It is no secret that in the modern world, the blood of the world economy is oil, the so-called black gold. Throughout the 20th and 21st centuries, it is oil that remains one of the most important minerals on the planet for mankind. In 2010, oil occupied a leading position in the world fuel and energy balance, accounting for 33.6% of total energy consumption. At the same time, oil is a non-renewable resource, and talk that sooner or later its reserves will come to an end has been going on for more than a dozen years.
According to scientists, proven oil reserves in the world will last for about 40 years, and unexplored ones for another 10-50 years. For example, in Russia, as of January 1, 2012, according to officially released information (up to this point, information on oil and gas reserves was classified), the volume of recoverable oil reserves of categories A / B / C1 was 17.8 billion tons, or 129, 9 billion barrels (according to the calculation at which one ton of export Urals oil is 7.3 barrels). Based on the existing production volumes, these explored natural resources will be enough for our country for 35 years.
At the same time, in its pure form, oil is practically not used. The main value lies in the products of its processing. Oil is a source of liquid fuels and oils, as well as a huge amount of important products for modern industry. Without fuel, not only the world economy will stop, but also any army. Cars and tanks will not go without fuel, planes will not take off into the sky. At the same time, some countries were initially deprived of their own reserves of black gold. Germany and Japan became a striking example of such countries in the 20th century, which, possessing a very meager resource base, unleashed World War II, each day of which demanded huge fuel consumption. During the Second World War, Germany to a large extent, in some years up to 50%, satisfied its fuel needs through the production of liquid fuel from coal. The way out for her was the use of synthetic fuels and oils. The same was done in the last century in South Africa, where Sasol Limited helped the South African economy to successfully operate under the pressure of international sanctions during the Apartheid years.
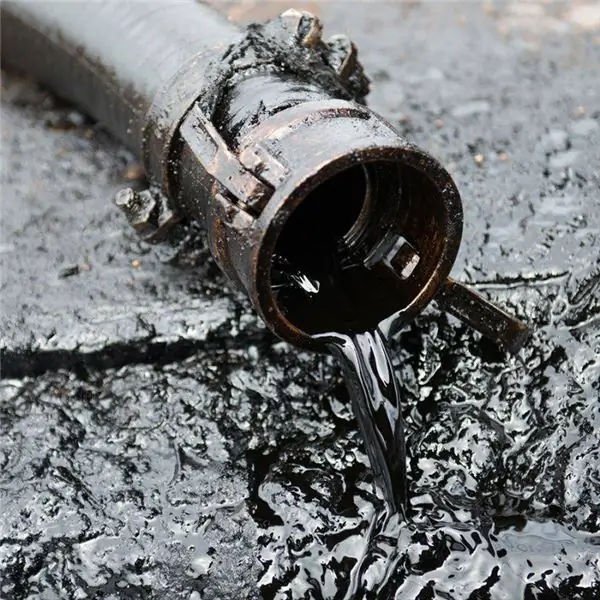
Synthetic fuels
In the 1920s, German researchers Franz Fischer and Hans Tropsch, who worked at the Kaiser Wilhelm Institute, invented a process called the Fischer-Tropsch process. Its fundamental importance was the production of synthetic hydrocarbons for their use as synthetic fuel and lubricating oil, for example, from coal. It is not surprising that this process was invented in a rather oil-poor, but at the same time, coal-rich Germany. It was widely used for industrial production of liquid synthetic fuels. Germany and Japan widely used this alternative fuel during the war years. In Germany, the annual production of synthetic fuels in 1944 reached approximately 6.5 million tons, or 124,000 barrels per day. After the end of World War II, captured German scientists continued to work in this area. In particular, in the United States, they participated in Operation Paperclip, working for the Bureau of Mines.
Beginning in the mid-1930s, the technology of gasification of condensed fuels for chemical-technological purposes began to spread in Germany, the USA, the USSR and other industrialized countries of the world, primarily for the synthesis of various chemical compounds, including artificial oils and liquid fuels. In 1935, 835 thousand tons and 150 thousand tons of synthetic gasoline were produced in Germany and England from coal, air and water, respectively. And in 1936, Adolf Hitler personally launched a new state program in Germany, which provided for the production of synthetic fuels and oils.
