First, let's work on the mistakes of the previous article. In it, the author argued that the USSR before the war had mastered the production of turning-boring machines capable of processing large-diameter tank shoulder straps, while the first machines with a faceplate diameter of 2000 mm were produced in 1937.
Alas, this is (at least partially) incorrect. Unfortunately, the history of machine tool building in the USSR is not well covered in our country, and it is extremely difficult to find the relevant literature. The author of this article eventually managed to get hold of a very detailed work by L. A. Aizenstadt. and Chikhacheva S. A. under the title "Essays on the history of machine tool construction in the USSR" (Mashgiz, 1957). According to L. A. Aizenstadt. and Chikhacheva S. A. the first single-column turning-boring lathe with a faceplate diameter of 800 mm was produced at the Sedin plant (Krasnodar) in 1935. Apparently, we are talking about machine 152, although this, unfortunately, is inaccurate - the authors of "Sketches", unfortunately, did not indicate the names of vertical lathes produced before the war. At the same time, as follows from the comparison of the "Sketches" with the data on the history of the plant posted on its official website, despite the production of the first sample in 1935, the machine 152 was adopted by the state commission with the resolution "fit for use" only in 1937.
As for other models of boring lathes, the "Sketches" report that in 1940 two more models of machines were produced: a single-column machine with a faceplate diameter of 1,450 mm and a two-column machine with a faceplate diameter of 2,000 mm. Unfortunately, it is completely unclear whether we are talking about experimental or mass production.
Although this does not apply to the topic under discussion, it is interesting that at the plant named after him. Sedin in 1941, the production of a giant turning-boring machine with a mass of 520 tons with a faceplate diameter of 9 m was completed - this machine was assembled by the plant named after S. Sverdlov in Leningrad.
Returning to the tank topic, we state that two very important issues remain unsolved. Firstly, unfortunately, the author was never able to find out whether the serial production of vertical lathes with a faceplate diameter of 2,000 mm was launched before the start of the war and during it in the USSR, and if such was established, then how many machines were produced in total in the pre-war and war years. As you know, the plant them. Sedina was in the occupied territory from August 9, 1942 to February 12, 1943, but before the retreat, the Germans almost completely destroyed the plant. But what can this tell us? A certain number of machine tools on it could have been made before the plant was "captured", moreover, the equipment needed for the production of machine tools could have been taken out during the evacuation, and then the production of vertical lathes could have been established somewhere yet. On the other hand, the author of this article did not find any mention of this. Here is L. A. Aisenstadt. and Chikhachev S. A. they say nothing about the military production of boring lathes. But at the same time, respected authors write that during the Great Patriotic War, the machine tool industry of the USSR mastered the production of a large number of machine tools of new designs, they give many examples, but they point out directly that it is absolutely impossible to list them all in some detail within the framework of one work. Maybe the production of vertical lathes remained outside the scope of their work?
The second question: unfortunately, it remains unknown whether it was possible to organize the production of tank shoulder straps on these machines, since, as many dear readers rightly noted in the comments to the previous article, the fact that the diameter of the faceplate is greater than the diameter of the shoulder strap does not guarantee such a possibility.
The thing is that the diameter of a tank shoulder strap is one thing, but the dimensions of the part that needs to be placed on the faceplate in order to process the tank shoulder strap is completely different. Nevertheless, the second question, most likely, can be answered in the affirmative, because it should not be assumed that for processing a tank shoulder strap it was required to perch a whole tower on a boring lathe. After all, the tower shoulder strap was one of its parts, and, as you can see in the photo of those years, it was processed separately from the tower. So, for example, in the previously cited photograph of a boring lathe.
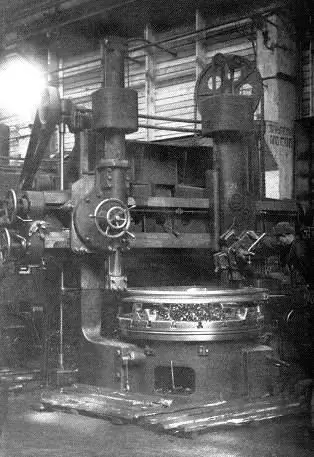
The procedure for processing a tank shoulder strap for a T-34 at factory # 183 in 1942 is just captured. Another photo.
