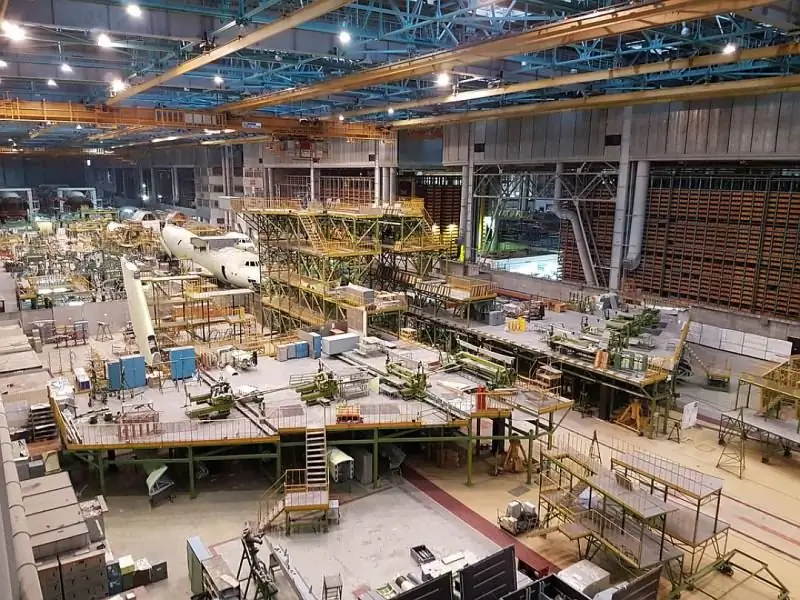
Previously, the IL-76 was made in Uzbekistan, at the Tashkent aircraft plant. But in the 25 years that have passed since the collapse of the Soviet Union, the company has managed to lose all its potential. In the end, the production was deprived of the opportunity to make new aircraft - neither the necessary equipment nor people remained.
Our military is in a difficult situation. IL-76 is the main heavy transport aircraft of the Russian army. And the defense industry simply cannot do without new machines. And the old ones need to be modernized and maintained somewhere.
Thank God, the authorities of the two countries were able to come to an agreement. The production of aircraft from Tashkent was transferred to Ulyanovsk, to the Aviastar-SP enterprise. The Uzbeks gave us all the documentation for the basic IL-76. Unfortunately, the blueprints for the modifications remained in the former Soviet republic.
Now the Il-76MD-90A is being designed using paperless technologies, in a 3D program. Russian engineers had to partially disassemble one of the new transport aircraft in order to make 3D models of all the advanced components. But now the domestic plant has everything you need to work.
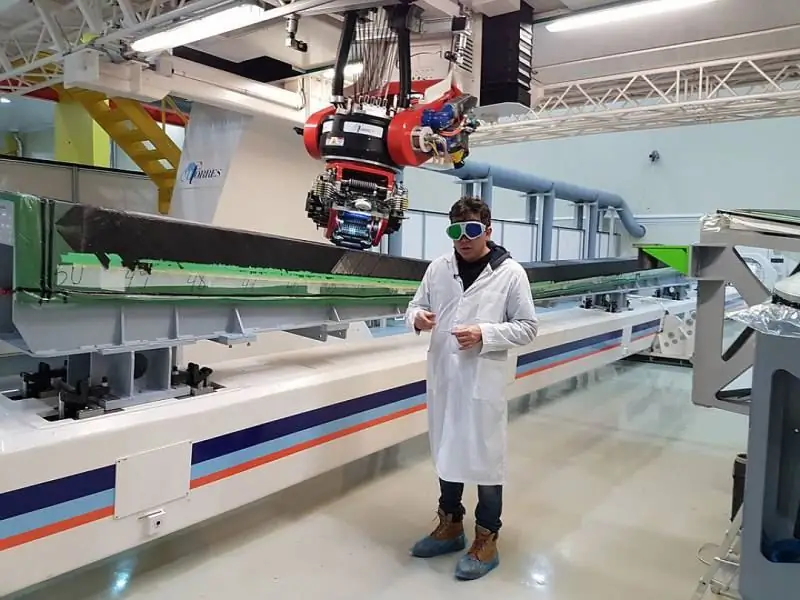
CONSTRUCTOR AIRCRAFT
The area of the Aviastar workshop can be compared to a small provincial town. The factory premises stretch for several kilometers. It seems to me that a beginner can easily get lost here - they will be looking for him for a few more days.
