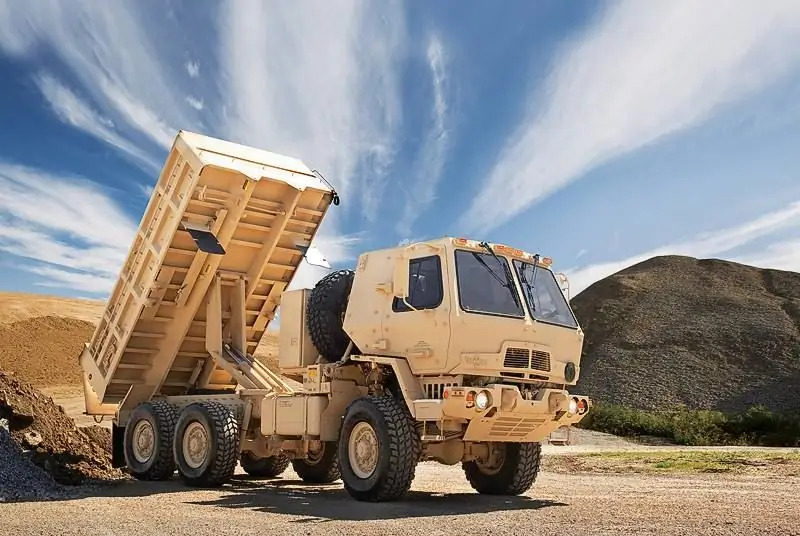
For the most part, military vehicles have remained similar to their civilian counterparts since their introduction in the First World War. In most armies, they often did not differ from commercial options, although they were painted green or sandy and had some military "options"
The paradigm has changed and quite quickly, with the result that many tactical trucks have taken on a new form. Some differences are visible to the naked eye, while others are hidden deep inside. All of them are due to the fact that many consider the new reality of hostilities, which are being conducted now and will be conducted in the future. Key changes in the design of military vehicles occur in three areas: crew protection, off-road patency, and reliability / availability.
Protection
Tactical trucks, like their civilian counterparts, have traditionally been unarmored. They were considered in the doctrine of the ground forces as support vehicles that operate behind the forward echelons. In reality, as trucks, they were never "safe" and often became targets for the enemy and took part in hostilities. The tactic of ambushing convoys became common practice and was widely used by the Viet Cong during the American invasion of Vietnam from 1965 to 1975. In operating units, trucks, as a rule, were equipped with impromptu protection. Today, increasing the level of protection of trucks has become a standard solution in many armies. The need to protect crew and cargo has been a response to the resurgence of mine warfare and the emergence of improvised explosive devices (IEDs), especially in the Iraqi and Afghan theaters of war. The blurred front line and the choice by the militants as targets of logistics and logistics units equipped with unarmored vehicles, coupled with increased sensitivity to military losses, especially among Western powers, force the military to add special protection kits for light, medium, heavy and even long-haul trucks responsible for moving goods between bases or logistics centers.
The US military, in response to massive attacks on its supply units, especially during the war in Iraq, began an accelerated program to develop and deploy cab protection kits to be fitted to existing trucks. For example, Stewart and Stevenson (currently part of BAE Systems) has developed an LSAC (Low Signature Armored Cab) armored cab for the Family of Medium Tactical Vehicles (FMTV) family of medium-duty military vehicles of the American army. In addition, armor kits were developed for the M-915 Heavy Equipment Transporter, manufactured by Oshkosh. The US Army is currently planning to equip most of its military trucks with protection kits, including bulletproof and improved mine action. Now, if you walk through all the available vehicles of the American army, it will be difficult to find an unarmored tactical truck.