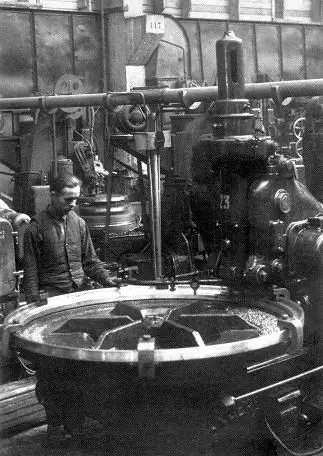
Demonstrates the procedure for cutting the teeth of a tower shoulder strap at the same plant No. 183 in the same 1942, but, of course, on a different type of machine. As we can see in both photos, the size of the processed parts is much smaller than the T-34 turret and, perhaps, is quite close to the shoulder strap diameter.
Accordingly, the question of whether turning-boring lathes suitable for processing wide shoulder straps of the T-34M and T-34-85 towers were produced in the USSR before the war remains controversial. But there is no doubt that even before the start of the Great Patriotic War, our factories had a large fleet of such machines with a large faceplate diameter, since the other considerations expressed by the author in the previous article remain valid. Of course, we needed machine tools for the production of locomotive wheels, excavators and other equipment, and if they were not of Soviet production, then, obviously, we acquired abroad. Let us also recall the letter of Lieutenant Colonel I. Panov, who reported in 1940 that Plant No. 183 had a sufficient machine park for the production of tanks with extended shoulder straps. Let us recall that the orders for 1941 for the purchase of imported equipment from factories No. 183 and 75, as well as STZ did not contain turning-boring machines. And this despite the fact that the plant No. 183 was to start production of the T-34M with a wide turret ring in 1941, and the STZ was required to be ready to launch the T-34 into series starting from January 1, 1942. Let us recall that the production The T-34-85 began at our factories earlier than imported machines under Lend-Lease were supposed to arrive, etc. And, of course, that for the production of 250 IS-2 tanks per month, plant No. 200 needed 7 vertical lathes with a large faceplate diameter, and how many of them were needed for plant No. 183, which produced up to 750 T-34-85 per month? Could his needs have been met by several machines we received under Lend-Lease?
And if you also remember that to date, no one has presented to the general public data on the volumes of supplies of vertical lathes under Lend-Lease, then it turns out quite interesting. We know that the USSR was going to order such machines abroad to fulfill the production program of 1944, but we do not know whether they were ordered, and if so, whether they were delivered, when and in what quantity. Similarly, it is not known whether such machines were supplied under Lend-Lease earlier, or by other channels: during the war years, the USSR acquired products that were not included in the lists of permitted under Lend-Lease, that is, within the framework of ordinary purchase and sale transactions.
Let's finish on this topic with vertical lathes and move on to the peculiarities of the production of the T-34 in 1941-42.
So, as we said earlier, at the time of putting into mass production, the T-34 project contained a number of shortcomings, the main of which were the insufficient crew size, poor visibility from the tank and significant transmission shortcomings. In addition, the tank suffered from a fair amount of "childhood diseases", which could be easily eliminated based on the results of experimental operation. And, as if this was not enough, the factories where it was planned to launch production of the T-34 had not previously produced medium tanks, since light BTs were made at plant No. 183, and no tanks had been produced at STZ before.
The shortcomings of the T-34 were well understood by our management, nevertheless, a decision was made to send the tank into mass production. There are 2 main reasons for this decision. The first of them was that even in its current form, the T-34 was definitely superior in combat qualities to light tanks BT-7, not to mention any T-26 and so on. The second is that it was impossible to organize the production of such a new and complex machine, which was the T-34, for factories No. 183 and STZ all at once, it was necessary to build an effective production chain within the enterprises and no less effective interaction with contractors-suppliers.
