With the outbreak of World War II, the US industry, which perfectly mastered the technology of mass conveyor production, very quickly reoriented itself from consumer goods to weapons and military equipment. Tanks, guns, airplanes and even ships were assembled on conveyors. In the second half of the war, the Americans produced more weapons per day than the Allies lost in battle. The heavy bomber B-24 "Liberator" can be considered a typical example of mass-produced military equipment. We are most interested in the road transport component of this process, since it clearly demonstrates the state of logistics and road transport involved in the production of aircraft in the United States during the war years.
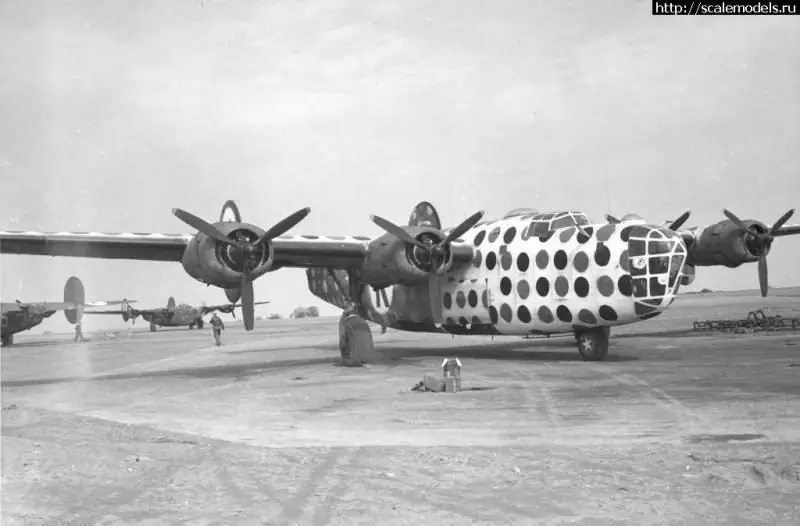
B-24 in the leader's livery.
The B-24 became the most massive four-engined combat aircraft of the war - 18 313 Liberators were produced in five and a half years, more than two times more than the more famous B-17 Flying Fortresses. The history of B-24 production is closely connected with the automobile concern "Ford". In 1940, two executives of the concern - Edzel Ford and Charles Sorensen - visited the Consolidated Vultee plant in San Diego. The purpose of this visit by motorists to aircraft manufacturers is to start serial production of the B-24 aircraft developed in San Diego at Ford's new plant in Willow Run, Michigan. E. Ford agreed to start producing aircraft, but with one condition - during production at Ford, the aircraft will not be modernized.
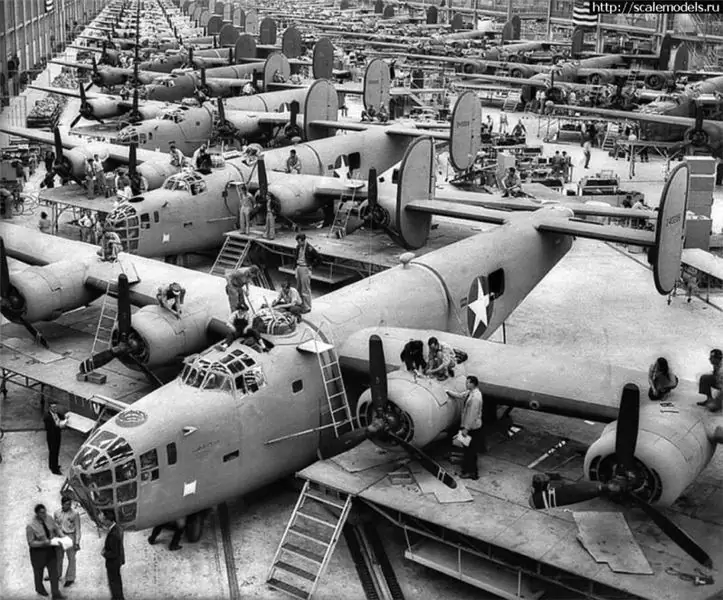
B-24 on the conveyor.
The customer, the Air Force, agreed with this unexpected demand, since the capacities of the three aircraft factories of Consolidated Vultee, North American Aviation and Douglas, which were supposed to produce the new bomber, were not enough to produce the required number of aircraft. E. Ford demanded not to change the design, not because of a whim, but because he intended to produce a bomber on a conveyor belt, like a car, and knew perfectly well that the slightest change in design immediately stops the conveyor.
