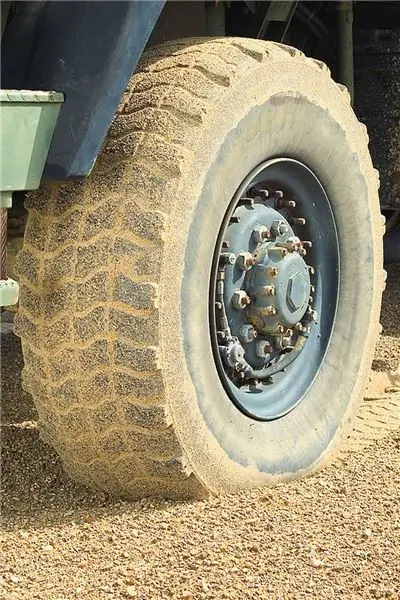
The Spicer system is designed to increase the machine's flotation by regulating the pressure in the tires to obtain the optimal size of the tire print on any ground.
Damage to a wheel or tire should not lead to extremely costly repairs, and even more so to a stuck combat vehicle right in the middle of a war zone. Elimination of such situations is the main task of specialized companies
When buying a new car today, you can easily leave the passenger compartment on a set of rubber with puncture-proof inserts, which will save you from the unpleasant task of replacing a flat tire on the side of the road. In the event of a puncture or damage to the tire, you can continue driving for up to 80 km without any serious consequences for the wheel itself, until you find a service center to replace it.
In addition to saving weight on the spare wheel and tools for replacing it with them, combat-resistant tires allow drivers not to worry about a puncture in bad weather or in an unsafe place to stop, because they can continue driving without risk of damaging the car even more.
Increase the cost of a vehicle by several hundred thousand dollars, the cost of changing a wheel by ten, replace a dangerous spot on the road with a war zone, and you will easily understand why improving tire technology is one of the most important aspects of protecting armored vehicles and their crews involved in military operations.
Wheel vulnerability
The tactical advantage of wheeled armored vehicles, which they provide through their flexibility, deployability and maneuverability, quickly made them the preferred vehicle type in Afghanistan. However, in the theater of operations (theater of operations), caused by the ubiquitous threat of improvised explosive devices (IEDs), they also had their weak points. While additional armor and newly developed double V hulls have contributed to increased levels of crew protection, the inevitable increase in vehicle weight in such cases has exacerbated problems associated with puncture or tire rupture.
Ten years ago, for most wheeled combat vehicles, the technology of combat-resistant inserts made of monolithic rubber was used. It is actually a reinforced “donut” placed inside the tire that absorbs the weight of the machine and protects the wheel in the event of damage and air release from the tire. In order for the insert (thickened tire sidewalls) to be able to carry the weight of the platform while maintaining speed over a considerable distance, the rubber must be very "hard", that is, in this case, powerful crimping tools are needed to install and remove the insert from the wheel, or the tire must be taken from the combat zone to the repair shop.
For the British army, whose entire fleet of wheeled vehicles used this technology, this led to serious logistical problems in Afghanistan. At one point in time, damaged tires were sent back to the UK for repairs, while the PTRF-RF (Portable Tire Repair Facility - Runflat) network of "Runflat" mobile wheel repair shops made it impossible to do everything locally. These deployable container modules allow for all kinds of operational tire repair and maintenance during a military campaign.
Soft step
The threat of IEDs forces tire manufacturers to constantly develop new solutions that, after a puncture or rupture of a tire, enable a car and a crew to safely reach base, and also minimize wheel damage.
Michelin, a manufacturer of X-Force versatile tires that are widely used on military vehicles, has developed a so-called "mine" tire. The tire, first shown at Eurosatory 2014, was developed to meet the needs of the French army, in particular for the SOUVIM II mine clearance system.
This system, manufactured by MBDA, designed for mine clearance and IED disposal, is capable of clearing up to 150 km per day. The system consists of two vehicles towing trailers to activate the min. The first car rolls over a push-action mine without activating it, while the mass of the towed machine - the mine-triggering trailer (RDM) - triggers push-pull mines in order to ensure the passage of the second car. That, in turn, tows two more RDMs with different wheelbases, thus clearing the track across the entire width.
