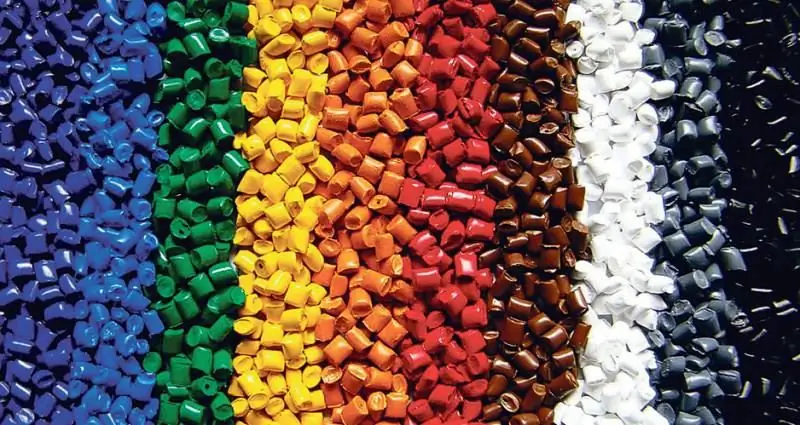
The production and use of domestic composite materials has recently been growing at an average annual rate of three to five percent. These are foreign assessments. Very complex technological processes for the manufacture of raw materials, semi-finished products and composites proper cannot be replaced overnight by purely Russian developments, as well as the very wide range of these products themselves.
For a long time, both the relevant technologies and finished products in this area were mainly imported - from China and a number of Asian countries (up to 60-65%), as well as from the West. Moreover, it is estimated that Soviet composite developments are used in at least 30 foreign countries, including NATO members, including France, Germany, Belgium, the United States, and Canada.
It hardly needs to be proved how important such materials are in the defense complex, in dual-use products and in many civilian industries. Therefore, in our country, as in the West, there is a requirement for maximum self-sufficiency in all components of the composite industry, especially in that part of it that is used in the defense industry.
Vladimir Putin set a strategic direction back in 2008, saying that Russia should not depend on foreign supplies to fulfill defense orders. This also applies to the composite sector, especially in connection with the increasingly stringent sanctions regime. Naturally, the embargo primarily covers products and technologies that can be used in the defense industry.
In July 2008, the government approved the Federal Target Program for the production of strategic composite materials (carbon fiber reinforced plastics) for weapons and military equipment, which provides for the refusal to purchase more than 300 types of components by 2020. In the next five years, a "road map" for carbon fiber was adopted, and the government approved a plan for the development of the production of composite materials. In 2012-2016, the Russian-Belarusian program “Development of innovative technologies and techniques for the production of competitive composite materials, matrices and reinforcing elements” was implemented.
According to estimates voiced at international forums held in 2017, more than 60 enterprises and at least 30 specialized research centers are now involved in the implementation of the adopted decisions. Import dependence in the segments related to the production and consumption of composites has decreased over the past 10 years by about 15 percent - to 30-35 percent. American and British sources estimate it at about 40 percent, noting a 10-12 percent decline over the same period. But in comparison with many Western countries, China, India, Israel, where composites and their derivatives are widely used in shipbuilding, oil and gas production and other material-intensive industries, the demand for carbon plastics in Russia is much lower. This is due to the long stagnation in this sector of the domestic economy and, as a consequence, the still low demand, for example, the consumption of composites in the shipbuilding complex of the Russian Federation does not yet exceed one percent of the global one.
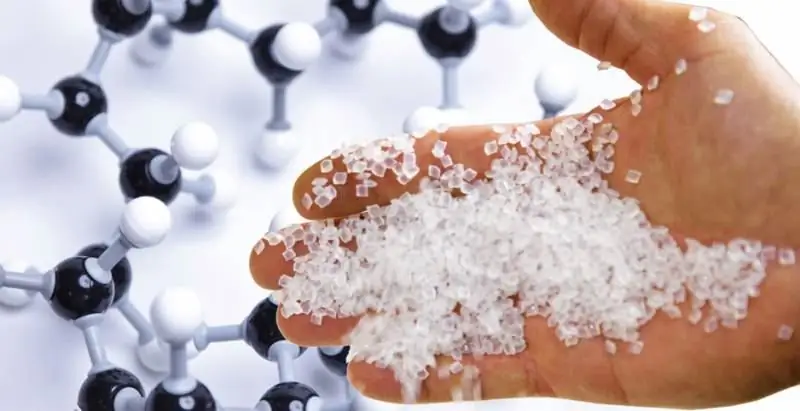
One way or another, the state has taken seriously the provision of the resource and strategic security of the composite industry (CI). On the whole, the trends are positive, although the oblivion of the problems of the country's industrial sectors, experienced in the 90s, still affects.