Therefore, it was decided to produce the T-34 in its current form, but at the same time develop an improved, modernized tank design that would be spared the known design flaws. The project of this tank is known as the T-34M - here is the commander's cupola, and five crew members, and a turret with a wide shoulder strap, and a new transmission … At the same time, the T-34M was supposed to go into mass production in 1941 and gradually displace T-34 model 1940
Obviously, such a solution made it possible to kill not even two, but several birds with one stone. On the one hand, the Red Army immediately began to receive medium tanks with a 76, 2-mm cannon and anti-cannon armor. The troops began to master new, unusual equipment for them. Factories - to develop production processes and the efficiency of their supply chains. The price for this was that the T-34 was supplied to the troops with already known, but not eliminated, shortcomings. Of course, one could have taken a different path and postponed the release of the T-34 until all its shortcomings were eliminated, but, apparently, the leadership of the Red Army rightly believed that it was better to have an imperfect tank in the troops than not to have a good one. … And besides, as the T-34M project and its units are ready, the domestic industry would have been prepared as much as possible for its serial production.
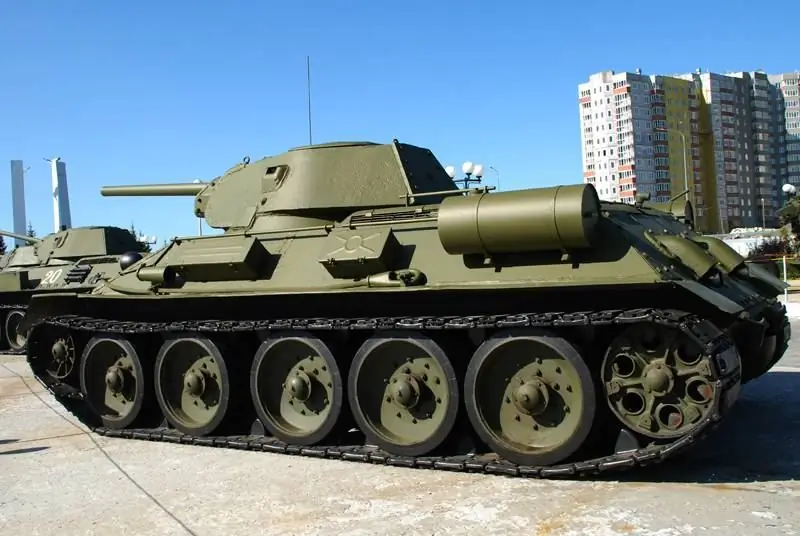
Thus, we see that the production of the "damp" T-34 before the war has quite reasonable explanations. But here another question arises. With the approach described above, the rejection of any serious modernization of the T-34 mod. 1940 - it did not make sense, since already in 1941 it was supposed to go into the T-34M series. But the war began, the new diesel engine for the T-34M was never ready, and it became clear that no "thirty-four-em" would go to the troops. Then why the first changes for the better - a new checkpoint, commander's cupola, etc. appeared on serial T-34s only in 1943? What prevented you from doing this before?
Very often in the descriptions of the T-34, the simplicity of the design of the tank is noted, thanks to which it was possible to establish its mass production in the belligerent USSR. This is undoubtedly correct, but it should be noted that the T-34 did not acquire this dignity at once. Of course, the creators of the tank, M. I. Koshkin and A. A. Morozov, put a lot of effort into achieving an outstanding result without resorting to complex technical solutions. But nevertheless, the design of the T-34 as of 1940 turned out to be very difficult for our factories, which were supposed to produce it, especially in wartime. So, for example, "History of tank building at the Ural tank plant №183 named. Stalin "indicates that" The design of armored parts … was carried out without taking into account the technological capabilities, as a result of which such parts were designed … the production of which in mass production would have been impossible … ". At the same time, unfortunately, initially "… the production technology was designed for the availability of skilled workers who could, using universal equipment, in small batches, perform machining of complex tank parts, and the quality of processing depended on the qualifications of the worker."
Simply put, the designers created a promising project of the tank, but it soon became clear that its design was far from optimal for production on the equipment available at Plant No. 183, or it required highly qualified personnel, which the enterprise lacked or did not have at all. In some other processes, the plant could have had enough equipment and qualified employees, but for relatively small volumes of mass production, and the tank had to become truly massive. Accordingly, it was required to find a compromise - somewhere to change the design of the machine or its individual parts, and somewhere to purchase and install new machines, change the production technology.
