Earlier, we examined how laser technologies are developing, what laser weapons can be created for use in the interests of the air forces, ground forces and air defense, and the navy.
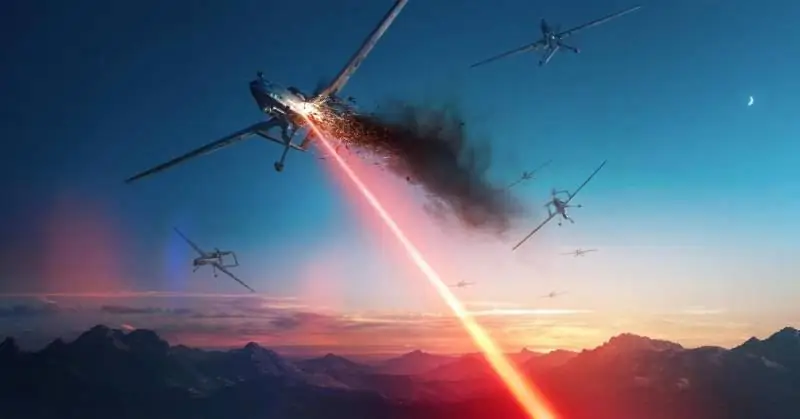
Now we need to understand whether it is possible to defend against it, and how. It is often said that it is enough to cover the rocket with a mirror coating or polish the projectile, but unfortunately, everything is not so simple.
A typical aluminum-coated mirror reflects about 95% of the incident radiation, and its efficiency is highly dependent on the wavelength.
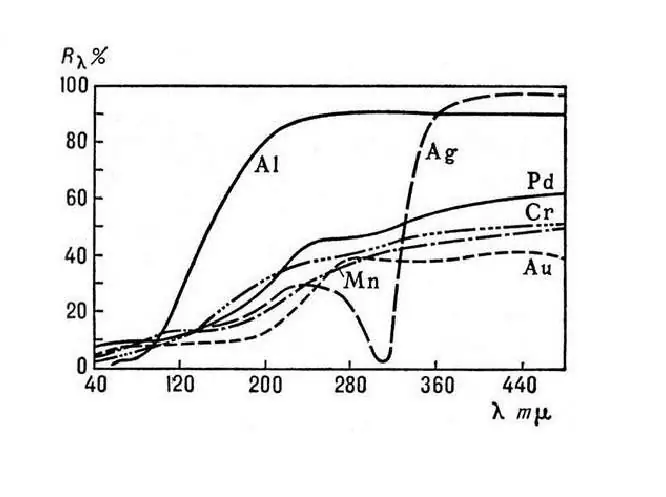
Of all the materials shown in the graph, aluminum has the highest reflectance, which is by no means a refractory material. If, when exposed to low-power radiation, the mirror heats up slightly, then when powerful radiation hits, the material of the mirror coating will quickly become unusable, which will lead to a deterioration in its reflective properties and further avalanche-like heating and destruction.
At a wavelength of less than 200 nm, the efficiency of the mirrors drops sharply; against ultraviolet or X-ray radiation (free electron laser) such protection will not work at all.
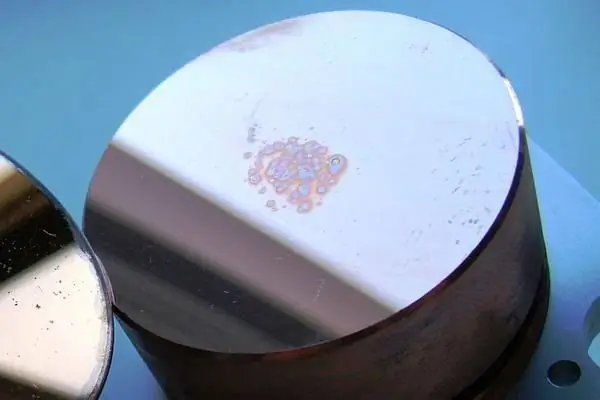
There are experimental artificial materials with 100% reflectivity, but they only work for a certain wavelength. Also, mirrors can be covered with special multi-layer coatings that increase their reflectivity up to 99.999%. But this method also works for only one wavelength, and incident at a certain angle.