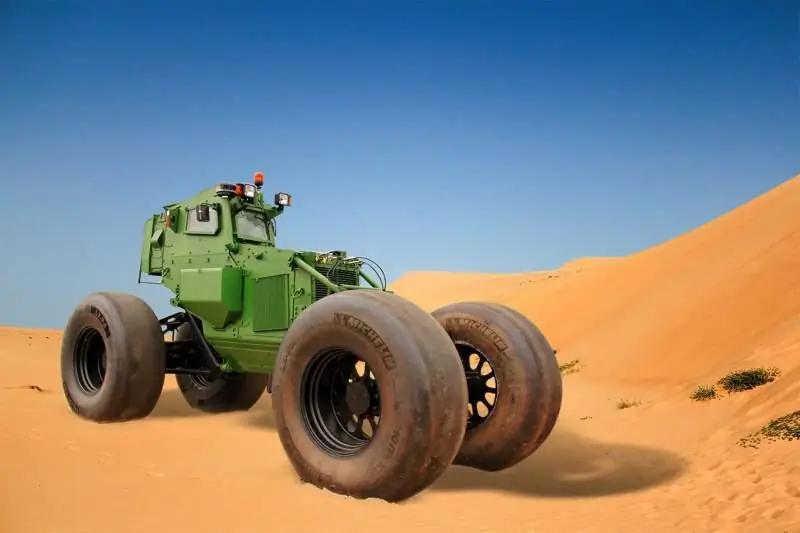
Michelin has created its mine tire with less ground pressure than a human foot. This allows you to clear safe passages in minefields without explosions.
The Michelin LX PSI 710/75 R34 mine-action tires allow the vehicle to travel through minefields without initiating and activating flat and conical landmines. This is made possible by very low pressure wheels. When these tires are installed on a 7, 5-ton SOUVIM II machine, the actual ground pressure refuses to be less than the pressure of a person's leg - 360g / cm2. A standard reconnaissance vehicle has a ground pressure of approximately 5 kg / cm2.
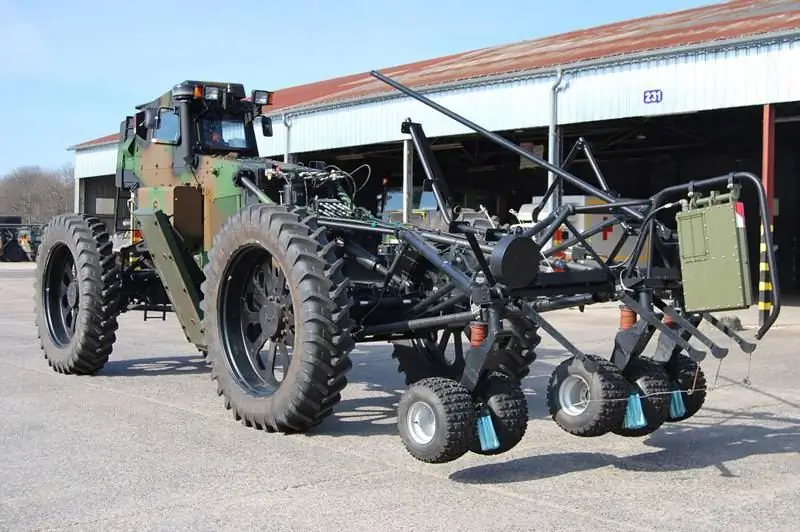
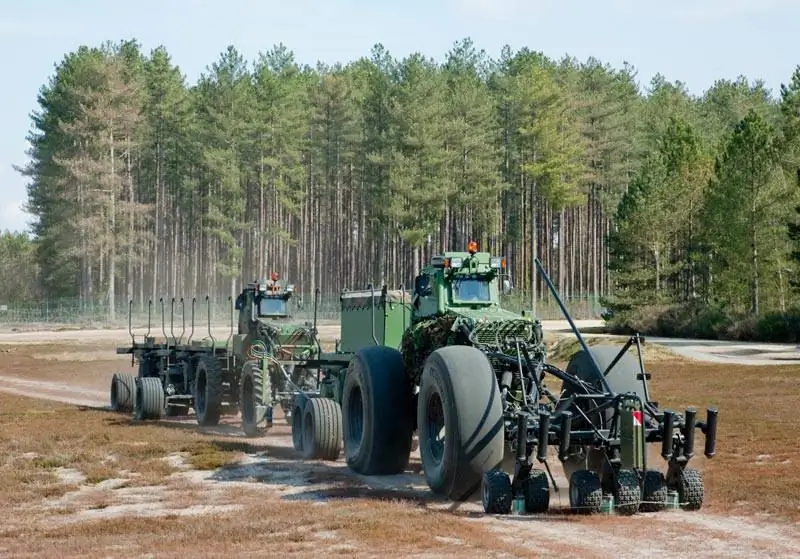
French Army SOUVIM II mine clearance system
The tire uses a 10 cm thick strip of foam that sticks to the tire, a development from Michelin's agricultural tires. The tire allows you to get the largest possible contact patch of the tire with the supporting surface, and the foam strip itself is covered with a thin protective rubber "film", which also increases grip.
