The currently privately funded Stratolaunch system was conceptually described in the early 1990s by a group of engineers at the V. I. Dryden commissioned by NASA. The air launch was worked out in connection with its all-azimuth, that is, the possibility of launching in any direction. The classic rocket launch from ground-based spaceports requires spatial maneuvers, for which a large part of the fuel supply is used. And the carrier aircraft can easily and naturally change course, go to the most favorable equatorial courses, and launch satellites (including dual-purpose ones) into geostationary orbit. It is also important to remember about the so-called exclusion zone, which must be present near cosmodromes - debris of the booster stages of rockets fall on its territory. The format of such zones can reach several thousand square kilometers with serious restrictions on any economic activity in their areas.
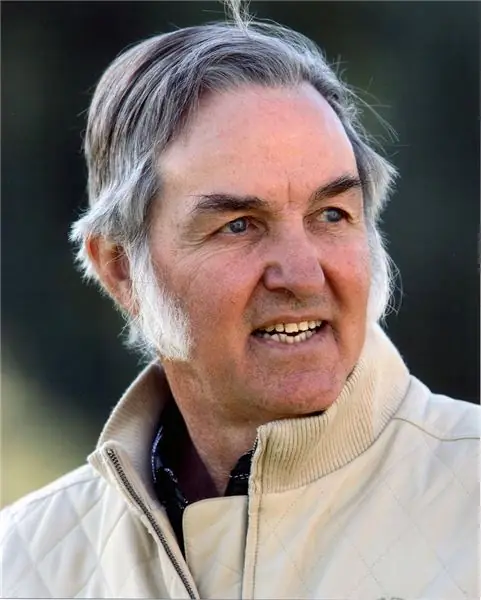
Bert Rutan. Source: popmech.ru
As always, there is an active personality in the history of non-trivial ideas, who put a lot of effort into translating it into reality. Such for the Stratolaunch project was aircraft designer Bert Rutan, who proposed abandoning the flawed, in his opinion, idea of remaking the existing flying "heavyweights" for air launch. And there were a lot of projects - the An-225 with a maximum take-off weight of 640 tons was proposed to be equipped with a 250-ton rocket, which, in turn, delivered no more than 12 tons of payload into orbit. But commercial calculations have shown that for payback it is necessary to throw at least 20-25 tons of net weight into orbit, and the weight of the carrier aircraft in this case will exceed 1000 tons. And all would be fine - there are no special theoretical difficulties for assembling such a machine, but where will such a giant sit? The creation of one or two aerospace centers for aircraft of this class actually devalues all the economic bonuses of an air launch. Rutan proposed the Grasshopper Grasshopper subsonic aircraft, which became the prototype for the Scaled Composites Model 351 Roc embodied in steel and composites. The vehicle was two-fuselage with a four-support chassis and was intended to launch a carrier rocket from heights exceeding 12 km. To some extent, the developments were implemented in the SpaceShipTwo tourist suborbital station. In 2010, the talent of Bert Rutan was joined by the financial potential of the investor Paul Allen, who created the Stratolaunch Systems project. The guys were already familiar - the SpaceShipOne rocket plane, capable of climbing 100 km or more, is their handiwork. Top-level specialists were invited to develop the six-engine miracle - engineers of the Space Shuttle project, as well as pilots of the reconnaissance and, concurrently, the fastest aircraft SR-71. During the year, we managed to create a three-pronged project - a flying launch platform, a medium-class launch vehicle and ground infrastructure, that is, a GDP, a hangar, and so on. The most interesting thing is that the idea generator Bert Rutan stopped working on his brainchild in April 2011, when he left his company Scaled Composites, which designed the Roc.