Do not forget that the operating conditions of weapons are far from laboratory ones, i.e. the mirror rocket or projectile will need to be stored in a container filled with an inert gas. The slightest haze or smudge, such as from handprints, will immediately impair the reflectivity of the mirror.
Leaving the container will immediately expose the mirror surface to the environment - atmosphere and heat. If the mirror surface is not covered with a protective film, then this will immediately lead to a deterioration of its reflective properties, and if it is coated with a protective coating, it will itself deteriorate the reflective properties of the surface.
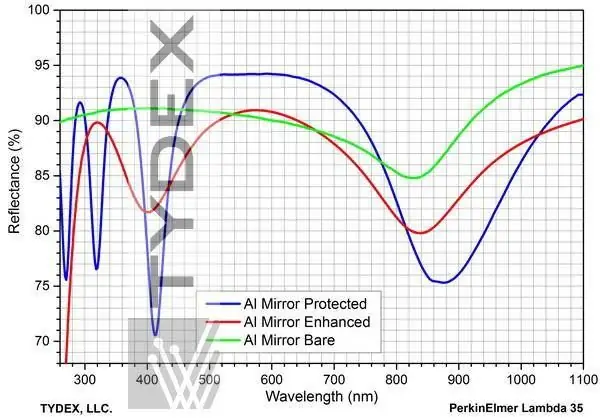
Summarizing the above, we note: mirror protection is not very well suited for protection against laser weapons. And what then fits?
To some extent, the method of "smearing" the thermal energy of the laser beam along the body by providing the rotational motion of the aircraft (AC) around its own longitudinal axis will help. But this method is only suitable for ammunition and to a limited extent for unmanned aerial vehicles (UAVs), to a lesser extent it will be effective when laser irradiated into the front of the hull.
On some types of protected objects, for example, on gliding bombs, cruise missiles (CR), or anti-tank guided missiles (ATGM) attacking a target when flying from above, this method also cannot be applied. Non-rotating, for the most part, are mortar mines. It is difficult to collect data on all non-rotating aircraft, but I am sure there are a lot of them.
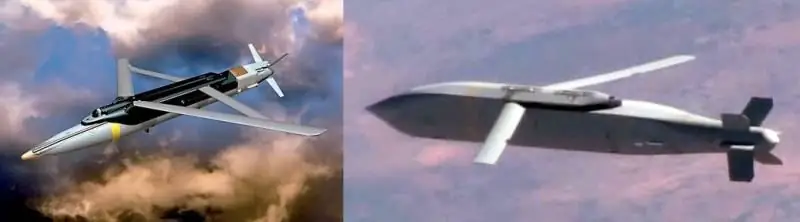
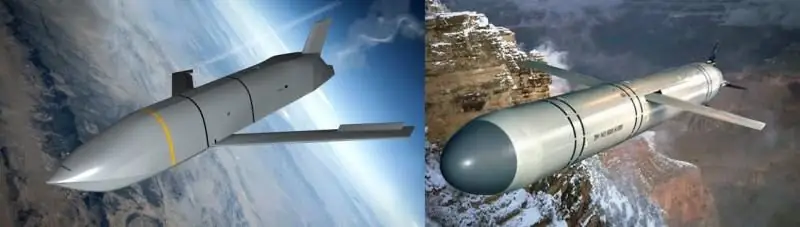
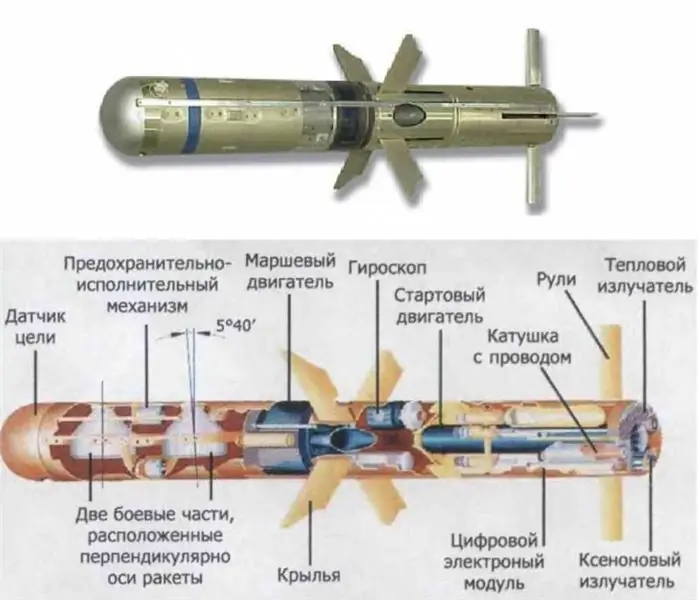
In any case, the rotation of the aircraft will only slightly reduce the effect of laser radiation on the target, becausethe heat transmitted by the powerful laser radiation to the body will be transferred to the internal structures and further to all the components of the aircraft.
