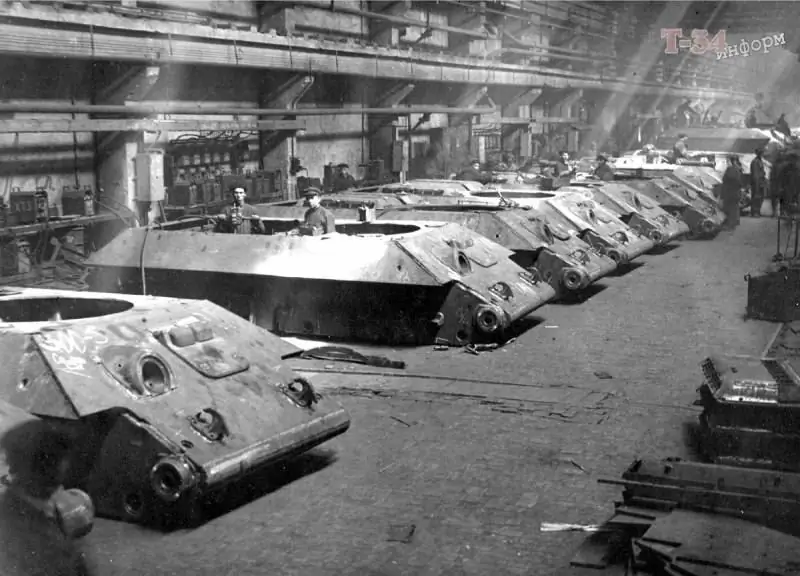
Weak links of the steel guard
How can an avalanche-like increase in the production of tanks badly needed by the front? Nikita Melnikov's book "Tank Industry of the USSR during the Great Patriotic War" provides data on the decline in the conditions for receiving finished products by military representatives.
Since January 15, 1942, tank factories have been very "liberal" in assessing the quality of the manufacture of armored vehicles. Only every tenth medium tank T-34 and heavy KV at the choice of the military representative was subjected to a short five-kilometer run. In the case of the T-60 tanks, there were obviously more doubts, so every fifth light tank was subjected to a run. Or maybe such machines were less needed at the front, so they were stricter towards them even at the acceptance stage. This indirectly confirms the control shooting of the cannon of every T-60 leaving the gates of the factories, while the T-34 and KV guns were tested only on every tenth vehicle. It was allowed to send tanks to the troops with missing speedometers, turret turning motors, intercoms if they were replaced with signal lamps, as well as tower fans. The last point, fortunately, was allowed only in winter.
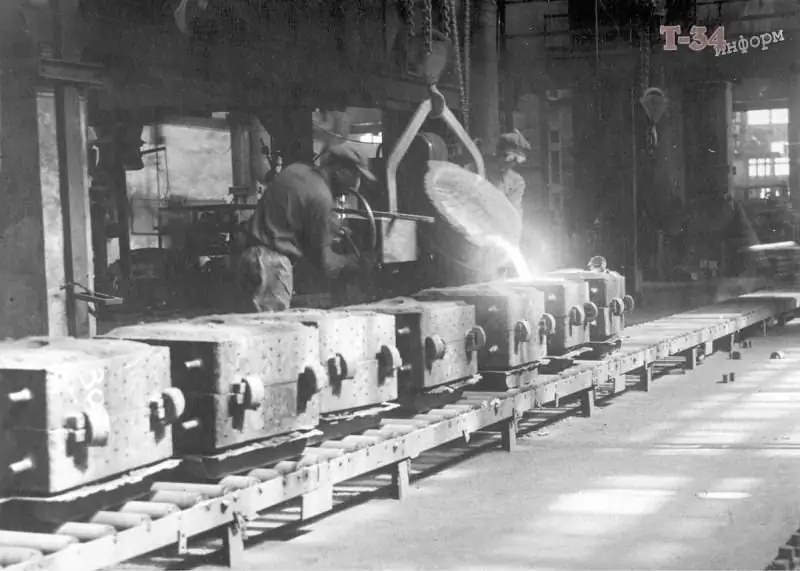
It should be noted separately that the tank industry had already successfully coped with the quantitative indicators of armored vehicles production by the middle of 1942. Uralmash regularly even exceeded the production standards for tanks, and the Kirovsky plant in Chelyabinsk, only from January to March, quadrupled the production of the V-2 diesel engine.