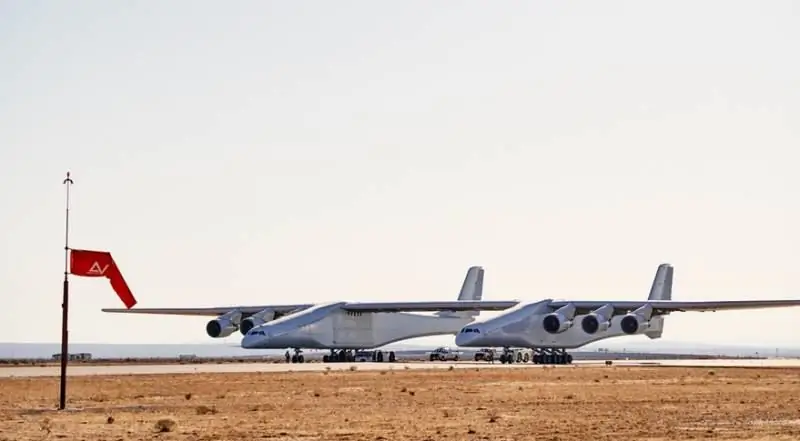
Scaled Composites Model 351 Roc ("Bird Roc") taxiing. Source: spacenews.com
Initially, the "birdie" was supposed to weigh about 544 tons, but in the process of development and assembly, this value grew to 590. The ubiquitous Elon Musk, without whom, it seems, not a single world hi-tech-kipish passes, oversaw the development of a launch vehicle based on own Falcon 9. The launch weight of the Falcon 9 exceeded 400 tons, the projected aircraft was unable to lift it off the ground, so the "nine" was cut to the Shorty version. The rocket was more compact, lighter (up to 250 tons) and had to fit in the inter-fuselage space of the Scaled Composites Model 351. The project assumed the launch of as much as 6, 12 tons of payload into orbit, which even then raised questions about the feasibility of this undertaking. But the work went on - the organizers rented 8, 1 hectares of area in the California Mojave Desert, where in October 2012 they built a workshop for the production of composite structures and a hangar for assembling the future aircraft.
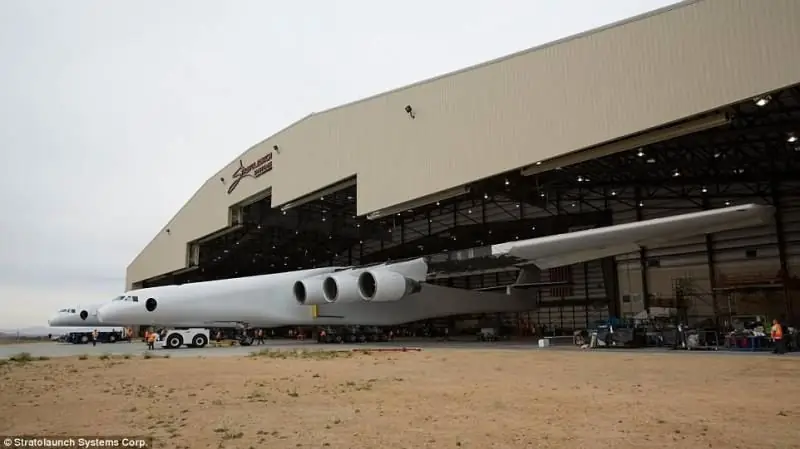
Rollout of Scaled Composites Model 351 Roc from the hangar. Source: dailymail.co.uk.
A large aircraft has large areas: the composite shop occupies 8100 square meters, and the hangar is already 8600. The take-off concrete, however, is quite compact for an aircraft of this size - only 3800 meters.
The Model 351 is in many ways a hodgepodge of industry-proven solutions, as the Boeing 747-400 shared the engine, landing gear, mechanized wing controls and avionics. Moreover, Paul Allen for the project bought two used (!) Aircraft from United Airlines, assembled back in 1997. The carrier aircraft of the Stratolaunch Systems system is designed according to the scheme of a two-fuselage high-wing aircraft with a straight wing of high aspect ratio and horizontal tail section of the fuselage. In the central part of the wing, between the fuselages, there is a suspension and drop system for a launch vehicle weighing up to 250 tons. The main structural material of the airframe is carbon fiber, which has become the hallmark of Scaled Composites.
