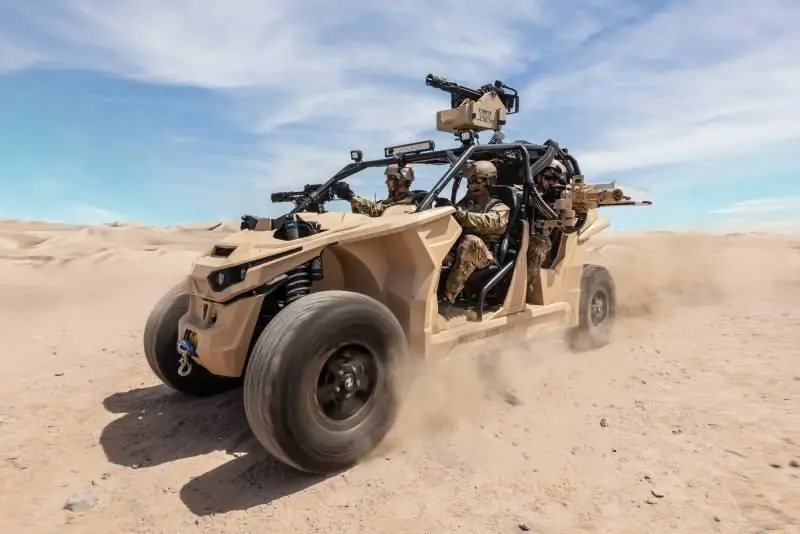
The energy required to propel ground vehicles and to operate their systems and assemblies is traditionally provided by diesel engines. Reducing fuel consumption not only increases the range, but also reduces the amount of logistics, which is determined by the maintenance of fuel reserves, and increases the protection of rear service personnel in the process of servicing equipment.
In this regard, the armed forces are striving to find a solution in which the high efficiency and high specific heat of combustion of diesel fuel inherent in systems with an electric drive would work in one "team". New hybrid solutions and advanced combustion engines have the potential to offer great practical benefits alongside quiet single-electric drive, quiet monitoring (battery operated sensors while stationary), and power generation for external consumers.
Power train potential
Research Canada (DRDC), for example, is investigating the feasibility of hybrid diesel-electric powertrains. The FDA published its research in 2018, focusing on light tactical platforms such as the HMMWV, DAGOR-class ultralight combat vehicles, and small single and multi-seat ATVs.
The report Feasibility of Hybrid Diesel-Electric Powertrains for Light Tactical Vehicles notes that in most driving modes where speeds and loads vary significantly (typically off-road), hybrids have 15% -20% better fuel efficiency in terms of fuel economy. compared to traditional mechanically driven machines, especially when using regenerative braking. In addition, internal combustion engines, including diesel engines, perform best when operated at carefully selected constant rpm, which is typical of sequential hybrid systems in which the engine operates only as a generator.
As the report notes, since engine power can be supplemented by batteries during short periods of peak power consumption, the engine can be tuned to provide only the average power required, with smaller powerplants generally using less fuel, all other things being equal.
With sufficient battery capacity, hybrids can also remain in silent monitoring mode for a long time with the engine off and working sensors, electronics and communication systems. In addition, the system can power external equipment, charge batteries, and even power a military camp, reducing the need for towed generators.
While hybrid drives offer superior performance in terms of speed, acceleration and gradeability, the battery pack can be heavy and unwieldy, resulting in reduced payload, DRDC said. This can be a problem for ultralight vehicles and single-seat ATVs. In addition, at low temperatures, the characteristics of the batteries themselves are reduced, they often have problems with charging and temperature control.
Although sequential hybrids eliminate the mechanical transmission, the need for an engine, generator, power electronics and battery inevitably makes them ultimately difficult and expensive to buy and maintain.
Most battery electrolytes can also pose risks when damaged, for example, lithium-ion cells are known to ignite when damaged. Whether this poses a greater risk than supplying diesel fuel is perhaps a moot point, the report points out, but hybrids carry both risks.
Combination selection
The two main schemes for combining internal combustion engines with electrical devices are serial and parallel. As mentioned above, the serial hybrid platform is an electric machine with a generator, while in parallel there is an engine and a traction motor, which, through a mechanical transmission connected to them, transmit power to the wheels. This means that the engine or traction motor can drive the machine individually, or they can work together.