Advantages of rubber
Rubber has a number of advantages in the technology of impact resistant inserts, and some manufacturers work exclusively with this material.
“Rubber does not tend to break, it absorbs some of the shock loads, which is important for military vehicles moving off-road in a hostile environment,” said Tyron CTO Tony Glazebrook.
“Unlike composites, which are themselves very hard materials and can cause high shock loads even with excellent suspension - and high shock loads increase the chance of wheel damage and loss of mobility - rubber dramatically reduces vibration and shock that is transmitted through the insert on wheels, axles and drive shafts”.
"This has a positive effect on vehicle handling and reduces damage to the inside of the tire, which means it can be potentially reused."
Rubber is also the only material that produces the so-called "lock" that is the centerpiece of Tyron's bulletproof inserts. The bead lock is a mechanical device that locks the bead (the edge that sits on the wheel) to the wheel itself. In an inflated wheel, the bead is pressed against the inner surface of the wheel rim by the pressure in the tire so that the tire and wheel rotate as a unit. In the event of a drop in tire pressure, for example in the event of a puncture or damage, the lock is necessary to prevent the tire from turning inside the wheel, which, in the end, can lead to a loss of mobility.
“Military vehicles must be able to continue on mission and return to base on one or all flat tires - guaranteed minimum 50 km with two or more flat tires or a minimum of two hours off-road with inclines and obstacles,” Glazebrook said. "Our All Terrain Rubber [ATR] inserts allow military vehicles to exceed this distance, and therefore, in the event of damage, the car can travel with one, two or even eight flat tires to the point where they will be repaired or replaced."
"Because our inserts are multi-piece, they can be installed without special tools and are easy to replace even on the side of the road using standard tire change equipment, while still retaining all the benefits of rubber."
Tried and tested
Tyron's customers have subjected ATR inserts to ballistic testing, with a focus on connectors, to ensure that the insert will remain functional under heavy kinetic attack. This is important because rubber absorbs significantly more energy (from curbstones to IEDs) than hard materials.
In September 2015, Tyron announced that it would work with Global Wheel to supply complete armor-piercing inserts for South African DCD Defense's Springbuck armored personnel carrier. The original contract was for the delivery of three complete sets of wheels, the design of which consists of a wheel rim from the Global Wheel, prefabricated ATR inserts from Tyron and tires from Continental.
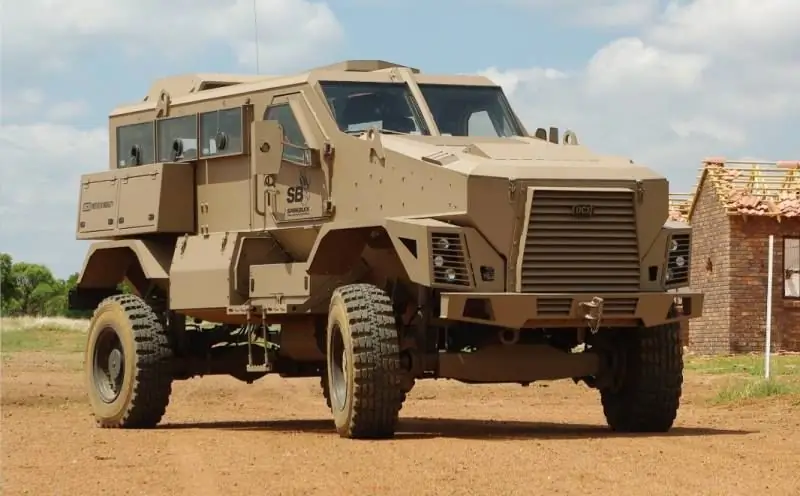
Together with its partner, Global Wheel, Tyron supplies complete wheels with impact-resistant inserts for the South African DCD Defense Springbuck armored personnel carrier.