In 1942, when the production of the B-24 at Willow Run was in full swing, one complete Liberator and two sets - the fuselage, tail, wings - for two more bombers were assembled on the assembly line every hour. But even in this huge factory, there was no room for two additional assembly lines. Could not find free space in the vicinity. Such areas and labor were available in the state of Oklahoma, in the city of Tulsa, as well as in Texas, in the city of Fort Worth. But from Willow Run to Tulsa it was 1,450 km. However, this did not frighten the Ford specialists. They knew the answer to the question - how to deliver large-sized elements of the bomber to the assembly site. Just load them onto road trains. The cost of transportation did not play a role - the state paid for everything. It was also known who would do it - back in the late twenties, "Ford" signed a long-term contract with entrepreneur Lloyd Lawson to deliver new "Fords" to sellers in all states. In the thirties, Robert Ellenstein joined him, and the E and L Transport company was born - at the outbreak of the war, Ford's most important partner in the field of transport services. It was she who received the order to organize the delivery of aircraft parts to the final assembly sites. The only condition was set for the transport workers - the delivery of elements to the factories should be carried out at the rate of aircraft assembly, i.e.every hour, so that the delivered parts are sent to assembly lines without intermediate storage "from wheels" …
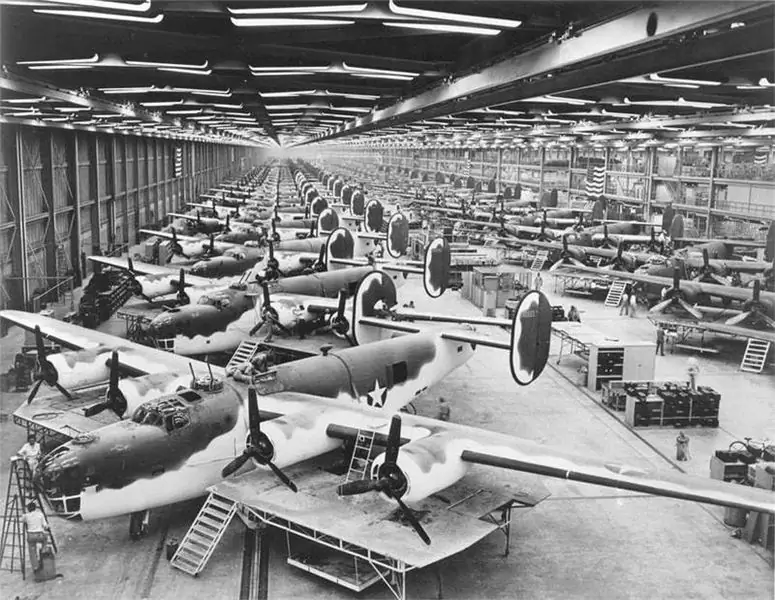
B-24 on a conveyor belt in camouflage.
But special semi-trailers were needed. They were designed and manufactured by Mechanical Handling Systems. The semi-trailer was 18.3 m long, 2.3 m wide and 3.0 m high. There was no roof, since the elements of the aircraft were loaded with a crane from above. After loading, the semitrailer was covered with a tarpaulin awning. To transport a set of elements of one bomber, two semi-trailers were required - in the first, parts of the fuselage and tail of the aircraft were loaded, in the second - the center section, wings, bomb compartment and engine hoods. Engines, chassis and internal equipment were manufactured by other firms, and they were also engaged in delivery to the assembly plant according to the same principles. However, there were problems with tractors for such large-sized road trains. The most important condition was great power and exceptional reliability, but even the highly developed US automotive industry at that time could not provide E and L Transport with such machines capable of delivering aircraft elements for assembly at a precise moment with a 100% guarantee. Therefore, they immediately abandoned all serial truck tractors as unreliable and insufficiently fast. L. Lawson, as an experienced transport worker, decided to order a tractor from a specialized company “Thorco”, which had considerable experience in converting serial “Ford” trucks into three-axle heavy vehicles. The design of the tractor chassis was almost traditional for three-axle vehicles - with a balanced suspension of the rear bogie on inverted semi-elliptical springs and a continuous beam of the front axle also on two semi-elliptical springs. Both drive axles were developed specifically for the future car. Well, the real "highlight" was the power unit, assembled on a stretcher pushed forward - two V8 engines of 100 hp were mounted side by side. from the passenger car "Mercury" along with their gearboxes. And they switched gears with a whole system of rods, which worked from one control lever; the clutch drive system was also redesigned accordingly. Each engine set in motion its "own" drive axle. Two engines were installed not so much to ensure high power as for reliability - so that in case of failure of one the road train would “reach” the workshop.
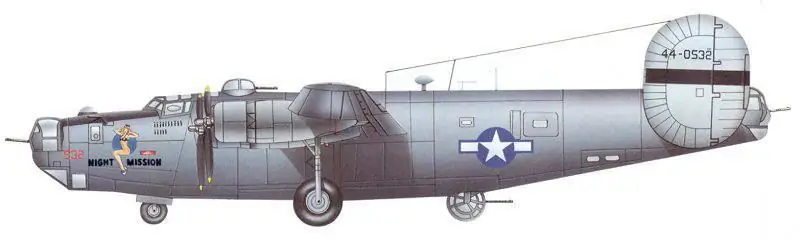
B-24 "Night mission"
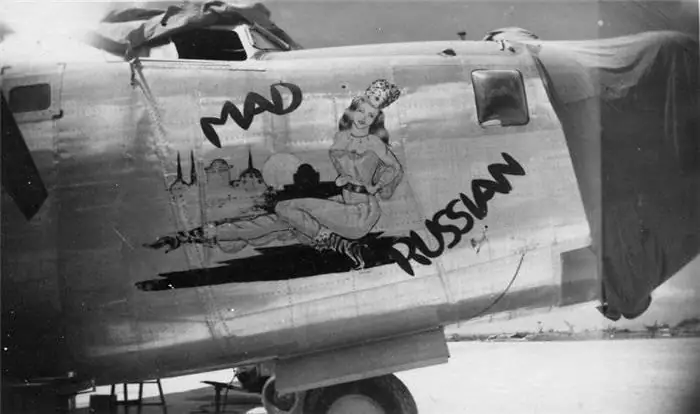
"Crazy Russian" - it happened that the B-24 was called this way …
It was necessary to move the motors out from under the cockpit because it was not folding. By the way, the cab, which was quite wide at that time, was composed of parts of the serial cabins of trucks and vans "Ford" in 1940, and it turned out to be more beautiful and comfortable than the cabins located above the engine that were produced at that time. The total length of the tractor with a semitrailer was 23.5 m.
