Currently, the leading armies of the world have begun implementing programs for the development of new types of small arms (Ratnik in Russia and NGSAR in the United States). As more than a century of experience in the development of unitary cartridges, and then intermediate and low-impulse cartridges, shows, the most promising solution is the advanced development of new types of ammunition.
Following the results of World War II, it was concluded that it was necessary to improve the design of the most consumable type of ammunition (cartridges for automatic small arms) and expand the resource base for their production.
Cartridges with metal sleeves
The saturation of infantry units with automatic weapons in the defense industry has caused a shortage of copper, traditionally used in cartridge brass (used to make cartridge cases) and tombak (used to make bullet casings).
The most effective solution to the problem of resource scarcity was the use of mild steel, coated on both sides with copper for protection against corrosion, or uncoated, used in wartime for the production of so-called surrogate liners. In the post-war period, the technology of coating steel sleeves with a special varnish was mastered, which protected them from moisture and reduced friction in the chamber (up to a certain temperature limit).
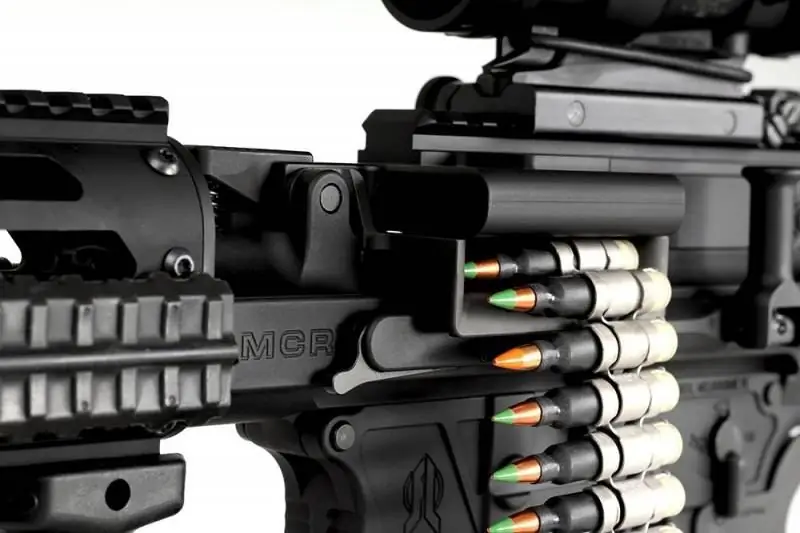
Despite the similar technical characteristics of mild steel and copper alloys, the latter have advantages in ductility and corrosion resistance. The lacquer coating of steel sleeves has low wear resistance and, in the process of reloading, upon contact with metal parts of the weapon, tends to be damaged and transferred to the elements of automation, disabling them. If unused cartridges are removed from the barrel after the end of firing, their casings are deprived of the lacquer coating due to its burnout upon contact with the heated surface of the chamber, after which they are accelerated oxidized and the cartridges become unusable.
The increased consumption of cartridges by infantrymen armed with automatic weapons served as the basis for an increase in wearable ammunition by reducing the weight of cartridges. Until the early 1970s, the main direction of reducing the weight of the wearable ammunition was the transition first to intermediate, and then to low-impulse cartridges, due to the desire to increase the accuracy of automatic fire from awkward positions. After the adoption of the AK-74 assault rifle and the M-16 automatic rifle, this reserve for reducing the weight of the wearable ammunition was exhausted - an attempt to use lighter swept bullets revealed their increased wind drift.
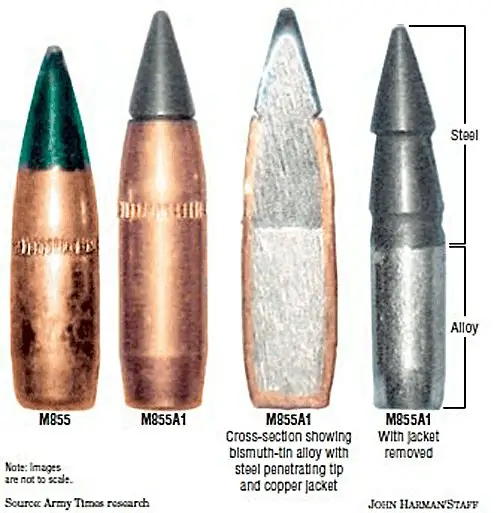
At present, bullets with a steel core, a lead jacket and a tompak jacket are mainly used as striking elements. In order to increase armor penetration, the US Army switched to the use of all-metal bullets of M80A1 EPR and M855A1 cartridges without a lead jacket, consisting of a tombak shell and a core with a steel head and a bismuth tail.
