In January 2017, Dmitry Medvedev announced the development by the Cabinet of Ministers of a new program for the development of the military-industrial complex for 2018-2025. It should also include the technological modernization of the production capacities of defense enterprises. The purchase of foreign equipment is hampered by the international situation. At the same time, the Russian machine-tool industry, according to consumers of its products, is going through hard times. The history of the fall and revival of the industry, the opinions of critics and plans of machine tool integrators, the requirements of customers from the defense industry - in the review material Voennoe. RF.
Knocked from below: historical anti-record as a demonstration of decline
After the change of the economic model from the state plan to market conditions, the machine-tool industry found itself in a deep crisis. Due to the general economic shock, the demand for machine tools fell among the main consumers - machine-building enterprises. At the same time, employees at enterprises lost their qualifications, wore out and production capacities went under the hammer, and money ran out.
In the zero years, the agony of the Russian machine tool industry continued. Key manufacturers went bankrupt and ended unprofitable projects. One of the many examples is the Ordzhonikidze Moscow Plant, on the former territory of which a business center is now located.
The lowest point was the post-crisis 2009, when the number of manufactured machine tools reached a historic low. According to rough estimates, by this time about 40 machine-tool enterprises ceased to function - about a quarter of all Russian manufacturers. The surviving organizations were in a deplorable state.

Meanwhile, in the world machine tool industry, equipment became more complex and intelligent, new generation machines were developed and introduced abroad. The scientific and technical lag caused by the paralysis of the Russian machine tool industry formed dependence on foreign manufacturers.
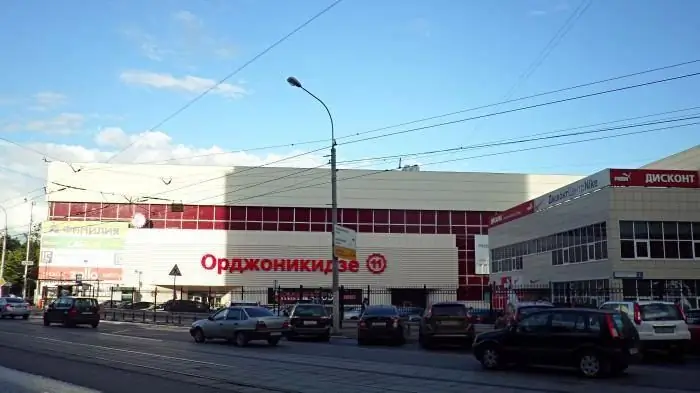
The government took notice of the industry's decline in 2007. Then Denis Manturov, at that time the Deputy Minister of the Ministry of Industry and Energy (the predecessor of the Ministry of Industry and Trade - ed.), First announced the idea of creating a machine-tool holding in Russia. It was assumed that a corporation called Rosstankoprom would unite state assets in industry enterprises to create an assembly point, after which private producers would voluntarily join it.
At the same time, the working group of the Ministry of Industry and Energy announced its intention to create a State Engineering Center on the basis of the Stankin profile university, whose tasks will include conducting R&D to overcome the technological backlog along with information and analytical assistance to private traders interested in upgrading production capacities and other intellectual processes.
The engineering center at Stankin was opened soon, in 2008. The first state structure, RT Mashinostroenie, created on the basis of conceptual developments by Manturov's working group, appeared a little later - in 2009. On its foundation in 2013, Rostec created Stankoprom, a system integrator of the Russian machine tool industry.
As before it won't work
Before explaining the actions of the government and explaining what is the point of forming a system integrator, consider the state of the industry at that time.
Its weak point was the low profitability of the production of new machine tools by Russian enterprises in the changed economic and organizational conditions: in 2007, the Expert magazine wrote that about 80% of the enterprises' income came from the repair and modernization of old equipment.
The fact is that in the days of the planned economy, machine-tool factories existed in a closed production cycle - most of the components for equipment were manufactured in-house. Due to the technological leap of the 1990s, this organizational model has become prohibitively expensive.
The leaders of the world machine tool industry have reformatted the industry in such a way that local centers of competence have taken up the production of high-tech components. So, electrospindles are produced by one company, turrets - by another, ball screws - by a third, CNC systems are being developed by a fourth. Ultimately, at the last stage, the company only assembles the machine from finished parts.