The very next year, Franz Fischer, together with Helmut Pichler (Hans Tropsch left Germany for the USA in 1931, where he died four years later) were able to develop a method for the synthesis of hydrocarbons at medium pressure. In their process, German scientists used catalysts based on iron compounds, a pressure of about 10 atmospheres and high temperatures. Their experiments were of great importance for the deployment in Germany of a large-tonnage chemical production of hydrocarbons. As a result of the implementation of this process, paraffins and gasoline with a high octane number were obtained as the main products. On August 13, 1938, a meeting was held in Karinhalle, the hunting estate of the Reich Aviation Minister Hermann Goering, at which a program for the development of fuel production was adopted, which received the symbol "Karinhalleplan". The choice of Goering's residence and his candidacy as the program manager was not accidental, since the Luftwaffe headed by him consumed at least a third of the fuel produced in Germany. Among other things, this plan provided for a significant development in the production of synthetic motor fuels and lubricating oils.
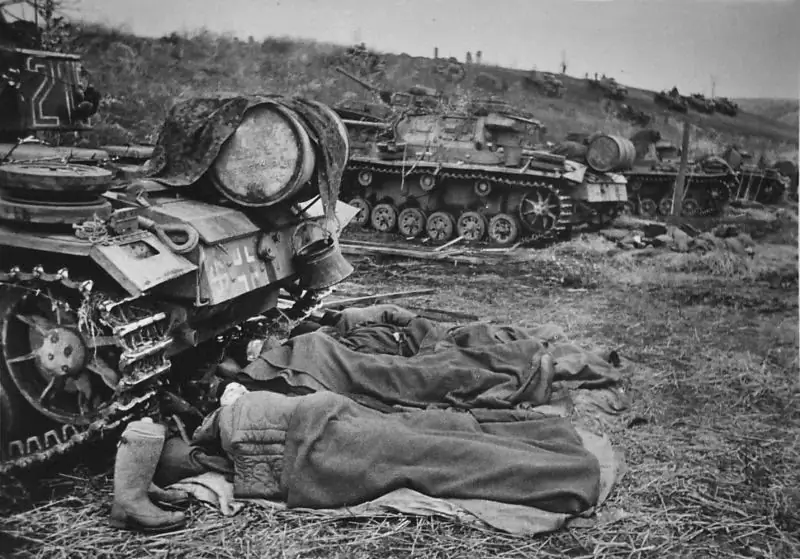
In 1939, the Fischer-Tropsch process was launched in the Reich on a commercial scale in relation to brown coal, the deposits of which were especially rich in the middle part of the country. By the beginning of 1941, the total production of synthetic fuel in Nazi Germany caught up with the production of oil fuel, and then exceeded it. In addition to synthetic fuel in the Reich, fatty acids, paraffin, and artificial fats, including edible fats, were synthesized from generator gas. So from one ton of conventional condensed fuel according to the Fischer-Tropsch method, it was possible to obtain 0.67 tons of methanol and 0.71 tons of ammonia, or 1.14 tons of alcohols and aldehydes, including higher fatty alcohols (HFA), or 0.26 tons of liquid hydrocarbons.
At the end of World War II, more than half a year from the fall of 1944, when the troops of the Red Army occupied the oil fields of Ploiesti (Romania) - the largest natural source of raw materials for the manufacture of fuel, which was controlled by Hitler, and until May 1945, the function of motor fuel in the German economy and the army performed artificial liquid fuels and generator gas. We can say that Hitler's Germany was an empire that was built on solid carbon-containing raw materials (primarily coal and to a lesser extent on ordinary wood), water and air. 100% of enriched nitric acid, which was necessary for the production of all military explosives, 99% of rubber and methanol and 85% of motor fuel were synthesized in Germany from these raw materials.
