Equipping Russian ships under construction with imported equipment has its own long history. This is confirmed by the ships built according to the programs of the military shipbuilding of the Russian Empire at the end of the 19th - beginning of the 20th centuries, the pre-war shipbuilding programs of the USSR (1935-1938), as well as the program for the development of the Russian Navy for 2011-2020.
The only exceptions were ships and vessels created according to the post-war shipbuilding programs of the USSR of 1945-1991, in which the priority in equipping was given to equipment, technical means and components, mainly of domestic production.
According to the authors, the high share of imported equipment in equipping Russian ships and vessels during the tsarist era and at the present time is the result of the technical and technological backwardness of the domestic industry, caused, among other things, by a misunderstanding of the role and place of the technical component in the economy of our state, and, consequently, underestimation of the importance of scientific, technical, engineering and labor personnel in Russian society.
Is it possible to avoid equipping ships and vessels of the Navy with imported equipment? According to the authors, this is possible when replacing diesel, diesel-gas turbine and gas-gas turbine power plants with other types of power plants, for example, air-water jets.
About imported "stuffing"
Almost all ships and vessels with imported equipment, as you know, have a number of features that affect not only their use in Russia, but also significantly increase operating costs in comparison with ships and vessels equipped with domestic equipment. These features include the following.
First, the objective need to resolve many additional issues related to the presence of ships and vessels with imported equipment in the Russian Navy. For example, training and retraining of all categories of personnel for the maintenance of imported equipment; carrying out factory repairs; supplying ships with components, spare parts, fuel and lubricants recommended by the manufacturing country, etc.
If these issues are resolved by the manufacturing country, then Russia will need to allocate large financial resources in foreign currency to pay for the services provided by the foreign party, at the same time, for repairs, modernization or replacement of imported equipment, the ships will be decommissioned for a longer time or repaired. in the manufacturing country abroad, thereby reducing the combat readiness of the Russian Navy. In this case, large financial costs in foreign currency will also be required, including the maintenance of the crew and the payment of travel expenses abroad.
When solving these issues, our country will also have to bear significant foreign exchange costs, for example, to pay for the services of foreign specialists and to purchase the required components, parts, tools, etc. from the manufacturing plant.
Secondly, the use of foreign equipment on ships and vessels that are part of the navy of other countries forces these countries to one way or another to compromise their national interests, since it forces them to follow the policy of the producing country, otherwise the ships and vessels can lose the opportunity to go to sea.
Thirdly, in case of deterioration or rupture of relations between former partners, as a rule, supplies of necessary components, spare parts, etc., as a rule, stop, and ships and vessels with imported "stuffing" become practically useless. History knows a lot of such examples. So, after the deterioration of relations between Indonesia and the USSR, the cruiser "Irian" (the former Soviet cruiser "Ordzhonikidze"), being part of the Indonesian naval forces, due to the cessation of supplies from the Soviet Union of naval fuel oil, fuel and lubricants, components, parts, spare parts and etc. for about 10 years he had no opportunity to go to sea, rusted at the wall of the naval base of Surabaya, performing the function of a floating prison, and was subsequently written off for scrap. A similar situation developed in the mid-1970s with ships of the Ethiopian Navy, produced in the USA, Great Britain and Italy.
Fourth, specialists are well aware that the technical characteristics of export products, including ships, vessels and elements of their power plants, differ somewhat (sometimes not for the better) from those of products intended for domestic use in the manufacturing country.
Fifth, the priority use of imported products, including the products of shipbuilding engineering, is one of the significant factors hindering the development of not only the national industry, but also domestic science and technology.
Finally, no country in the world will provide for export (even to its closest allies) the latest (newest) weapons and military equipment. This also applies to the elements of the power plant. As a rule, physically new, but obsolete samples, products and technologies are sold abroad.
Facts from history
In the history of the Russian navy, there were enough examples of equipping warships with mechanisms, devices and weapons of foreign production.
Since in those days steam power plants (PSU) received the greatest development, then during the implementation of the shipbuilding program of 1895, the ships of the Imperial Russian Navy were equipped with PSU of foreign production, including British triple expansion steam engines with steam boilers Yarrow (shipbuilding company "Yarrow Limited"), and also British steam engines of Yarrow triple expansion with licensed French Belleville steam boilers of Russian production.