Such rates of production growth were largely due to a serious decline in the quality of the tanks coming off the assembly line. An illustrative example is the 121st Tank Brigade, which, in the course of a 250-kilometer throw, lost half of its heavy KVs due to breakdowns. It happened in February 1942. For a long time after that, the situation did not fundamentally change. In the fall of 1942, 84 KV tanks were inspected, which were out of order for technical reasons, which did not even work out 15 motorcycle hours. Most often, there were faulty motors, broken gearboxes, defective rollers, unusable triplexes and many minor flaws. In the summer of 1942, up to 35% of all T-34 tanks were lost not due to being hit by enemy shells or being blown up by a mine, but due to the failure of components and assemblies (mainly motors). Nikita Melnikov in his work suggests that some of the losses can be attributed to the low level of crew qualifications, but even taking this into account, the percentage of non-combat losses is too high. However, such malfunctions of the KV and T-34 could well be eliminated in the field, sometimes by simply replacing the unit or assembly. But it was useless to fight with the unsatisfactory quality of armor on the T-34 at the front - the armored hulls were cooked from steel with low viscosity, which, when hit by enemy shells, caused cracking, delamination and spalling. Often, cracks formed on new machines, which sharply reduced the crew's chances of a favorable outcome when a German shell hit a crack or an adjacent armor area.
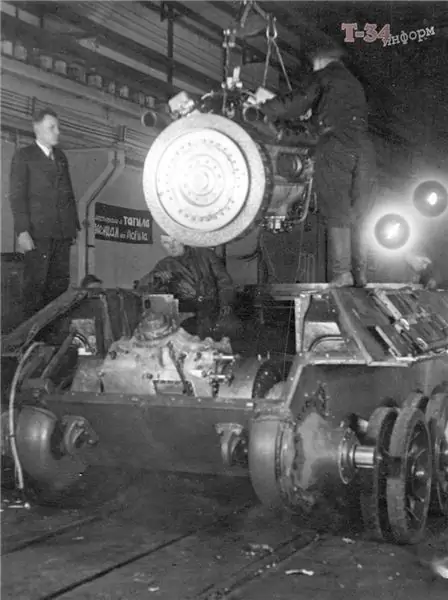
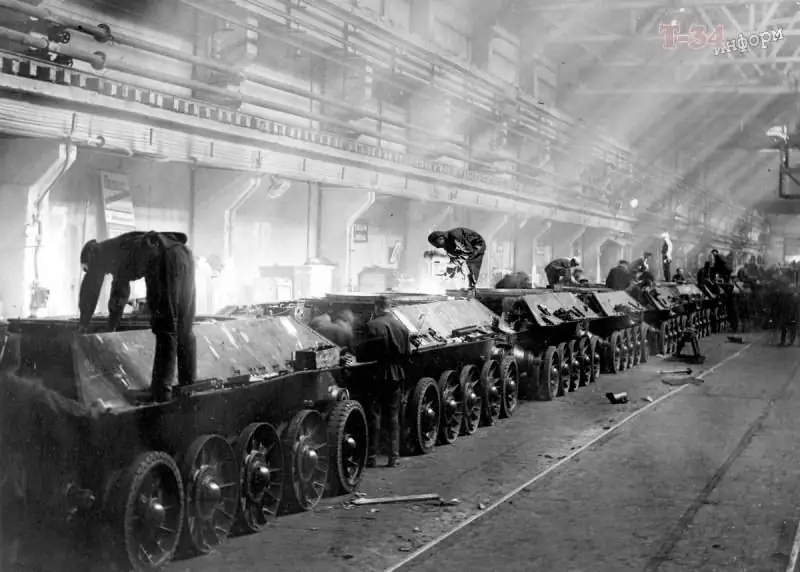
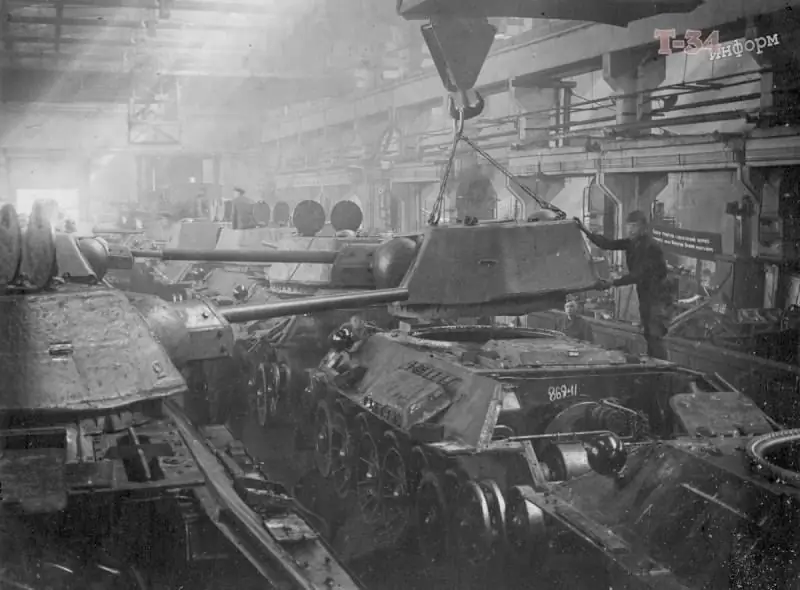
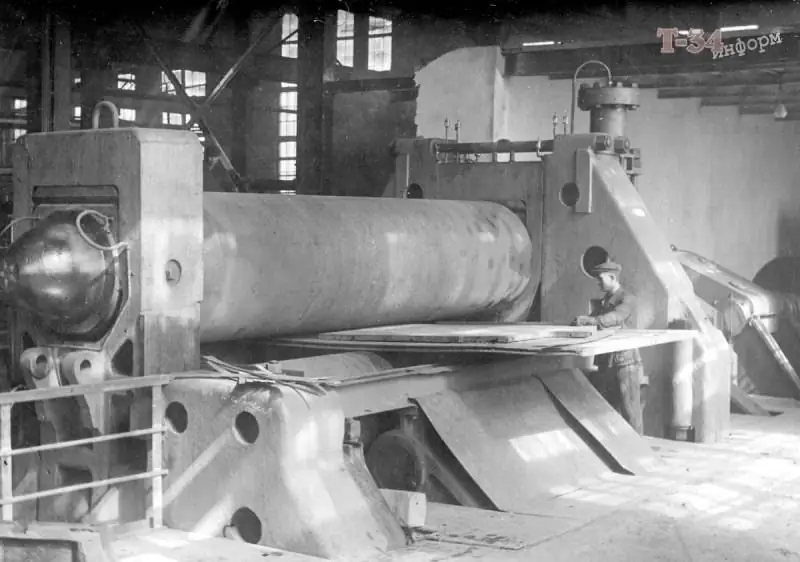
The first alarming calls about the arrival of cracked T-34 units were made in May 1942: factory # 183 received claims for 13 vehicles that month, for 38 tanks in June, and for seventy-two T-34s in the first ten days of July. … The government could not remain silent in this case, and on June 5 the State Defense Committee adopted a resolution "On improving the T-34 tanks."At the same time, the USSR Prosecutor's Office was instructed to investigate the reasons for this decline in the quality of tanks.
In the course of the work, the investigators, in particular, found out numerous facts of theft of products from the diet of workers of the tank industry enterprises. The factory workers were simply undernourished. One example of such a predatory attitude is given in a series of materials about Isaac Zaltsman, the most controversial leader of tank factories.