In both types of hybrids, the electrical component is typically a motor-generator set (MGU), which can convert electrical energy into motion and vice versa. It can drive a car, charge a battery, start an engine and, if necessary, conserve energy through regenerative braking.
Both series and parallel hybrids rely on power electronics to manage battery power and regulate battery temperature. They also provide the voltage and amperage that the generator must supply to the batteries and the batteries in turn to the electric motors.
This power electronics comes in the form of semiconductor inverters based on silicon carbide semiconductors, the disadvantages of which, as a rule, include large size and cost, as well as heat loss. Power electronics also require control electronics similar to those that power an internal combustion engine.
Until now, the history of electrically powered military vehicles has consisted of experimental and ambitious development programs that were ultimately closed. In real operation, there are still no hybrid military vehicles, in particular, in the field of light tactical vehicles, several unresolved technological problems remain. These problems can be considered largely solved for civilian vehicles as they operate in much more favorable conditions.
Electric cars have shown themselves to be very fast. For example, Nikola Motor's experimental battery-powered Reckless Utility Tactical Vehicle (UTV) four-seater can accelerate from 0 to 97 km / h in 4 seconds and has a range of 241 km.
"Layout, however, is one of those big challenges," says the DRDC report. The size, weight and heat dissipation of battery packs are quite large, and a compromise must be made between the total energy capacity and the instantaneous power they can deliver for a given mass and volume. Allocation of volume for high-voltage cables, their reliability and safety are also bottlenecks along with size, weight, cooling, reliability and waterproofing of power electronics.

Heat and dust
The report says the temperature swings faced by military vehicles are perhaps the biggest problem, as lithium-ion batteries won't charge in sub-zero temperatures and heating systems add complexity and need energy. Batteries that overheat during discharge are potentially dangerous, they must be cooled or reduced to a reduced mode, while motors and generators can also overheat, finally, do not forget about permanent magnets, which are prone to demagnetization.
Likewise, at temperatures above about 65 ° C, the efficiency of devices such as IGBT inverters decreases and therefore needs cooling, although newer power electronics based on silicon carbide semiconductors or gallium nitride, in addition to operating at increased voltage, withstands higher temperatures and, therefore, can be cooled from the engine cooling system.
In addition, the shock and vibration from rough terrain, plus the potential damage that could be caused by shelling and explosions, also makes it difficult to integrate electric drive technology into light military vehicles, the report notes.
The report concludes that DRDC should order a technology demonstrator. It is a relatively simple lightweight sequential hybrid tactical vehicle with electric motors installed either in the wheel hubs or in the axles, the diesel engine is tuned to the appropriate peak power, and a set of super- or ultracapacitors is installed to improve acceleration and gradeability. Supercapacitors or ultracapacitors store a very large charge for a short period of time and can release it very quickly to generate power pulses. The car will either not be at all, or a very small battery will be installed, electricity will be generated during the regenerative braking process, as a result, the modes of silent movement and silent observation are excluded.
Power cables running to the wheels alone, replacing the mechanical transmission and drive shafts, will significantly reduce the weight of the machine and improve explosion protection, since the scattering of secondary debris and fragments is eliminated. Without a battery, the internal volume for the crew and payload will increase and become safer, and the problems associated with maintenance and thermal management of lithium-ion batteries will be eliminated.
In addition, the following goals are set when creating a prototype: lower fuel consumption of a relatively small diesel engine operating at constant rpm, combined with energy recovery, increased power generation for operating sensors or energy export, increased reliability and improved service.