Most of the ships (battleship Oslyabya, cruiser Almaz, cruiser Zhemchug, cruiser Aurora, battleship Prince Suvorov, battleship Eagle, battleship Sisoy the Great, etc.) built according to the shipbuilding program of 1895 of the year, participated in the Battle of Tsushima in May 1905.
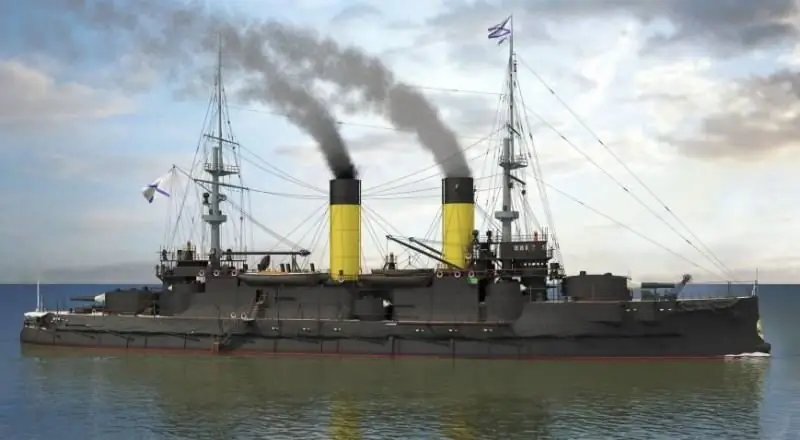
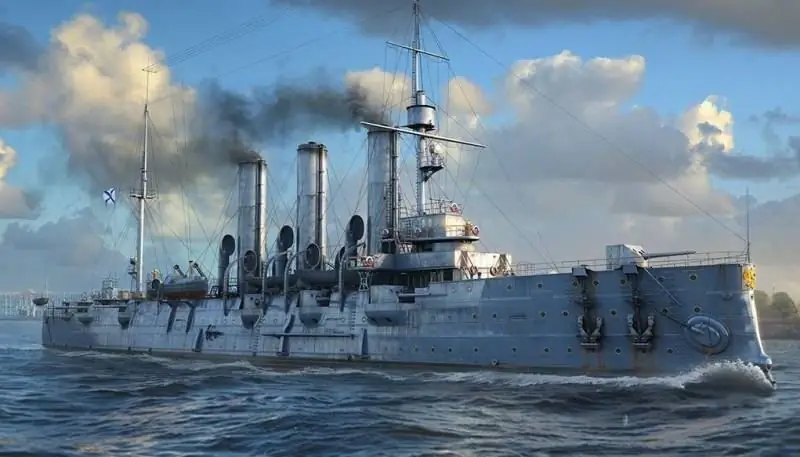
The general disadvantages of the main power plants (GEM) of domestic ships of the early 20th century, equipped with imported equipment, were operational problems of boilers (low parameters of steam generated, low productivity, overconsumption of coal, accumulation of soot in boilers, overheating of boilers, formation of hard-to-remove resinous deposits in the furnace, emission of flue gases from the furnace to the boiler room and others) and triple expansion steam engines (low efficiency, large mass-dimensional characteristics, low speed, high crankshaft speed, etc.), as well as the absence of domestic automatic control systems for boilers and steam engines … In addition, low steam parameters and low steam capacity of boilers required a large number of them on the ship - from 18 to 25 units. The existing shortcomings of the power plant of foreign production significantly reduced the tactical and technical indicators of domestic ships (speed, cruising range, maneuverability, reliability, survivability), against the background of which other objective and subjective reasons that led the Russian Imperial Navy to the Tsushima tragedy were aggravated. After Tsushima, the Russian fleet lost its status as an ocean one for almost half a century, and Russia lost its status as a great maritime power.