Caseless cartridges
In the 1980s, in the USSR and NATO countries, an attempt was made to radically solve the problems of the high material consumption of classic cartridges by switching to caseless ammunition. The greatest progress in this direction was achieved by the German company Heckler und Koch, which created the HK G11 automatic rifle, using caseless DM11 cartridges developed by Dynamit Nobel.
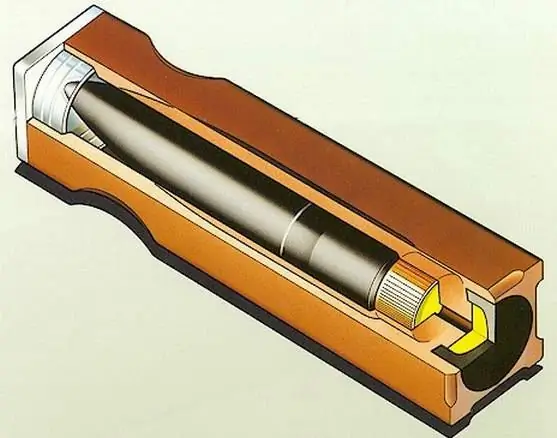
However, the military operation of a series of 1000 HK G11 rifles in the FRG border service demonstrated their danger to servicemen due to the regular spontaneous combustion of caseless cartridges in the chamber, despite its structural separation from the rifle barrel. As a result, the German border guards were first banned from using the automatic mode of firing, and then the HK G11 was completely removed from service due to the senselessness of its use as a purely self-loading weapon in the presence of overcomplicated automation ("cuckoo clock").
Cartridges with plastic sleeves
The next attempt to reduce the material consumption of small arms ammunition and increase wearable ammunition was carried out in the 2000s in the United States by AAI (now Textron Systems, a production division of Textron Corporation) as part of the LSAT (Lightweight Small Arms Technologies) program, which led to the creation of a light machine gun and an automatic carbine, designed for combined ammunition with cartridges with a brass sleeve, a plastic sleeve and caseless, made in a telescopic form factor.
Caseless cartridges, as expected, were noted for spontaneous combustion in the barrel chamber, despite its detachable design, so the choice in the LSAT program was made in favor of cartridges with a plastic sleeve. However, the desire to reduce the cost of ammunition led to the wrong choice of the type of plastic: polyamide was used as such, which has all the necessary characteristics, except for one, but the most important - its maximum operating temperature does not exceed 250 degrees Celsius.
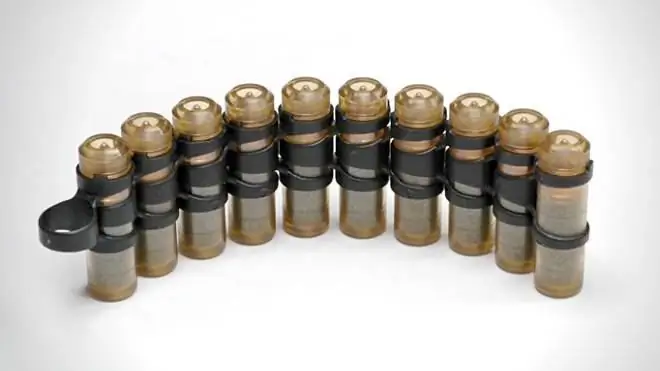
Back in the 1950s, based on the results of field tests, it was determined that the barrel of the DP machine gun in conditions of continuous firing in bursts with interruptions for changing stores heats up to the following values:
150 shots - 210 ° C
200 shots - 360 ° C
300 shots - 440 ° C
400 shots - 520 ° C
In other words, in conditions of intense combat, after using up the first two hundred rounds of cartridges, the barrel of a light machine gun is guaranteed to reach the melting point of polyamide.
In connection with this circumstance, the LSAT program was closed in 2016 and the CTSAS (Cased Telescoped Small Arms Systems) program was launched on its basis with the aim of developing telescopic cartridges on a new material basis. According to an interview with the US Army Program Administrator Corey Phillips given to thefirearmblog.com in March 2017, the most heat-resistant engineering polymer to date, polyimide, was selected as the material for the plastic liners, with a maximum operating temperature of 400 ° C.