Many countries followed suit, their industries taking on this task, integrating both fixed and removable protection kits into their military transport. For example, Mercedes Benz's Unimog, Zetros and Actros vehicles have standard armor protection in the form of welded steel sheets, complemented by composite panels and anti-splinters. Some armored configurations are almost indistinguishable from the non-armored version. Most often, the levels of protection provide protection against small arms and the survival of the crew when blown up by a mine or IED. Participation in the Afghan campaign forced the armies and vehicle manufacturers of many countries directly related to it to install protection kits on their military trucks, both in active units and immediately in production. Renault Trucks Defense, Iveco, Volvo, Rheinmetall-MAN Military Vehicles and many others offer armored supply trucks. In addition, Plasan, Ceradyne, QinetiQ, TenCate and others continue to develop and refine the protection solutions best suited for trucks. QinetiQ's Blast Pro additional mine protection, Blast Ride energy-absorbing seats and LAST overlay armor are designed to neutralize vehicle and crew-specific threats. Plasan has teamed up with military vehicle manufacturers Oshkosh and Tatra to create the ECP-59 Armor Protection Kit (APK) and offer it to the MTVR (Medium Tactical Vehicle Replacement) family of military vehicles, the Wrecker HEMTT (Heavy Expanded Mobility Tactical Truck) and other vehicles. The APK, which includes cab protection and cargo platform armoring, as well as suspension and air conditioning upgrades, is a typical example of such an effort.
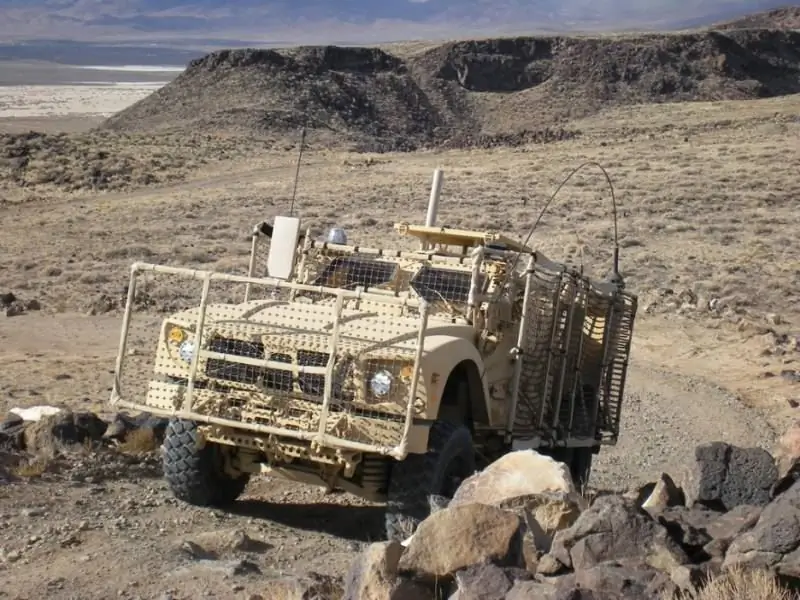
Mobility
Improving the off-road passability of military trucks through the introduction of new technologies in suspension systems has also received a lot of attention recently. The impetus for the adoption of these measures is, among other things, the increase in mass due to the installation of protection systems; for example, an ARC kit adds 3045 kg. In addition, it is highly desirable for support vehicles to travel off-road. The idea here is that off-road driving makes it difficult for the opponent to determine the traffic patterns and, as a consequence, the locations of the mines. Also being able to roam more freely means that tactical trucks can more effectively support forward ground forces. However, in this case, the risk of being attacked by the enemy increases, and this again increases the need to protect the crew.
Increased traction on soft and sandy terrain will allow you to overcome even the most difficult terrain, such as mud or sand dunes, climb grassy banks and cross water obstacles. CTIS (Central Tire Inflation System), previously considered a “nice to have” option and now standard, significantly enhances the off-road performance of military vehicles. CTIS allows the driver to inflate, deflate and adjust tire pressure to suit different loading conditions and terrain types. CTIS even allows you to continue driving with minor damage to the wheel due to the constant supply of air.
The most significant improvement in mobility has come from advances in suspension systems for wheeled vehicles. One of the first such systems to be widely installed was the TAK-4 developed by Oshkosh. Jennifer Christiansen, Vice President of Business Development at Oshkosh Defense, explained that “TAK-4 independent suspension allows for 400 mm wheel travel and, accordingly, excellent cross-country ability in areas where rough terrain and unpaved roads prevail. It also provides increased fluidity while driving, allowing soldiers to be more alert to combat missions after a long journey.”A further step forward is the intelligent independent suspension TAK-4i, developed for its JLTV (Joint Light Tactical Vehicle) armored car, which enters the US Army and Marine Corps in large quantities. In this regard, she noted that “the intelligent TAK-4i system uses high pressure nitrogen to achieve 508mm suspension travel, advanced shock absorbers, and ride height adjustable from the in-cab control panel. It allows you to increase your travel speed on rough terrain by 70 percent. TAK-4 is installed on the MTVR military truck, M-ATV (Mine-Resistant, Ambush-Protected All Terrain Vehicle - off-road vehicle with enhanced mine protection), the PLS truck (Palletized Load System - loading and unloading system using pallets) of the American Army and Logistics Vehicle System Replacement (LVSR) supply vehicles, all manufactured by Oshkosh.