In Russia, it turned out that there was no one to cooperate, and there was nothing to assemble machines. The modern component base was practically not produced. In turn, the "old-fashioned" machines were less and less interested in potential buyers.
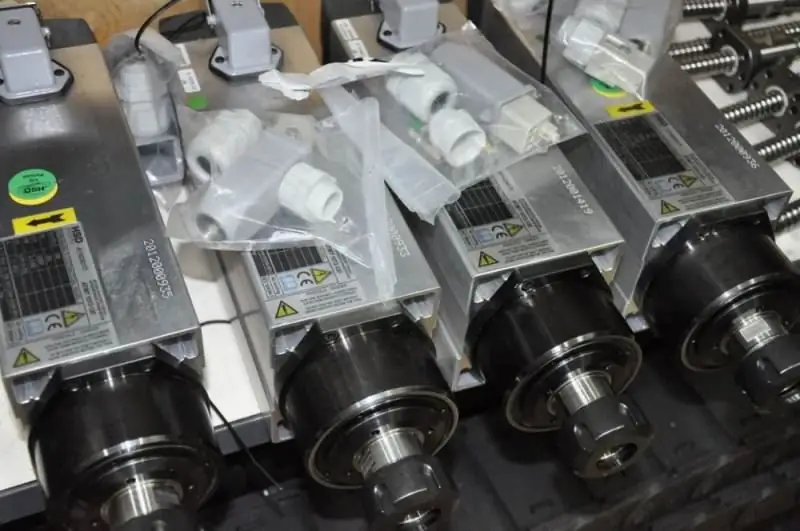
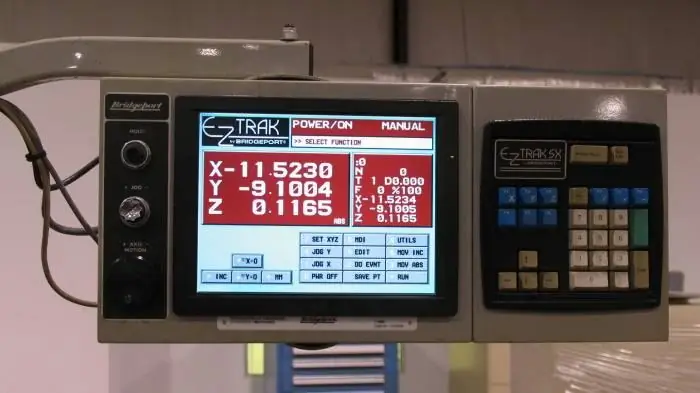
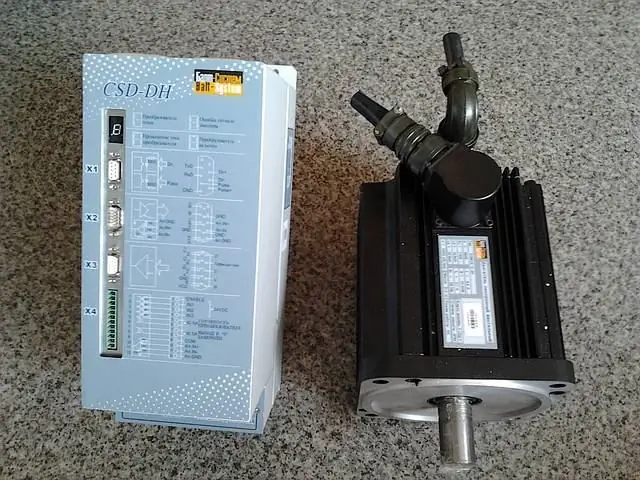
A side effect of the industry crisis is that Russian products have a bad reputation: when choosing between imported and local equipment, consumers are likely to prefer the former. In the parlance of economists, this is called “unfavorable demand forecast”.
The work of managers, employees of sales departments and marketing specialists of machine-tool factories also caused and still causes questions. It should be noted, however, that they had a hard time in the face of competitive pressure from manufacturers of high-tech equipment on the one hand and Chinese dumping on the other.
Add to this the problem with the inflow of fresh personnel, which has set all Russian industrialists on edge, as well as the high lending rate for enterprises at the level of 17% - and we will get an idea of what machine-tool industry was like in the second half of the 2000s.
