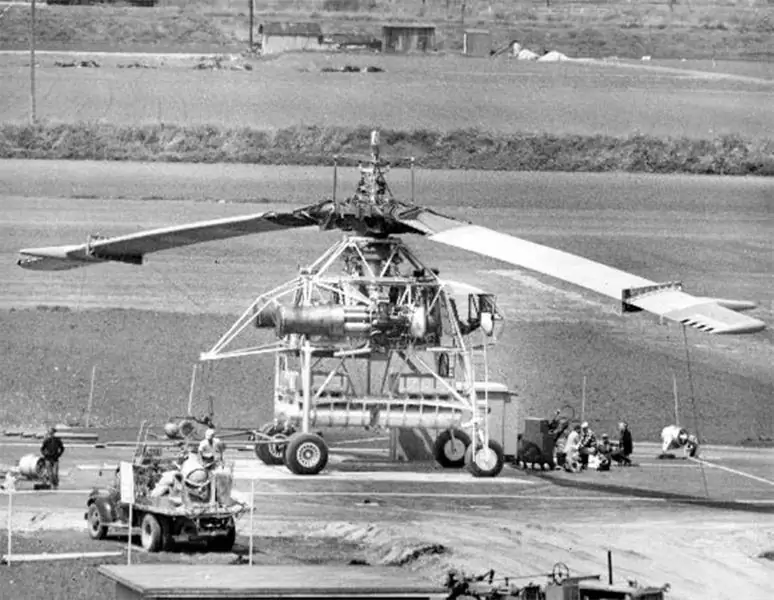
In 1952, the first flight of an experimental transport helicopter XH-17 Flying Crane developed by Hughes Aircraft took place in the USA. During the tests, this machine showed a lifting capacity that was unique for its time, but at the same time it had a lot of serious shortcomings. As a result, "Flying Crane" did not go into series - although it served as the basis for a new project.
Military wishes
The history of the XH-17 project dates back to the mid-forties and was initially written without the participation of the Howard Hughes company. By that time, the US Department of Defense had studied the available helicopters and understood all the prospects for this direction. Already on January 31, 1946, a tactical and technical assignment for a promising transport vehicle appeared. By the standards of that time, it was a "heavy" helicopter.
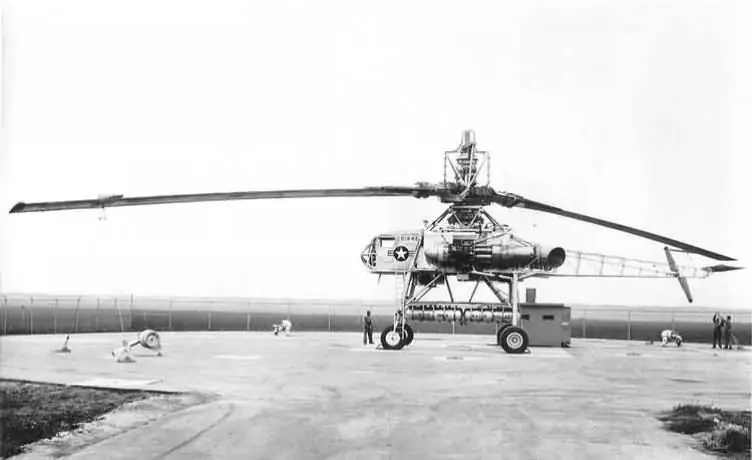
The military wanted a helicopter capable of carrying cargo measuring 2.44 x 2.44 x 6, 1 m and weighing 10 thousand pounds. He was supposed to fly at speeds up to 105 km / h, climb to an altitude of at least 900 m and have a tactical radius of 160 km, subject to a 30-minute stay at the maximum distance from the base. The design should have been made collapsible - for the transfer of equipment by land transport.
Research organizations from the US Army Air Force conducted research and clarified requirements. It turned out that the current level of technology and mastered solutions do not allow creating a helicopter with the required characteristics. The search for alternative structures with the desired potential was started. One of them was suggested by the German specialist Friedrich von Doblhof. He came up with the concept of a rotor-driven rotor helicopter. According to this idea, the engine in the fuselage was supposed to supply compressed air to the nozzles on the blades, which were responsible for the rotation of the propeller.