Another IL-76MD-90A is in a large assembly hall - the enterprise is now fulfilling a large order for the Ministry of Defense. A huge plane, which fits three trucks or a whole tank, seems like a baby compared to the surrounding building.
“We are now making a tanker aircraft,” Nikolai Dyachenko, deputy director for IL-76 production, told KP. - The machine has been modified so that, if necessary, additional tanks (for 20 tons of fuel each) can be easily removed. In just two to three hours, the tanker turns into a regular transport or landing aircraft designed to transport people.
The plane is now painted light green. This is a technological coating. Then the corps will be made the way the army needs.
IL-76MD-90A under construction is covered with workers. All of them are drilling, screwing, riveting something. It is incomprehensible to the mind how much effort is spent on the manufacture of one aircraft. According to the standard, one such flying tanker is made for a year and a half. But then the car will serve another 40 years - the first boards, built in 1971, are still in service.
Aviastar has a serious technical control department. That is, each screw or rivet is then checked for reliability and correct installation.
The crew of the new IL-76MD-90A consists of five people: a navigator, a flight engineer, two pilots, and a loader. Too much. Western planes are operated by only two people.
- Can't all processes be automated and transferred to a computer? - I ask Dyachenko. - Then people need to cook less.
- Still, military aircraft have their own specifics. They have to fly in combat conditions when ordinary things stop working (for example, navigation is jammed). Then the navigator needs to calculate everything himself. The flight engineer is able to fight for the survivability of the aircraft if the vehicle was attacked. Civilian pilots flying in peacetime do not have to do all this, so only two people can be entrusted with the controls.
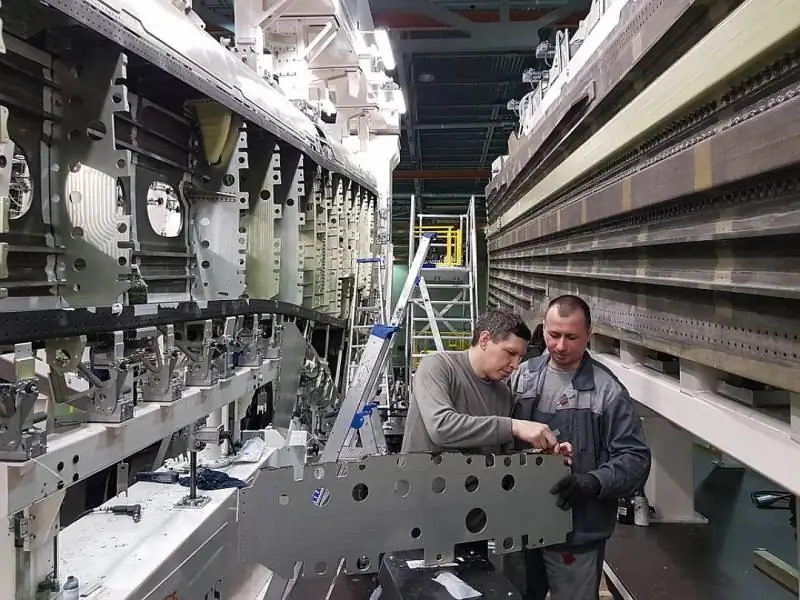
YOUNG EVERYWHERE WE HAVE A ROAD
Modernization, mastering a new aircraft for themselves, orders from the army breathed new life into the Ulyanovsk aircraft plant. For some time, young people reached out to the enterprise.
“Now we have 35% of workers under the age of 30,” Vadim Oveichuk, HR Director of Aviastar, told KP. - I had to go to different tricks to make the plant interesting for young people.
For the first three years, beginners are given a cash bonus in addition to their salaries. At the same time, every 12 months, the worker must confirm his qualifications - they will not just feed the loafers.
In addition, the company helps specialists from other cities and even countries who want to move to Ulyanovsk.
“In recent years, 300 people have moved to us from Tashkent,” said Oveichuk. - Everyone has a rich experience in the assembly of Il-76 aircraft. Everyone received lifting money from us. The plant, together with the regional authorities, paid the down payment for an apartment on a mortgage to the migrants. Now the workers have a place to live.
Now Aviastar employs 10, 5 thousand people. Not bad - especially when you consider that in the 90s and 2000s the company was practically out of work. Old employees have the opportunity to pass on their experience to the young before retirement.