Private Russian companies did not want to invest in saving the industry, and for foreigners there was no reason for this at that time, even more so. Levers of influence on the situation remained only with the state.
State machine mechanisms launch
The government took action at the turn of the decade. In addition to the creation of an engineering center and the first attempts to design a state corporation, the Ministry of Industry and Trade in 2011 developed a conceptual program for reanimating the industry. It was named "Development of the domestic machine tool and tool industry for 2011-2016". Funding for the five-year program amounted to 26 billion rubles.
The objectives of the program were the creation of conditions for the serial production of competitive equipment, the organization of production sites for their release, as well as the creation of system integrators.
Notorious integrators are needed to build a cooperative chain between the community of component manufacturers, as well as to study the needs of customers in a particular machine tool range. Delivering finished products to customers is the task of the integrator.
The state corporation "Rostec" undertook to supervise an integrator called "Stankoprom", which Gleb Nikitin, deputy head of the Ministry of Industry and Trade, later called "an agent from the state" in an interview with Kommersant.
In 2017, the structure of "Stankoprom" includes research centers, engineering structures and a company for the production of production facilities. In addition, the integrator owns production areas and equipment, which the holding rents out to machine tool builders, in particular, the Savelovsky Machine Building Plant. In February, the press service of the government of the Tver region reported that the plant received a package of orders from military industrialists in the amount of 900 million rubles.
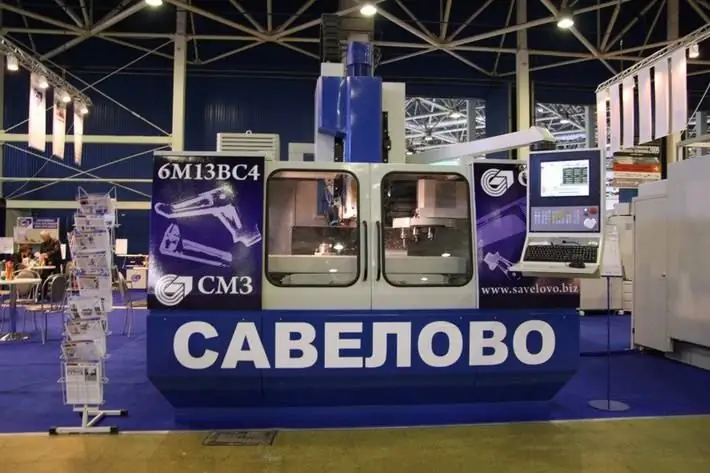
Protectionist measures became another area of work of the state. We are talking about a government decree adopted back in February 2011 banning purchases of foreign equipment by enterprises of the military-industrial complex at the expense of the state in the presence of Russian counterparts. According to the Ministry of Industry and Trade, the volume of imports on the Russian machine tool market in those years reached 90%. In the same 2011, a program to modernize the defense industry was launched, and it was expected that the growth of orders would increase due to the renewal of equipment at enterprises.
Be that as it may, protectionism and the creation of state players are meaningless if the scientific and technological lag behind the advanced countries continues to increase. To remedy the situation, the state invested 10 billion rubles from the state program in R&D.
Additionally, the program included the development of imported machine-tool know-how through direct procurement of technologies, the development of cooperative ties with foreign manufacturers and the localization of foreign production in Russia. To this end, the government announced the creation of machine tool clusters in a number of regions of the country: in the Urals, in the Ulyanovsk, Rostov and Lipetsk regions, as well as in St. Petersburg and Tatarstan.
The promotion of localization bore fruit rather quickly. The Japanese company Okuma opened a joint venture with the Russian company Pumori in Yekaterinburg, their compatriots Takisawa launched an assembly plant in Kovrov, the Indians of Ace Manufacturing systems came to the Perm Territory, and Kovosvit from the Czech Republic came to Azov.
The government's strategy was to first stimulate foreign investors to create enterprises for assembling machine tools from components manufactured abroad, and then to attract them to localize the production of assemblies in Russia.
One of these "alien" enterprises, the German-Japanese DMG-MORI from Ulyanovsk, was assigned the status of a Russian manufacturer by the Ministry of Industry and Trade in September 2016: 70% of the components for their machines are produced by domestic suppliers.