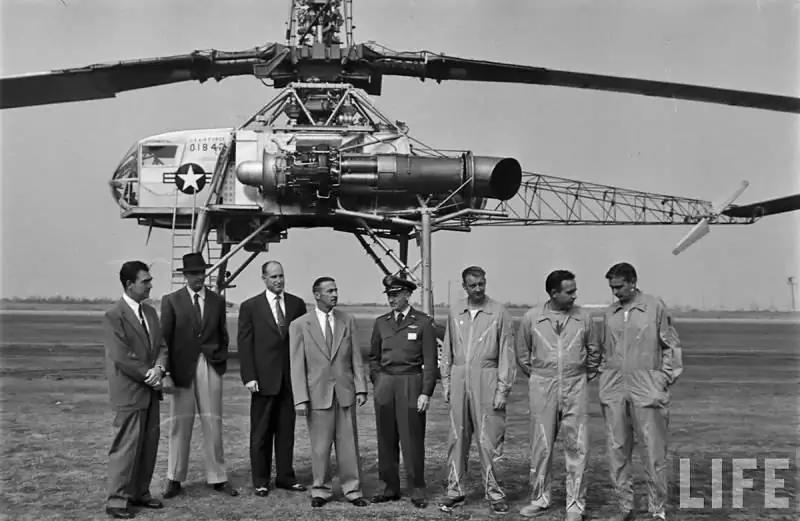
First try
Several aircraft building companies took up the job at once. By order of the Ministry of Defense, they worked out the issue of creating a ground stand simulating the units of a helicopter of unusual architecture. On May 2, 1946, the Kellett Autogiro Corporation of Pennsylvania won the competition for the development of the prototype system. She had to complete research and design, which was given a year.
New calculations showed the complexity of the task. So, it turned out that none of the available jet engines will allow you to create sufficient thrust at the nozzles and ensure the required rotational speed of the main rotor. In this regard, it was necessary to develop a larger diameter propeller with the required bearing characteristics. In addition, the power plant was compelled to supplement with a second engine.
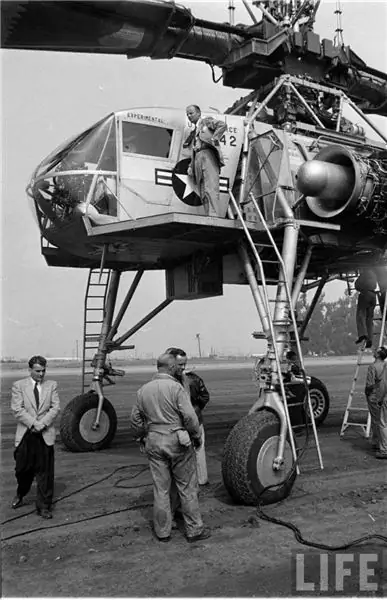
On August 27, 1947, a contract was signed for the construction of a ground stand. This document also stipulated the future restructuring of the stand units into a full-fledged experimental helicopter - it was assigned the working designation XR-17 (a new one would be introduced later - XH-17). Within a few months, Kellett completed part of the construction work, but then the situation changed.
Kellett faced financial difficulties and the project had to be sold in 1948. The buyer was Hughes Aircraft. She paid 250 thousand dollars (about 2.75 million dollars at current prices), for which she received all the documentation for the project and an unfinished stand. In addition, G. Hughes lured into his company all the responsible participants in the project. The United States Air Force did not object to this, as the most important project passed into the hands of a well-known and reliable contractor.
Stand and helicopter
The units and documents were transported to the Hughes Aircraft site in California, after which construction was completed. By this time, the stand was actually a full-fledged helicopter, which was not yet going to be lifted into the air. Nevertheless, he already had almost all the components and assemblies necessary for this.
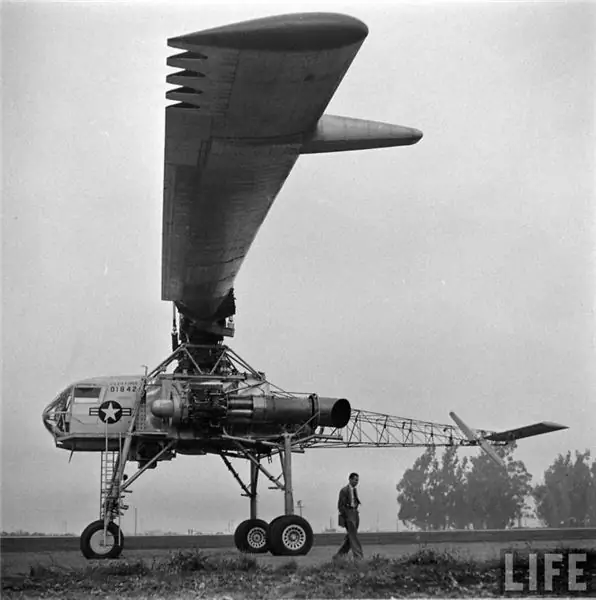
The basis of the helicopter stand was a welded frame of a characteristic type. It was distinguished by high landing gear struts, a massive base for the propeller hub and a long tail boom. To save money, most of the units were borrowed from serial equipment. So, the cockpit was taken from the Waco CG-15 airframe. A 2,400 liter fuel tank from a B-29 bomber was installed behind her. The wheels of the landing gear were borrowed from the B-25 and C-54 aircraft.