Work on this contract is ongoing and the company claims that it sees a great interest in its products from the manufacturers of cars with 4x4, 6x6 and 8x8 wheel configurations.
“As with the Springbuck, the insert can be supplied as part of a complete wheel for installation on a new machine,” said Glazebrook. “They can also be supplied as a new component for mid-life upgrades as the machine axle can take on extra weight. They do add mass to the car just like any other insert, but most armored vehicles can take some mass and so there is no problem here."
Comparison with composites
As the main alternative to rubber, composite materials have their own advantages - they are lighter, less expensive to manufacture and can be adapted to the existing one-piece wheel.
RunFlat International offers several composite wheel solutions, including its Dynamic RunFlat system, which consists of two or three bulletproof composite segments bolted to the wheel rim. The advantage of the two- or three-piece system over the donut style is that it can be installed and removed in the field using standard equipment.
When the tire is fully inflated, the segments remain fixed to the rim, but when the tire is deflated, they “spin” against the forward rotation of the tire and wheel, compensating for the difference in inflated / uninflated tire diameters on each side of the axle. This allows the car to travel up to 100 km with one or more flat tires.
“Our modular inserts make it relatively easy to swap out turbine tires, which is very important because tires in Afghanistan last less than their design life,” said Tom Westley, head of sales at RunFlat International.“In addition, our products do not wear out over time, and they cope well with ballistic attacks or rough terrain, which is always the cause of insert breakage.”
The polymer created and used by the company is capable of withstanding ballistic attacks. The material does not split, it absorbs energy and is pulled back regardless of the temperature. According to the company, this material is lighter than rubber, which makes it possible to increase the carrying capacity of the machine.
Depending on customer requirements, different Dynamic RunFlat solutions allow a car with a flat tire to travel different distances: from 15 km at a speed of 50 km / h on the road and up to 100 km on the road or 60 km off-road. The patented locking system makes them easy to install; no lubrication is needed inside the tire, it is only needed on the inner profile of the insert, which is in contact with the rim, which contributes to a smoother sliding of the tire when flat. The company also offers the Static RunFlat system for the collapsible wheel rims of military vehicles, which often travel off-road. The system consists of three bulletproof segments rigidly bolted around the wheel hub; they lock and hold the tire in place, deflated or not. Thanks to its patented collar shape, the system is particularly stable when the wheel is flat. This system is primarily intended for military applications on the road and off-road, it usually allows you to drive with flat tires from 50 to 100 km.
RunFlat International does not name military projects using its products, but it has several contracts in the Middle East - the second largest market after Europe - that are currently underway.
“The withdrawal of troops from Iraq and Afghanistan has had a negative impact on demand … but large new combat vehicle projects are starting that will determine the need for inserts in the coming years,” Westley is optimistic. “Our ability to supply lightweight, durable and easy-to-use wheels that can be adapted to each project is very important here.”
“Providing higher levels of protection against IEDs has resulted in vehicles gaining a lot of weight, and heavier vehicles need to be shod with wheels that can withstand increased loads. As a tire and wheel specialist, we can design and supply a wheel that is fully compatible with a ballistic insert or lock, as well as a wheel assembly that is completely ready to be installed on a car."