It is easy to talk about this when it comes to one enterprise, but in some cases, such design changes concerned not only the plant where the final assembly of tanks is carried out, but also its subcontractors. And now let us also remember that the T-34 manufacturing plant was far from alone, and, of course, the machine park and the qualifications of the workers on them differed significantly.
“What did you think about before the war?”, The dear reader will ask, and, of course, he will be right. But remember that the production volumes for 1941 did not boggle the imagination at all: 1,800 tanks for factory # 183 and 1,000 tanks for STZ. This is only 150 and 84 cars per month. For this production program, the management of the enterprises determined the need for an additional machine park, personnel, etc. At the same time, with the beginning of the war, it was necessary to increase production volumes several times, for which, obviously, the machine park and personnel of STZ and plant No. 183 were not fully designed.
And we are talking only about those factories where it was planned to produce T-34s even before the war, and, accordingly, various preparatory measures were carried out. But let's not forget that during 1941-42. production of the T-34 was mastered at 4 more plants: No. 112, 174, as well as UZTM and ChKZ.
Before the war, factory # 183 was clearly the leader in the production of the T-34, so, for example, in the first 6 months of 1941 it produced 836 tanks, while at STZ only 294. In June 1941, factory # 183 produced 209 vehicles., and STZ - only 93. But the plant No. 183 was located in Ukraine, in Kharkov, and, of course, it urgently needed to be evacuated (to Nizhniy Tagil), which was done in the period from September to October 1941. It is clear that something like that “relocation”, and even in such a short time, would have become extremely difficult even in peacetime, but in wartime it was a real labor feat. And, taking into account all of the above, it was necessary to somehow manage at the same time and increase production volumes … In December 1941, plant No. 183 produced only 25 tanks, in March 1942 - already 225, thereby surpassing any monthly production of the pre-war period, and in April - 380 vehicles, which is 42, 8% higher than the best production in Kharkov (266 tanks in August 1941).
As for the STZ, it, unlike the Kharkov plant, did not relocate anywhere, but there were plenty of problems on it even without evacuation. The front "rolled" closer and closer, a significant part of subcontractors stopped working, or no longer had the opportunity to supply spare parts and components to STZ. Thus, the plant had to master an increasing number of productions directly at home, and at the same time - to increase the pace of production … which STZ did - the production of the T-34 on it continued until the battles began on the very territory of the plant (and even a little over Togo).
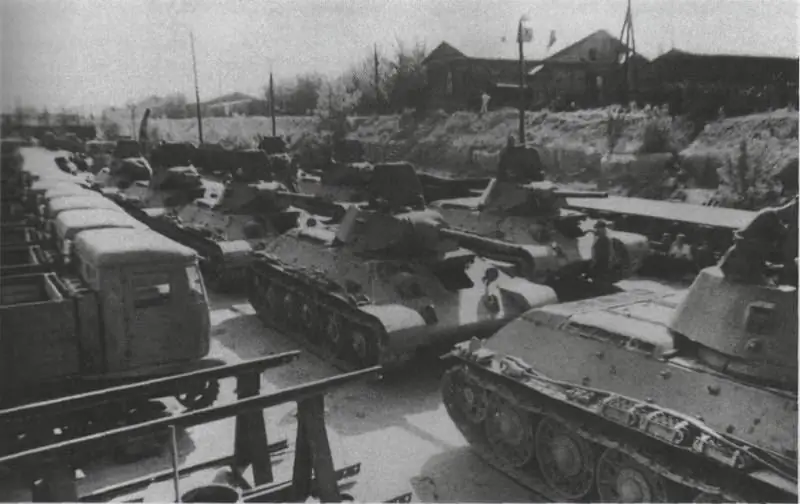
As for the rest of the factories, they were faced with an equally titanic task - they should have mastered the production of completely new equipment for them in wartime. Plant No. 112 began serial production in September 1941, the other three above-mentioned factories - in June-September 1942.
So, it is quite obvious that in such conditions all efforts should have been focused precisely on bringing the design of the T-34 to a level that would allow organizing its mass production, and not delaying this release by further complicating its design. Therefore, starting at least from the winter of 1941 (and in fact - even earlier), the designers and technologists of the plant No. 183 focused on work in the following areas:
1. The maximum possible reduction of parts that are of secondary importance in the tank, the exclusion of which should not lower the technical and combat qualities of the vehicle.