WITHOUT DEPARTURE FROM PRODUCTION
Several years ago - just when the revival of the enterprise began - the Ulyanovsk aircraft plant faced the problem of training new personnel. It turned out that most of the graduates of local technical schools are simply not ready to work with modern equipment. Aviastar uses 3D printing, virtual modeling, and 5-axis computer-controlled machines. You cannot master all this in half a day.
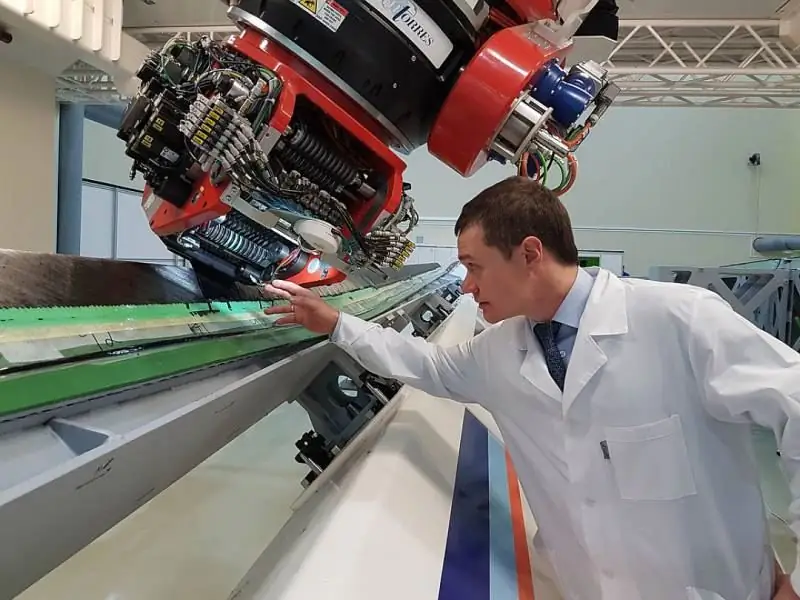
“We and the local aviation college had to deal with a real education reform,” said Oveichuk. “Now students spend half of their study time at our plant. They really learn to use modern machines. So we are confident that after graduation, workers will be able to get down to business immediately.
And that is not all. An Interregional Competence Center is being opened at the Ulyanovsk Aviation College under the state program. The project is being implemented jointly by the United Aircraft Corporation, the Ministry of Education, the government of the Ulyanovsk region and Aviastar. Here, from the beginning of 2017, they begin to train specialists of a new formation for high-tech industries.
- Take, for example, metalworking, - says Oveichuk. - Now several people are engaged in the production of one aluminum part. One thinks on what equipment and how to make a part. Another is setting up the machine. The third writes a program for the machine. The fourth one stands in the shop, presses the buttons and starts the same automatic manufacturing program. And it is necessary that all this be done by one person!
In addition, the college began to train specialists in composite materials. Previously, there was no such training program in Ulyanovsk at all.
The main thing is that the College-based International Competence Center will train specialists according to the international methodology and WorldSkills standards. (WorldSkills is an international movement founded more than 60 years ago with the aim of increasing the prestige of blue-collar occupations and developing professional education. The movement includes 76 countries, Russia joined it in 2012. On behalf of President Vladimir Putin, the WordSkills Russia Union was created ).
In fact, WorldSkills is a system that allows young workers to learn and adopt the best skills and practices from both their own and foreign colleagues. The main feature of WorldSkills is periodic competitions. Relatively speaking, for example, the best turners (they are chosen in the country at the qualifying industry and national championships) from 50 countries of the world come to one place and begin to perform the test task. The winner is the one who does everything better.
- The WorldSkills Championships give us an impetus, a message to change the existing outdated system of secondary vocational education, to transition to new forms of education. The championships are like a locomotive that can bring our vocational education system to the modern level. Participation in international championships makes it possible to determine how and in what direction it is necessary to change the system of training specialists in secondary vocational education. After all, international standards of specialties often set broader competencies for specialists, explains Oveichuk.
The first time a team from Russia went to the WorldSkills competition three years ago and took almost the last place there. It turned out that working specialties abroad have gone far ahead in comparison with our level. Take the same metalworking that Oveichuk spoke about. One Japanese technician can do the same as four of our narrow specialists.