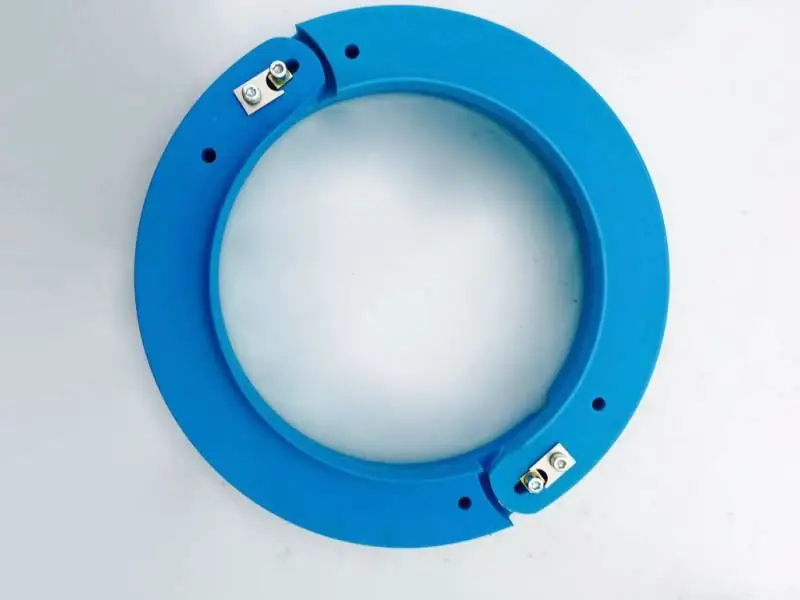
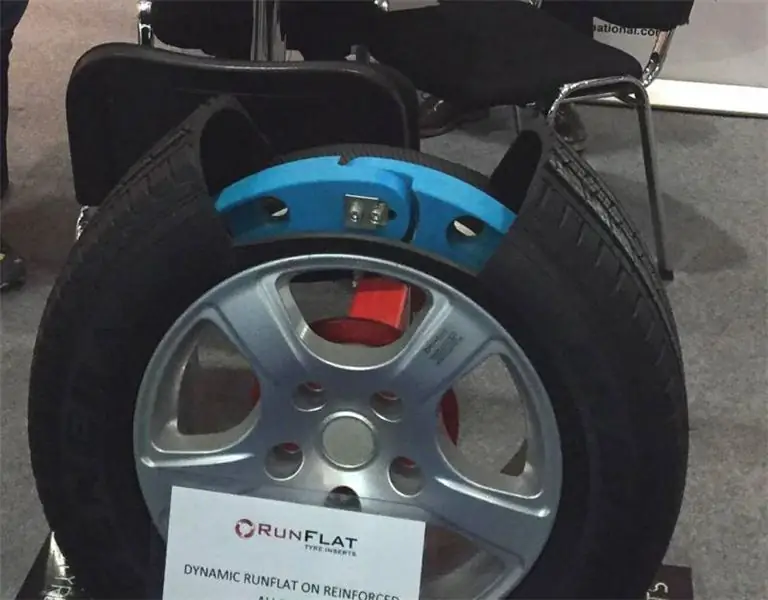
Dynamic runflat system consists of two or three bulletproof composite segments bolted to the wheel rim
In solid state
The concept of "airless" or non-pneumatic tires has been explored for several years. They are mainly intended for the civilian market, especially for slow moving vehicles that do not use or require no suspension, such as lawn mowers. But this technology has moved into the military realm as a potential solution capable of countering landmines and IEDs.
Bridgestone has developed a number of prototypes for the Air Free Concept Tire, while Michelin is interested in military applications for its X Tweel Airless Radial Tire (ART) solution, a tire-and-wheel assembly available in multiple versions for off-road vehicles.
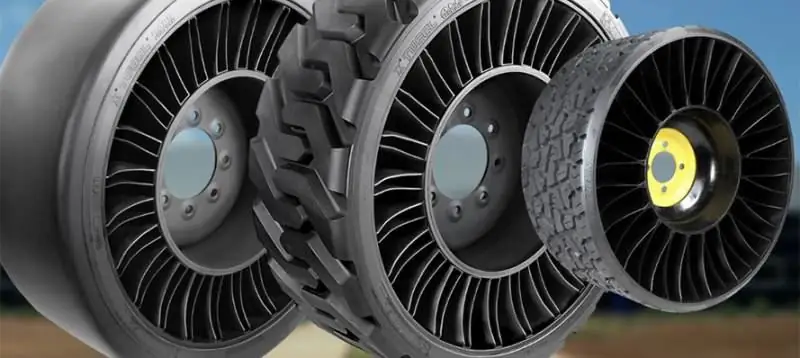
Michelin Tweel family
The Tweel solution is a set of high-strength steel belts that act as a semi-rigid cylindrical “longitudinal wall” that forms a kind of elastic mechanical spring around the wheel; High strength polyresin spokes connect the steel bands to the wheel hub. As with conventional air tires, a low specific pressure is achieved with a relatively low total weight.
Another option was developed by Resilient Technologies. Non-Pneumatic Tire (NPT) non-pneumatic tire under a contract with an army research laboratory, issued in the mid-2000s, was developed and tested from the very beginning for the HMMWV armored vehicle. The NPT tire offers exceptional mobility and safety compared to insert tires, as it will not puncture or deflate when hit by a bullet, debris or an IED detonation.