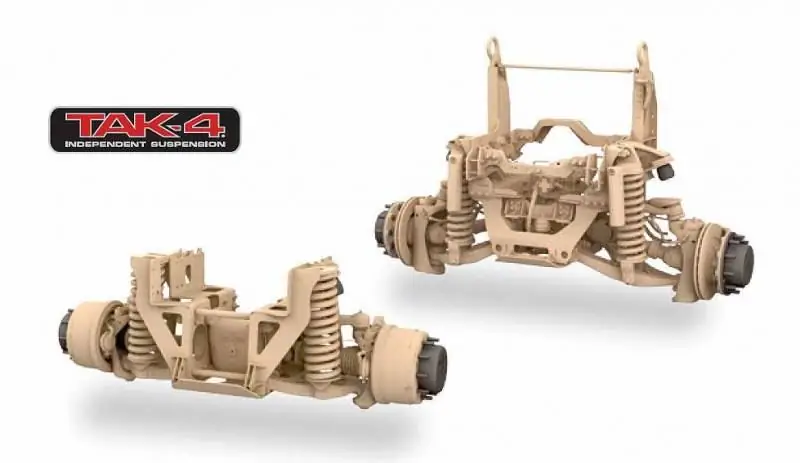
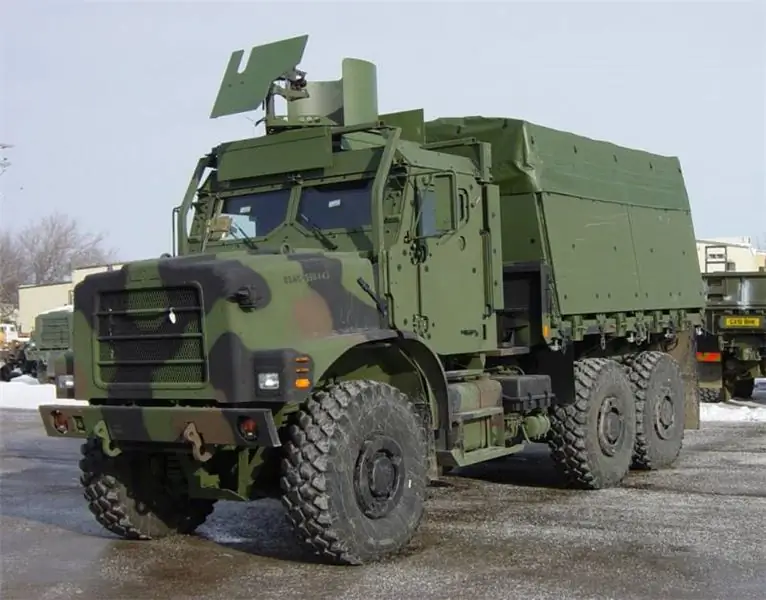
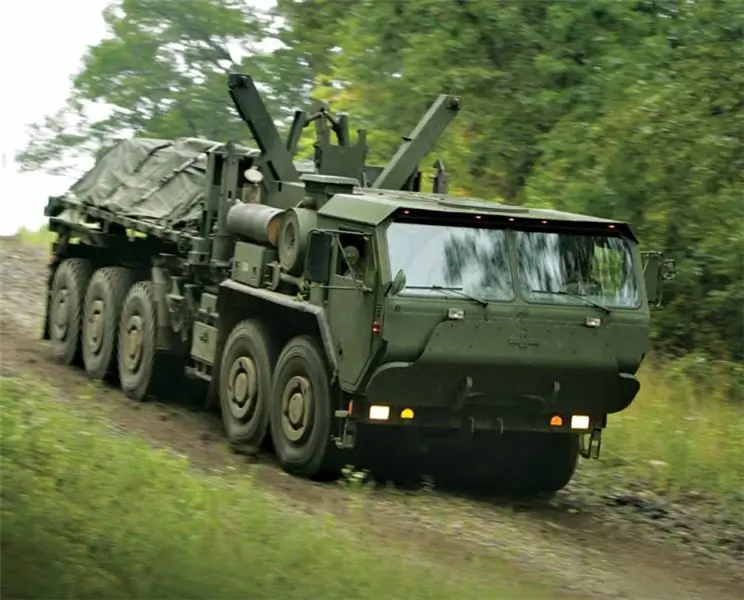
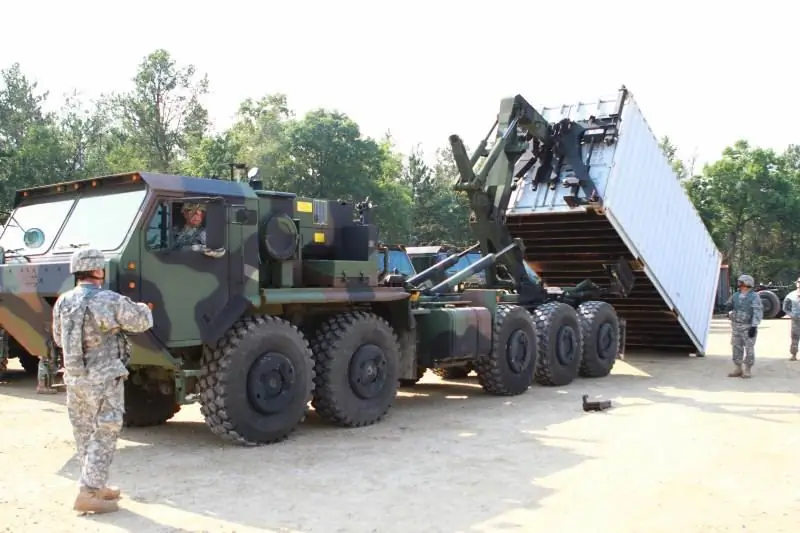
Hydropneumatic suspension offers significant advantages and is manufactured by many companies. VSE from the Netherlands has redesigned the hydropneumatic suspension and developed an advanced electro-hydraulic control of the truck's rear axles. A company spokesman said that "these systems provide additional payload, increased maneuverability and excellent wheel load distribution," adding that "our systems are already installed on more than 50,000 trucks." Hendrickson Defense manufactures a complete line of high pressure gas suspension systems, including integrated systems such as Hydro-Pneumatic Suspension, which provide ride height adjustment and superior ride comfort, ease of steering, improved stability, increased durability, whatever you need for the harsh conditions in which military transport operates. The company's systems can replace existing mechanical components and offer improved ride and stability while reducing weight by 50 percent and volume by 60 percent.
The Horstman Defense HydroStrut hydraulic shock absorber is a lightweight, structurally complete system that combines the work of a spring with a damping element. It allows you to obtain an adjustable suspension with a travel stop during reverse travel and automatic compensation for changes in spring stiffness depending on external conditions and temperature. The company's CTO Mark Bowles said that “the key characteristics of the suspension are maximum wheel travel, lightest weight and high reliability in tough operating conditions. Basically, everything revolves around the released energy and its reduction. The use of nitrogen at a very high working pressure plus the spring block results in a very compact design and the progressive spring rate reduces shock loads. This not only contributes to improved comfort for the crew, but also provides load stability and better handling. In addition to being able to tackle more difficult terrain and do it at higher speeds, these more efficient suspension systems can positively impact the reliability of other vehicle subsystems. Shock loads when driving over rough terrain are transmitted through the body of the vehicle to the crew, as well as electronics and other components, and this increases the likelihood of their failure. Reducing the frequency and magnitude of shock loads while driving will certainly increase the reliability of vehicle components and subsystems.
