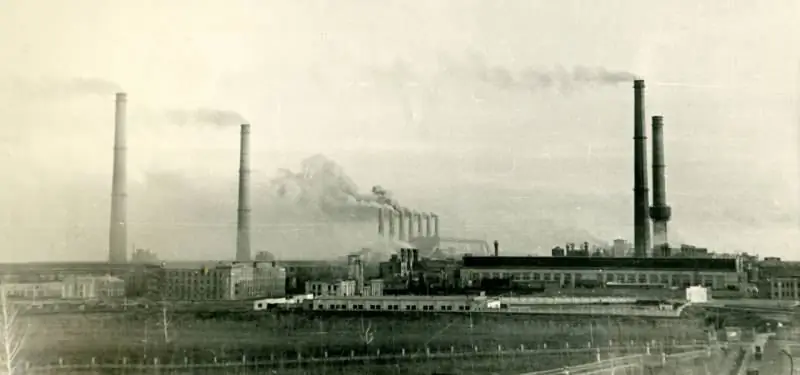
Chemical educational program
Iron, manganese, chromium, oil, rubber, aluminum, lead, nickel, cobalt, antimony, arsenic, mercury, molybdenum, tungsten, diamonds, sulfur, sulfuric acid, graphite and phosphates are among the irreplaceable raw materials on which strategic success depended battles in World War II. These elements play a special role in mechanical engineering. Academician Alexander Evgenievich Fersman once mentioned that at least thirty elements are required for the production of a tank, and all combat aircraft flies on almost fifty elements. In addition to the highly demanded aluminum and copper, the real "vitamins" of the military industry were nickel with molybdenum ("metals of tank armor"), lead with antimony (batteries, chrome protective paints, babbits, bullet cores, etc.), tungsten with cobalt (cores of sub-caliber shells, tool steel) and mercury with zirconium (primers, detonators, smokeless powder ingredients). Less known, but no less important were lithium (life support systems in submarines), titanium and tin salts (smoke screens), bismuth (antiseptic and healing compounds), and vanadium and platinum, used as catalysts in the oil industry of the Soviet Union.
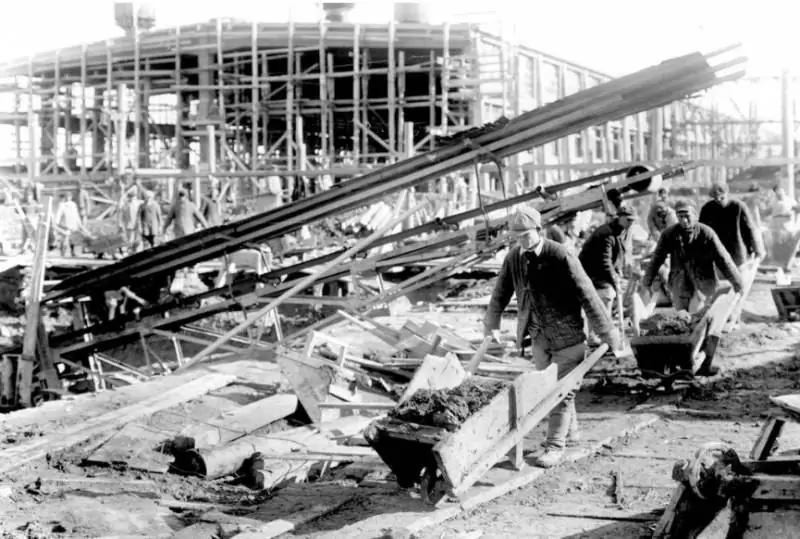
Non-ferrous metals are in many ways a real skeleton of war (as you know, oil is blood). For example, in 1914, the offensive of the German army fell through, according to the historian McNeill, precisely because of the acute shortage of copper, which is part of the alloy for the casings. It is noteworthy that tsarist Russia, already in 1916, actually worked out all of its explored deposits of non-ferrous metals in Siberia, the Urals and the Caucasus. And by 1917, another problem arose - an acute shortage of rolling stock, which paralyzed the transit of ore to smelters in Moscow and St. Petersburg.
In order to understand the degree of influence of non-ferrous metallurgy on the production of military goods, I will cite statistical data. In June 1941, the share of products for the Red Army in the structure of the People's Commissariat for Non-Ferrous Metallurgy was a record 60%. Even at the People's Commissariat of Heavy Engineering, only half of the production went into the army. And already in July 1941, the share of military products from the People's Commissariat of Nonferrous Metallurgy jumped by 15%. And in the future, the government did everything possible to ensure the uninterrupted production of scarce non-ferrous metals. So, already on July 28, 1941, the USSR People's Commissariat of Defense was instructed to send 10 construction battalions to help the builders of the Ural aluminum plant. As a result, the capacity of one of the few then aluminum enterprises was increased faster.