It was then that the authorities began to think about reforming the system of secondary vocational education in technical schools and colleges. Now the Ministry of Education is creating the first seven Interregional Competence Centers in the country. There will be more of them further.
Moreover, the functions of these centers include not only training personnel in accordance with international standards and taking into account advanced technologies, but their mandatory preparation for national and international WorldSkills competitions. After all, after joining the WorldSkills movement, our country began annually holding industry and national championships, using them as the main tool for raising the professional level of young workers. And even on behalf of the government, they launched their own WordSkills Hi Tech championship, where specialists of high-tech specialties compete. The third such national championship was held in Yekaterinburg at the beginning of November this year. All of our major industrial corporations are partners or sponsors of this championship and present their national teams to the competition. The team of the United Aircraft Corporation at the current championship entered the top three winners, taking 5 gold, 2 silver and 4 bronze medals.
By the way, the WorldSkills 2019 international championship will be held in Russia, in Kazan. Our country won this right last year.
WALKING ON A VIRTUAL AIRPLANE
Almost all aircraft, marine and spacecraft manufacturers have now started using virtual design. The advantage of this technology is that you can put all the parts together on a computer and see how they will fit together.
“When earlier the nodes were individually drawn on paper, it was impossible to avoid some miscalculations,” said Anton Buyandukov, a virtual design specialist. - The worst part is if the details just don't fit together. Then I had to redraw everything. But there were also ergonomic errors. For example, a crane could have been placed so that it was simply impossible to get close to it.
With computer simulations, everything is easier. A person can see in advance if there will be any locked valves or other bottlenecks.
In the working laboratory of Aviastar, a projector displays a three-dimensional model of a promising Russian aircraft MC-21 on the wall. Specialists in 3D glasses watch for possible errors.
- I can separately consider every detail, - says Buyandukov. - The system even includes physical efforts that a worker will have to apply in order to maintain a particular node. The developers try to avoid any nuts that will become too exhausting for the maintenance staff.
WE FLY ON A COMPOSITE WING
Literally behind the fence of Aviastar there is a plant where they make composite wings for the future MS-21. AeroComposite - Ulyanovsk is one of the most equipped enterprises in the world.
Now all the world's leading aircraft manufacturers are starting to use composites instead of aluminum. A part made from interweaving carbon tapes weighs less than an aluminum one, and serves the same. In terms of reliability, CFRP is in no way inferior to traditional aircraft alloys.
The top Boeing-787 consists of more than half of composite parts. Airbus-350 has about a quarter of carbon fiber assemblies. In the promising Russian MS-21, one third of the aircraft will be made up of composites.
The peculiarity of Western models is that they use relatively small carbon fiber parts made using traditional technology. The same wing of the Boeing-787 consists of a significant number of composite panels - due to the fact that they are connected by metal, the weight gain is not so noticeable.
The MS-21 wing will be made of a single piece of carbon fiber, made according to a unique Russian technology. The aircraft will save 6-7% of fuel compared to classic aluminum counterparts due to better geometry.
RIBBON TO RIBBON
At first glance, composite parts are easy to manufacture. The machine puts carbon ribbons on the base around the clock - the layers, like shingles in old houses, lie at an angle to each other. The laser holds it all together.
The next step: the future wing or any other composite product is sent to a special chamber. There, under the influence of vacuum, the carbon tapes are impregnated with epoxy resin. The output is already a strong part.
At the very end, the edges of the workpiece are cut off with a special cutter. Then the composite panels are sent to the assembly, where a whole wing is made of them.
Difficulties, as usual, lie in the details. The wing is formed, and not in an autoclave, as is the case in most other enterprises. Due to the use of a large number of industrial robots, the share of manual labor has decreased several times. Robots monitor the safety of the units. There are no other such in the world. The same applies to the oven in which the epoxy resin is impregnated.
The thickness of the panels is different in different places. Where the load is stronger, the machine places more carbon tapes there. All this is calculated even at the design stage.
ONLY NUMBERS
Unfortunately, so far we are far behind the West in terms of the number of aircraft built. In 2015, only one Boeing assembled 762 aircraft, Airbus - 635. All Russian enterprises, taken together, produced 157 aircraft. Of these, there are only about 30 civilians (not fighters and transporters).
The overwhelming majority of domestic aircraft are made exclusively for the army. And in the international civil aviation market, we occupy a relatively small niche - in 2015 we made only 18 Sukhoi-Superjet-100s.