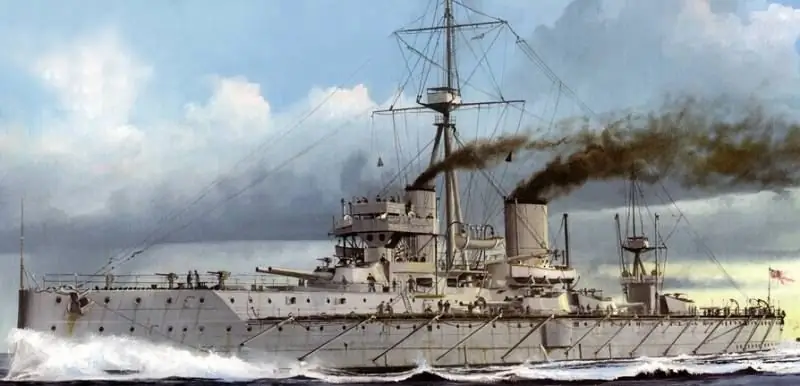
Delivering obsolete ship equipment abroad, since the beginning of the twentieth century, for example, Great Britain has already equipped its ships with boiler and turbine installations (KTU) with more efficient technical means. Thus, the power plant of the Dreadnought battleship, which became part of the British fleet in 1906, consisted of 4 Parson steam turbines and 18 Babcock and Wilcox steam boilers.
Lessons from the Battle of Tsushima
These lessons were taken into account, albeit in part, in the shipbuilding program of 1911-1914. Thus, the battleships of the Sevastopol type (4 units) and the Empress Maria type (2 units), introduced into the Russian Imperial Navy during this period, were equipped with more efficient and small-sized Parson steam turbines instead of ineffective and bulky triple expansion steam engines. However, even in this shipbuilding program, the development and equipping of Russian ships with domestic equipment and technical means was not provided for, which made the combat effectiveness of the fleet dependent on supplies from the manufacturing countries.
In the 30s of the twentieth century, the issue of equipping ships under construction in accordance with the shipbuilding programs (1935 and 1939) with power plants was also acutely faced by domestic shipbuilders, which was due to the technical and technological backwardness of our country. At that time, shipyards could quickly and well build hulls of ships of various classes, including cruisers, leaders of destroyers and destroyers, but the production of elements of the main power plant (ship steam boilers, ship steam turbines serving their mechanisms, etc.) was underdeveloped and lagged significantly behind the advanced shipbuilding states.
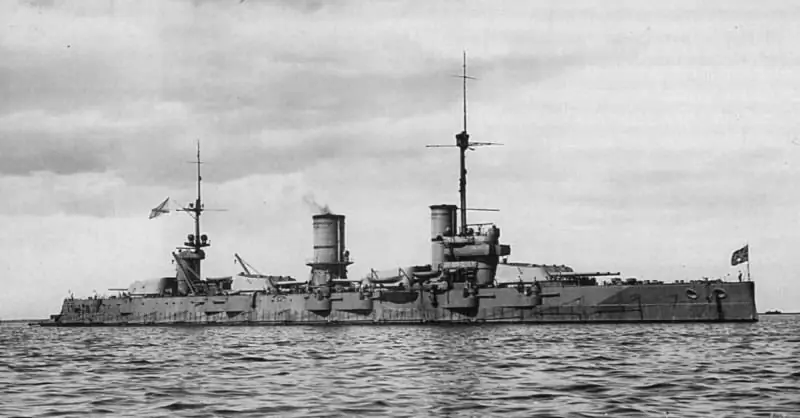
To speed up the process of building new ships for the USSR Navy, the country's leadership decided to equip part of the hulls of ships under construction with power plants produced abroad, in particular in Great Britain.1… This was how the first light cruiser of Project 26 (Kirov), the first of the three leaders of the destroyers of Project 1 (Moscow), and several Leningrad-built destroyers of Project 7U (Sentorozhevoy series) were equipped. All these ships were introduced into the combat composition of the USSR Navy before the war.