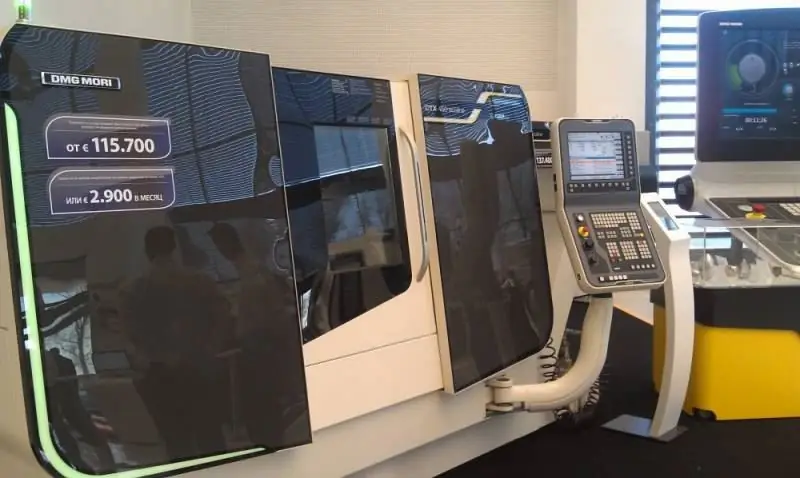
In 2013, the Machine-Tool Building project was launched - the concept of merging two manufacturing enterprises of the Chelyabinsk Region, the St. Petersburg Polytechnic University and the engineering Baltic Industrial Company. Partners in cooperation have created a Russian machine tool brand called F. O. R. T. with its own product line.
Finally, a number of domestic enterprises consolidated around the Stan holding, formed on the basis of the Sterlitamak machine-tool plant. Manufacturers from Kolomna, Ryazan, Ivanovo and Moscow consistently entered Stan.

However, do not flatter yourself. According to Andrey Kostenko, deputy director of the Balt-System company, which produces CNC devices, in 2016 Russian enterprises produced about 250 automated machines, and this is an extremely low figure. But again, in 2013, 133 CNC machines were produced in Russia, that is, almost two times less.
Every year the government increases funding for the industry. So, in 2015 additional deductions from the budget amounted to 1.5 billion rubles, in 2016 - already 2, 7 billion. The Ministry of Industry and Trade expects that eventually the volume of imports of foreign machine tools in 2020 will decrease to 58% 88%).
In March 2017, Deputy Minister of Industry and Trade Vasily Osmakov said that in the summer the department would send an updated strategy for the development of the industry until 2030 to the government. The emphasis of the document will be on "the development of components and components, which are now sorely lacking." Osmakov also did not rule out a partial re-profiling of defense enterprises, which may be engaged in the manufacture of machine tools and their components in accordance with the new program.
Not cloudless. Whom and for what to criticize?
Despite the government's efforts, pessimistic sentiments often circulate in machine tool circles, and the reputation of Russian enterprises remains ambiguous. A cross-sectional survey of customers and manufacturing equipment suppliers revealed what is holding the industry back from growing dynamically.
The interlocutor of the portal from the St. Petersburg defense plant "Arsenal", who wished to remain anonymous, criticized the state of the "daughters" of the machine-tool holding "Stan". According to him, the Ivanovo plant has not produced new products for a long time, demonstrating the same machine at exhibitions, and the Ryazan plant is in a state of disrepair.
At the Ivanovo machine-tool plant, they agreed with this comment. "The plant practically does not work. We found investors, yes. Only these investors, I believe, destroyed a unique enterprise in a year and a half. Since December 1, 2014, the plant has produced two machines under the auspices of Stan LLC. People come to the plant, but there is no work ", - a source at the enterprise told the Voennoye. RF correspondent, who also, for obvious reasons, preferred to remain anonymous.
At the same time, the Stan holding calls the United Shipbuilding Corporation its key supplier. When asked about the most high-tech equipment in the country, the press service of USC answers the following: "in the light of the position of the Ministry of Industry and Trade of the Russian Federation in terms of classifying products as manufactured in the Russian Federation, these are, for example, the machines of the Kolomna Heavy Machine-Tool Building Plant."
