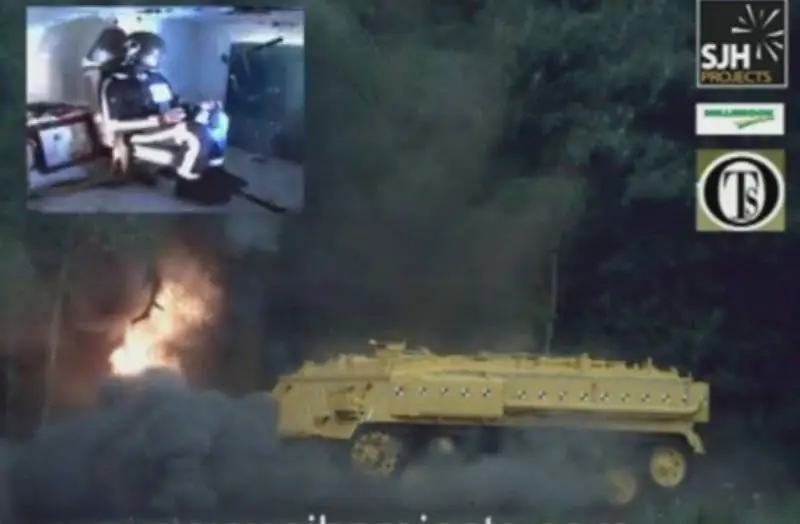
Explosive testing of the FV432 machine. Instruments can be seen flying around the dummy. This indicates the danger of loose equipment in the event of an explosion. Training significantly increases the likelihood of surviving a mine or IED detonation. At the same time, the fastening straps and the correct placement of equipment are of paramount importance, this is the basis of the soldier's safety.
Explosion-proof seats, often taken for granted, increase the survival rate of mine and IED detonations. New developments in the field of enhancing protection are considered. Explosion-dampening seats are not a new phenomenon, and Soviet-era cars were equipped with roof and side-mounted seats. But in recent years, technologies and designs have been developing especially rapidly in this area, along with the development of mine-protected vehicles, which have become commonplace on the battlefield
Until recently, all attention was undoubtedly focused on solutions to protect against mines and improvised explosive devices (IEDs) of the vehicle, and not the people inside it, since it is obvious that preventing a car from being punctured is the most important and most urgent requirement in the event of a detonation. …
The statistics of hostilities in Iraq and Afghanistan show that the vehicles have become more protected and tenacious, the number of wounded and killed for the most part has decreased. However, in fact, the number of some types of injuries has increased and the number of deaths due to secondary effects remains surprisingly high, even in cars equipped with elementary energy-absorbing seats.
One of the most important and pressing problems in this area is the so-called "tossing effect" caused by the huge negative acceleration of a car thrown into the air and then abruptly landing back on the ground.
Loss statistics are always classified, but anecdotal evidence from medical professionals in Afghanistan indicated that the number of deaths decreased, but field hospitals and main health facilities continued to provide a large amount of physiotherapy and appropriate treatment for survivors. Doctors helped the military to cope with injuries to the back, muscles and joints, which went unnoticed for some time, since the soldiers simply did not survive in such cases.
Modern explosion-proof seats are available in a wide variety of types and designs. In general, the first successful designs were standard crew seats that were attached to the sides or roof of the vehicle. They reduced the force of impact arising from the deformation of the bottom of the car and acting directly on the seated person.
In this regard, a different approach can be illustrated with the example of a seat, which is structurally a so-called Suspended Dynamic Seat, developed by Autoflug. The company has very extensive experience with parachute lines and in this design, it seeks to isolate the soldier from the blast wave and loose objects inside the vehicle by hanging the seat on tensioning belts with inertial reels. Other seats of this type also use fabric and rope bindings, as they do not transmit compressive forces, which are very well transmitted through metal.
Up to seven straps can secure the Autoflug seat, allowing freedom of movement and adjustment while protecting the soldier from direct explosion. The user is held in the seat by four-point seat belts and leg straps, which, in the event of an explosion, serve to secure the limbs moving upward, which could result in additional injury and injury.
It must be understood that seat belts are an absolutely essential part of the seat structure and if they are not comfortable or difficult to throw over body armor or equipment, soldiers will not wear them and, if detonated, will instantly lose the benefits of any explosion-proof seat.