2. Reduction of the normal parts used on the tank, both in quantity and in size.
3. Reduction of places to be machined on parts, while revising the cleanliness of the parts to be machined.
4. Transition to the manufacture of parts by cold stamping and casting instead of the applied hot stamping and forging.
5. Reducing the range of parts requiring heat treatment, various types of anti-corrosion and decorative coatings or special surface treatment.
6. Reduction of assemblies and parts obtained in the order of cooperation from the outside.
7. Reduction of the range of grades and profiles of materials used for the manufacture of the tank.
8. Transfer of parts made from scarce materials to production from substitute materials.
9. Expansion, where it is allowed by operating conditions, permissible deviations from technical conditions.
So, in 1941 - 1942. amazing results have been achieved in these areas. As of January 1942, changes were made to the drawings of 770 parts, and the use of 1,265 part names was completely abandoned. It seems to be a fantastic figure, but in 1942 it was possible to exclude another 4,972 names of parts from the design of the T-34!
But simplification or the elimination of details, of course, was not enough. Technological processes also changed. So, for example, by the end of 1941, it was possible to abandon the machining of the welded edges of the armored parts. This led to the fact that the complexity of manufacturing one set has decreased from 280 to 62 machine-hours, the number of finishing jobs - by half, and the number of straightening rolls - by half.
Of course, simplifying technology was a double-edged sword. On the one hand, production was simplified and cheapened, but on the other, alas, the quality was falling: for example, the refusal of machining made increased demands on the quality of the welded seam of armored parts, etc. However, domestic designers and technologists perfectly understood these interrelationships, trying to compensate for the simplifications in the T-34 design with the latest technologies, such as the introduction of automatic welding, which was tested even before the war, but was massively introduced already in the course of hostilities. Or, for example, such as rolling measuring strips equal in width to finished parts. Often, the use of such technologies not only compensated for the simplification of the design, but also brought considerable savings in itself. So, automatic welding significantly reduced the requirements for the qualifications of workers and their labor costs, and the rental of measuring strips reduced labor costs for parts obtained from them by 36%, reduced the consumption of armor steel by 15%, and also reduced the consumption of compressed air by 15 thousand cubic meters. m. for 1,000 buildings. Of course, by drastically simplifying the design and technology of the thirty-four, it was possible to drastically reduce its cost, for example, the T-34-76 produced by plant # 183 cost:
1939 release - 596,373 rubles;
1940 release - 429,256 rubles;
1941 release - 249,256 rubles;
And, finally, 1942 - 165,810 rubles.
Alas, in all likelihood, it was not always possible to combine simplifications and technologies that compensate them in a timely manner, and it should be assumed that individual batches of T-34s produced during that period could be much more vulnerable than the "reference" tanks mod. 1940, produced before any simplifications.
Of course, in 1941-42. The USSR managed to solve the problem of explosive growth in the production of the T-34. In 1941, "thirty-fours" were produced 3 016 cars, in 1942 - 12 535 cars. The maximum monthly production of tanks of this type in 1941 was reached in May and amounted to 421 vehicles / month, and in 1942 the minimum production per month was higher and amounted to 464 tanks (in January). In December 1942, they managed to bring it up to 1,568 vehicles!
At the same time, historians rightly say that it is extremely difficult to somehow distribute this flow among tank modifications. For the Germans, everything was simple - a tank of a certain design is being produced, and let it be for itself. Then they figured out how to improve it, introduced changes - they added a letter to the name of the tank, and that's the modification. They came up with new improvements - they marked the improved car with the next letter, etc. This was not the case with the T-34 in the USSR. The fact is that constant changes in design and technology, as well as adaptation of the design of the tank to the capabilities of each specific plant led to the fact that the T-34 of the same production time, but different plants or different batches of the same plant were often far from the same machines. … Much depended on the technologies that a particular plant mastered, so, in 1942, the T-34 of plant No. 183 cost, as mentioned above, 165,810 rubles, but the T-34, produced at the "neighboring" UZTM (Chelyabinsk) - 273 800 rubles.