General Electric 7E-TG-180-XR-17A engines, based on the serial GE J35, were mounted on the sides of the helicopter. The compressors of the engines had a compressed air extraction system. Through pipelines, it was fed into the rotor hub, and then through a complex system of pipes and movable joints - into the blades. Also in the sleeve there were connections for transferring fuel to the blades.
Two propeller blades were built on the basis of a tubular spar, which provides air supply to the tips. At the end of the blade there were four combustion chambers, where air and fuel were supplied. The thrust from the cameras was supposed to ensure the rotation of the propeller. Due to the large size and mass of the blades, it was necessary to develop a special rotor hub with appropriate fastening means and a reinforced swashplate.
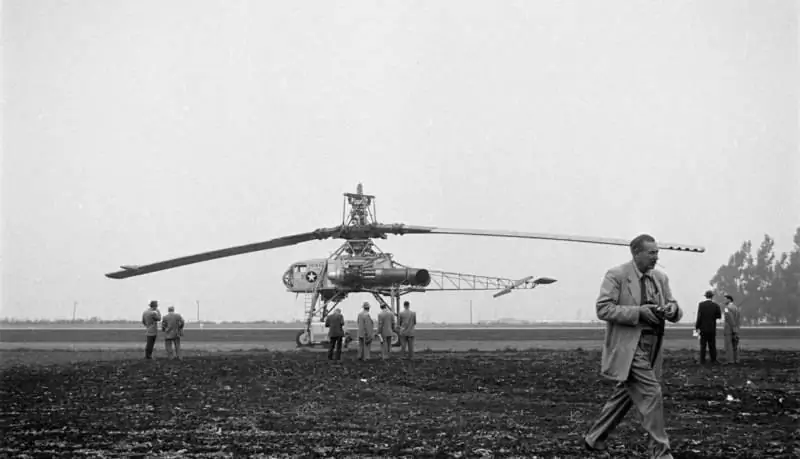
The main rotor with a record diameter of 39.62 m was supposed to rotate at a speed of 88 rpm. - slower than other helicopters of the time. The total power of the power plant reached 3480 hp, which ensured overfulfillment of the basic requirements of the customer in terms of carrying capacity.
On the ground and in the air
On December 22, 1949, Hughes specialists performed the first launch of the XH-17 stand. The mechanisms have confirmed their efficiency, but not without "childhood illnesses". It took several weeks to fix the identified shortcomings. After that, full-scale ground tests began.
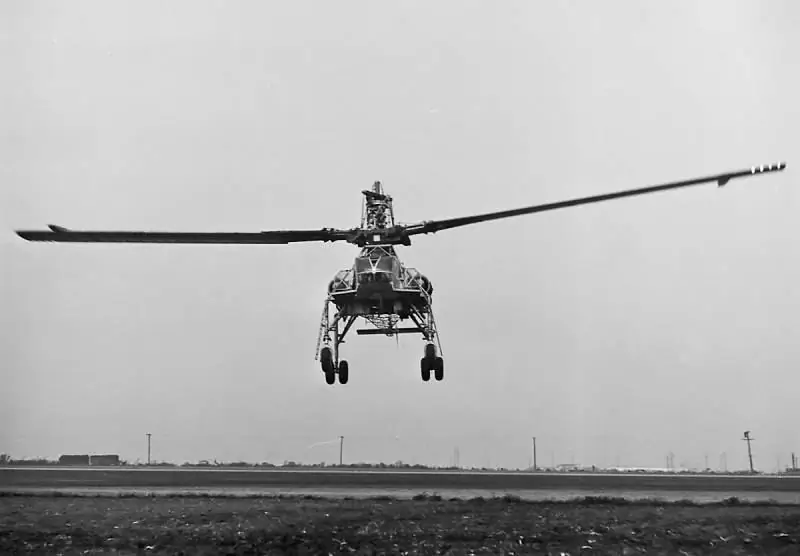
In June 1950, during the next tests, there was a serious breakdown of the swashplate. The stand was in need of complex repairs, but the customer was not worried and was optimistic. The development company was recommended to repair the stand, recycle some of the units - and lift the helicopter into the air. However, this time the list of necessary improvements was quite long.