Among the enterprises that "distinguished themselves" in the production of defective T-34s, the famous plant in Nizhny Tagil took the first place. Moreover, the peak in the release of defective products fell just at the time of the leadership of the aforementioned Zaltsman. However, the director of the enterprise, as we remember, was not demoted, but immediately appointed People's Commissar of the tank industry. Obviously, in the highest echelons of power, it was decided to blame first of all Vyacheslav Aleksandrovich Malyshev, the 1st People's Commissar of the tank industry of the USSR. True, the sobering up came a year later, in the summer of 1943, Malyshev was again put in the place of the people's commissar, which he retained until the very end of the war.
The prosecutor's office in the course of work at the evacuated enterprises of the tank industry, in addition to the half-starved existence of the factory workers, revealed another problem of the unsatisfactory quality of tanks - a serious violation of the production cycle.
Simplification at the expense of quality
As you know, the Mariupol plant named after Ilyich could not be defended, it ended up in the hands of the enemy, and with a mass of technological equipment that they did not manage to evacuate. It was this enterprise (the only one in the country) that was capable of producing full-fledged armored hulls for the T-34 in compliance with all standards. In the Urals, not a single plant could offer such a thing, so the research team of the Armored Institute (TsNII-48) began to adapt the Mariupol practices to the realities