Such suspended structures are still popular and widespread, especially in heavy vehicles, such as main battle tanks (MBT). Such cars in most cases do not get much acceleration, unless they are blown up on very large charges. The freedom of movement that they allow during normal operation can cause unusual sensations at first, since it is obvious that the controls of the machine are static, and the user can move relative to them, but the crew quickly gets used to this freedom of movement.
However, the problem becomes much more complex for smaller vehicles, where designers typically face two major challenges. Firstly, the lower mass means that the impact of the explosion is much stronger and therefore more forces must be reduced, and, secondly, being smaller, the seats must be installed on a relatively small supporting surface.
Nevertheless, a huge amount of work is underway around the world to develop the corresponding seats and the financial rewards for them are very significant due to the fact that the United States, among other countries, has a strong desire to replace all the seats of its huge fleet of armored vehicles such as HMMWVs with explosion-proof versions. This is not an easy task, according to experts, as such vehicles have limited internal volume to a certain extent, and approximately 7.5 inches of space under the seat will need to be used very effectively to provide an acceptable level of protection. However, tests carried out under this program have shown that this problem has a solution.
When the UK began to consider transferring the now ubiquitous Jackal from purely special forces to regular infantry in Afghanistan, contracts were awarded to Supacat and Jankel Armouring to address these issues on arguably the most proven type of vehicle. Jankel Managing Director Andrew Jankel said the company was initially involved only in securing reservations and wanted to buy pre-fabricated seats, but market research and experience in supplying such products (highly negative) encouraged the company to develop its own design.
These seats were designed under tight deadlines and successfully explosively tested. Under the designation JBAS (Jankel Blast Attenuating Seats) they have been approved and accepted for the company's urgent modernization program.
These were relatively simple, floor-mounted, shock-absorbed seats in which the space under the seats was used to soften upward motion and reduce the impact of the blast on the seated.
Jankel continued to develop the design leading to the Blastech family of seating in 2009. These seats are available in a variety of options with different mountings for a wide variety of vehicles. The Jackal variant, known as the F Series, has an "anti-submarine" base that prevents the seated person from slipping out from under their four-point harness; the seat is adjustable back and forth, in height and rotation. A folding seat is also available to increase the interior space in the car.
A roof or stern mount option is available under the R-series designation, primarily designed for aft seated troopers, and comes standard with a folding base. The E-series for engineering vehicles (developed for the British Talisman JCB clearing vehicle) has anti-blast protection like the rest of the seats, but this variant adds an integrated air suspension to mitigate shaking when driving on rough terrain, which these vehicles mainly operate on.
Finally, the last option is the X series, which includes several options, such as a folding backrest, large height adjustment for the stowed and firing positions, plus options for installation in the tower, stern, with attachment to the sides and bottom.
All seats generally offer the same blast protection, but are designed for different cost and weight or footprint requirements. While Jankel keeps the level of protection of the seats on offer a secret, it is clear that they can withstand peak accelerations of more than 2000 G in 2 milliseconds, transferring only a fraction of these loads to the seated person.
The blast is absorbed by a gas-filled “weakening cartridge” and rails that allow the machine to move upward in the space under the seat while the cartridge softens the shockwave to an acceptable level. Jankel's sales manager Daniel Crosby, however, said that Blastech seats are characterized by automatic weight adjustment and reset function.