Coal gasification and hydrogenation plants were the backbone of the German economy in the 1940s. Among other things, synthetic aviation fuel, which was produced according to the Fischer-Tropsch method, covered 84.5% of all Luftwaffe's needs during the war years. During the Second World War in Nazi Germany, this method for the synthesis of diesel fuel was used at eight factories, which produced about 600 thousand tons of diesel fuel per year. Moreover, this project was fully funded by the state. The Germans built similar factories in the countries they occupied, in particular in Poland (Auschwitz), which continued to work until the 1950s inclusive. After the end of the war, all these factories in Germany were closed and partially, along with technologies, were taken out of the country at the expense of reparations from the USSR and the USA.
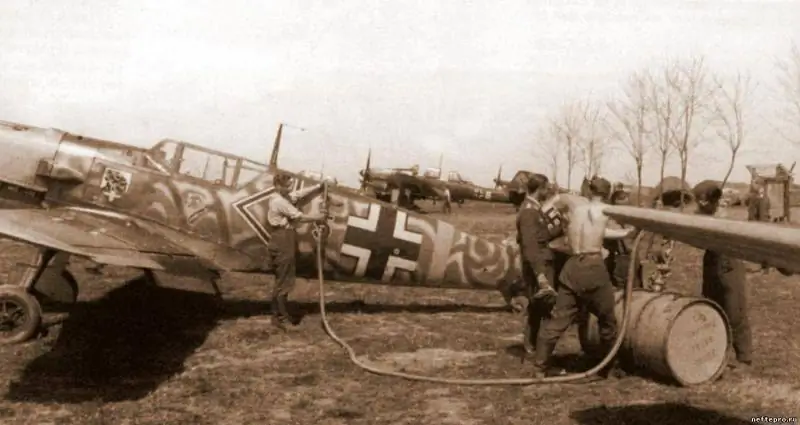
shale oil
The second source for the production of fuel, in addition to coal, is shale oil, the topic of which has not left the pages of the world press for the past few years. In the modern world, one of the most important trends observed in the oil industry is a decrease in the production of light oil and medium density oil. The reduction of proven oil reserves on the planet is forcing oil companies to work with alternative sources of hydrocarbons and to search for them. One of these sources, together with heavy oil and natural bitumen, is oil shale. The reserves of oil shale on the planet exceed the reserves of oil by an order of magnitude. Their main reserves are concentrated in the United States - about 450 trillion tons (24.7 trillion tons of shale oil). There are significant reserves in China and Brazil. Russia also possesses vast reserves, which contain about 7% of the world's reserves. In the United States, shale oil production began in the late 1940s and early 1950s using the mine method. For the most part, the extraction was experimental and carried out on a meager scale.
Today in the world there are two main ways of obtaining the required raw material from oil shale. The first of them involves the extraction of shale rock by the open or mine method, followed by processing in special installations-reactors, in which the shale is subject to pyrolysis without air access. In the course of these operations, shale tar is obtained from the rock. This method was actively tried to develop in the Soviet Union. Similar projects are also known for the extraction of shale at the Irati field in Brazil and in the Chinese province of Fushun. In general, both in the 40s of the XX century, and now the method of shale extraction with their subsequent processing remains a rather costly method, and the cost of the final product remains high. In 2005 prices, the cost of a barrel of such oil was $ 75- $ 90 at the output.