of the evacuated factories. For the production of high-quality armor in the volumes required by GKO, there was an acute shortage of thermal furnaces, so the institute developed a new cycle of hardening of armor parts. In Mariupol, the armor plate first went to hardening, then to high vacation, then again to hardening. Finally, a low vacation followed. To speed up production, the first hardening was initially canceled, and then high tempering, which directly affects the toughness of the armor steel and reduces the likelihood of cracking. Also, among the measures necessary, according to the specialists of the Armor Institute, the requirement was to load not one, but immediately four or five rows of armor plates into the thermal furnace. Naturally, this turned out to be much faster, but the final quality of the slabs was very heterogeneous. Interestingly, the Armored Institute later decided to cancel the low tempering procedure, which reduces the residual stresses of the metal, which again did not fail to negatively affect crack formation.
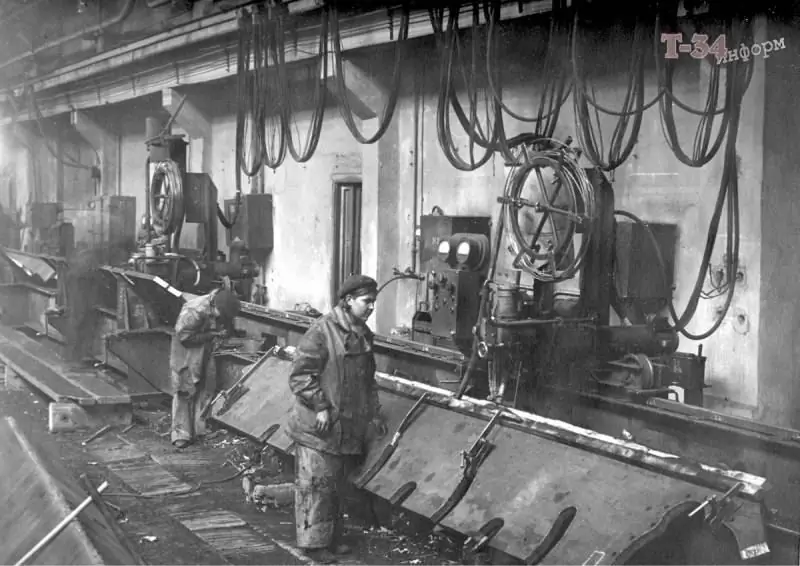
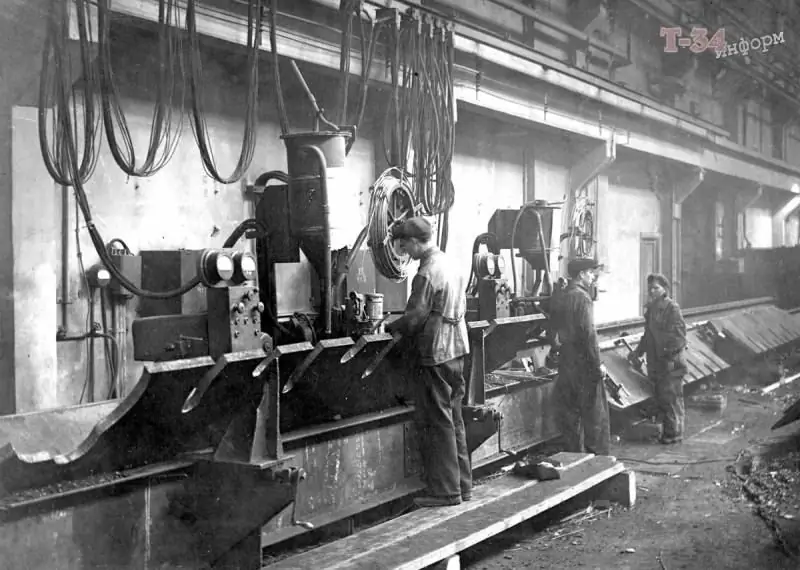
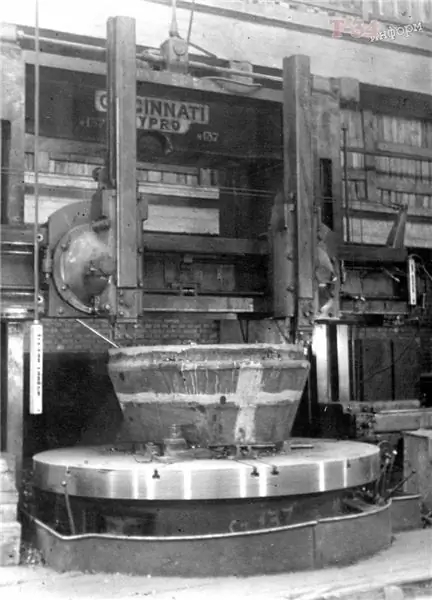
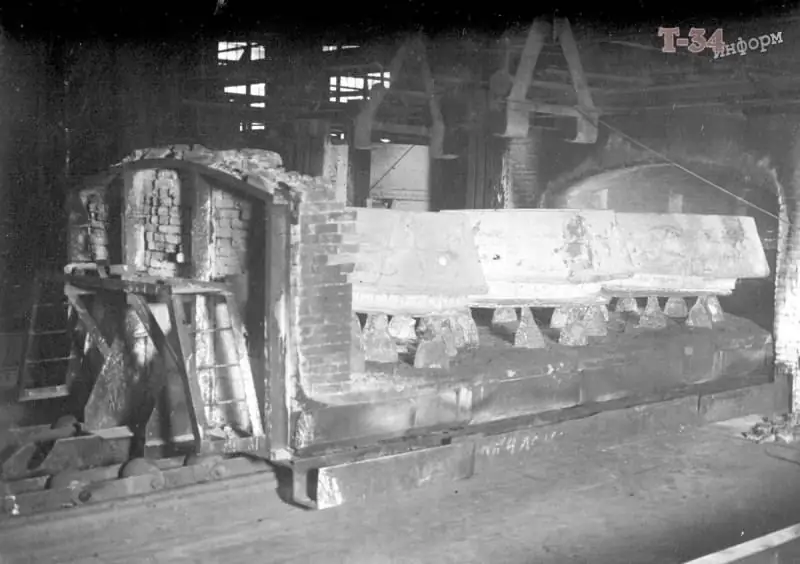
You cannot cut hardened steel with gas cutters - this thesis is known to everyone, but the realities of the production of T-34 armored hulls forced to resort to this unpopular method. The point was in steel 8C, which expanded after quenching, and, naturally, this forced the factory workers to cut it with high-temperature burners. The sense of hardening armor in the cutting area was lost.