Most of the units have undergone one or another modification. In addition, a completely new hydraulic control system was developed for the helicopter. A tail rotor was placed on the tail boom, taken from the H-19 helicopter. For him, it was necessary to develop a drive with power take-off from the engines. It is noteworthy that the main rotor with the original drive did not create a significant reactive moment, and thanks to this, the main task of the tail rotor was heading control.
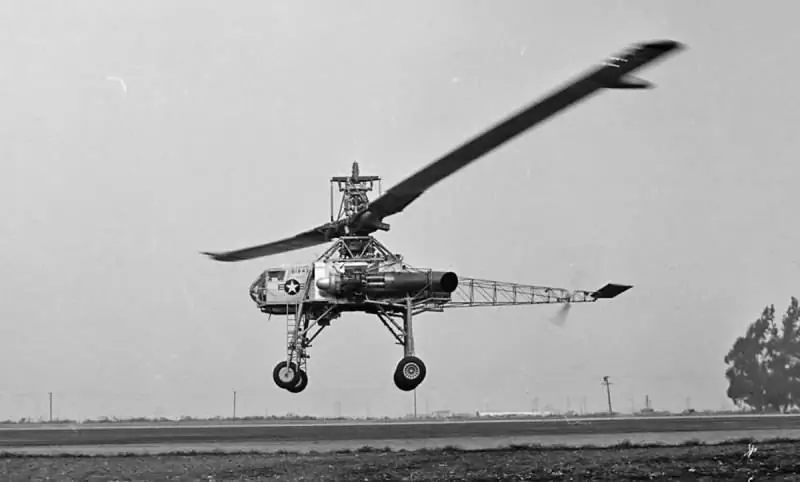
The XH-17 helicopter was taken out for testing only in the summer of 1952. They again carried out a full cycle of ground tests, after which they received permission for the first flight. On October 23, pilot Gail Moore took the XH-17 into the air for the first time. The flight lasted for about a minute. After taking off, the pilot noticed an excessive load on the controls and immediately landed.
After adjusting the control systems, flights continued. New possibilities were constantly demonstrated, as well as various shortcomings were identified and immediately corrected. At the same time, it was not possible to get rid of the rotor vibrations. Despite this, it turned out to carry out an almost complete test cycle, incl. with the definition of the main characteristics.
The helicopter 16, 25 m long and 9, 17 m high had a dry weight of 12956 kg and could lift the required load of 1,000 pounds. During the tests, a flight was carried out with a maximum mass of 19.7 tons and a load twice that required by the customer. Payloads of various kinds were suspended between the landing gear struts. The maximum speed of the vehicle reached 145 km / h, the range was 64 km.
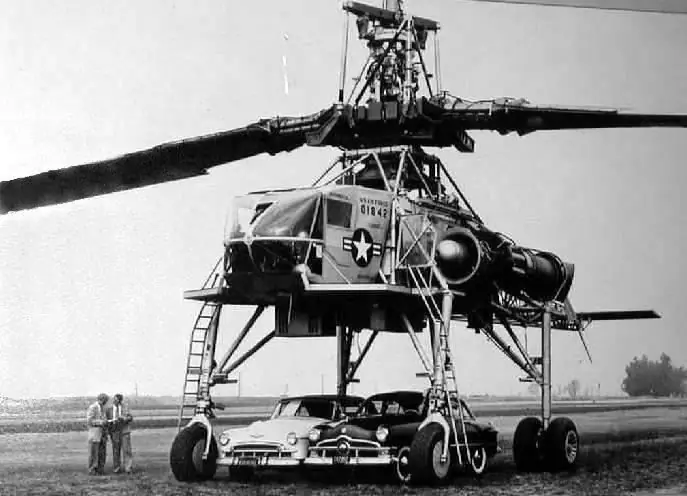
Ambiguous result
In early 1952, Hughes received an order to develop a new helicopter. Based on the experience of the XH-17 project, the XH-28 helicopter should have been created - a full-fledged machine suitable for operation in the army. Work on the XH-28 continued until mid-1953, after which the customer refused further support for the project.
In this regard, the prospects of the existing XH-17 helicopter were questionable. It was used for research and experience in the interests of the next projects, but now all this work actually did not make sense. Nevertheless, Hughes Aircraft did not stop testing and continued scientific work, even without real prospects.