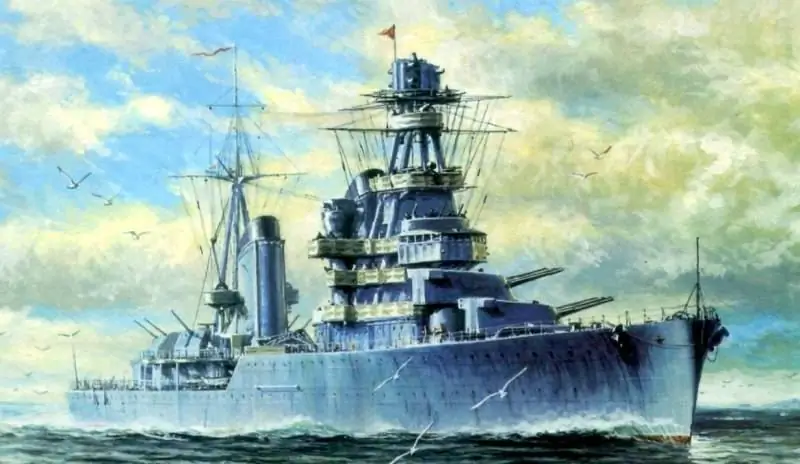
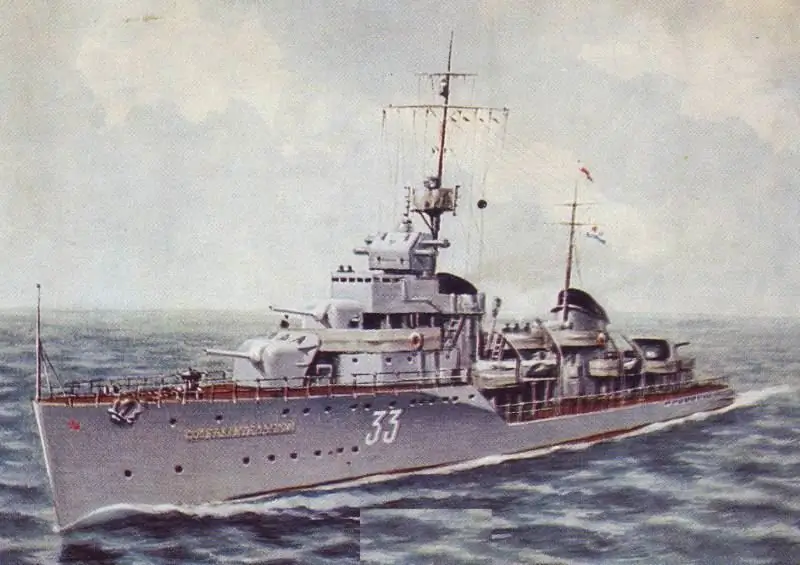
The Great Patriotic War of 1941-1945, as you know, was the hardest test not only for all our people, but also for military equipment, including the ships of the Russian Navy. Unfortunately, not all ships built in the 1930s passed the harsh wartime exams. Let's turn to historical facts.
On June 26, 1941, the leader of the destroyers "Moskva", having completed the combat mission of shelling the Romanian naval base and the port of Constanta, headed for Sevastopol. Upon returning to its base, the prevailing operational-tactical situation (enemy air raid) required the ship to develop the maximum possible move for a long time. Long-term operation of the power plant at a supernominal mode led to the destruction of the support devices (foundations) of the main steam turbines, which could not withstand the conditions of harsh operation. At first, the foundations cracked and then began to collapse. The reason for the destruction of the foundations was the material of their manufacture - cast iron - a brittle metal that is not able to withstand long-term ultimate dynamic stresses. The result of the accident caused by the use of cast-iron foundations was the loss of the leader of the destroyers of the course and the death of the ship from the effects of enemy weapons.
It should be added that in the peacetime pre-war time, the operation of the power plants of warships at the nominal and supernominal modes was carried out for a very short time only during the acceptance test run, and after the ships were accepted into the fleet, the long-term operation of the ship's power plant at maximum modes was completely prohibited by a special circular.
From the help report2 People's Commissar of the USSR Navy, Admiral N. G. Kuznetsov, the country's leaders followed that as of June 21, 1941, the Navy included 37 destroyers of the Watchtower series (project 7 and 7U), of which 10 were combat-ready, the rest of the ships could not go to sea, mainly due to the malfunction of the superheaters of the main steam boilers and the impossibility of replacing them.