There were also fundamental shortcomings in the Soviet Union in the pre-war period, with which the industry entered the Great Patriotic War. First of all, this is a chronic shortage of non-ferrous metals, which caused both the plans for the production of civilian equipment and military products to suffer. The production of cartridges suffered: on average, from 1930 to 1933, the percentage of fulfillment of the defense order varied from 38.8 to 57. During this period, artillery shells were not fired even half of the required amount - in 1932 the order was fulfilled by 16.7%. And in the future, this situation was never completely reversed. The second problem in the production of weapons and, accordingly, the consumption of expensive non-ferrous metals, was the high proportion of waste. So, in the first five-year plan, in the production of shells, up to 60% of the metal went to waste, in the manufacture of artillery systems - up to 70%. For comparison, in the UK, waste rates were more than half as much.
Aluminum hunger
The beginning of the Great Patriotic War was a serious shock for non-ferrous metallurgy - the production of rolled metal fell 430 times. Under the Germans were the factories that supply nickel, copper, magnesium, zinc, the country lost up to 60% of the vital aluminum. There were serious problems with aluminum at that time. Initially, before the war, it was possible to build several enterprises for the smelting of this valuable metal. In June 1930, construction began on the Volkhov Aluminum Smelter, which was noted for its first smelting already in 1932. It is noteworthy that the poor Tikhvin bauxite was not originally intended to be used for the Volkhov Combine - the specialists of the American Aluminum Company ALCOA could not help the Soviet metallurgists in any way. However, domestic chemists-technologists managed to solve this problem. The most powerful enterprise for the production of aluminum in the USSR was the Dneprovsky Combine, which in 1937 accounted for up to 70% of all metal in the country. By the way, a year earlier the country took the second place in Europe (after Nazi Germany) in aluminum smelting. This includes the share of the Ural Aluminum Smelter, which reached its design capacity in 1939. But even this was not enough for the industry of the Soviet Union. So, in the pre-war 1940 (IV quarter), the shipment of commercial aluminum was completed by 81 percent. The "aluminum famine" had a negative impact on the production of military aircraft - in 1941 it was planned, at best, for the whole country to receive 90 thousand tons of "winged metal" when the need for the aviation industry alone was 87 thousand tons. Where to get another 20 thousand tons for other needs, it was not clear. The aviation industry not only suffered quantitative losses - the quality of aircraft in the 30s lagged behind world standards. The structures of the winged machines were predominantly made of composites: wooden fuselages and metal wings, as well as wooden wings and a metal fuselage from trusses covered with canvas. In fact, only bombers of the TB-3, SB and IL-4 types could be completely made of duralumin.
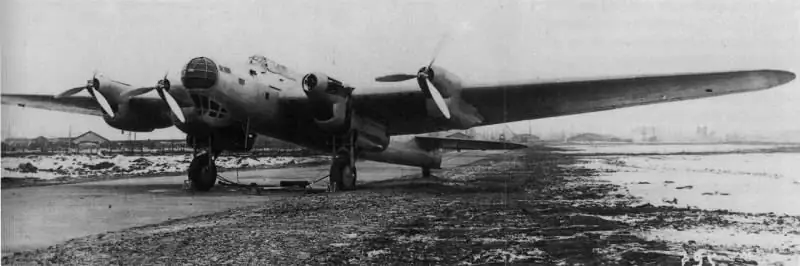
For comparison, we present data on Germany, which from 1937 to 1939 increased the total production of aluminum from 120 thousand tons to 192 thousand tons. And in 1941, the Germans generally managed to melt a record 324 thousand tons! This was one of the secrets of the success of the German aviation - there was simply a lot of aluminum. The USSR was not helped by the supply of aluminum from abroad - from 1938 to 1940, imports fell from 7652 tons to a scanty 513 tons. Many reduced supplies due to the war (France and Norway), and the US cut supply channels due to the militarization of the Soviet Union's economy.