One of the main conclusions of the forum on composites held at the end of October 2017: among the main reasons hindering active import substitution are the low speed of changes in standards related to new materials, the underdevelopment of the domestic market and the lack of personnel who understand the problems of the industry.
The opinion of Kirill Komarov, Director of the Development and International Business Unit of the State Atomic Energy Corporation Rosatom, expressed at the same forum: the process of certification of a new composite material for equipment takes up to three years, twice as long as abroad. In addition, there is a need for "a more compact procedure for the development of standards, research and testing should not be carried out sequentially, but synchronously." And in order to apply new materials, it is not enough to allow their fixation and description in regulations - trained personnel are needed.
According to the aforementioned program documents, by 2020 the volume of production of composite materials and products from them should amount to 120 billion rubles. The development and adoption of at least 550 normative-technical, normative-legal and other documents necessary for the development of the industry are envisaged. At the end of October 2017, Deputy Minister of Industry and Trade Sergey Tsyb said that 363 new standards, 25 sets of rules, 4 classifiers, 16 estimated standards and 5 professional training programs had already been developed and approved for the composite sector.
Conspiracy threads?
Domestic production of carbon fiber (HC) shows the highest growth rates. According to Andrey Ignatiev, Sales Director of Umatex Group, the capacity of the domestic HC market is about 300 tons with the potential to multiply in the near future. In 2015, the country's largest plant "Alabuga-fiber" with an annual capacity of 1400 tons of hydrocarbons per year was commissioned. By 2030, this enterprise plans to enter the register of the largest hydrocarbon producers. Although the plant already produces five times more carbon fiber than is required by the Russian market, therefore a significant part of the production is exported. However, there are concerns that, due to the projected growth in domestic demand for hydrocarbons, export will run counter to domestic needs.
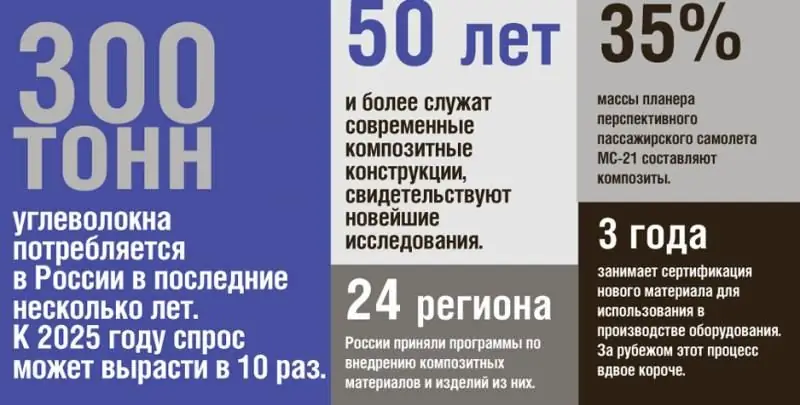
As for thermoplastic polymer compositions, Russia still has only a two percent share in the world market, the volume of demand in the country is no more than six million tons per year. Meanwhile, imports, according to Sergey Kiselev, an expert at Polyplastic, have made at least 25 percent over the past three years and may increase mainly due to the fact that foreign suppliers, especially East Asian ones, offer low- and medium-price assortments, while Russian counterparts are more expensive, although mostly of higher quality.
There are some nuances regarding resins for the production of composites. At the end of last year, the consumption of unsaturated polyester resins will be at least 45 thousand tons, with about 80 percent of Russian products. But in the segment of epoxy resins with a domestic market capacity of 40-42 thousand tons, the share of domestic producers does not exceed 10 percent. This niche is confidently occupied by foreign, mainly Chinese suppliers. Their products are again cheaper, often at the expense of quality. So the pace of import substitution in this sector is due not only to a physical increase in production volumes, but also to a decrease in production costs.
In the segment of chemical fibers (CVN), nonwovens and products based on them, the situation with import substitution remains difficult. As noted at last year's forum "Building a technological chain for the production of synthetic materials: from hydrocarbons to the final product", unsecured domestic demand for these products remains at least 60 percent, despite the growth of Russian production in this sector. Among the reasons for the shortage is the almost complete loss in the late 1980s and 1990s of small and medium-sized chemistry and its raw material base, as well as the close to 100% dependence of most sectors of the chemical industry on foreign equipment. The same dumping products from the PRC and developing countries prevail in commodity imports. Nevertheless, over the past three years, the production of nonwovens using CVI as a result of demand in the defense industry and other industries has increased by a third, which was provided primarily by the enterprises Kuibyshevazot, Kurskkhimvolokno, Gazpromkhimvolokno and Termopol.