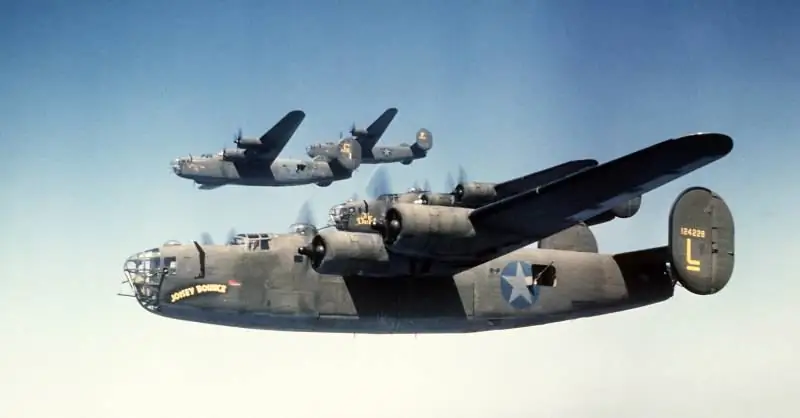
B-24 in the air.
The routes of the road trains to the assembly plants were chosen so that there were enough "Ford" workshops along the way. Their owners were ordered by martial law to work 24 hours a day, 7 days a week. Two road train drivers replaced each other every 5 hours. During the trip, there were four stops, one hour each, for inspection and food. At the factory, a semi-trailer with elements of a bomber was uncoupled, an empty one was immediately adjusted, and the drivers were sent back. And so every day for three and a half years … "Bombers" were not the only load of the described road trains. They serviced Ford's WACO transport glider plant in Iron Mountain. A little later, the experience of "Ford" was adopted by the aircraft manufacturer "North American Aviation" in organizing the mass production of the best American fighter of the Second World War - the P-51 "Mustang".
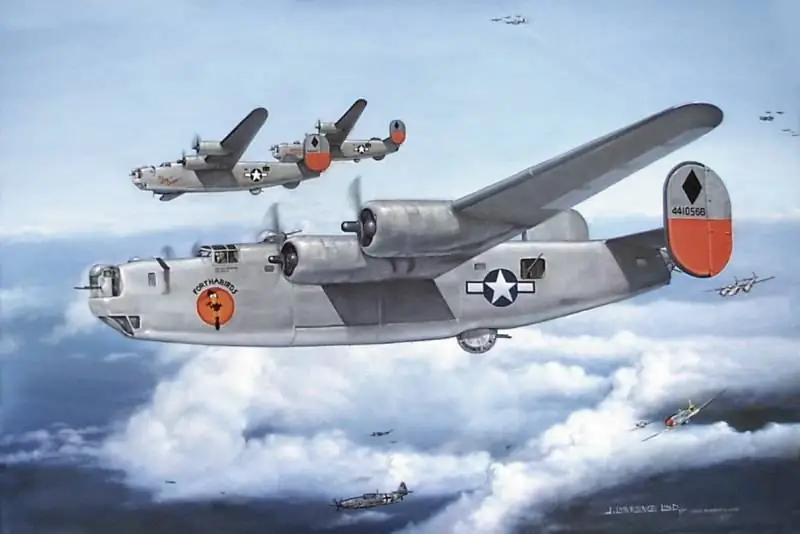
"Messerschmit" was shot down by us, and the car is flying, on parole and on one wing …"
After the end of the war, unique road trains carried elements of the new B-32 bombers for some time until they were replaced with more modern ones. They served in small private companies and gradually went to the landfill. In the nineties of the last century, one, probably the last of the remaining tractors, was found in a landfill and completely restored. Unfortunately, we have not yet found any of the several hundred semi-trailers, so you can only see the “airplane” road train in old photos …
What is the conclusion? The principle of “just in time” was invented not by the Japanese at all, but much earlier - in America during the Second World War. It was the organizational skills of the Yankees at that time, during the war years, that, thanks to cars, helped to unite the factories remote from each other into one giant assembly line, to make them work in the same rhythm, in the same technological chain.