The shipbuilders also said that in September 2016, a meeting of the chief engineers of USC and Stan was held in Kolomna, following which the parties signed a joint protocol on interaction.
The Stan press service explained the criticism to Voennoye. RF correspondent by the fact that the company is the most prominent player in the equipment market. According to representatives of the holding, Stan's products occupy half of the Russian machine-tool industry.
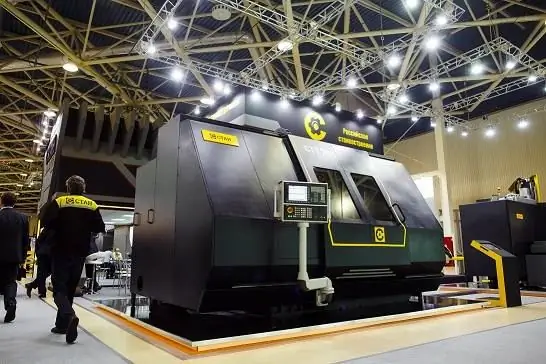
Besides management, there are other vulnerabilities. One of Voennoye. RF's interlocutors, a CNC machine operator with 20 years of experience, said that he considered Russian computer-aided design systems and other software uncompetitive.
The problem of personnel also remains topical. Tatiana Valova, Commercial Director of the Simbirsk Machine-Tool Plant, notes that it will take time to educate a new generation of qualified engineers.
"Technical universities now graduate engineers, yes. But a specialist must first come to the plant and work there for 5-6 years before he begins to understand something. Theory is one thing, but practice is quite another," Tatyana Valova argues. Another problem she calls the habit of young workers who come to the plant, immediately demand high wages, without having the proper experience and category. According to her, the younger generation has no other motivation, except for financial, to work at the enterprise.
Tatyana Valova notes that financially prosperous industries invest their own funds in attracting young people. However, there are not as many such enterprises in the country as we would like.
The specialist also draws attention to the fact that not all Russian enterprises can participate in state programs, in particular, in the program of concessional lending "Machine-Tool Building" - too high requirements for its participants. Unfortunately, the Simbirsk Machine-Tool Plant does not meet these requirements either.
At first glance, the requirements are, in general, fair, since we are talking about the financial stability of enterprises, market prospects and production feasibility of the project. But a vicious circle arises, as in the case of attracting personnel: specialists do not go to the plant because they are not satisfied with the salary, and the salary cannot be raised, because there are not enough engineers to carry out serious projects. Here and there: only financially stable producers are allowed to enter the program, but how can this stability be achieved without preferential loans? The enterprise can get out of the stalemate only by merging with consolidated machine tool structures.
Other industry representatives confirm that outside state programs loans to machine tool builders are issued at too high a percentage.
"Loans? But what can I say. We seem to work" for banks ", as if everything was specially organized for this, - said the marketing department of the Vladimir Machine-Tool Plant. - The percentage depends on how long you take out a loan. It is more than average values in 16% ".
The company said that even participation in R&D does not guarantee a reduction in the technological backlog of manufactured products. “Just while we go through the bureaucratic procedures, a lot of what we are going to do is becoming outdated,” the plant representatives emphasized.
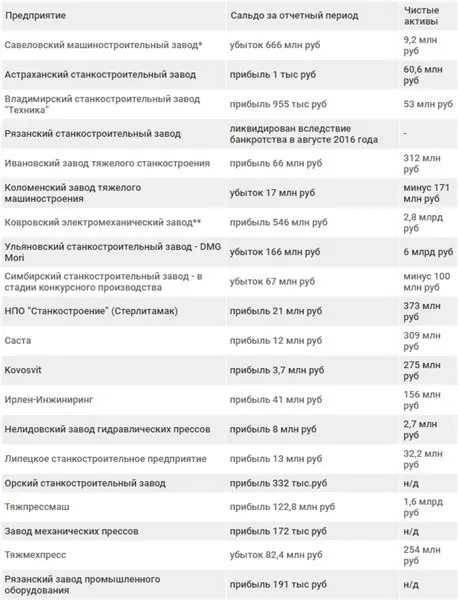
* The currently functioning Savelovsky Machine-Tool Plant was established as a legal entity on September 15, 2016. The data in the table refers to its predecessor.