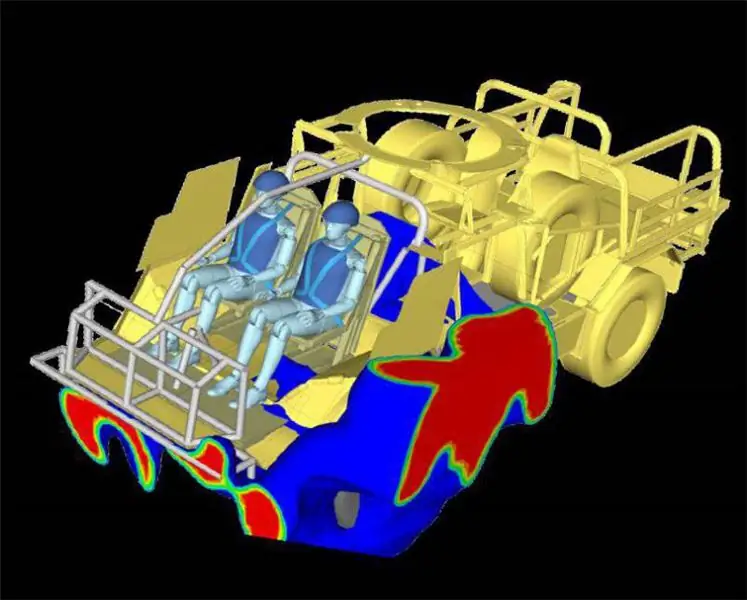
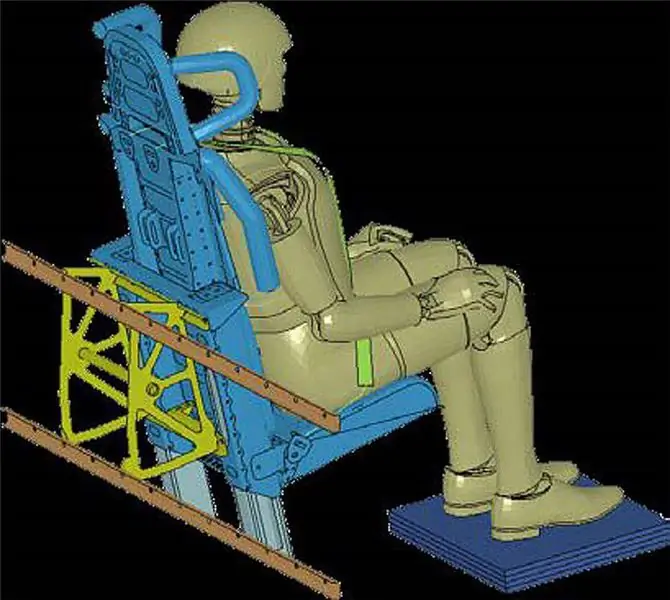
Jankel has developed advanced analytical tools to simulate the impact of an explosion on Blastech family seats; This can be seen in the example of the seats installed in the Supacat Jackal (above). The company also has its own instrumental dummies and a shock stand for confirming computer calculations.
Weight adjustment
Crosby argues that early blast seats were primarily designed for fairly large foot soldiers, but as the threat of IEDs has increased and every theater of operations now faces this threat, the one-size-fits-all approach does not justify myself. In short, soldiers with a higher mass are at risk of not getting enough protection, as the car bounces under them and the seat can roll over at the end of its stroke, while the opposite is true for lighter soldiers. Also, the size and weight of a soldier can fluctuate due to the presence of body armor, waist bags or other equipment.
To solve this problem, Blastech's seats have been fitted with automatic weight adjustment. The seated person can use the lever to set the level of reduction in the force of the impact of the shock wave that is optimal for his mass.
The reset function is a patented seat feature that absorbs upward shockwave by sliding on rails and then reloads the cushion capsule to absorb secondary throwing forces while providing protection on both axes. This actually allows for at least 160 percent of the space under the seat, Crosby said.
Seats are available with either inertial reel seat belts, four or five points, or fixed woven belts.
Jankel has carried out extensive drop tests on their seats, detaching the impact of the shockwave. They have proven to be excellent when installed on a variety of machines operating in hot spots. The company also developed advanced computer-aided testing to validate CAD models and predict weaknesses, with results Crosby assessed as very close to those of field blast tests.
The seats are reusable and contain control chips to check for damage. However, a few simple checks must be carried out daily to log into the user profile in order to ensure adequate feedback. Jankel said it has developed a number of replacement kits to repair the seats and keep them in good working order.
Another member of the blast seat market is Creation UK, whose desire to release its seat in early 2010 was very similar to that of Jankel.
CTO Robin Hall says the company was disenchanted with existing designs and manufacturers that supplied the seats for the Ranger. Creation created this car in collaboration with Universal Engineering, and then used this experience to develop its lightweight Zephyr patrol car.
“We just couldn't find a seat with the right weight and performance,” he said, adding that “the existing designs also seemed quite expensive.”
As a result, Creation began designing its own computer seat in Catia v5, based on the work done by Iliac Design on orthopedic and osteopathic seats. Davis said that the initial testing of the steel frame model during the two blast tests in accordance with STANAG 4569 Level 2 "did not match exactly" with the computer analysis, so the company is preparing its own test bench to continue the impact tests and refine them, as well as further development. and validation of the finite element method and dynamic analysis.
The final main structure is made of aluminum (to reduce weight) and uses springs, dampers and a rubber buffer to reduce the effects of an explosion. The spring and damper are off-the-shelf products, but everything else is custom made.
Hall declined to name the level of protection the seats provide, but said they passed shatter tests. The tests confirmed the calculations of the gradual failure of these seats and "it is quite clear that in the event of an explosion, the seat will fulfill its function."