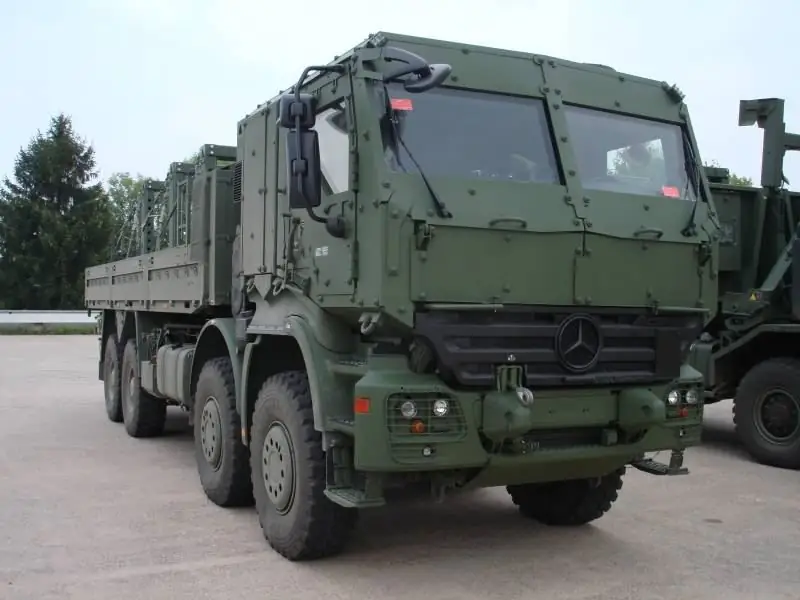
Another solution is active suspension control. For example, the ASM (Active Shock Management) system developed by General Kinetic Engineering Corporation consists of electronic controls for an adjustable damping valve and proprietary software algorithms for smooth running. ASM system allows you to upgrade existing systems; it can be applied to existing shock absorbers and dampers, after which the suspension is converted into a "semi-active" system with significantly increased efficiency. The LORD Corporation's Controllable MR Suspension uses another approach based on magnetorheological technology to move fluid in a system. These integrated units continuously respond to vehicle movements and terrain conditions, adapting the suspension to the situation in microseconds and thereby increasing dynamic stability.
Maintenance, repair, operation
The third area of increasing the efficiency of military vehicles is improving maintenance and repair and increasing reliability and operational readiness. For military equipment, especially in combat operations, “readiness” is of paramount importance. The availability of equipment ready for operation and execution of a combat mission at the very moment when it is needed can determine the completeness and success of the upcoming mission. This allows you to clearly understand the range of tasks of the department and its available resources at any time. The combination of new design approaches, innovative maintenance and repair methods and the use of some technologies, previously widely implemented and tested on commercial trucks, made it possible, even in difficult combat conditions, to raise the level of operational readiness to 90 percent or more.
The main concern of the military when a vehicle or a component breaks down is how quickly it can be repaired and returned to service. Military aviation has faced this problem for many years, since it is extremely important to keep a limited number of aircraft ready for departure at all times. To solve it, military pilots adopted a methodology for detecting faults and correcting them, the basis of which is the identification of faulty components and their immediate replacement. Combat vehicles were among the first ground platforms to adopt this approach. For example, the Kraus-Maffei Wegmann company for its Leopard-2 main battle tank and the Marder combat vehicle has developed the so-called “power unit” concept, when the engine, transmission, drives, fuel pumps and cooling system are combined in a single compact unit. Every effort has been made to simplify the connecting assemblies and elements so that you can quickly "pull" the power unit from the machine and install it back. This concept is currently being adopted for tactical trucks as well.
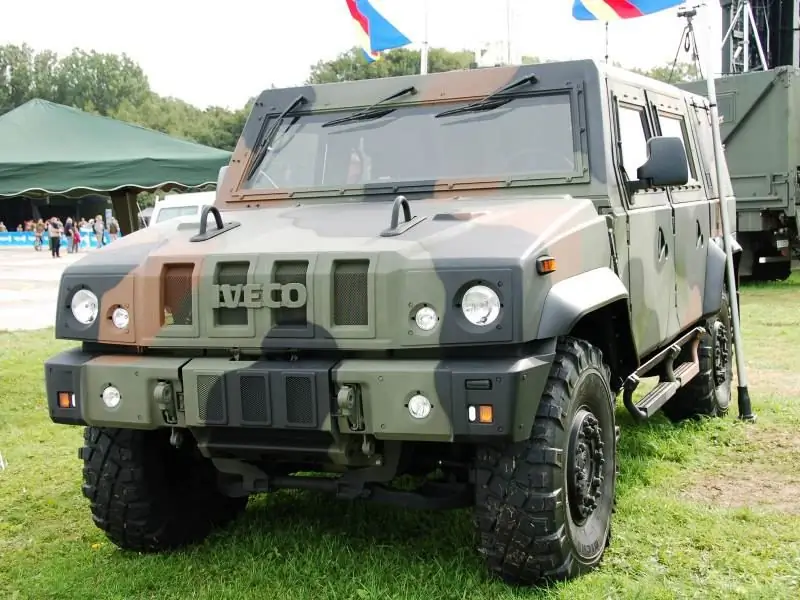
For tactical trucks, the need to not only simplify repairs and the time they take, but also the need for daily preventative maintenance is now clearly recognized. An example is Mercedes Benz's line of military trucks, which have easy-to-reach service points to simplify inspections and procedures and reduce time spent on them. All the experience gained in the operation of military equipment speaks of the great importance of preventive maintenance.