The fact is that ship steam boilers made in Great Britain, installed on ships, were designed to use heavy fuel of English production, while the combustion of domestic naval fuel oil in boilers, especially at maximum fuel load, led to the burnout of superheaters, which resulted in a violation operability of boilers and power plant as a whole. In addition, the size of the boiler room for destroyers of this series did not allow for the repair of constantly failing tail elements of the boiler pipe system in ship conditions, and also excluded their dismantling by the crew for repair at the factory. In the first blockade Leningrad winter of 1941-1942, scientists carried out many thermal engineering calculations, which showed that imported steam turbines of destroyers of projects 7 and 7U are capable of operating on wet steam, that is, without overheating, and the absence of steam superheaters in steam boilers, although somewhat limited, but still does not lead to a significant deterioration in the tactical and technical characteristics of the power plant and the ship as a whole. The results of the work performed allowed the leadership of the Navy in wartime conditions to make an informed decision on the further operation of ships of these projects without superheaters. The superheaters of the ship's boilers were simply dismantled and until the end of the war, the destroyer's turbines operated on wet steam. However, precious time was lost and many ships in the first period of the Great Patriotic War, the most difficult for our country, performed combat missions, standing at the berths and factory walls, without going to sea.
Unfortunately, the examples considered show that the experience gained in the Great Patriotic War of using domestic warships with an imported electromechanical installation can hardly be considered successful, since individual ship power plants of foreign production for one reason or another have lost their performance under extreme operating conditions. It is obvious that the failure of the elements of the main power plant significantly reduced the combat effectiveness of both an individual ship and the navy as a whole. It becomes obvious that many ships built according to pre-war shipbuilding programs and equipped with imported equipment were more suitable for parades than for war, as evidenced by the historical facts set out above.
The lessons of the combat use of Soviet ships in the Great Patriotic War were not in vain and were taken into account in the post-war shipbuilding programs of the USSR, ships and auxiliary vessels of the Russian Navy began to be equipped with mechanisms and devices exclusively of domestic production, which made it possible not only to eliminate the causes of many emergencies, but also at the end of the 50s of the last century to withdraw the Soviet fleet to the world ocean, and to our country again to return the status of a great maritime power.
Soviet-made ship power engineering was at the level of foreign ones, and for a long time it occupied a leading position in the world in high-speed diesel engines and gas turbines. In general, the level of domestic shipbuilding corresponded to the world level, with the exception of the production of radio electronics and individual components for ships and ships, which was due to the lag in the production of the element base. In general, the level achieved by the shipbuilding of the USSR made it possible to have a navy that would meet the country's objectives and, in a sense, equal to the US Navy.
What about today?
At present, Russia, as you know, is implementing a large-scale shipbuilding program GPV 2011-2020, the purpose of which is to qualitatively and quantitatively update the domestic Navy, including through the introduction of surface ships into its combat composition - frigates, corvettes and small ships. as well as new generation auxiliary vessels.
Initially, according to the terms of reference, new warships and auxiliary vessels were to be equipped with main power plants (GEM) of foreign (mainly German and Ukrainian) production, however, after the introduction of sanctions, the European Union imposed an embargo on these products as dual-use products, and German the firm MTU Friedrichshafen (Baden-Baden, Germany), a manufacturer of marine diesel engines, despite the existence and partial payment of contracts, stopped supplying its products to Russia. At the same time, SE NPKG Zorya-Mashproekt (Nikolaev, Ukraine) unilaterally broke off military-technical cooperation with Russian shipyards.
The lack of marine engines and the impossibility of purchasing them abroad once again raised the question for domestic shipbuilders: "How can we replace imported marine main engines?"
The problem of the lack of engines led to a freeze in the construction of ships and auxiliary vessels of the Russian Navy and actually disrupted the planned timeframe for the implementation of the domestic shipbuilding program as a whole. The hulls of some new ships and vessels built, but not equipped with engines, were launched, where they are kept in storage until the issue with power plants is resolved. For example, three frigates pr. 11356 (Yantar plant, Kaliningrad).
To date, a way out of this situation has been found, but only partially.
Marine diesel installations of the German company MTU were replaced by domestic marine diesel engines: 10D49 (16ChN26 / 26) of the Kolomna plant - on frigates and M507D-1 of the Zvezda plant (St. Petersburg) - on missile boats.
Gas turbine engines M90FR for frigates have already been manufactured in Rybinsk at UEC-Saturn and are ready for shipment to the Severnaya Verf plant (St. Petersburg), but the fleet needs not just gas turbine engines (GTE), but main gas turbine gear units (GGTZA), including, in addition to the gas turbine engine, gearboxes, the manufacture of which is entrusted to the Zvezda plant (St. Petersburg). However, there is no information about the timing of the manufacture and delivery of gearboxes for M90FR gas turbine engines.