In other words, about the "thirty-fours" of 1941-42. release can be said not as a single T-34 tank of different modifications, but on a whole family of tanks, approximately the same performance characteristics, but having significant differences in design, constantly adapting to the equally constantly changing manufacturing technology at various factories.
Was it possible to introduce any changes in the design of the T-34 tank? Probably, it is possible, but such changes would certainly cause a decrease in output - it would take time to master them. Could we afford to reduce the production of the T-34? Recall that in 1942 we produced (without SPGs) 24,448 tanks, including:
KV of all modifications - 2 553 pcs. (10.4% of the total issue);
T-34-76 - 12 535 (51, 3%);
T-60 - 4 477 (18, 3%);
T-70 - 4 883 (20%).
As you know, even before the start of the Great Patriotic War, the leadership of the Red Army and the country understood perfectly well that tanks with bulletproof armor were categorically outdated, and if they were good for something else, then only for performing some auxiliary functions. Nevertheless, in 1942 38, 3% of all tanks produced were light T-60 and T-70 with their 15-mm sides, a crew of two and 20-mm and 45-mm guns, respectively.
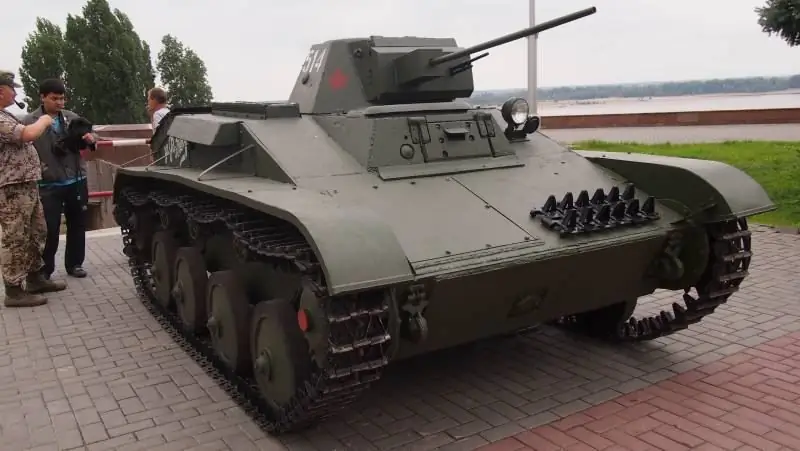
Such a flow can be explained extremely simply - the Red Army categorically lacked tanks, and any, even the most inferior tank is much better than its absence. But as a result, our army was forced to use the T-60 and T-70 as, so to speak, main battle tanks, although of course such a concept did not exist in those years. Of course, the results of the fact that at that time light armored vehicles were forced to carry out the whole range of tasks facing the tank forces of those times were extremely high losses of both the armored vehicles and its crews.
Was it possible to reduce the production of the T-34 at this time, which at that time (1941-42) still retained the title of a tank with anti-cannon armor?
Often in the comments to certain publications one has to read that, they say, the mass production of unmodernized T-34s, and even often not of the best quality, "excellent" characterizes the cannibalistic character of the then leadership of the USSR and, of course, Comrade Stalin personally. But if the production workers had taken care of the new checkpoint and the commander's cupola in time, the losses in the T-34 crews would have been much less than it actually happened.
Of course, the losses among tankers would have been less in this case. But there would be fewer tanks in the troops. And who can count how many additional riflemen, machine gunners, artillerymen and other soldiers who were left without the support of tanks as a result of reducing their production from what was actually achieved would have fallen into the ground?
Arithmetic is, in fact, nightmarish. And it is difficult to predict even now, for us, people, in the fullness of the aftermath of analyzing the events of those bloody days. And to decide what is right and what is not, in those years … Perhaps, of course, the leadership did not act quite optimally. Maybe the introduction of the same commander's turrets would not have slowed down production so much, who knows? Here you need to analyze the changes in labor intensity, as well as the capabilities of the machine park of each plant … all this is far beyond the knowledge of the author of this article. But there is no reason to doubt one thing - the stake on the all-round expansion of production of the T-34, which was made in the most difficult conditions of 1941-42. and only later, after 5 manufacturing plants reached their design capacity, the modernization of the T-34 looks quite a reasonable alternative to any other decision that could have been made at that time.