It should not be argued that the recommendations for improving the production process were only negative for the quality of the armor. So, a real innovation in the assembly of the hulls of T-34 tanks was the welding of armor plates "in a thorn" instead of the old "in the lock" and "in a quarter". Now the mating parts did not cut into each other, but partially overlapped each other. Only this decision seriously reduced the volume of machine-hours per case from 198.9 to 36.
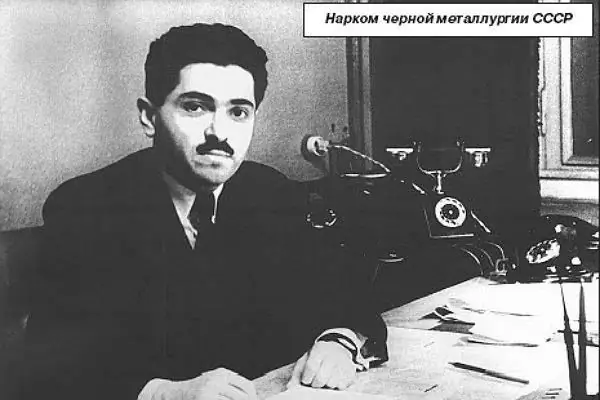
The main supplier of defective steel sheet for factories producing T-34 was the Novo-Tagil plant of the People's Commissariat of Ferrous Metallurgy. At first, he was interrupted by supplies from the Mariupol plant, and when he switched to his own, a stream of complaints came from the front and from the factories. In particular, in the composition of the 8C armor from this enterprise there were serious discrepancies with the technical specifications (TU) in the content of carbon, phosphorus and silicon. In general, there were difficulties with TU. The People's Commissariat of Ferrous Metallurgy did not agree to preserve the TU according to Mariupol standards, in which phosphorus, in particular, should be no more than 0.035%. In early November 1941, the People's Commissar of Ferrous Metallurgy Ivan Tevosyan approved new standards for phosphorus, which increased the possible content to 0.04%, and from April 4 to 0.045%. It is noteworthy that historians still have no consensus on this, of course, an important factor in the quality of armored steel. Nikita Melnikov, in particular, mentions that the Novo-Tagil plant, on the