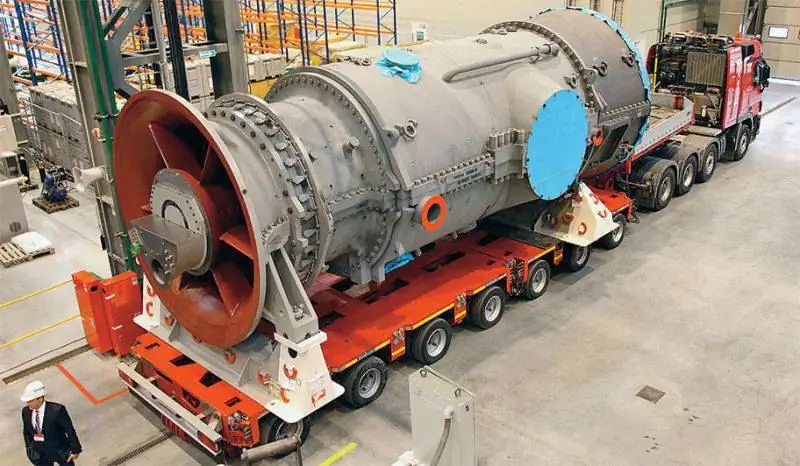
Russia has neglected the development of its own energy gas turbine building, now it is important to accumulate high-tech competencies at factories built in the country by foreign companies
On June 18, at the site of the Greenstate industrial park in Gorelovo, in the south of St. Petersburg, a ceremony was held to launch the Siemens Gas Turbine Technologies (STGT) plant - a joint venture between Siemens and Power Machines, timed to coincide with the opening of the St. Petersburg Economic Forum. The importance of the event was emphasized by the presence of high-ranking officials - the Russian side, in particular, was represented by the speaker of the State Duma Sergei Naryshkin and the governor of the Leningrad region Alexander Drozdenko, the German side - by Siemens AG board member Siegfried Russvurm. However, the participation of the head of the Russian parliamentary corps, judging by his speech at the opening with a noticeable anti-American rhetoric, should have rather emphasized a simple thesis: despite the sanctions, cooperation in the field of high-tech with European countries and companies continues. The project itself, the speakers argued (among whom the Russian side was represented by the First Deputy Energy Minister Alexei Teksler, and the General Director of OJSC Power Machines, Roman Filippov), will help accelerate the modernization of the domestic energy sector, as well as strengthen economic ties between the countries in difficult political conditions.
Lost leadership
Undoubtedly, the opening of such a plant is another step in the development of high-tech production in Russia. And this news is from the category of very good. Gas turbines will be produced in Gorelovo - high-tech power equipment, justifiably considered the pinnacle of the power machine-building high-tech, and the plant itself, which currently employs about 300 specialists, is equipped with modern equipment, including unique machines for plasma spraying of turbine parts, laser welding and water-jet cutting. Siemens has only three similar enterprises and engineering departments for the production of high-power gas turbines in the world: in Berlin, German Mülheim and American Charlotte.
The product line of the St. Petersburg joint venture includes two gas turbines with a capacity of 172 and 307 MW, but later the site can also be used for assembling gas turbines of lower capacity. Here, work will be organized on the piping, assembly and packaging of centrifugal compressor equipment intended for the transportation of natural gas, and in the future they will begin to manufacture the compressor modules themselves. But now we are not talking about superchargers. It is important for us to be able to produce specifically high-power gas turbines, albeit under the Siemens trademark. And that's why.
Power engineering (EMC) and electrical engineering are high-tech sectors of the real economy, testifying to the technological viability of any state. Gas turbine engineering is the industry pinnacle of power engineering, which keeps the entire production and innovation sphere in good shape. Until relatively recently, only a limited number of states possessed their own EMC, and even a smaller number of initiates had developed gas turbine engineering, including both energy and aircraft and ship engines; almost until the end of the 20th century, their number in the world did not exceed a dozen: Great Britain, Germany, Italy, USSR / Russia, USA, Switzerland, Sweden, France, Japan. Later, the pool of countries producing such equipment was replenished by developing countries (primarily, of course, about China). But we took a peculiar path in this area of technology as well.
It so happened that the USSR, having been from the beginning of the 70s of the last century in the role of the undisputed technological leader of the power gas turbine construction (then at the Leningrad Metal Plant, the world's first serial machines with a capacity of 100 MW were produced), already in the 80s began to lose ground. This happened primarily due to the fact that the country moved towards powerful nuclear, hydro and thermal power plants, and subsequent difficult attempts to create 150 megawatt gas turbines at the LMZ were simply lost in the grandeur of the Soviet energy swing. Cheap energy resources finished off the trend of abandoning the resource-saving gas turbine and combined cycle technology, as a result, the Soviet Union (and after its collapse, Russia) was left without its spent large-capacity gas turbine plant.
By the end of the first decade of the 21st century, the only gas turbine that, with an eye to the history of the issue (the roots of the turbine go back to the naval developments of the Soviet era, and it was designed at the Zarya-Mashproekt design bureau in the Ukrainian Nikolaev), was GTU-110, which, with the support of Anatoly Chubais, was perfected at the Rybinsk NPO Saturn, but it was never completed, and now out of five such turbines installed at two stations in Ivanovo and Ryazan, only one worked last year. After the closure of RAO UES and the departure from Saturn in 2010 of an ardent supporter of the development of the general director of the enterprise, Yuri Lastochkin, its improvement, in fact, stopped (for more details see "We need a national gas turbine project" in Expert No. 11, 2010). Representatives of the current owners of the Rybinsk enterprise, the United Motor Corporation (UEC), do not speak clearly and publicly about the continuation of this work. On the other hand, UEC, together with the state-owned company Inter RAO UES, created a joint venture in 2011 in the same place, in Rybinsk, in order to build a gas turbine plant, which is competitive with Saturn, in partnership with General Electric. Now the assembly of the first two gas turbine units with a capacity of 77 MW is underway on the order of Rosneft.