Modern technology is also providing another tool to revolutionize vehicle maintenance and repair. The system, designated VHM (Vehicle Hearth Monitoring) or Integrated VHM, uses the increased level of digitization of modern vehicle systems to collect data from sensors installed in a wide variety of locations. They collect data about all revolutions, engine, suspension travel, mileage, engine hours and so on, which are sent and stored in the HMD (Health Monitoring Unit). Then, during maintenance, this stored data can be loaded in order to obtain a near real-time "snapshot" of the utilization rate and health of each of the subsystems of the machine. The collected data can be used to estimate the wear of various subsystems and loading conditions. The wireless transmitter can automatically send and download this data even from a remote location.
The main task of the IVHM system is to determine in advance, through the use of diagnostic and prognostic methods (predictive diagnostics), possible malfunctions in order to carry out further corrective measures. Additional benefits provided by the system: increased vehicle availability through planned maintenance based on utilization and actual wear, increased reliability through better understanding of the overall condition of the vehicle and subsystems, and reduced maintenance time and costs. But by monitoring, recording and analyzing the performance characteristics, it is possible to understand what loads and stresses are acting on the machine. All of this can now be combined with location information based, for example, on GPS (Global Positioning System) in order to further assess the conditions in which the machine was operated. Bringing together all this information is possible through predictive programs, which often use accumulated technical "stories" about machines of the same model, not just to identify a broken part, but to predict the likelihood of future breakdown. This allows you to repair and replace a part or assembly in advance, while significantly reducing the likelihood of breakdown during important tasks. In addition, it improves service and repair efficiency by replacing components during scheduled maintenance, that is, before they fail.
Oshkosh's Integrated Electronic Diagnostic and Monitoring System Command Zone allows diagnosis of all major vehicle networks. A company spokesman explained that “the heart of the Command Zone system is an advanced multiplexing technology. This allows machine components to work in concert, optimize diagnostics and troubleshooting … it allows real-time access to critical information via control networks, laptop computers, on-board displays or handheld personal devices locally or remotely.” The system is installed in the JLTV armored car and can be integrated into other military vehicles.
The IVHM system is also offered by North Atlantic Industries as a "plug-in". Its IVHM-35CP0C black box is an off-the-shelf unit that can receive data from on-board sensors, “allowing technicians to plan maintenance based on actual performance and conditions, rather than when a component is already broken.” In fact, the move to an open architecture networked vehicle systems allow proactive diagnostics not only of the engine and chassis, but also of virtually any equipment on the vehicle.
Many armies understand the potential benefits of adopting IVHM systems. For tactical trucks based on commercial models such as those offered by Mercedes, DAF and Mack, IVHM and on-board diagnostic equipment are becoming standard. If this technology is widely adopted, the military can gain a number of benefits, in particular in the management of large fleets of trucks and heavy / construction equipment. Improving the operational readiness of tactical platforms (which has already been implemented in commercial vehicles) is vital and of paramount importance for the military. Anticipating problems even before they happen allows you to correct them when the system is not busy with the task, including during short pauses (waiting for cargo, unloading, loading). This allows you to maintain a high level of availability of vehicles and increase the level of confidence in them. The army gains the most important advantage in planning and conducting military operations, when often (especially in deployed troops) the amount of equipment is limited. In addition, reducing the likelihood of vehicle breakdown during operations in a hostile environment or in the immediate vicinity of battle formations makes it possible to accordingly reduce the likelihood of a rescue operation (often under enemy fire).