But the largest project in this segment - a polyester complex in the Ivanovo region - has not yet been implemented, the construction start dates are regularly postponed. However, this is a private initiative that does not provide for government funding. Experts note that the non-state status of the project hinders its implementation, and this, in turn, negatively affects the domestic production of import-substituting chemical products, including composite ones.
At the mentioned forum, it was proposed to develop a comprehensive "roadmap" for the development of domestic production of CVI and related products. And soon, by order of the Ministry of Industry and Trade, an interdepartmental working group headed by Deputy Minister Sergei Tsyb was formed to develop an action plan for the development of the sub-industry of artificial and synthetic fibers and threads for the period until 2020. It consists of specialists from 20 specialized enterprises, including, for example, Gazpromkhimvolokno, Union of Composite Producers, Sibur, Kompozit, NIITEkhim, Balakovo Carbon Production, Khimprominzhiniring, Kazanorgsintez.
Or PAN, or disappeared
Prospective development is, first of all, the formation of an interregional sectoral industrial cluster "Composites without Borders". It has been created since 2016 on the initiative of the Umatex Group (part of Rosatom). At the conference "Import Substitution-2017", the general director of the company Alexander Tyunin, presenting the project, noted that the task was to increase the Russian market for carbon fiber and materials based on it. Now it is 0.5 percent of the global, and by 2025 it should quadruple. The cluster will create conditions for large, medium and small enterprises, as well as for young businessmen who are ready to organize advanced production facilities and develop new high-tech products based on composites. 23 enterprises from Tatarstan, Moscow and Saratov regions confirmed their interest in the project. The cluster is expected to be fully formed by the end of this year.
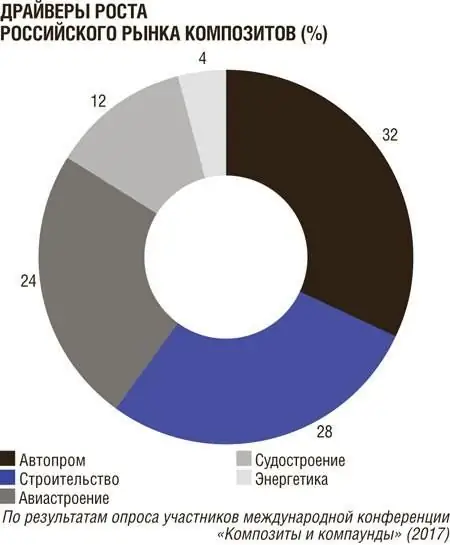
As for composite and related R&D and projects, it is necessary to highlight the technology developed by the Perm Research Technological University for the use of recycled carbon fiber from polymer composites. Associate professor Yulia Kulikova supervises these developments. According to her, research on the extraction of carbon fibers from the composition of polymer composite materials (PCM) by reagent methods has no analogues in Russia, they create the basis for the formation of a new industry for the production of structural and other products. The main goal of the project is to increase the life cycle of PCM products, including in the aviation and space industries, in mechanical engineering, through the reuse of resources. A minimum reduction in the mechanical strength of PCM from a secondary product in comparison with materials from primary fibers has been achieved. The introduction of this technology is planned at the waste disposal enterprises Uralplast and Bumatika. In Alabuga, with the help of the Industrial Development Fund, this year a furnace is being modernized for the production of high-quality fiberglass. The cost of the project is about 900 million rubles, of which 441.5 million will be provided by a concessional loan from the IDF. According to the Ministry of Industry and Trade of the Russian Federation, the demand for the project is due to the fact that fiberglass is among the most competitive reinforcing materials used in the basis of composite products. It is also the main product for the production of materials approved for use in the defense industry. By the way, the global consumption of fiberglass is 85 percent of the volume of all fibers used for reinforced composites, and only 13.5 percent is accounted for by other polymers.
In early 2017, a cooperation agreement was signed between the government of the Saratov region and JSC NPK Khimprominzhiniring on the implementation of a project for the production of carbon fiber at the Saratovorgsintez site. This enterprise produces the necessary raw material - acrylic acid nitrile, from which Khimpromnizhiniring will produce PAN-precursor - white fiber that forms the basis of composite materials. The project was discussed in the regional administration back in November 2016. Then it was announced that the investor would invest 3.5 billion rubles in production. The capacity of the plant in Saratov will be four thousand tons per year with a subsequent increase to 25 thousand. It is planned to implement this project within three years. The plant in Balakovo (Saratov region) plans to manufacture finished products based on the PAN precursor.