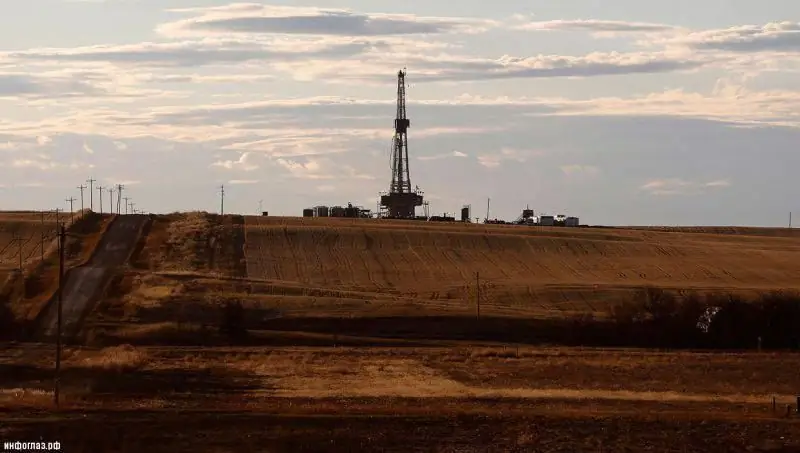
The second method of extracting shale oil involves extracting it directly from the reservoir. It is this method that has developed in the United States over the past few years and has made it possible to talk about a "shale revolution" in oil production. This method involves drilling horizontal wells followed by multiple hydraulic fracturing. In this case, it is often required to carry out chemical or thermal heating of the formation. It is also obvious that such a mining method is much more complicated, and therefore more expensive than the traditional mining method, regardless of the technologies used and progress in the scientific field. So far, the cost of shale oil is significantly higher than conventional oil. According to the estimates of the oil producing companies themselves, its production remains profitable with the minimum oil prices on the world market above $ 50-60 per barrel. Moreover, both methods have certain significant disadvantages.
For example, the first method with open-pit or mine mining of oil shale and their subsequent processing is significantly constrained by the need to utilize huge amounts of carbon dioxide - CO2, which is formed in the process of extracting shale tar from it. Finally, the problem of utilizing carbon dioxide has not yet been resolved, and its emissions into the earth's atmosphere are fraught with serious environmental problems. At the same time, when shale oil is extracted directly from reservoirs, another problem arises. This is a high rate of decline in the flow rate of the wells put into operation. At the initial stage of operation, the wells, due to multiple hydraulic fracturing and horizontal injection, are characterized by very high production rates. However, after about 400 days of work, the volume of the extracted products decreases sharply (up to 80%). In order to compensate for such a sharp drop and somehow level out the production profile, wells in such shale fields must be put into operation in stages.
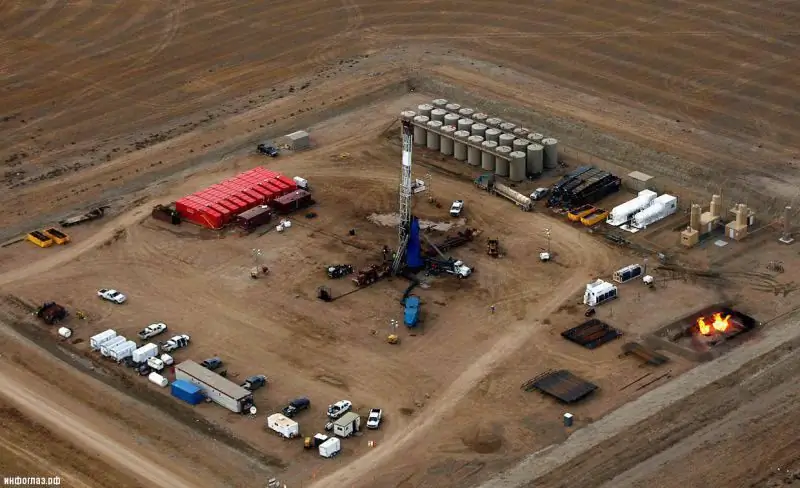
At the same time, technologies such as horizontal drilling and hydraulic fracturing have allowed the United States to increase oil production by more than 60% since 2010, bringing it to 9 million barrels per day. Currently, one of the most successful examples of the use of shale oil production technologies is the Bakken field, located in the states of North and South Dakota. The development of this particular shale oil field has created a kind of euphoria in the North American market. Just 5 years ago, oil production at this field did not exceed 60 thousand barrels per day, and now it is already 500 thousand barrels. As geological exploration was carried out here, the oil reserves of the field increased from 150 million to 11 billion barrels. In addition to this oil field, shale oil production in the United States is being conducted at the Bone Springs in New Mexico, Eagle Ford in Texas and Three Forks in North Dakota.