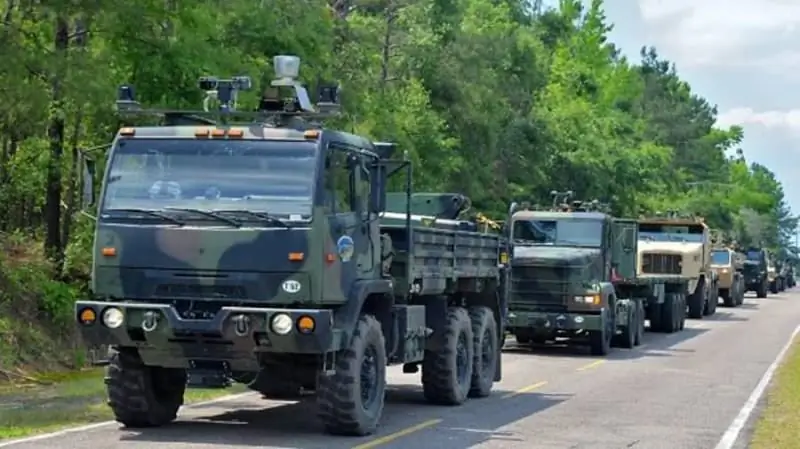
What's next?
The increase in the speed of computing and the amount of computer memory, the progress of geographic positioning and communication tools, as well as the construction of various types of networks open up new opportunities. One of the directions is the further improvement of diagnostic and prognostic tools. The ability to automatically predict component failure and report it to take preventive corrective action is clear and predictable. The failed system is identified and reported to the repair department, which orders or prepares (if available) it in order to be replaced immediately at the earliest opportunity.
Computing power, combined with fully adjustable suspension systems, which often run on high pressure nitrogen, will no doubt improve a vehicle's performance based on terrain, load and speed data. This will improve the vehicle's cross-country ability on rough terrain, take more cargo on board, increase stability and, accordingly, safety. The next step would be to convert tactical vehicles into fully autonomous unmanned systems. The US Army held several demonstrations of unmanned convoy technology in June 2016. Oshkosh Defense unveiled its own development of TerraMax unmanned vehicle technology there. The truck with integrated TerraMax technology has shown its capabilities not only as a separate system, but also as part of a column.
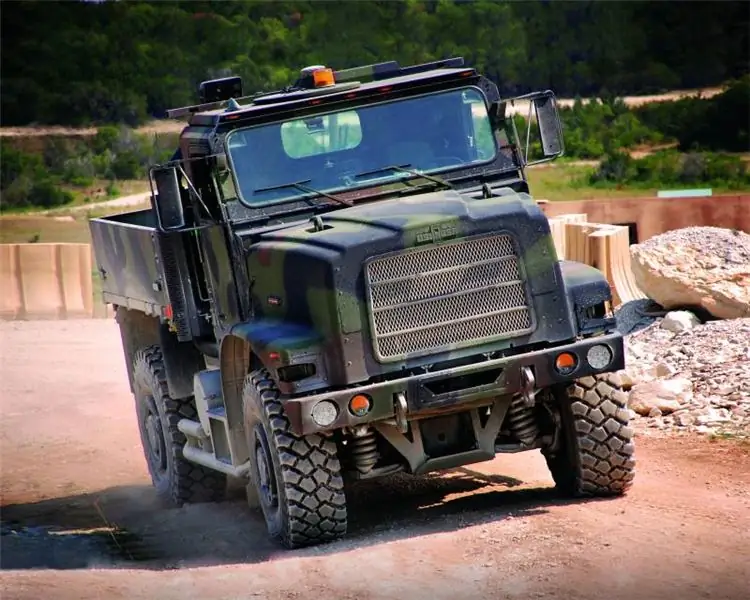
It is not yet clear when, and whether unmanned vehicles (at least supply vehicles) will become commonplace at all, but it is undoubtedly that the tactical truck is taking on a new form. While these changes remain largely invisible to the eye, the opportunities they provide to vehicles are significant. In addition, they are radically changing the way vehicles are operated and maintained. There are big changes ahead of us, and it will therefore be interesting to see how the military will react to them, whether they will ultimately perceive the benefits that will come from the introduction of these new technologies.