The use of fumes and aerosols as countermeasures against laser weapons is also limited. As already mentioned in the articles of the series, the use of lasers against ground-based armored vehicles or ships is possible only when used against surveillance equipment, to the protection of which we will return later. It is unrealistic to burn the hull of an infantry fighting vehicle / tank or surface ship with a laser beam in the foreseeable future.
Of course, it is impossible to apply smoke or aerosol protection against aircraft. Due to the high speed of the aircraft, smoke or aerosol will always be blown back by the oncoming air pressure, in helicopters they will be blown away by the air flow from the propeller.
Thus, protection against laser weapons in the form of sprayed fumes and aerosols may be required only on lightly armored vehicles. On the other hand, tanks and other armored vehicles are often already equipped with standard systems for setting smoke screens to disrupt the capture of enemy weapons systems, and in this case, when developing appropriate fillers, they can also be used to counter laser weapons.
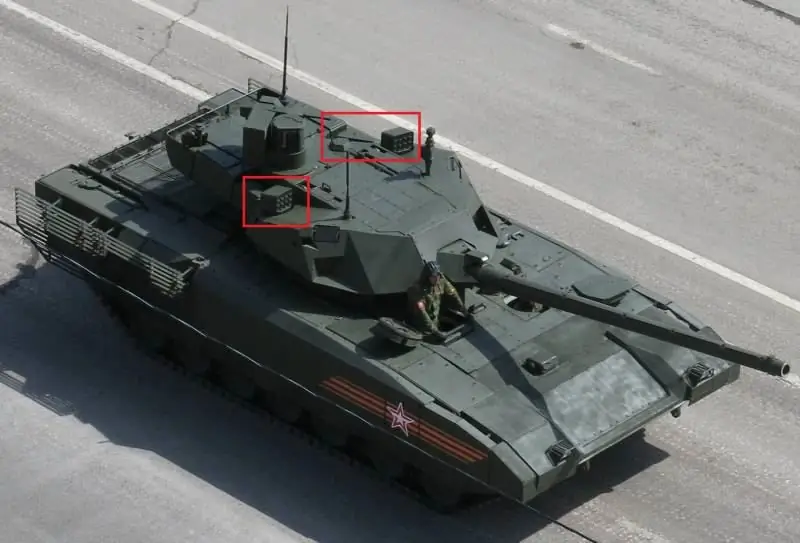
Returning to the protection of optical and thermal imaging reconnaissance means, it can be assumed that the installation of optical filters that prevent the passage of laser radiation of a certain wavelength will be suitable only at the initial stage for protection against low-power laser weapons, for the following reasons:
- in service will be a large range of lasers from different manufacturers operating at different wavelengths;
- a filter designed to absorb or reflect a certain wavelength, when exposed to powerful radiation, is likely to fail, which will either lead to laser radiation hitting the sensitive elements, or failure of the optics itself (clouding, image distortion);
- some lasers, in particular the free electron laser, can change the operating wavelength over a wide range.