Thus, it has not yet been possible to organize a full-fledged import substitution in equipping ships and vessels with domestic power plants.
Authors' proposal
The collapse of the Soviet Union led to the loss of ship mechanical engineering in Russia (ship gas turbine engines, diesel engines, boilers and steam turbines) and today, in the new Russia, it is necessary to re-create this production, which will take a significant amount of time. To speed up the process of equipping ships and vessels under construction, it is first possible to develop and implement the simplest and cheapest ship power plants, for example, water-jet propulsion systems.
According to the authors, an air-water jet-cavitation apparatus, in which the outlet diffuser is replaced by a nozzle, can be used as a water cannon or a water jet propeller in the proposed power plant. High-pressure air is used as the active (working) medium of such a jet-cavitation propulsive device, and outboard water is used as the passive (sucked in) medium.
The backbone element of the specified power plant is a source of compressed air, for example, an air compressor designed to compress the required amount of air to the parameters required for the normal functioning of the jet-cavitation propulsion device. In addition, the power plant includes a high-pressure air pipeline, shut-off elements, control and measuring devices and other elements combined into a single system according to their functional purpose. The pressure line of the air compressor is connected by means of a high pressure air line with the working branch pipe of the jet apparatus. The jet propeller is mounted inside the ship's hull at the bottom of the transom (English Transon - flat cut of the stern) of the ship at an inclination, while the outlet and suction nozzles of the propeller are placed outside the hull and buried under the water level. The power plant can have one or several echelons, the number of which is determined by the ship's displacement.
The echelon of the power plant works as follows. High pressure air (HPA) from the air compressor through the HPV pipeline enters the nozzle of the air-water jet-cavitation apparatus, in the working chamber of which, when air flows from the nozzle, a vacuum is created sufficient for self-priming of water from behind the side. At the exit from the jet propulsion unit, an air-water jet is thrown directly into the water under pressure, thus creating an emphasis necessary for the movement of the vessel. In this case, the change in the speed of the vessel occurs due to an increase or decrease in the parameters (flow rate and pressure) of air after the compressor supplied to the nozzle of the jet-cavitation propeller.
The use of an air-water jet-cavitation apparatus as a water-jet propeller will eliminate many of the disadvantages of the propeller and the traditional water-jet propulsion device.
It is obvious that a power plant with air-water jet-cavitation propellers is more economical and has significantly lower weight and size characteristics than those used today. In addition, by implementing certain design measures, it is possible to significantly increase the survivability of the proposed power plant and the vessel as a whole.
The authors believe that the creation of a shipborne air-water jet power plant (UHVEU), the echelon of which includes, for example, one diesel compressor (domestic production), consisting of a high-pressure air compressor K30A-23 (with a power of 235 kW / 320 hp, air capacity 600 m³ / h and final air pressure of 200 ÷ 400 kg / cm²), driven by a diesel engine YaMZ 7514.10-01 (277 kW / 375 hp, specific fuel consumption - 208 g / kW * hour); high pressure air pipelines; high pressure air cylinders; instrumentation and one / two air-water (s) jet-cavitation (s) water jet (s) propeller (s) is currently quite realistic, for example, for small displacement ships, in particular for missile and artillery boats. Obviously, with an increase in the displacement of a ship or vessel, the number of echelons of UHVEU will increase.
For the implementation and use of the proposed power plant, the necessary calculations and full-scale tests should be carried out. At the same time, the final decision on equipping newly built ships and vessels with the considered power plant, including mechanisms, devices and systems of domestic production, remains with the leaders who have the authority to do so.
conclusions
HISTORY is an important SCIENCE, since it is a guideline for movement in the right direction not only for an individual, but also for society as a whole. Those who ignore and do not know history or do not learn its lessons subsequently pay dearly for it.
Carrying out the order of Admiral S. O. Makarov to the descendants of "REMEMBER THE WAR", Russian ships and auxiliary vessels of the Navy must be equipped with technical means and systems exclusively of domestic production, otherwise you can step on the same rake again.