Polyimide as the material of the cartridge case also has another valuable property - when heated above the specified level, it charred without melting with the release of volatile substances that do not contaminate the barrel chamber, while the charred surface of the cartridge case serves as an excellent antifriction material when it is extracted after a shot. The strength of the liner rim is provided by a metal flange.
A temperature of 400 degrees is the permissible limit for heating small arms barrels, after which they warp, since the temperature of the technological tempering of the barrels is from 415 to 430 degrees. However, the tensile strength of polyimide at a temperature of 300 degrees or more drops to 30 MPa, which corresponds to a pressure in the chamber of 300 atmospheres, i.e. an order of magnitude less than the maximum level of pressure of powder gases in modern models of small arms. When trying to remove the spent cartridge case from the chamber of the classical design, the metal flange will tear off with the ramrod knocking out the remains of the cartridge case from the barrel.
The heating of the cartridge in the chamber of the classical design can be controlled to a certain extent by firing from an open bolt (machine guns), but in the case of intense firing and firing from a closed bolt (machine guns and automatic rifles), heating the cartridge over 400 degrees is almost inevitable.
Cartridges with aluminum sleeves
Another alternative to copper alloys is aluminum alloys used in the casings of serial pistol cartridges, in experimental development of rifle cartridges and in serial shots for the 30-mm GAU-8A automatic cannon. Replacing copper with aluminum allows you to remove the restriction on the resource base, reduce the cost of the cartridge case, reduce the weight of the ammunition by 25 percent and, accordingly, increase the wearable ammunition load.
In 1962, TsNIITOCHMASH developed experimental cartridges of 7, 62x39 mm caliber with an aluminum alloy sleeve (code GA). The liners had an antifriction graphite coating. In order to prevent electrochemical corrosion, the capsule cup was made of an aluminum alloy.
However, the use of such sleeves is hindered by their only negative property - spontaneous ignition of aluminum and its alloys in air when heated to 430 ° C. The heat of combustion of aluminum is very high and amounts to 30.8 MJ / kg. The outer surface of products is subject to spontaneous combustion when heated to a specified temperature and an increase in the permeability of the oxide film for oxygen in the air or when heated to a lower temperature in the event of damage to the oxide film. A nonplastic ceramic oxide film (thickness ~ 0.005 microns) is destroyed when a plastic metal sleeve is deformed under the action of the pressure of propellant gases, the permeability of the oxide film is achieved as a result of heating during intense firing. Liners spontaneously ignite only in air after extraction from the barrel, where a negative oxygen balance is maintained during the combustion of the powder.
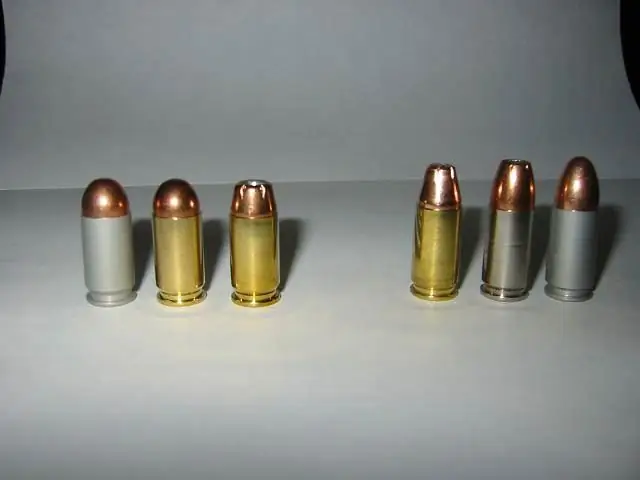
Therefore, aluminum casings have become widespread only as part of pistol cartridges of calibers 9x18 PM and 9x19 Para, the intensity of fire of which and the temperature reached in the chamber cannot be compared with these indicators of machine guns, automatic rifles and machine guns.
Aluminum was also used in the 6x45 SAW Long prototype cartridge, the sleeve of which was equipped with an elastic silicone liner that tightens cracks in the metal and oxide film. However, this decision led to an increase in the linear dimensions of the cartridge, the associated dimensions of the receiver and, accordingly, the weight of the weapon.