Protection of optical and thermal imaging reconnaissance equipment can be carried out for ground equipment, ships and aviation equipment, by installing high-speed protective screens. If laser radiation is detected, the protective screen should cover the lenses in a fraction of a second, but even this does not guarantee the absence of damage to the sensitive elements. It is possible that the widespread use of laser weapons over time will require at least duplication of reconnaissance assets operating in the optical range.
If on large carriers the installation of protective screens and duplicating means of optical and thermal imaging reconnaissance is quite feasible, then on high-precision weapons, especially compact ones, this is much more difficult to do. Firstly, the weight and size requirements for protection are significantly tightened, and secondly, the impact of high-power laser radiation even with a closed shutter can cause overheating of the components of the optical system due to the dense layout, which will lead to partial or complete disruption of its operation.
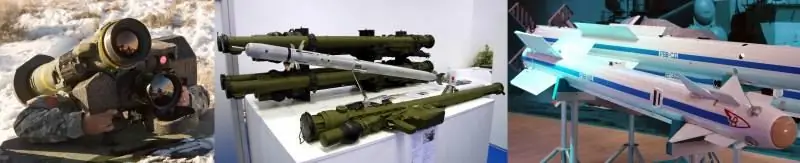
What methods can be used to effectively protect equipment and weapons from laser weapons? There are two main ways - ablative protection and constructive heat-insulating protection.
Ablation protection (from the Latin ablatio - taking away, carrying away the mass) is based on the removal of the substance from the surface of the protected object by a stream of hot gas and / or on the restructuring of the boundary layer, which together significantly reduces the heat transfer to the protected surface. In other words, the incoming energy is spent on heating, melting, and evaporation of the protective material.
At the moment, ablation protection is actively used in descent modules of spacecraft (SC) and in jet engine nozzles. The most widely used are charring plastics based on phenolic, organosilicon and other synthetic resins containing carbon (including graphite), silicon dioxide (silica, quartz), and nylon as fillers.
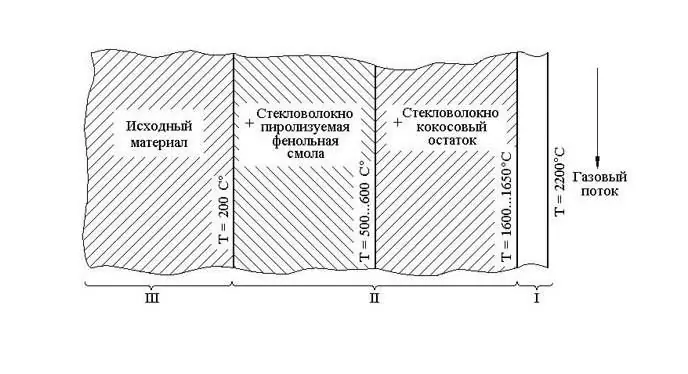
Ablative protection is disposable, heavy and voluminous, so it makes no sense to use it on reusable aircraft (read not all manned, and most unmanned aircraft). Its only application is on guided and unguided projectiles. And here the main question is how thick should be the protection for a laser with a power, for example, 100 kW, 300 kW, etc.
On the Apollo spacecraft, the thickness of the shielding ranges from 8 to 44 mm for temperatures from several hundred to several thousand degrees. Somewhere in this range, the required thickness of ablative protection from combat lasers will also lie. It is easy to imagine how it will affect the weight and size characteristics, and, consequently, the range, maneuverability, warhead mass and other parameters of the ammunition. Ablative thermal protection must also withstand overloads during launch and maneuvering, comply with the norms of the terms and conditions of ammunition storage.