He said the design is based on non-deformable parts, so it could actually be adjusted and rebuilt after “normal” use, including road accidents and “bridge jumps,” without any maintenance or repair. In the normal position, the seat is installed on the rails in the upper position of the working stroke; with a strong impact, it will slightly move along them, but then return to its original position. Hall explained that this makes it effective at exploding and being thrown hard.
The bench is reusable and, after detonation, the seat is checked with an angle gauge to ensure that the main components are not bent and otherwise maintenance-free.
The damper is structurally similar to the dampers borrowed from the suspension of road cars and "must withstand the life of the seat" without question. The seat cushions are attached with Velcro straps and are therefore easy to replace.
Hall said the seat was developed based on information from Dstl (Defense Science and Technology Laboratory), which proposed a hip support and 3-inch wide Securon four-point belts, both of which were incorporated into the design. Dstl's Steve Burgis also helped with the seat back design, which can now be used comfortably with equipment on or even removed if a soldier feels uncomfortable wearing a bulletproof vest during extended rides. Creation seats can be mounted in a wide variety of places in vehicles, in the direction of travel or perpendicular to it. Hall explained that structurally, the seats are mostly identical, but are installed in a subframe that has attachments to the bottom, sides or roof.
The development and explosive tests have now been completed.
However, if necessary, some modifications may be made in the future. For example, in theory, they could be protected by bulletproof casings if installed in an open machine, but this should not be necessary, since the machines must be sufficiently protected in any case.
Hall said the footrests could also be included in the seat. For now, he believes they are unnecessary due to the fact that the Zephyr and Ranger have double bottoms to absorb some of the shockwave energy, and that even folding structures will impair access and reduce interior space.
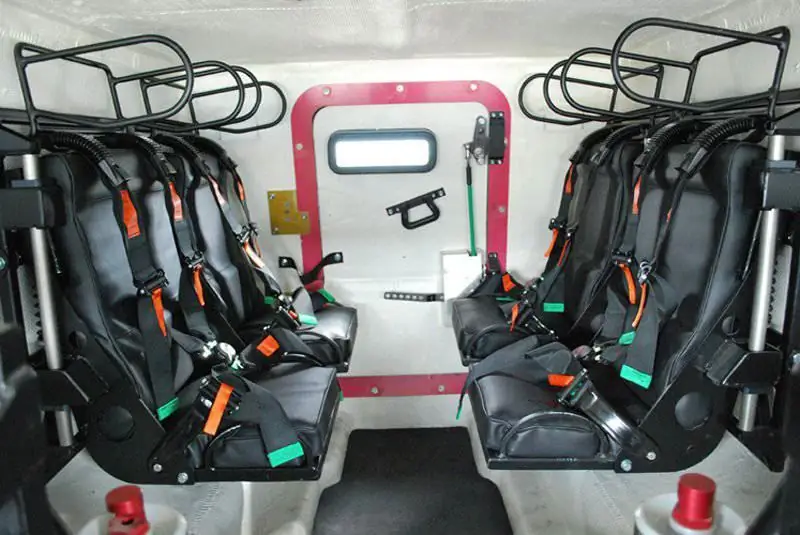
Explosion-proof seats from Creation installed in a Zephyr machine. Double bottom eliminates the need for footrests, but since they are attached to the sides, the seats have passive head restraints
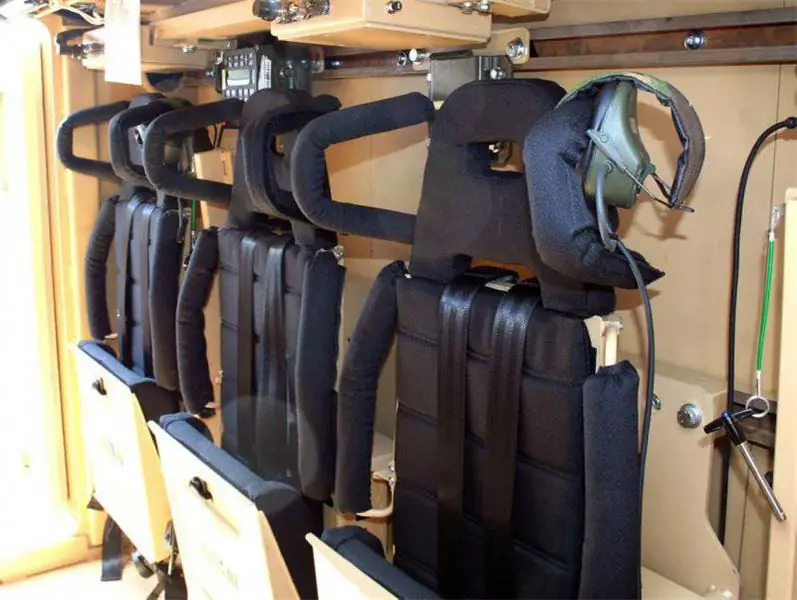
Jankel BLASTech Series Seats
Jankel seats can be equipped with footrests, but the company has also developed its J-PAD (Jankel Pulse Attenuation Device) floor panel, which is installed directly in front of the seat and absorbs shock energy that can damage the shin bones of the seated person.