** For "Kovrovsky Electromechanical Plant" data are given for 2016. In addition to machine tools, the company's assortment includes mobile robotic systems and hydraulic systems.
A word to the military industrialists
In early February, an innovative Italian machine Spirit 100 worth about 6 million euros was inaugurated at the Baltic plant. This one-off example clearly demonstrates the demand for advanced industrial equipment from the defense and shipbuilding industries. But is there a proposal?
Most of the questions from consumers are caused by the insufficient technological level of domestic machine tools. For example, the head of the marketing department of the Kaliningrad Yantar Ilya Panteleev drew attention to the fact that not all Russian machine tools meet the needs of the shipyard in terms of their capabilities.
“First of all, we are talking about large and high-precision jig boring machines, which occupy a special place in the production process. such a plan, thanks to the efforts of our machine tool builders, has risen a notch higher, he said.
In turn, Igor Krasilich, director of the technical development department of the Sukhoi aircraft building company, told Voennoye. RF that he expects the development of domestic five-axis high-performance equipment with large table dimensions, high spindle speeds up to 24,000 rpm and a set of options.
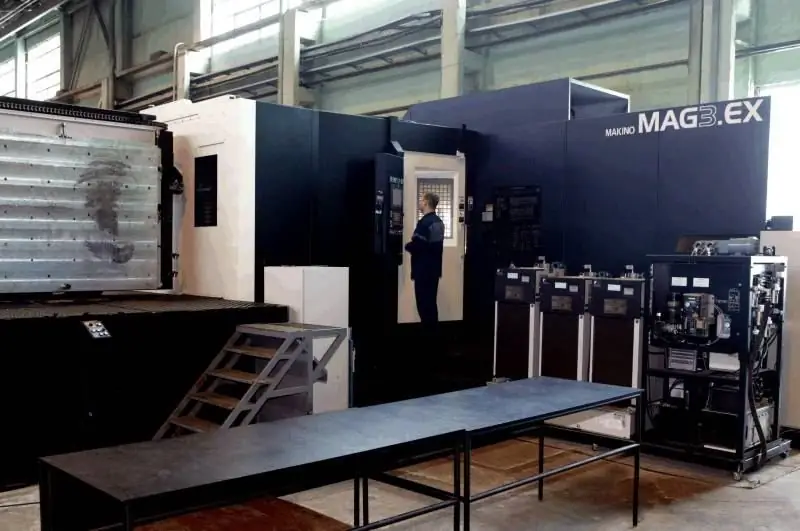
At the Amur shipyard, in response to a question from Voennoe. RF about the "problematic positions of machine tool construction," they said that these were CNC metalworking machines. As explained in the press service of the shipyard, Russian equipment is not able to meet the needs of the plant due to the insufficient level of technological capabilities.
Creeping consolidation as an attempt to break the strategic impasse
"In all problem areas, issues are now being resolved. And we believe that we will nevertheless solve them," Sergei Novikov, deputy editor-in-chief of the industry magazine "Stankoinstrument", shared his optimism with the Voennoye. RF editors.
The expert said that now the industry circles are actively discussing the idea of creating a federal center for scientific, design and technological support of machine tool building on the basis of MSTU "Stankin". It is assumed that the center will include both sectoral institutions and manufacturers themselves.
"Ultimately, the center's activities should end with the release of specific promising equipment," Novikov said, adding that the project is still only at the stage of conceptualization and elaboration.
If we leave aside the skepticism in relation to the incessant processes of integration, then we can assume that we will see a further unification of intellectual and productive resources into a single public-private organism, where the Ministry of Industry and Trade acts as the central nervous system.
This thesis is confirmed by the statement of Denis Manturov that by the end of 2017, five more plants will join the Stan company.
It should be noted that the technological gap has been partially reduced over the 10 years of government work in this direction. Of course, there is no need to talk about its complete overcoming. Nevertheless, a number of Russian manufacturers and structural "think tanks" have begun to master high-tech component nodes and build up their own capacities and capital.