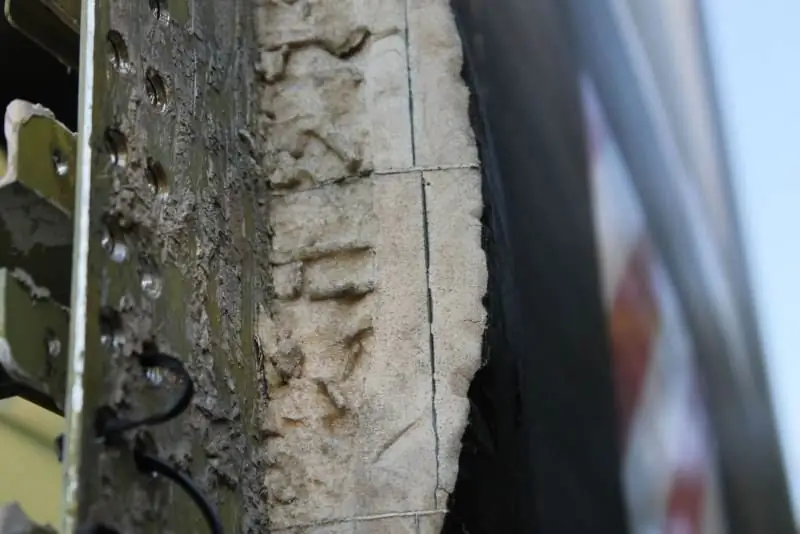
Unguided ammunition is questionable, since the uneven destruction of ablative protection from laser radiation can change the external ballistics, as a result of which the ammunition deviates from the target. If ablative protection is already used somewhere, for example, in hypersonic ammunition, then you will have to increase its thickness.
Another method of protection is a structural coating or execution of the case with several protective layers of refractory materials that are resistant to external influences.
If we draw an analogy with spacecraft, then we can consider the thermal protection of the reusable spacecraft "Buran". In areas where the surface temperature is 371 - 1260 degrees Celsius, a coating was applied consisting of amorphous quartz fiber 99.7% pure, to which a binder was added - colloidal silicon dioxide. The covering is made in the form of tiles of two standard sizes with a thickness of 5 to 64 mm.
Borosilicate glass containing a special pigment (white coating based on silicon oxide and shiny alumina) is applied to the outer surface of the tiles in order to obtain a low absorption coefficient of solar radiation and a high emissivity. Ablation protection was used on the nose cone and wing tips of the vehicle, where temperatures exceed 1260 degrees.
It should be borne in mind that with prolonged operation, the protection of tiles from moisture may be impaired, which will lead to the loss of thermal protection of its properties, therefore it cannot be directly used as anti-laser protection on reusable aircraft.
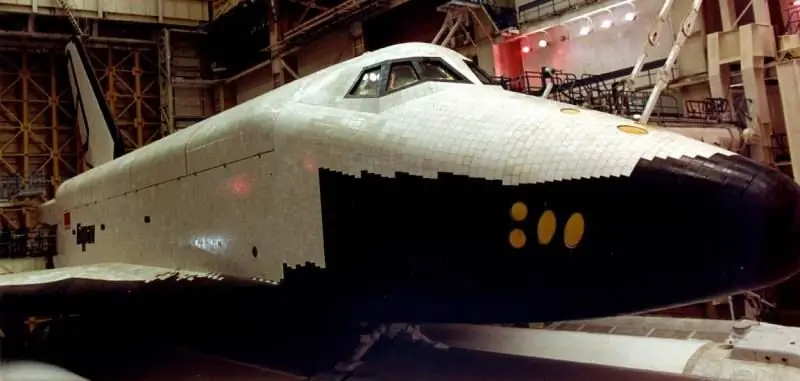
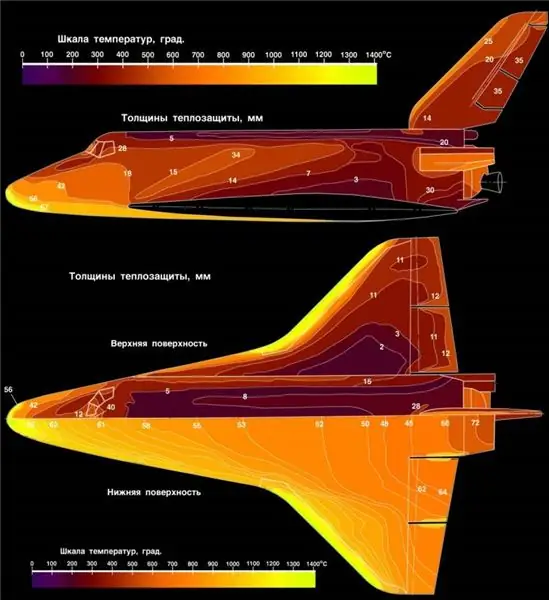
At the moment, a promising ablative thermal protection with minimal surface wear is being developed, which provides protection for aircraft from temperatures up to 3000 degrees.