The market is completed. Are the technologies adopted?
GTU and CCGT (combined cycle plant) are still the main abbreviations for our power industry. The fuel balance of power plants is now dominated by gas - it produces, according to the Ministry of Energy last year, over 44% of Russian electricity. The modernization of gas-fired thermal power plants and their transfer from a steam-power cycle to a steam-gas cycle could save up to a quarter of those 160-odd billion cubic meters of natural gas, which is mostly burned in boilers of condensing power plants with 38% efficiency, at best. CCGT is a much more efficient instrument for using gas. In the best modern models of CCGT, built on the basis of those turbines that are planned to be produced at the plant in Gorelovo, the efficiency reaches 60%.
In the past five years, the power supply gas turbine market, thanks to capacity supply agreements (CDAs were invented during the Chubais industry reform to ensure that the state will reimburse the investor for funds invested in the construction and partly in the modernization of plants with an increase in capacity) - the fastest growing in terms of demand for equipment segment of new power plants. In 2014 alone, at the expense of CCGT in the country, more than 3.2 GW of new capacities were commissioned at large TPPs that are part of the Unified Energy System of Russia. However, almost all of this market is left to the mercy of foreign manufacturers, primarily Siemens and General Electric.
Only Siemens SGT5-4000F with a capacity from 270 to 285 MW (modern version 307 MW) - these are the ones that are supposed to be assembled in Gorelovo - eleven units are already in operation in Russia, and seven more projects are at different stages of implementation. This means that Siemens has supplied equipment to Russia for a CCGT unit, the installed capacity of which is approaching 7.5 GW, which is more than the country launched nuclear power units for the entire post-Soviet period! According to the company itself, the total capacity of Siemens gas turbines made using Siemens technology, including small and medium-sized machines sold in Russia, exceeds 13 GW. General Electric lags behind Siemens in terms of installed capacity, but this company also accounts for gigawatts in deliveries (the author of these lines counted more than 20 turbines from 77 to 256 MW with a total capacity of about 2 GW, installed by GE at Russian TPPs only in 2010-2012).
For the Russian energy sector, the supply of gas turbine units by these companies is a gratifying fact, these are excellent machines. But the domestic engineering industry has lost billions of dollars due to the government's reluctance to really invest in such an important segment of technology. So, according to estimates, only about $ 20 million was spent on the development of the GTE-110 project, and in the United States, the Department of Energy invested more than a billion dollars on the development and fine-tuning of some H-class turbines in the 2000s (and not only in GE, but and the current gas turbine division of Westinghouse, owned by Siemens).
There is still some positive experience in technology transfer in the industry. In 1991, the Leningrad Metal Plant (now a branch of Power Machines) organized, together with Siemens, the Interturbo JV. The enterprise produced 19 V94.2 machines under the Siemens brand, which were sold to nine countries of the world, including Russia. In 2001, Power Machines bought a license to produce V94.2 under its own brand name GTE-160 (a total of 35 such machines were produced, of which 31 were for Russian consumers). The share of domestic components in installations reached 60%, but critical units - components of the hot section, broaching grooves in discs, electronic part of the control system, gas fuel block - remained in the area of responsibility of Siemens.
Goodwill localization
At the peak of its success, Power Machines developed the GT-65 unit, relying on it and the CCGT on its basis to replace numerous obsolete steam turbines with a capacity of up to 110 MW. Mosenergo, which supported the project, was soon eliminated - why risk sponsoring the expensive development and fine-tuning of a Russian gas turbine, when you can buy a finished foreign turbine and still get a refund for it under CDA agreements. In 2011, Power Machines, in fact, abandoned the independent development of this subject, transferring the SKB of gas turbines, which had been working at LMZ since 1956, to the new Siemens Gas Turbine Technologies, which acquired Interturbo, and the assets in the joint venture redistributed in favor of Siemens (65%).
The first turbine SGT5-2000E has already been assembled at the newly opened plant; the share of domestic suppliers in it is still about 12% at cost price. But, according to the general director of STGT, Niko Petzold, the company intends to increase it to 70% in accordance with the targets set by the Russian government. According to him, several Russian companies are now being considered and are undergoing appropriate certification. There are no direct binding documents prescribing a localization program, but the demand from state-owned companies often already requires a certain degree of product localization. Therefore, says the top manager, only by expanding the range and improving the quality of localization, it is possible to gain wider access to the rather competitive Russian market of gas turbine products.
In particular, at the OMZ Spetsstal plant, says Alexander Lebedev, CTGT technical director, rotor parts for the next turbine - rotor discs, end parts (total 28 components) - have already been manufactured from a batch of forgings in the process of supplier certification. And this is a very responsible product, often coming from abroad.
The share of Russian manufacturers, including the supply of high-tech components through their gradual certification in accordance with Siemens standards, will gradually increase. Domestic components will also be used in turbines intended for foreign markets.