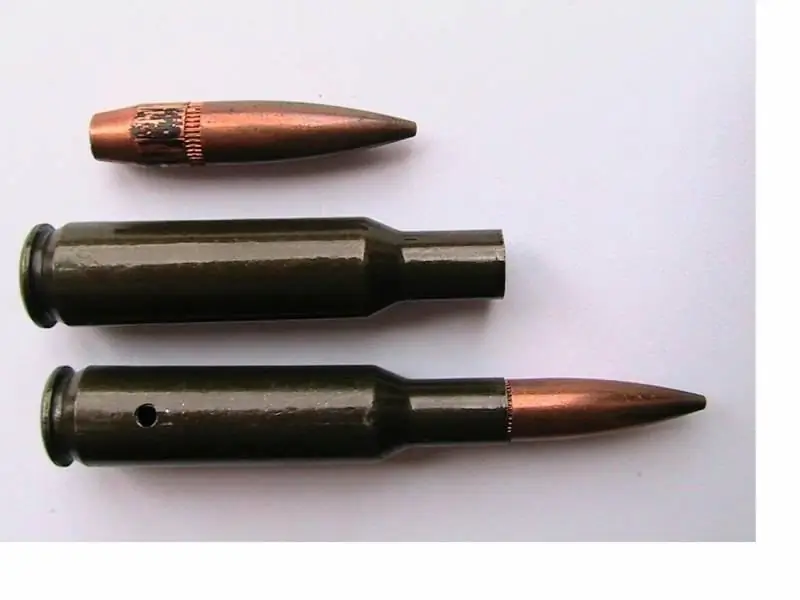
Another solution, but brought into service, is a 30-mm artillery round 30x173 GAU with an aluminum alloy sleeve. This became possible due to the use of a special low-molecular "cold" propellant charge. The thermochemical potential of the powder is directly proportional to the combustion temperature and inversely proportional to the molecular weight of the combustion products. Classic nitrocellulose and pyroxylinic propellants have a molecular weight of 25 and a combustion temperature of 3000-3500 K, and the molecular weight of the new propellant was 17 at a combustion temperature of 2000-2400 K at the same impulse.
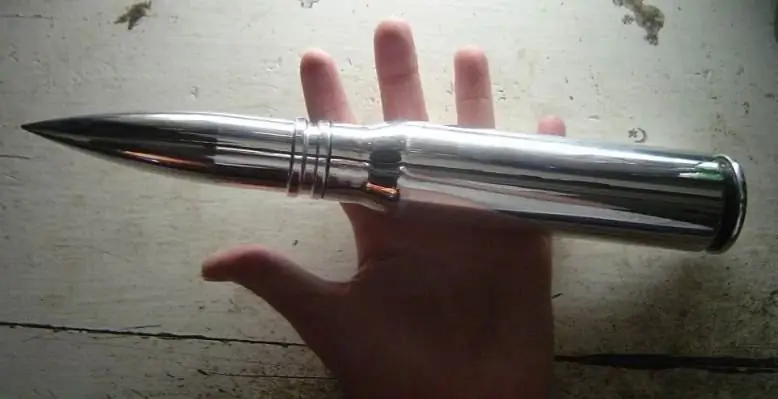
Promising sintered metal sleeve
The positive experience of using artillery shots with an aluminum sleeve makes it possible to consider this metal as a structural material for small arms cartridge cases (even without a special propellant composition). In order to confirm the correctness of the specified choice, it is advisable to compare the characteristics of brass and aluminum alloy liners.
Brass L68 contains 68 percent copper and 32 percent zinc. Its density is 8.5 g / cm3, hardness - 150 MPa, tensile strength at 20 ° C - 400 MPa, tensile elongation - 50 percent, sliding friction coefficient on steel - 0.18, melting point - 938 ° C, temperature zone of brittleness - from 300 to 700 ° C.
As a replacement for brass, it is proposed to use aluminum alloyed with magnesium, nickel and other chemical elements in a volume fraction of not more than 3% in order to increase the elastic, thermal and casting properties without affecting the resistance of the alloy against corrosion and cracking under load. The strength of the alloy is achieved by reinforcing it with dispersed aluminum oxide fibers (diameter ~ 1 μm) in a volume fraction of 20%. Protection against surface self-ignition is provided by replacing the brittle oxide film with a plastic copper / brass coating (~ 5 μm thick) applied by electrolysis.