A team of scientists from the Royce Institute at the University of Manchester (UK) and Central Southern University (China) have developed a new material with improved characteristics that can withstand temperatures up to 3000 ° C without structural changes. This is a ceramic coating Zr0.8Ti0.2C0.74B0.26, which is superimposed on a carbon-carbon composite matrix. In terms of its characteristics, the new coating significantly outperforms the best high-temperature ceramics.
The chemical structure of heat-resistant ceramics itself acts as a defense mechanism. At a temperature of 2000 ° C, the materials Zr0.8Ti0.2C0.74B0.26 and SiC oxidize and transform into Zr0.80T0.20O2, B2O3, and SiO2, respectively. Zr0.80Ti0.20O2 partially melts and forms a relatively dense layer, while low-melting oxides SiO2 and B2O3 evaporate. At a higher temperature of 2500 ° C, the Zr0.80Ti0.20O2 crystals are fused into larger formations. At a temperature of 3000 ° C, an almost absolutely dense outer layer is formed, mainly consisting of Zr0.80Ti0.20O2, zirconium titanate and SiO2.
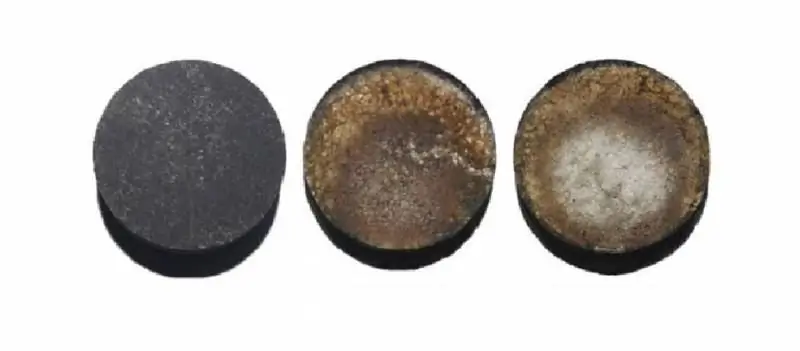
The world is also developing special coatings designed to protect against laser radiation.
Back in 2014, a spokesman for the People's Liberation Army of China stated that American lasers do not pose a particular danger to Chinese military equipment sheathed with a special protective layer. The only questions that remain are the lasers of what power this coating protects, and what thickness and mass it has.
Of greatest interest is a coating developed by American researchers from the National Institute of Standards and Technology and the University of Kansas - an aerosol composition based on a mixture of carbon nanotubes and special ceramics, capable of effectively absorbing laser light. The nanotubes of the new material uniformly absorb light and transfer heat to nearby areas, lowering the temperature at the point of contact with the laser beam. Ceramic high-temperature joints provide the protective coating with high mechanical strength and resistance to damage from high temperatures.
During testing, a thin layer of material was applied to the surface of copper and, after drying, focused on the surface of the material a beam of a long-wave infrared laser, a laser used to cut metal and other hard materials.
Analysis of the collected data showed that the coating successfully absorbed 97.5 percent of the laser beam energy and withstood an energy level of 15 kW per square centimeter of surface without destruction.
On this coating, the question arises: in tests, a protective coating was applied to a copper surface, which in itself is one of the most difficult materials for laser processing, due to its high thermal conductivity, it is unclear how such a protective coating will behave with other materials. Also, questions arise about its maximum temperature resistance, resistance to vibration and shock loads, the effects of atmospheric conditions and ultraviolet radiation (sun). The time during which the irradiation was carried out is not indicated.