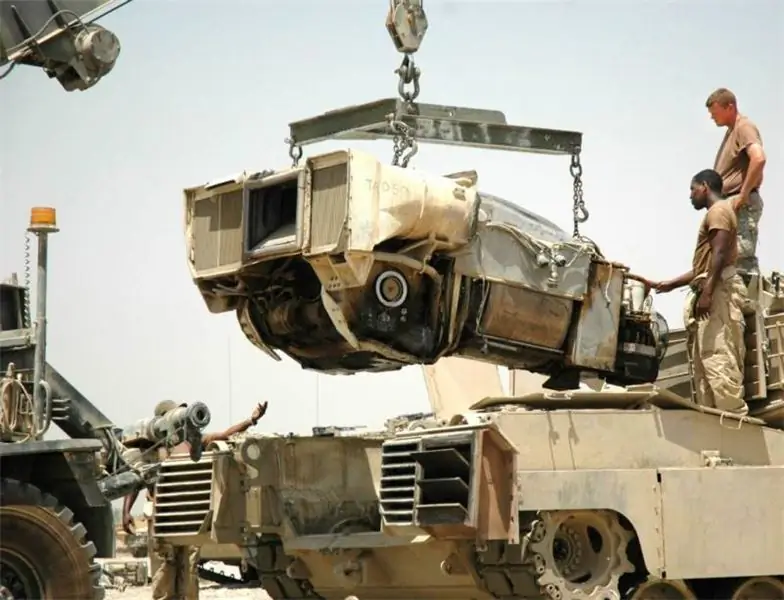
The bumps do not care
As Bruce Brandl of the Armored Research Center (TARDEC) explained at a presentation on engine development, the US Army wants a propulsion system that will allow its combat vehicles to move through more difficult terrain at higher speeds, which will significantly reduce the percentage of terrain in war zones. on which current cars cannot move. The so-called impassable terrain makes up about 22% of these zones and the army wants to reduce this figure to 6%. They also want to increase the average speed in most of the area from today's 16 km / h to 24 km / h.
In addition, Brandl emphasized that the energy demand on board is planned to be increased to at least 250 kW, that is, higher than what the machine's generators can provide, as loads are added from new technologies, for example, electrified towers and protection systems, cooling of power electronics., energy export and directed energy weapons.
The US Army estimates that meeting these needs with current turbodiesel technology will increase the engine's volume by 56% and the vehicle's weight by about 1400 kg. Therefore, when developing its advanced power plant Advanced Combat Engine (ACE), the main task was set - to double the total power density from 3 hp / cu. ft to 6 hp / cu. foot.
While higher power density and better fuel efficiency are very important for the next generation of military engines, it is equally important to reduce heat output. This generated heat is wasted energy dissipated into the surrounding space, although it could be used to propel or generate electrical energy. But it is far from always possible to achieve a perfect balance of all these three parameters, for example, the AGT 1500 gas turbine engine of the M1 Abrams tank with a capacity of 1500 hp. has low heat transfer and high power density, but very high fuel consumption compared to diesel engines.
In fact, gas turbine engines generate a large amount of heat, but most of it is removed through the exhaust pipe, due to the high rate of gas flow. As a result, gas turbines do not need the cooling systems that diesel engines need. A high specific power of diesel engines can be achieved only by solving the problem of thermal control. Brandl emphasized that this is mainly due to the limited volume available for cooling equipment such as piping, pumps, fans and radiators. In addition, protective structures such as bulletproof grilles also take up volume and restrict airflow, reducing the efficiency of the fans.
Pistons towards
As Brandl noted, the ACE program focuses on two-stroke diesel / multi-fuel engines with opposed pistons due to their inherent low heat dissipation. In such engines, two pistons are placed in each cylinder, which form a combustion chamber between them, as a result, the cylinder head is excluded, but this requires two crankshafts and an intake and exhaust ports in the cylinder walls. Boxer engines date back to the 1930s and have been continuously improved over the decades. This old idea was not spared by the company Achates Power, which, in cooperation with Cummins, revived and modernized this engine.
An Achates Power spokesperson said their boxer technology has improved thermal efficiency, which translates into lower heat losses, improved combustion and reduced pumping losses. The elimination of the cylinder head significantly reduced the surface area-to-volume ratio in the combustion chamber and thereby the transfer and release of heat in the engine. In contrast, in a traditional four-stroke engine, the cylinder head contains many of the hottest components and is the main source of heat transfer to the coolant and the surrounding atmosphere.
The Achates combustion system uses twin fuel injectors diametrically positioned in each cylinder and a patented piston shape to optimize the air / fuel mixture, resulting in low soot combustion and reduced heat transfer to the combustion chamber walls. A fresh charge of the mixture is injected into the cylinder, and exhaust gases exit through the ports, aided by a supercharger that pumps air through the engine. Achates points out that this direct-flow blowdown has a beneficial effect on fuel economy and emissions.
The US Army wants the ACE family of modular scalable powertrains to include engines with the same bore and stroke and different cylinder counts: 600-750 hp. (3 cylinders); 300-1000 HP (4); and 1200-1500 hp. (6). Each power plant will occupy a volume - a height of 0, 53 m and a width of 1, 1 m and, accordingly, a length of 1, 04 m, 1, 25 m and 1, 6 m.