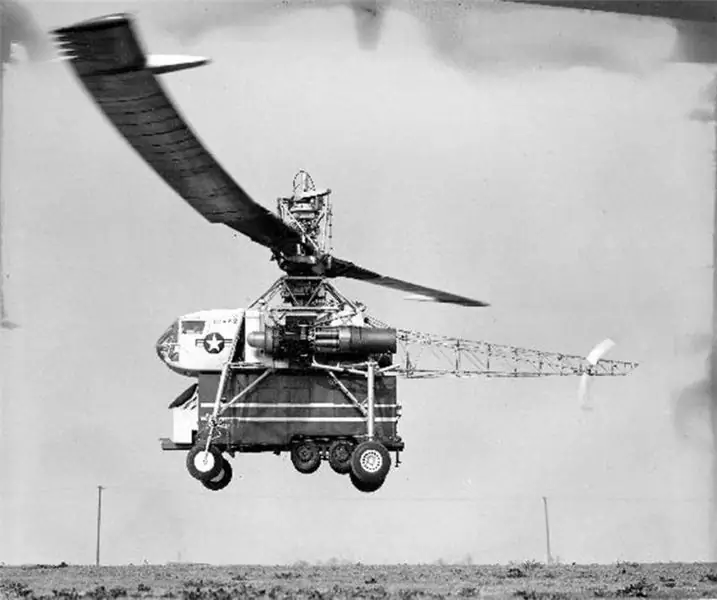
Flight tests of the experienced Hughes XH-17 Flying Crane continued until the end of 1955 and ended in connection with the development of the service life of the rotor blades. By this time, all the required data had been collected, and the project had lost its real future. Therefore, the production of new blades was considered appropriate.
In terms of performance, the helicopter as a whole met the earlier requirements. He could carry all the planned cargo - and even more. After fine-tuning, the helicopter was distinguished by a low level of vibrations in the cockpit and an effective control system based on hydraulics.
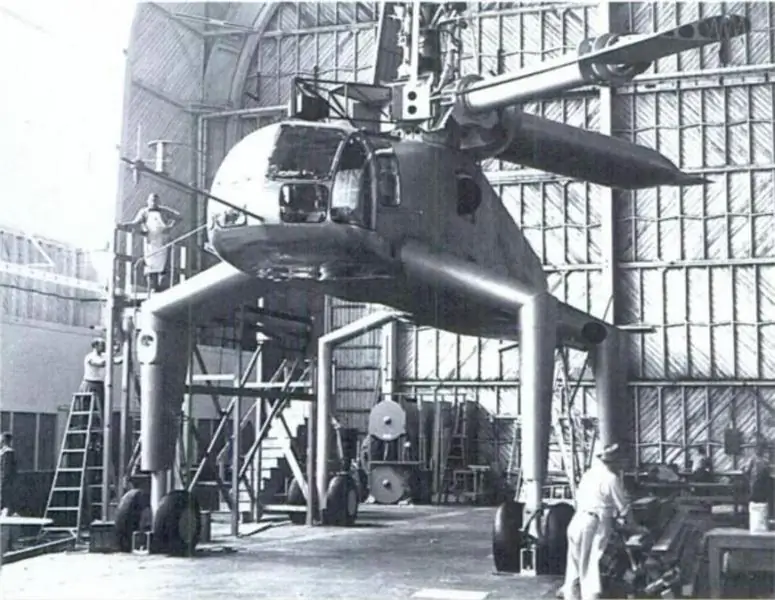
At the same time, the vehicle turned out to be insufficiently maneuverable and carried out commands with a noticeable delay. During the tests, the lack of reliability of some units appeared, which is why the helicopter was regularly sent for repairs. Probably the main problem was the excessive fuel consumption of the two engines. Because of this, the practical radius was limited to only 64 km instead of the required 160 km.
The main developments on the XH-17 helicopter were used in the new XH-28 project, but it was not completed. After the end of the tests, the experienced XH-17 went to the parking lot with no clear prospects. Later it was dismantled as unnecessary. The same thing happened with the full-size XH-28 mockup.
Despite the lack of real results, the "Flying Crane" by Kellett and Hughes has remained in the history of the American and world helicopter industry. He showed record performance and special capabilities - by the standards of his time. Further development of helicopters led to new achievements, but one of the XH-17 records still remains intact. Its main rotor is still the largest helicopter built to this day. However, this did not help the car reach the series and operation.