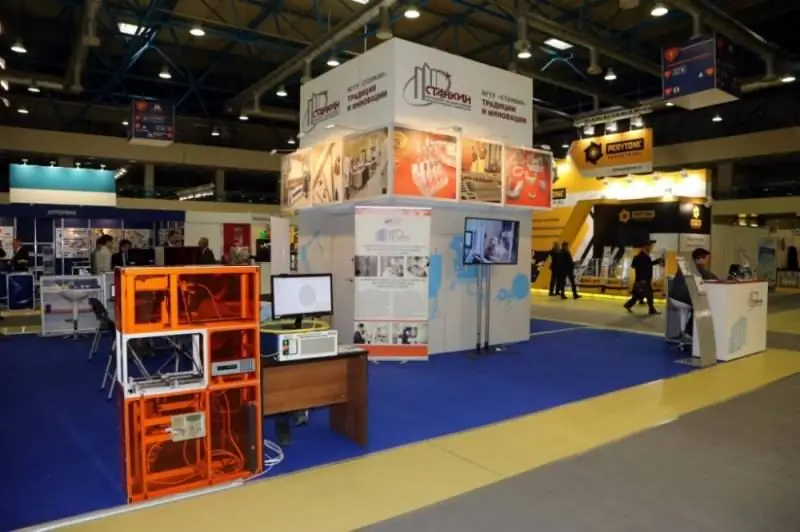
The trend towards recovery in the industry has emerged, although the pace is far from optimal. In addition, it can be assumed that the sectoral consolidation centers in the medium term will absorb enterprises that have at least some attractive assets at their disposal.
A key trend in the machine tool industry is a slow but sure strengthening of the positions of Russian component manufacturers. "Our CNC screens and their components, such as drives, cables and sensors, occupy 60% of the market. Siemens and Fanuc are following us," said Andrey Kostenko, deputy director of Balt-System. software for CNC ".
However, the specialist noted that 70-75% of products manufactured by Balt-System are used for modernization of old equipment by defense enterprises, and only the remaining quarter of components are mounted on new machines.
Considering the industry's prospects, it is necessary to understand what demand for machine tools is expected in the future. The press service of the United Shipbuilding Corporation of the Voennoye. RF editorial office reported that the technical re-equipment of the main machining facilities is already being completed.
“Our main task is to manage to create the required number of production facilities to ensure the projected order in 2016,” said Gleb Nikitin, Deputy Minister of Industry and Trade three years ago. It is fair to say that the "main task" has been only partially completed.
On the other hand, as mentioned at the beginning of the article, Dmitry Medvedev announced a new large-scale program for the development of the military-industrial complex for 2018-2025. The program is likely to stimulate the demand for machine tools.
A moderately optimistic forecast is given by reputable marketers of BusinesStat. They analyzed the demand and needs of the Russian machine tool market. According to their estimates, in 2017 the market demand for machine tools will recover, and in 2018 there will be a full-fledged growth in sales by 7, 9-13, 6%. By the end of 2020, sales of machine tools will amount to 20, 07 thousand pieces.
"There is now an interesting trend in the world - to sell not machine tools, but their working hours. This is done, for example, by the Japanese company Mazak. They send the machine to production, it works, and the company pays for its" labor hours ", - said about the experimental practice Sergey Novikov, deputy editor-in-chief of the Stankoinstrument magazine. "At the same time, the" landlords "remotely monitor its condition and work to carry out maintenance if necessary. I think we will also come to this."
Voennoe. RF found out that the first attempts to shift the Japanese practice of renting machine tools to Russian realities have already been made. As mentioned above, "Stankoprom" leases equipment to the "Savelovsky Machine-Tool Plant" - the general director of the holding Dmitry Kosov told the editorial office about this. It is logical to assume that in the future the integrator will use this business model not only with Tver enterprises, but also with other factories.
The above facts, despite the persisting problems in the industry, allow us to speak about the industry's exit from the peak. If current trends continue, such as the amount of funding, attention from the government, purposeful work with R&D and the development of new component units by manufacturers, the Russian machine tool industry will increase its competitiveness and increase the volume of products by 2022.
This does not mean that Russian machine tools will surpass all analogues, conquering the world market. However, the conditions for the further development of machine tool building have been created - and it may well be that in five years, knowledgeable interlocutors from defense enterprises will stop responding to questions about the quality and quantity of Russian machine tools produced with a sad sigh.