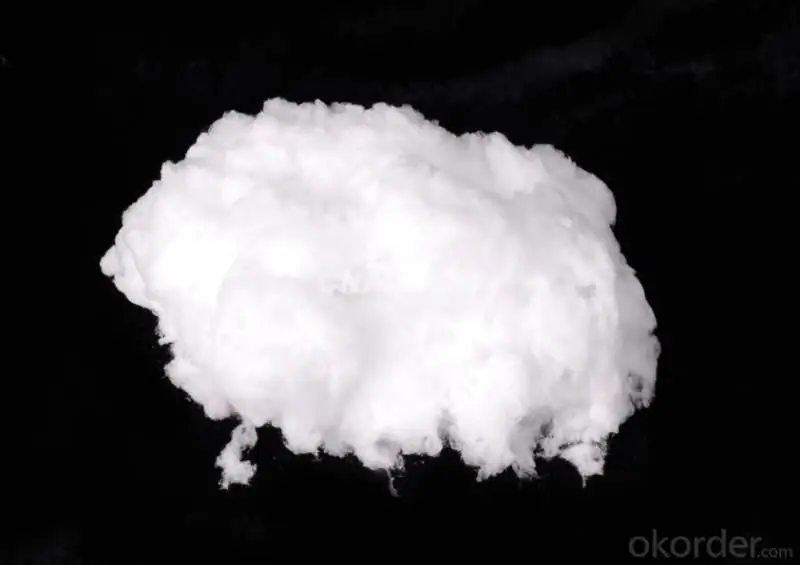
The resulting cermet composite belongs to the class of cermets and is formed into a final product by injection molding in order to orient the reinforcing fibers along the liner axis. The anisotropy of the strength properties makes it possible to preserve the compliance of the composite material in the radial direction to ensure tight contact of the sleeve walls with the chamber surface under the action of the pressure of the powder gases in order to obturate the latter.
The antifriction and anti-seize properties of the liner are ensured by applying a polyimide-graphite coating (thickness ~ 10 microns) on its outer surface with equal volume fractions of binder and filler that can withstand a contact load of 1 GPa and an operating temperature of 400 ° C, used as a coating for internal combustion engine pistons.
The density of cermet is 3.2 g / cm3, tensile strength in the axial direction: at 20 ° C - 1250 MPa, at 400 ° C - 410 MPa, tensile strength in the radial direction: at 20 ° C - 210 MPa, at 400 ° C - 70 MPa, tensile elongation in the axial direction: at 20 ° C - 1.5%, at 400 ° C - 3%, tensile elongation in the radial direction: at 20 ° C - 25%, at 400 ° C - 60%, melting point - 1100 ° C.
The sliding friction coefficient of the antifriction coating on steel is 0.05 at a contact load of 30 MPa and above.
The technological process for the production of cermet sleeves consists of fewer operations (mixing metal with fiber, casting of sleeves, hot knurling of the rim and bore, brass plating, application of an anti-friction coating) compared to the number of operations in the technological process of manufacturing brass sleeves (casting of billets, cold drawing in six passages, cold knurling of the rim and neck).
The weight of the brass sleeve of the cartridge 5, 56x45 mm is 5 grams, the weight of the cermet sleeve is 2 grams. The cost of one gram of copper is 0.7 US cents, aluminum - 0.2 US cents, the cost of dispersed alumina fibers is 1.6 US cents, their weight in the liner does not exceed 0.4 grams.
Promising bullet
In connection with the adoption of army body armor class 6B45-1 and ESAPI, not penetrated by bullets of hand-held small arms with a steel core at a distance of 10 meters or more, it is planned to switch to the use of bullets with a sintered alloy core of tungsten carbide (95%) and cobalt powders (5%) with a specific gravity of 15 g / cc, not requiring weighting with lead or bismuth.
The main material of the shell of the bullets is a tombak, consisting of 90% copper and 10% zinc, the density of which is 8.8 g / cc, the melting point is 950 ° C, the tensile strength is 440 MPa, the compressive strength is 520 MPa. hardness - 145 MPa, relative elongation - 3% and coefficient of sliding friction on steel - 0.44.
Due to the increase in the initial speed of bullets to 1000 and more meters per second and an increase in the rate of fire to 2000 and more rounds per minute (AN-94 and HK G-11), the tombak no longer meets the requirements for the shell of bullets due to high thermoplastic wear bore due to the high coefficient of sliding friction of copper alloy on steel. On the other hand, artillery shells are known, in the design of which the copper leading belts are replaced by plastic (polyester) ones, the friction coefficient of which is at the level of 0, 1. However, the operating temperature of the plastic belts does not exceed 200 ° C, which is half the maximum temperature of small arms barrels up to the beginning of their warping.
Therefore, as a shell of a promising bullet with an all-metal core, it is proposed to use a polymer composite (thickness ~ 0.5 mm) containing polyimide of the PM-69 type in equal volume fractions and colloidal graphite with a total density of 1.5 g / cc, tensile strength 90 MPa, compressive strength 230 MPa, hardness 330 MPa, contact load 350 MPa, maximum operating temperature 400 ° C and sliding friction coefficient on steel 0.05.