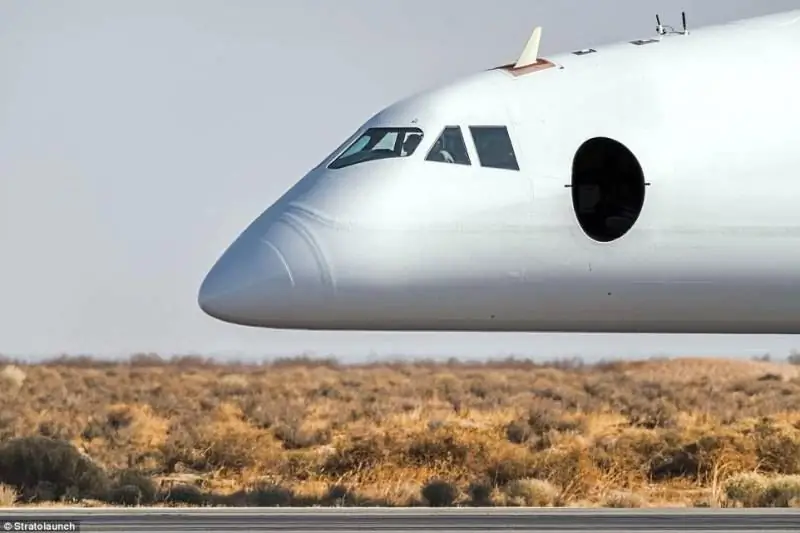
One of the two cockpits. Source: dailymail.co.uk
28 wheels of the aircraft landing gear allow it to be rather gentle on the take-off concrete with a mass of 590 tons. Under the wing consoles are suspended six good old PW4056 from Pratt & Whitney, creating 25.7 tons of thrust each. The wingspan makes the Roc Bird the most in aviation history - the An-225 Mriya (88.4 m), the A380 (79.8 m), and even the immortal creation of Howard Hughes H-4 Hercules with his gigantic 97.5 meters. But in the maximum take-off weight, the two-fuselage noticeably loses to Mriya with its 640 tons, but firmly holds the second line in this indicator in the world. Engineers are planning the aircraft's ability to accelerate to 850 km / h and launch the launch vehicle at a distance of up to 2200 from the parent airfield. An important design decision was the fact that the Model 351 could be used as a transport (read, military transport) aircraft in order to recoup development and operation costs. For this, the rocket coupling-uncoupling unit is dismantled and the aircraft is ready for transportation of oversized cargo, which, for example, cannot fit into the An-124 Ruslan. The short history of the Model 351 has the following chronology:
- May 31, 2017 - rolling out of the hangar;
- June 29, 2017 - the US Federal Aviation Administration issued the tail number N351SL;
- September 2017 - the first starts of the motors;
- December 18, 2017 - the first taxiing and jogging along the airfield at a speed of 50 km / h.