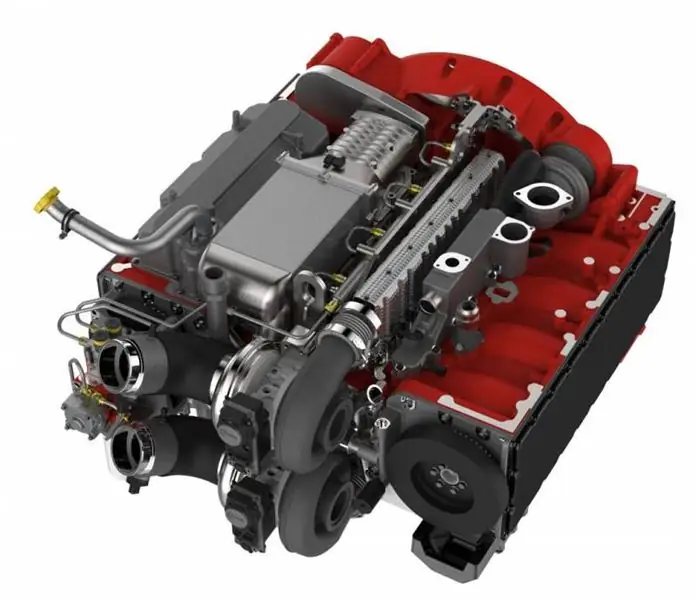
Technological goals
An internal Army study conducted in 2010 confirmed the benefits of boxer engines, resulting in the Next-Generation Combat Engine (NGCE) project, in which industrial enterprises presented their developments in this area. The task was to reach 71 hp. per cylinder and a total power of 225 hp. By 2015, both of these numbers were easily exceeded on an experimental engine tested at the Armored Research Center.
In February of the same year, the army awarded contracts to AVL Powertrain Engineering and Achates Power for experimental ACE single-cylinder engines under a two-year program, within the framework of which the goal was to achieve the following characteristics: power 250 hp, torque 678 Nm, specific fuel consumption 0, 14 kg / hp / h and heat dissipation less than 0.45 kW / kW. All indicators were exceeded, except for heat transfer, here it was not possible to fall below 0.506 kW / kW.
In the summer of 2017, Cummins and Achates began work under an ACE Multi-Cylinder Engine (MCE) contract to demonstrate a 1,000 hp four-cylinder engine. torque of 2700 Nm and the same requirements for specific fuel consumption and heat transfer. The first engine was manufactured in July 2018 and initial operational tests were completed by the end of the same year. In August 2019, the engine was delivered to the TARDEC Directorate for installation and testing.
The combination of a boxer engine and a hybrid electric drive would improve the efficiency of vehicles of various types and sizes, both military and civilian. With this in mind, the Advanced Research and Development Authority issued $ 2 million to Achates to develop an advanced single-cylinder boxer engine for future hybrid vehicles; in this project the company collaborates with the University of Michigan and Nissan.
Piston control
In accordance with the concept, this engine for the first time so closely integrated the electrical subsystem and the internal combustion engine, each of the two crankshafts rotates and can be driven by its own motor-generator set; there is no mechanical connection between the shafts.
Achates confirmed that the engine is only designed for sequential hybrid systems, as all the power it generates is transmitted electrically and the gensets charge the battery pack to extend the range. Without a mechanical connection between the shafts, the moment is not transmitted, which leads to a decrease in loads. As a result, they can be made lighter, reduce overall weight and size, friction and noise, and reduce costs.
Perhaps most importantly, the decoupled crankshafts allow independent control of each piston through the use of power electronics. "This is an important part of our project, it is important to determine how the development of electric motors and controls could improve the efficiency of the internal combustion engine." An Achates spokesperson confirmed that this configuration allows for crankshaft timing control, which opens up new possibilities. "We strive to improve the efficiency of piston control, which is not available with traditional mechanical communication."
At this point, there is little information available regarding how independent piston control can be used, but in theory it is possible to make the stroke larger than the compression stroke, for example, and thereby extract more energy from the charge of the air / fuel mixture. A similar scheme is implemented in four-stroke Atkinson engines installed in hybrid cars. In the Toyota Prius, for example, this is achieved through variable valve timing.
For a long time, it was obvious that big improvements in mature technologies, such as internal combustion engines, are not easy to achieve, but advanced boxer engines could be what would provide real advantages to military vehicles, especially when combined with electric propulsion systems. …