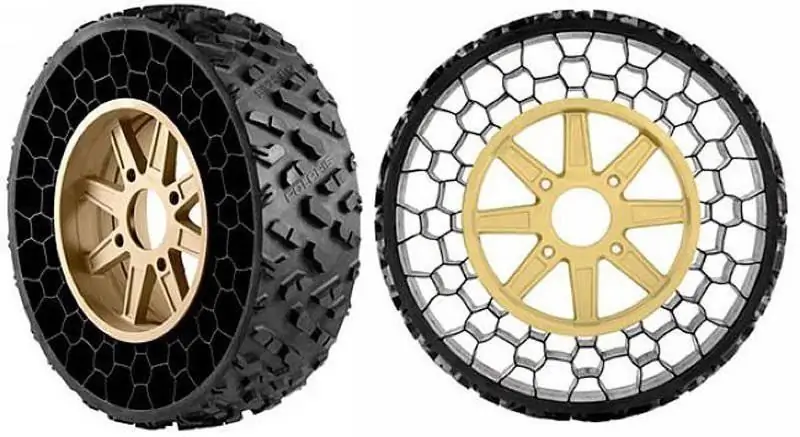
Non-Pneumatic Tire (NPT)
After the purchase of Resilient Technologies by Polaris, NPT non-pneumatic tires were available as an option for the Sportsman MV850 SUV. TerrainArmor NPT tires can withstand bullets, sharp stones and other objects that can damage pneumatic tires, eliminating the need for a spare wheel on the machine. Driving on these non-pneumatic tires is no different from driving on pneumatic tires.
The tire structure consists of a rim, a polymer disc and a tread strip, which together form a "virtually indestructible" wheel. The blade, disc and rim are specially designed for the target load and prevailing terrain.
Tire control technologies
Sophisticated "tire management" technologies are also gaining ground in the defense market as users want improved four-wheel drive performance, better mobility, and a comprehensive diagnostic suite integrated into a single subsystem.
Dana announced in September 2015 that it will supply its Spicer tire pressure control system for the new Joint Light Tactical Vehicle (JLTV), which Oshkosh will produce for the US Army and Marine Corps. The system is designed to enhance the performance of tactical wheeled vehicles on dirt roads, steep slopes, sand or mud, while increasing speeds in a wide variety of terrain and getting to base in the event of a tire puncture. The system also allows you to reduce the ground clearance when transporting the vehicle by various modes of transport.
In fact, the system allows, if necessary, to inflate and download tires, adjust the pressure in them to a level corresponding to the relief, which increases traction with the ground and maintains passability. The operation of the system is controlled by an electronic-mechanical control unit, which detects and solves all problems with tire pressure, allowing each wheel to be monitored separately. The control unit is an integrated module that includes mechanical, electrical and computer subsystems.
Dana has two base systems in its portfolio with slightly different configurations. The first system is optimized for light 4x4 vehicles and is currently contracted for the JLTV project. A second, more efficient system is installed on some larger military vehicles, such as the MRAP categories or the FMTV family of medium-duty military vehicles. The main components include a pneumatic control unit, quick release valves, an electronic control unit, and wheel valves.
Dana's head of sales, Robert Goldston, said the company has been active in contracting for all projects that competed for the JLTV program, from conceptualization through technical design to full development and production preparation.
“Through these efforts and strong relationships with our system component suppliers, we have been able to navigate clearly through every step of the JLTV program,” he added. - This system is essentially a ready-made commercial system that we have modified for light military vehicles operating in difficult conditions. It remained for us to carry out some revision of the software in order to fulfill all the requirements of the JLTV project in terms of tactical and technical characteristics."
The company is currently preparing for high-volume series production, with systems for the initial batch already delivered.
A major driving force behind Dana's R&D efforts was customer insistence on integrated user interfaces and algorithms to work consistently with other machine subsystems.
“For example, if there is a request for the suspension to go into a certain mode, then the pressure control system will also enter the predetermined mode. In addition, customers want to reduce the time it takes to inflate and deflate their tires so that they can transition from one type of terrain to another as quickly as possible.”
In addition, the system is field programmable, and built-in diagnostic tools alert the driver to potential tire problems and provide the status of the entire system. Looking ahead, the company is working on solutions that will help reduce tire inflation and deflation times.