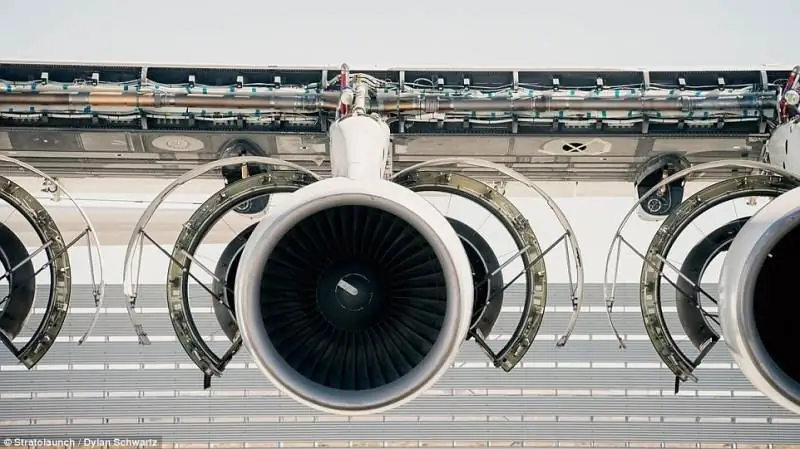
Pratt & Whitney PW4056 triple with hoods open. Source: dailymail.co.uk
Development engineers are optimistic that in the current "Bird Roc" will take its wing, and in 2019 will launch the first rocket into space. True, there is nothing to launch yet - SpaceX Mask came out of their project back in 2012 due to a lack of resources for a secondary project for them. And the rework of the Falcon 9 design for Stratolaunch Systems was already too fundamental. The search for new rocket scientists led Paul Allen to the OSC company, which proposed a solid-propellant Pegasus II, which sends 6.1 ton of useful mass to low-earth orbit. But by 2014, Pegasus was abandoned in favor of a new product - a three-stage Thunderbolt rocket equipped with two solid-fuel and one liquid (hydrogen + oxygen) engines. By September 2014, the American firm Sierra Nevada spoke about the development of the Dream Chaser spaceplane, adapted for the Stratolaunch system. Such a spaceplane will send up to three astronauts into space and safely return them to earth. Finally, the system can send spacecraft and similar objects in a suborbital mode to any part of the world in just 1.5-2 hours. Feel the ambiguity of Stratolaunch Systems and Sierra Nevada's "peace" mission?
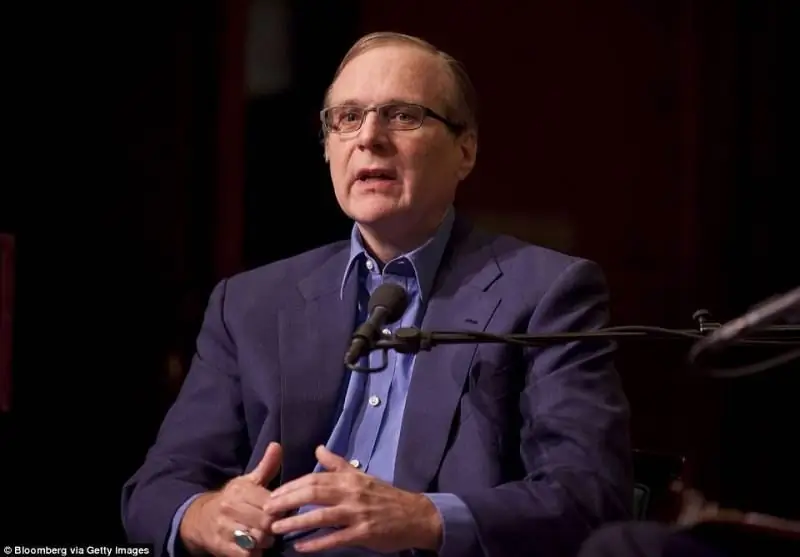
Paul Allen, chief financier of the Stratolaunch Systems project, trying to go down in the history of the global aviation industry. Source: dailymail.co.uk
As a result, the news about the last two projects slowly left the information field, and Paul Allen got sick with a new idea of using his brainchild. It is proposed to hang three light Pegasys XL missiles at once under the wing of the Model 351, but the market for services of such "kids" is very narrow - no more than one launch per year. Is it worth it for the sake of such a fence for such a monster? So the engineers were able to persuade the leadership of Stratolaunch Systems to develop … its own launch vehicle. By June 1, 2018, the company plans to test its first rocket engines at the Stennis Space Center, for which the first $ 5, 1 million has already been allocated. As a result, Paul Allen was faced with the need to develop the entire air launch complex from scratch - from the GDP to the launch vehicle. And to do with "used" spare parts here, it seems, will not work.