contrary, by the middle of 1942 reduced the proportion of phosphorus from 0, 029% to 0, 024%. It seems that different scientists find different reasons for the appearance of defective T-34s at the front. Be that as it may, the specified norms for the content of chemical elements in the composition of steel were sometimes not observed. It was difficult for the factories to establish a simple uniformity of the supplied rolled products. The prosecutor's office also revealed that at the enterprises of ferrous metallurgy in open-hearth furnaces, armored steel was "undercooked" - instead of 15-18 hours in reality, no more than 14 hours.
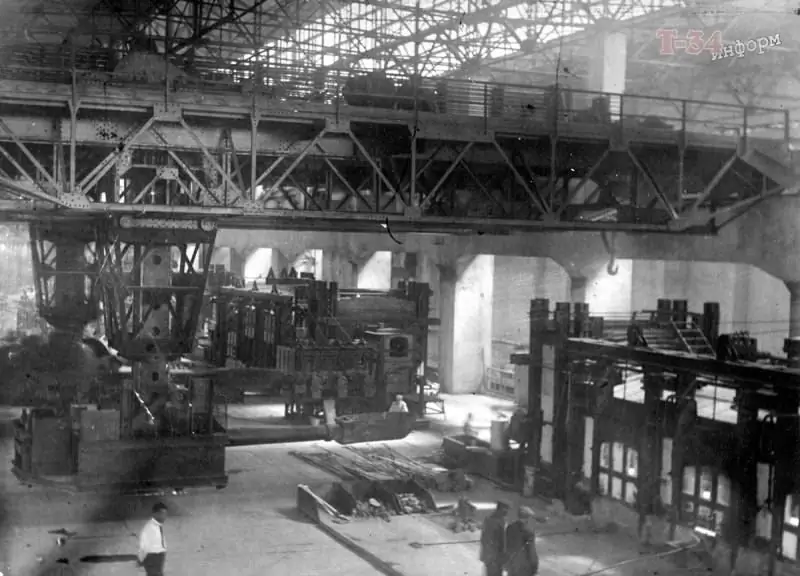
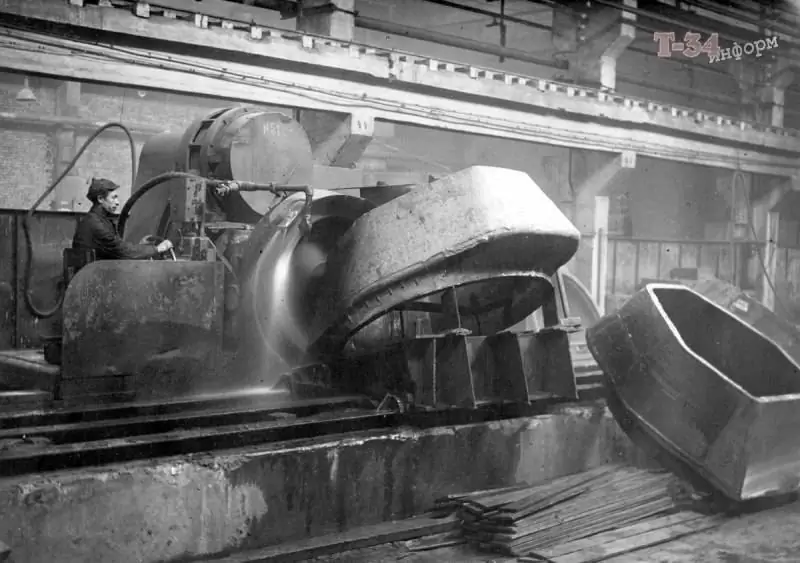
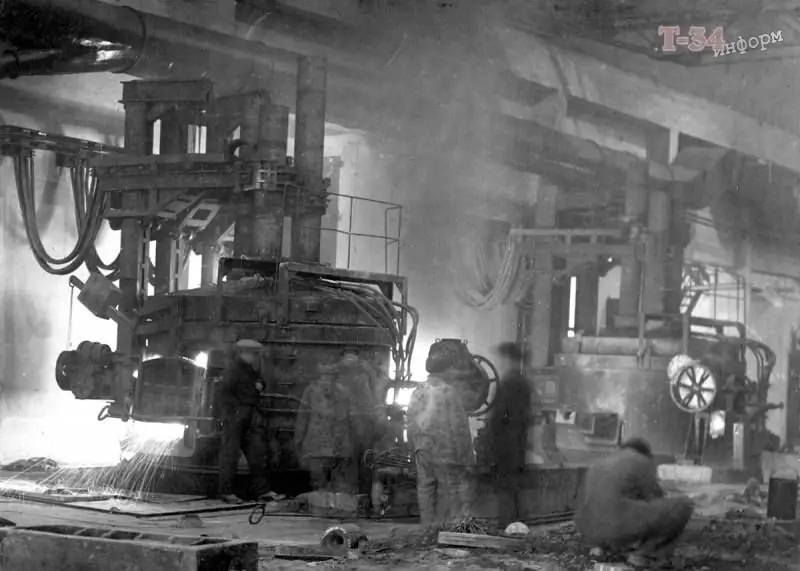
When information about the causes of cracking on the T-34 hulls reached Molotov, the people's commissariats of ferrous metallurgy and the tank industry began to shift the responsibility onto each other. For one, the main reason was the high content of phosphorus in the armor plates, for the other, serious violations of the hull production technology at tank factories.
As a result, TsNII-48 was involved in the work on combating cracks on the T-34 (although he was indirectly guilty of their appearance). The set of measures proposed by the institute only by the end of 1943 made it possible to eliminate some of the comments. And the improvement in the quality of steel production at ferrous metallurgy enterprises made it possible to reduce the proportion of rejects from 56, 25% in 1942 to 13, 30% in 1945. The enterprises did not reach the level close to 100% until the end of the war.