David Kiernan, spokesman for US-based explosion-proof seats, Global Seating Solutions (GSS), said that “footrests are causing a lot of controversy in the industry; we have various designs and do our best to make them comfortable and efficient to use. Fixed footrests make it difficult to get on and off and can potentially injure you as they sit in the space between the footboard and the bottom. At the moment of explosion under the car, the bottom starts to move first and then the leg (foot) can be broken."
“We developed two footpegs that were well received by users. Some have folding elements, the second are triggered when detonated and remove the legs of the person sitting from the bottom. If the position, use and operation of the footrest is not properly thought out, then if the force is not applied correctly to the seated person, this can cause certain problems at the time of the explosion."
The opposite part of the person - the head also forces the development of different head restraints, although designers already offer many different head restraints to prevent unnecessary rotation of the head in the helmet during a detonation. They are especially needed for soldiers sitting perpendicular to the movement and therefore especially prone to neck, back or spine injuries, therefore the seats located at the rear are equipped with rod or hoop restraints.
The Battlesafe 208 from Australian company Stratos Seating is a good example of this rather rudimentary style of protection with its side fenders that restrict head and shoulder movement. In addition to this passive solution, at least one manufacturer on the market is known to be testing an airbag system.
Kiernan added that “active head restraints have their advantages in accidents and explosions. There are several solutions, and air bags are one of them, but here you have to deal with a rather complex problem, the sensory mechanism. Any airbag deployment at the wrong time can have serious consequences, but when operated accurately, they constitute an excellent safety system."
“There are several mechanical ways to add an active headrest to a seat assembly, which are very dependent on the actual event and the movement of the seated person within the seat,” he added. "Airbags show great potential in other areas, such as air-cushion seat belts or side impact softening seats."
GSS has several seat designs and its latest project is a family of seats with integrated five-point belts, designated XYZVR Generation II, developed in collaboration with Techno Sciences Inc (TSI). XYZVR stands for X, Y and Z protection, vibration reduction (Vibration) and rollover protection.
TSI has extensive experience in the development of aircraft seats, such as the bucket crew seats fitted to the US Navy's SH-60 Seahawk. These seats are equipped with active anti-vibration features to improve comfort. This technology, based on adaptive magnetorheological energy absorption, has been incorporated into the latest XYZVR seats.
Essentially, magnetorheological technology works in the same way as the active suspension found in some cars to get more stable motion at the touch of a button. When electric current passes through a liquid damper with metal filings, the resistance can be increased or decreased if necessary.
Kiernan explained: “Our system accepts different masses for a known shock impulse and if the impulse changes, it can change the level of protection. In the very near future, we will have a system that will adjust to the weight of the seated person, react to the acceleration of the car and minimize the vibrations of the car transmitted to the human body."
The seats are reusable and the individual seats have been subjected to multiple explosive tests. "Once activated, only one element needs to be replaced and this replacement takes very little time."
At one time they tried to introduce this technology into the EFV combat vehicles of the Marine Corps, but the program was closed. Other seats from GSS are already installed on LHTV light and heavy military vehicles and MRAP vehicles.
Despite all of this work, a source at military vehicle company Force Protection said there was tremendous room for improvement, but the vast majority of seat manufacturers do not have access to much of the data on the impact of vehicle bombings. Therefore, they independently independently investigate the direct effects on the seat and seated person.
He believes that manufacturers of vehicles and protection systems could start working closely together in the future through extensive exchange of explosive test data.
GSS's Mr Kiernan agreed, clarifying that, ideally, design should start at the user level and progress to higher levels. In the current state of affairs, they first design the car, and then install the seats in it. He said that “if we had a manufacturer who wanted to build a truck based on optimal survivability solutions, that would be great. But in reality, we are working with the space that is allocated to us and we are required to make the most efficient and safe seat within these boundaries."