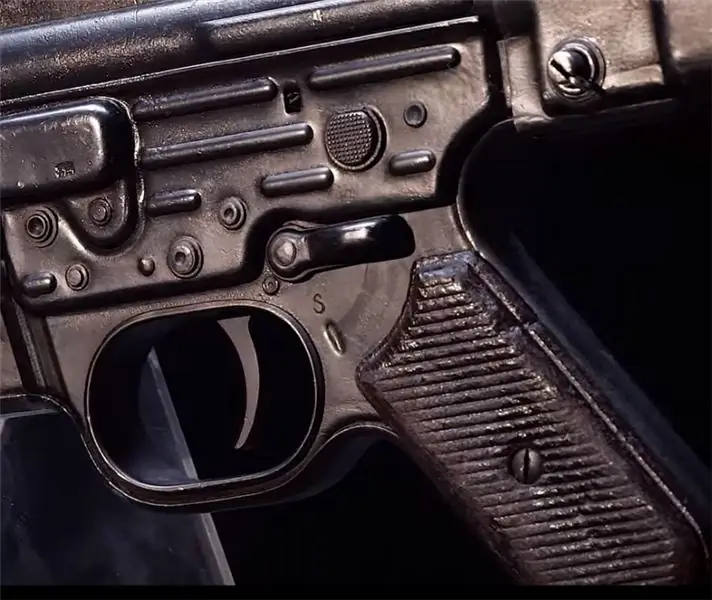
Actually, we will start with the stamps, but not with those that are the matrix-punch. Let's start with the mental clichés that can often be heard in the form of statements about one reason or another. Most often, they carry false information, since either they were created on the basis of speculation due to the lack of information or the author's ignorance, or they are used in isolation from the context of the topic of conversation or discussion. I will give the source of information that served as the basis for the article. We are talking about the introduction of mass production of AK-47 in Izhevsk.
By this time, the design of the AK had already "settled down", and all that the German specialist could theoretically help at this stage was setting up serial production with widespread use of stamping. But here, too, there was an embarrassment - the Izhevsk plant was not ready to withstand the required quality of stamping, heat treatment and riveting of the receivers, so in 1950 the designers of Izhmash had to create a new milled receiver for the AK. In this, they needed the help of the “ate dog” on punching Schmeisser like the dog's fifth leg.
However, the beginning of production of the winning model of M. T. Kalashnikov made it clear that it was quite difficult for the Soviet industry in 1949 to reach the level of Germany in 1942. Even despite the "import" from the capitulated Germany of a part of the machine park and a number of specialists (including the chief designer of the Henel company and the creator of the MKb42 (H) Hugo Schmeisser), it was not possible to launch the production of a "stamped" machine gun, the percentage of rejects turned out to be unacceptably high. As a result, the USSR had to make a compromise, starting in 1951 to manufacture AK with a milled receiver. It was finally possible to switch to stamping only with the adoption of the AKM in 1959.
So:
Stamp 1. Schmeisser was a stamping specialist.
Schmeisser was a designer. A constructor, though not so-so, but a constructor, and stamping is a technology. He could just as well be called a metallurgy or accounting specialist, or an effective manager, which, however, is also used in another cliche that Schmeisser was the organizer (of design work or production). The roots of these myths can be easily found. Schmeisser himself was never distinguished by his mastery of organization and management, rather the opposite, but he was an outstanding master of marketing and PR. There is no other way to explain the fact that the MP-40 submachine gun is still called "Schmeisser", and the designer himself is the father of almost all European rifle automatics.
If the simple design abilities of a gunsmith do not require special training and are most often an innate gift of people like Kalashnikov, Browning, Degtyarev, Shpagin and many others, then becoming a stamping specialist requires certain knowledge and skills to work with numbers and reference books that you can obtain only in specialized educational institutions. The stamping specialist was Doctor of Technical Sciences Werner Gruner, who, together with Schmeisser, worked in Izhevsk along with other German specialists in weapons and motorcycles. The merit of Gruner in the creation of the MG-42 - the best machine gun of the Second World War, is precisely in the production technology of this machine gun, and not in its design, for which Kurt Horn, the designer of the Grossfus company, was responsible. I remember very well how as a child I heard the legend that the famous Schmeisser worked for Izhmash, and his son studied at the Izhevsk school. But Gruner's two sons studied at school, and Schmeisser's son remained in Germany! Is it any wonder that the fame of a stamping specialist also stuck to his fake fame as an outstanding gunsmith? Or even a "stamping organization specialist."