The shell is formed by mixing the polyimide oligomer and graphite particles, extruding the mixture into a mold with an embedded part - the bullet core and temperature polymerization of the mixture. The adhesion of the shell and the bullet core is provided due to the penetration of polyimide into the porous surface of the core under the influence of pressure and temperature.
Promising telescopic cartridge
Currently, the most progressive form factor of a small arms cartridge is considered to be telescopic with the placement of a bullet inside a pressed propellant checker. The use of a dense checker instead of the classic grain charge with a lower bulk density allows to reduce the length of the cartridge and the associated dimensions of the weapon's receiver by up to one and a half times.
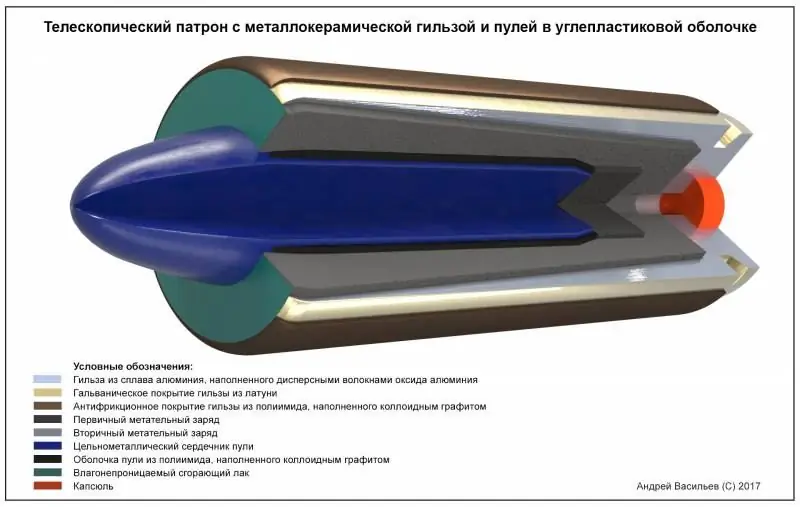
Due to the design of the reloading mechanism (detachable barrel chamber) of small arms models (G11 and LSAT) using telescopic cartridges, their bullets are recessed into the propellant checkers below the edges of the sleeve. The open end of the secondary propellant charge protects a plastic cap from dirt and moisture, which simultaneously acts as a front obturator when firing (by blocking the joint between the detachable chamber and the barrel after a bullet breakthrough). As the practice of military operation of telescopic cartridges DM11 has shown, such a method of assembling the cartridge, which does not provide an emphasis of the bullet in the bullet entrance of the barrel, leads to distortions of the bullet when fired and, accordingly, loss of accuracy.
To ensure the specified sequence of operation of the telescopic cartridge, its propellant charge is divided into two parts - a primary charge of relatively low density (with a higher burning rate), located directly between the capsule and the bottom of the bullet, and a Tuesday charge of relatively higher density (with a lower burning rate), located concentrically around the bullet. After the primer is pierced, the primary charge is triggered first, pushing the bullet into the bore and creating a boost pressure for the secondary charge, which moves the bullet in the bore.
To keep the checker of the secondary charge inside the cartridge, the edges of the open end of the sleeve are partially rolled up. The retention of the bullet in the cartridge is carried out by pressing it into the block of the secondary charge. Placing a bullet along its entire length in the dimensions of the sleeve reduces the length of the cartridge, but at the same time creates an empty volume of the sleeve around the ogival part of the bullet, which leads to an increase in the diameter of the cartridge.
In order to eliminate these shortcomings, a new layout of the telescopic cartridge is proposed, intended for use in small arms with a classic integral barrel chamber with any type of reloading mechanism (manual, gas engine, movable barrel, semi-free breechblock, etc.) and a method of firing (with front or rear sear).
The proposed cartridge is equipped with a bullet that extends its ogival part beyond the sleeve and due to this abuts against the bullet inlet of the barrel. Instead of a plastic cap, the open end of the propellant charge is protected by a moisture-resistant varnish that burns out when fired. Some increase in the length of the proposed cartridge in comparison with the known telescopic cartridges is compensated by a decrease in its diameter due to the elimination of unfilled volumes inside the sleeve.
In general, the proposed telescopic cartridge will increase the number of cartridges in the infantryman's wearable ammunition by a quarter, and will also reduce the material consumption, labor intensity and production cost of cartridge cases.