Another interesting point: if the aircraft engines are also coated with a substance with high thermal conductivity, then the entire body will be evenly heated from them, which maximally unmasks the aircraft in the thermal spectrum.
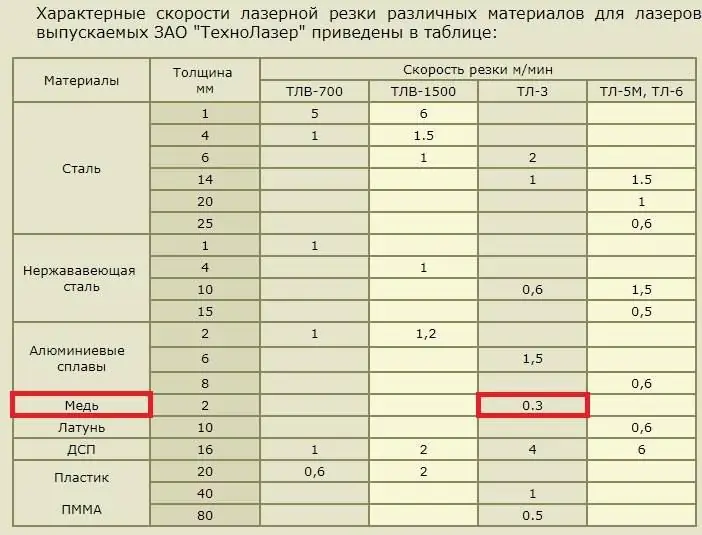
In any case, the characteristics of the above aerosol protection will be in direct proportion to the size of the protected object. The larger the protected object and the coverage area, the more energy can be scattered over the area and given in the form of heat radiation and cooling by the incident air flow. The smaller the protected object, the thicker the protection will have to be. the small area will not allow enough heat to be removed and the internal structural elements will be overheated.
The use of protection against laser radiation, no matter ablative or constructive heat-insulating, can reverse the trend towards a decrease in the size of guided munitions, significantly reduce the effectiveness of both guided and non-guided munitions.
All bearing surfaces and controls - wings, stabilizers, rudders - will have to be made of expensive and difficult to process refractory materials.
A separate issue arises on the protection of radar detection equipment. On the experimental spacecraft "BOR-5", the radio-transparent heat shield was tested - fiberglass with a silica filler, but I could not find its heat-shielding and mass-dimensional characteristics.
It is not yet clear whether a high-temperature plasma formation can arise as a result of irradiation with powerful laser radiation from the radome of radar reconnaissance equipment, albeit with protection from thermal radiation, which prevents the passage of radio waves, as a result of which the target can be lost.
To protect the case, a combination of several protective layers will probably be used - heat-resistant-low-heat-conductive from the inside and reflective-heat-resistant-high-heat-conductive outside. It is also possible that stealth materials will be applied on top of the protection against laser radiation, which will not be able to withstand laser radiation, and will have to recover from damage from laser weapons in the event that the aircraft itself survived.
It can be assumed that the improvement and widespread distribution of laser weapons will require the provision of anti-laser protection for all available ammunition, both guided and unguided, as well as manned and unmanned aerial vehicles.
The introduction of anti-laser protection will inevitably lead to an increase in the cost and weight and dimensions of guided and unguided munitions, as well as manned and unmanned aerial vehicles.
In conclusion, we can mention one of the methods being developed to actively counter a laser attack. California-based Adsys Controls is developing the Helios defense system, which is supposed to knock down enemy laser guidance.
When aiming the enemy's combat laser at the protected device, Helios determines its parameters: power, wavelength, pulse frequency, direction and distance to the source. Helios further prevents the enemy's laser beam from focusing on a target, presumably by aiming an oncoming low-energy laser beam, which confuses the enemy's targeting system. The detailed characteristics of the Helios system, the stage of its development and its practical performance are still unknown.