Hugo Schmeisser himself has legally ruled the Haenel since 1943, and before that served as chief engineer. But in fact, together with his brother Hans, they ran this company since 1925, removing the incapable young heir and owner, Herbert Henele.
Finally, at Haenel there was no stamping at all. The stamped parts for the Sturmgewer were designed and manufactured at Merz-Werke from Frankfurt am Main. Subsequently, the production of "stamping" was scattered across several enterprises, from where it was sent to the final assembly of stormgears in "Haenel", "ERMA", "Sauer & Sohn" and "Steyr".
So Schmeisser did not eat any dogs, since he knew even less about stamping technology than about design. The fact that the other five German gunsmiths from among the German specialists who worked at Izhmash in 1952-1956 had nothing to do with the production of AK-47 and could not have, has already been written.
In general, technologists are undeservedly in the shadows. The overwhelming majority do not know what they are doing in production, and to be completely objective, their merit in ensuring the reliability and, in the end, the world fame of the weapon model, is sometimes more significant than even the design of the weapon itself. Fans of tank history probably know the name of Boris Evgenievich Paton - the creator of the automatic welding machine, thanks to which the welding of the hulls of T-34 tanks accelerated ten (!) Times. But which of the "experts" can name the authors of the technology for the production of weapons barrels by the method of radial compression or the production of turbine blades of aircraft engines by the method of directional crystallization? No matter how perfect the design of the sample, no matter what outstanding characteristics it possesses, until the technology of cheap mass production is created, it will remain in the form of a model or an experimental batch.
Stamp 2. Soviet stamping in 1949 could not reach the level of German stamping in 1942.
This refers to the well-known fact when, when mastering the AK-47, it was necessary to temporarily abandon stamped receiver boxes and switch to milled ones. Let's talk about this fact, as well as about the peculiarities of the stamped design of the Stg-44, but actually at the “level” of stamping it is worth stopping.
The Germans were indeed pioneers in the use of stamped parts in small arms. The MP-40 submachine gun and the MG-42 submachine gun, in terms of technological innovations, have left a noticeable mark on the evolution of weapons. But we had PPSh-41 and PPS-43, which also had stamped parts in their design. If we compare two samples of weapons of the same class, then they will be MP-40 and PPS-43. In all tactical and technical characteristics, our machine is superior to the German one. In terms of reliability, the Sudaev assault rifle is still unattainable by many foreign models. Now let's compare the production figures.
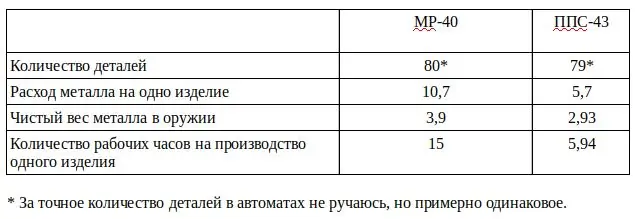
We take into account that in the production of German weapons, the labor of prisoners and forcibly deported to Germany citizens from the occupied countries was used, that is, the cost of a working standard hour in Germany was cheaper than in the USSR. And if we consider that the shortage of workers in the USSR was replaced not by prisoners of high-tech savvy German soldiers and not by citizens of "occupied" countries, but by women and adolescents?
We can tell by looking at these numbers that the "level" of manufacturability in the production of submachine guns, which includes, among other things, stamping operations and spot welding, in 1943 was in the USSR more than twice as high as in Germany?!
Reaching the level of manufacturability is a function of time. Remember what Guderian said regarding the copying and production of T-34 tanks:
The proposals of the front-line officers to produce exactly the same tanks as the T-34 … in the shortest time possible … did not meet with any support from the designers. The designers were confused, by the way, not with aversion to imitation, but the impossibility of producing with the REQUIRED FAST the most important parts of the T-34, especially the aluminum diesel engine.
Please note that this is not about the design and not about the lack of aluminum, but about the technology. The time for mastering mass production, which includes the design and manufacture of fixtures and technological equipment, calculation and selection of heat treatment and metal cutting modes, can significantly exceed the time and money spent on the development and testing of a prototype, and this can be a decisive factor in achieving political or military successes.