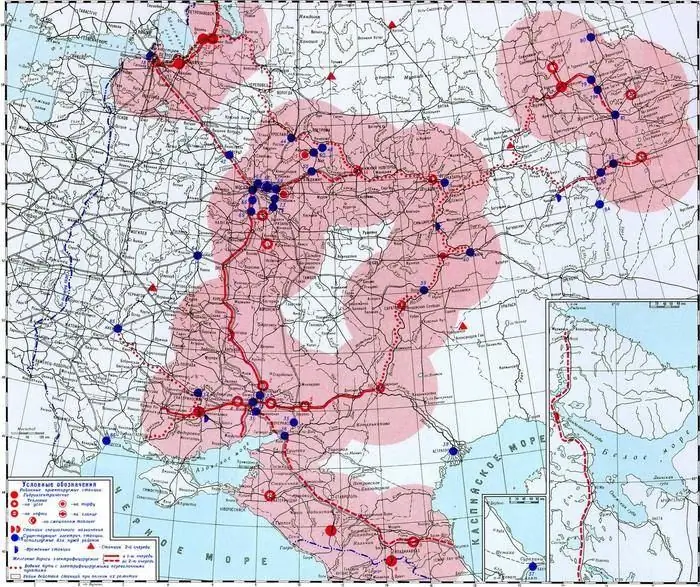
Among the many plans of the Council of the Defense Industry in the summer of 1940 was the construction of two rolling mills with a capacity of 20 thousand tons each. Even then there was an understanding that by 1943 the industry would demand about 120 thousand tons of aluminum annually. It was planned to allocate up to half a billion rubles for the construction, and an additional 63, 5 million were supposed to be spent on the pipe-pressing shop and the reconstruction of plant No. 95, engaged in the production of duralumin. Also in the plans was the purchase of a Junghaus continuous casting unit from the Germans for 3 million rubles. In this situation, the aluminum plant being built in Kandalaksha could help, but before the outbreak of the war it was not put into operation. In 1941, the plans were revised again. By 1942, 175 thousand tons of winged metal had to be smelted. There is a feverish attempt to catch up with the German military-industrial complex in aluminum production, or at least close the gap. Even intelligence helped to save metal in the era of the "aluminum famine". On November 15, 1940, from the General Staff to the Council of People's Commissars, a translation of decrees No. 39 and No. 47 of the German Reich Directorate based on materials was received. They talked about the logic and the possibility of saving valuable non-ferrous metals, as well as the prohibition of their use in a number of products.
The Germans were supposed to help Soviet Russia with the supply of commercial aluminum in 1941. After Europe was occupied, and the Americans were "offended" at us, the country's leadership had no choice but to turn to a potential enemy for help. In accordance with the agreement on mutual supplies from May 11, 1941 to August 1, 1942, at least 20 thousand tons of aluminum were to come to the USSR from Germany. History, as you know, has perverted everything. With the beginning of the practical implementation of the Barbarossa plan, two large aluminum enterprises - the Dneprovsky and Volkhovsky plants - were under the enemy. There is only one plant left that is engaged in the smelting of winged metal - the Ural aluminum plant.
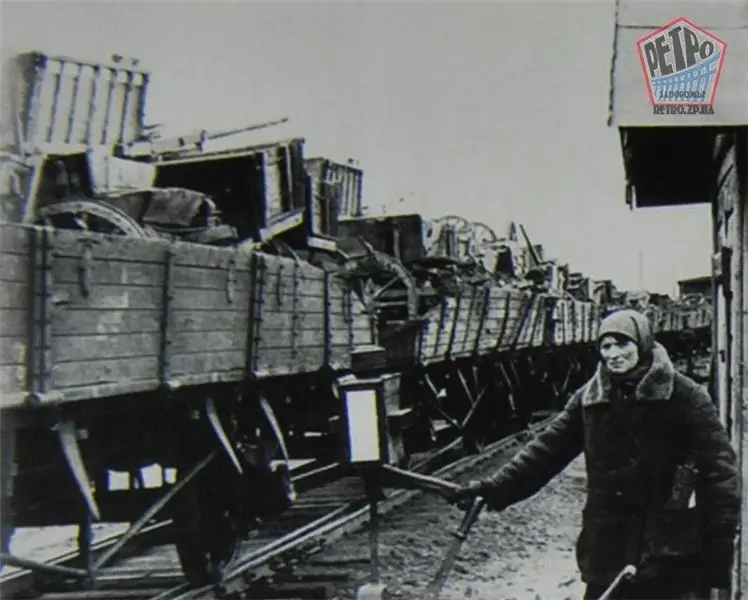
In the end, I will quote the words of one eyewitness to the shutdown of the Dneprovsky aluminum plant, which were published in the book "Non-ferrous metallurgy during the Great Patriotic War":
“It was a slightly cool, clear, sunny morning. Enemy planes passed to the East. Heavy artillery shelling of the sixth village began from the right bank. On August 18, 1941, the power system dispatcher ordered the converter substation to completely turn off the electricity. The bus voltage dropped to zero; all motor generators stopped, and after a few minutes there was absolute silence in the converter station. All three plants of Glavaluminium were stopped at full speed with loaded furnaces, equipment filled with solutions, electrolyzers with molten electrolyte and aluminum."
The country entered into a protracted war, and the "aluminum famine" was felt especially acutely.
The end follows …